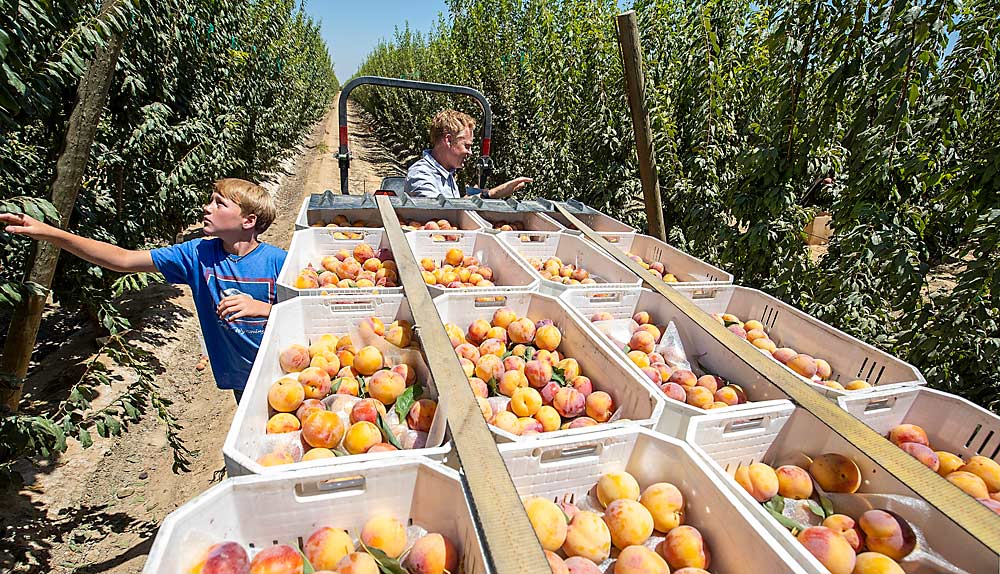
Stone fruit growers want trellised, two-dimensional fruiting walls that could boost efficiencies of labor, space and water while paving the way for mechanization.
They have a way to go, said Eric Wuhl, research director for Family Tree Farms in Reedley, California, one of the stone fruit industry’s leaders in this transition.
Growers are still finding the right combination of varieties, rootstocks and training systems to catch up with the productivity of apple orchards.
“This is where stone fruit is the furthest behind other fruits,” Wuhl said.
Family Tree is answering many of those efficiency questions. As one of the early adopters, the farm has passed the trial stage; the company has installed wires on a large percentage of its new planting acreage and also uses platforms for commercial harvest, pruning and thinning.
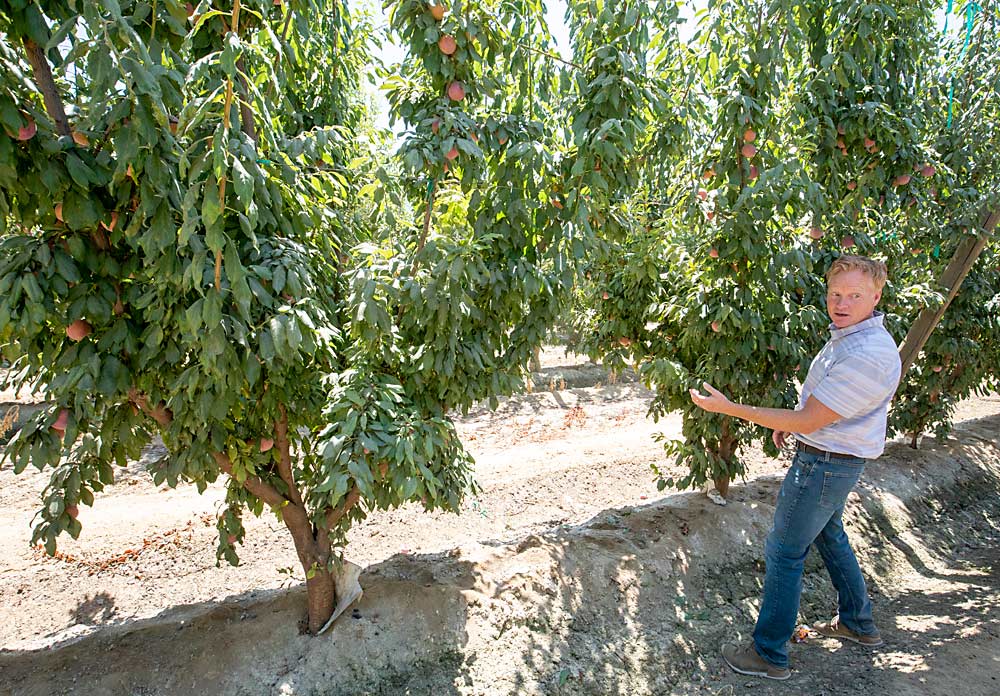
California has about 200 stone fruit growers, but Family Tree is one of seven vertically integrated producers that account for the bulk of stone fruit volume from California’s Central Valley near Fresno, the most productive region of the United States, said Ian LeMay, president of the California Fresh Fruit Association. All of them are looking for efficiency improvements as they vertically integrate to keep up with the same industry pressures — rising labor costs, increasingly complex regulations and water sources that seem to become more scarce every year.
“The stone fruit industry is becoming smaller and smaller in terms of the amount of growers represented,” said Andy Muxlow, one of the four primary owners of Family Tree Farms.
Those consolidating companies have made investments in the packing facilities, but trees are the next target for efficiencies. “The collective industry focus is now out in the orchard,” LeMay said.
Planar fruiting walls on trellises are not exactly normal yet, but they’re getting closer each season as companies replace blocks and adopt technology such as platforms.
Systems and mechanization
Finding the right orchard system is the biggest challenge, Family Tree leaders said.
Family Tree Farms has been using trellises for over 25 years to create fruiting walls, moving toward high-density with every new planting.
“That’s the name of the game. You fill up the wall of space, so you look down and it’s just a wall of fruit,” Muxlow said.
All apricots, plums and plumcots get trellises, and all trellises are Tatura-style. Trees are planted with a single trunk and split into two or more leaders in the shape of a V. Workers reach through the canopy to prune inside, a never-ending job for trees that want to grow vertically.
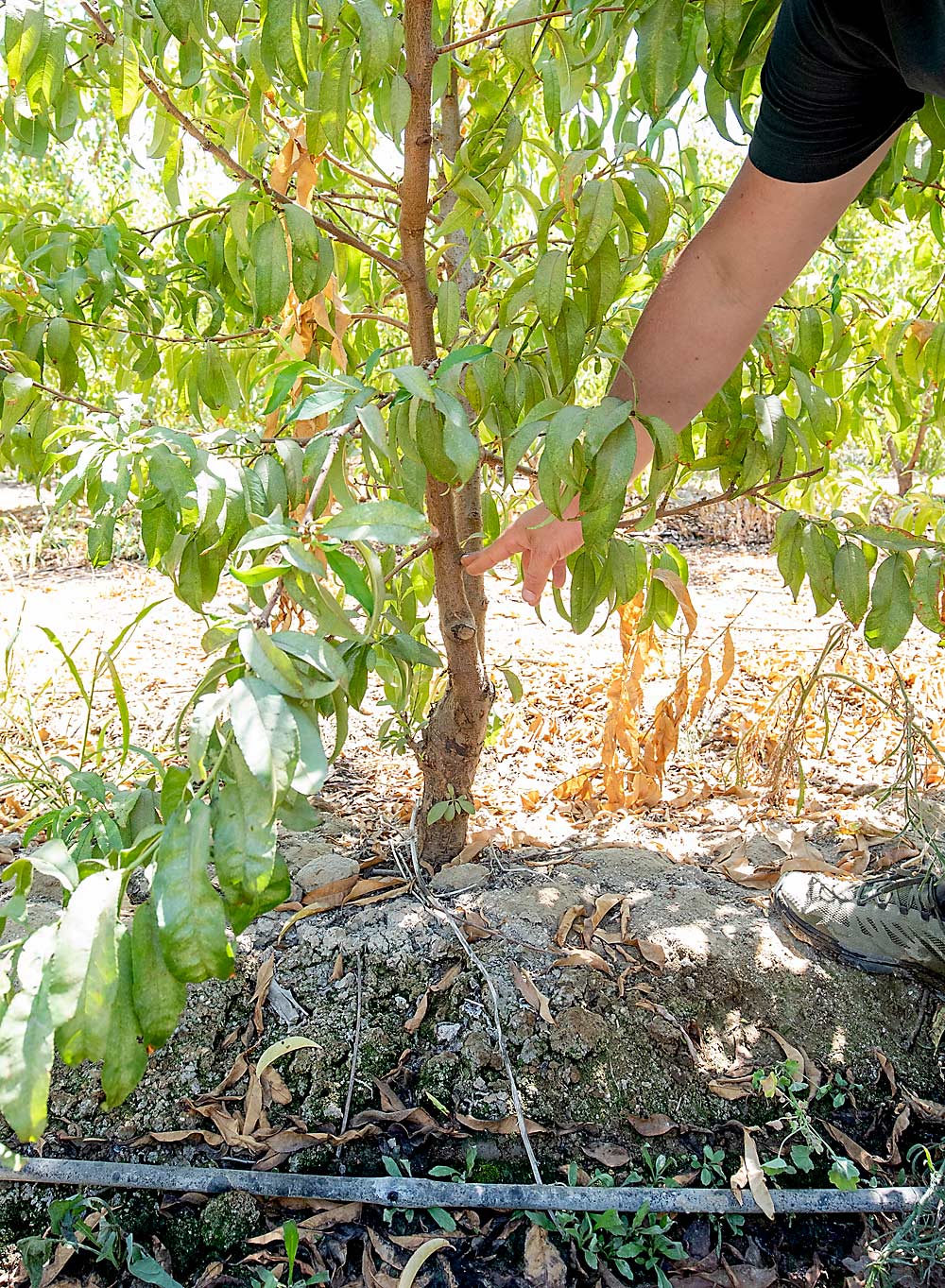
The family uses three wires, moving them up as trees grow. At the full, 12-foot tree height, the first wire will be at 6 feet, easy for workers to duck underneath, Muxlow said.
Wires only support the leaders, or what the family calls “scaffolds.” The lateral fruiting branches — “hangers” — grow free. The family also does not use growth regulators or scoring to encourage lateral breaks. Wounds from trellis wires have not been a problem, Muxlow said.
Trellised peaches and nectarines are planted at 17- by 9-foot spacing on traditional rootstocks, probably a medium density, Muxlow said. They are trained into four scaffolds, two on each side of the V.
More vigorous plums and plumcots at the same spacing get six or eight scaffolds. The trees can handle more fruit, and the hangers don’t grow as long. In fact, crews usually tip them shorter.
Most future plantings will be trellised, but family members do not use trellises for all of their fruit, because sometimes they want to save on initial startup costs, Muxlow said.
The majority of peaches and nectarines still are free-standing, trained on bamboo stakes with their canopies roped into a compact shape. It’s not perfect, but platforms work there, too, Muxlow said.
The company has 24 platforms — and a goal to completely replace ladders. They have also found that crews on a platform operate faster than crews working on the ground, because they don’t have to walk anywhere to empty their buckets, Muxlow said.
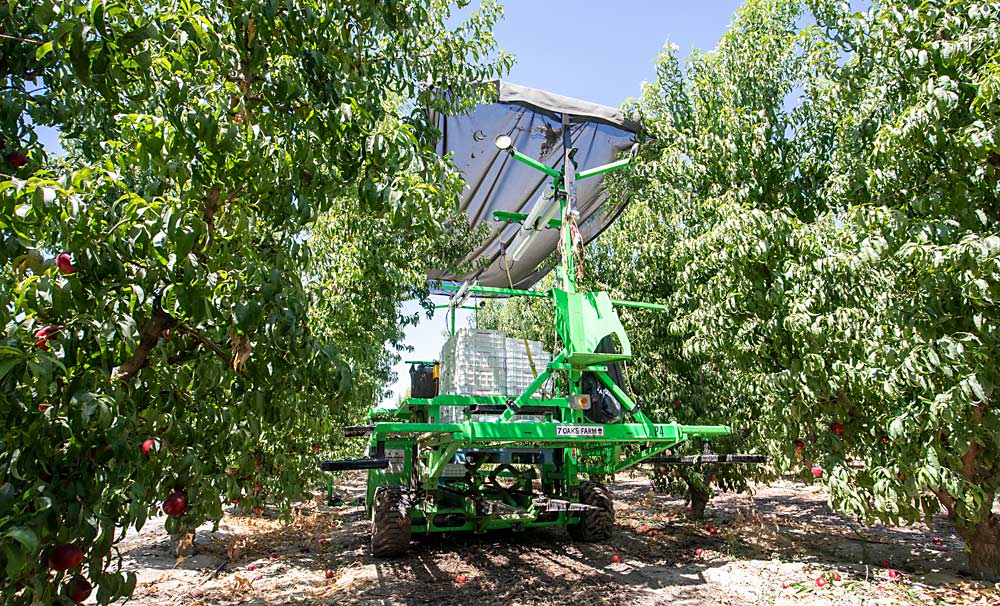
The business also ran trials with GUSS automated spray vehicles and has purchased four units.
During an August 2021 visit by Good Fruit Grower, Ty Muxlow, Andy’s son, showed his block of trellised Pearlicious white nectarines with trunks emerging from berms at a 3.5-foot tree spacing. He used only two scaffolds, one in each direction, to form the V.
“It’s pretty experimental,” said Ty Muxlow, a young farm manager and a member of the family’s third-generation owners.
Good Fruit Grower also visited a block of Gold Rush plumcots on traditional rootstocks, spaced at 17 by 9 feet. It had eight scaffolds, four on each side of the trunk.
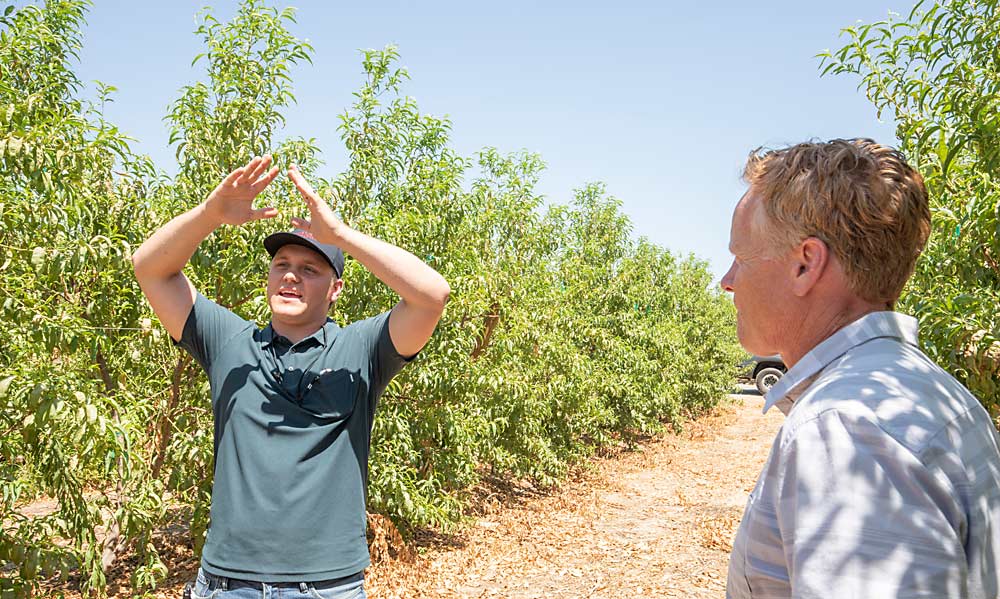
Rootstocks and water
Rootstock costs, compatibility and availability factor into the trellis decisions, too.
The company runs trials of 20 different rootstocks in its own research and development orchard.
Rootstocks are expensive — $4 each, and you need about 1,000 per acre, said Wuhl, the farm’s research director. It takes 12 to 14 years to evaluate a rootstock.
Compatibility problems sometimes don’t manifest until trees reach 8 or 9 years old, he said.
New efficiencies are needed for water, too. Drought in California is an annual story that becomes bleaker every year.
The farm has a history of furrow irrigation, but those days are almost over. More than 95 percent of the farm’s acreage is drip irrigation now, and they are rapidly converting the rest, leveling the furrow berms to make way for those platforms.
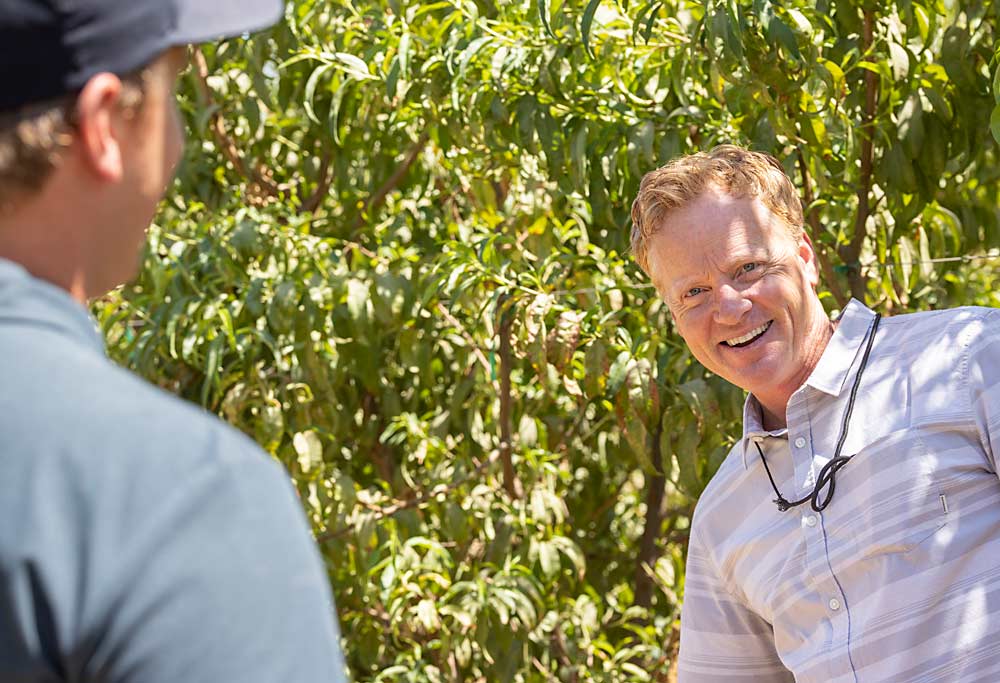
The company uses mostly well water, but California has ground water regulations coming that will affect stone fruit operations. For example, in one section of Family Tree Farms, they had to remove about 40 acres to comply.
The family also irrigates strategically, Andy Muxlow said. Farm supervisors carefully monitor irrigation levels 10 days before harvest, to increase Brix measurements in fruit. They also use limited water at bud differentiation, to encourage trees to develop more fruit buds than vegetative growth, for the following year.
Despite Family Tree Farms’ sophistication and size — 10,000 acres overall, including citrus, nuts and blueberries in the U.S. and overseas — the company is still a family-driven affair. David Jackson, one of the four owners and Andy’s father-in-law, is patriarch of the family. He has 21 grandchildren, and the farm has “college blocks” that the kids manage as coming-of-age projects to save up for their future educational goals.
“We consider it a calling,” Jackson said of farming.
The never-ending quest for efficiencies helps to make the industry sustainable for the next generation.
“I’m hopeful,” Andy Muxlow said. •
—by Ross Courtney
Leave A Comment