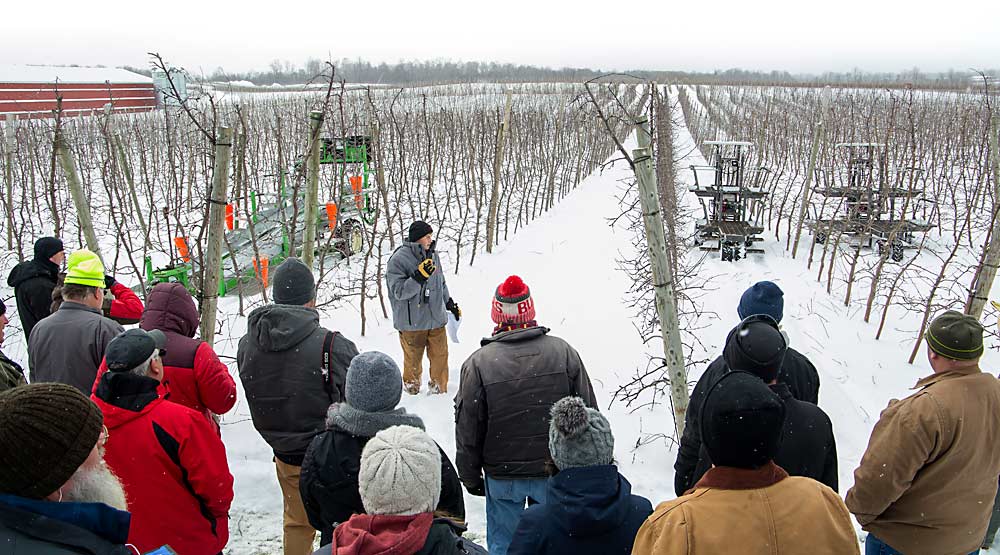
The apple growers along New York’s southern shore of Lake Ontario, where half the fruit goes to processing, are embracing change, planting high densities of new varieties, preparing their orchards for mechanization and sometimes inventing their own tools to move the needle further toward the fresh market.
“You have to change,” said Matt Wells of New York Apple Sales. “Complacency equals failure.”
Wells and numerous other presenters and organizers pleaded with growers to seek change, with some urgency, at the annual International Fruit Tree Association’s conference and tours in Rochester, New York, in February.
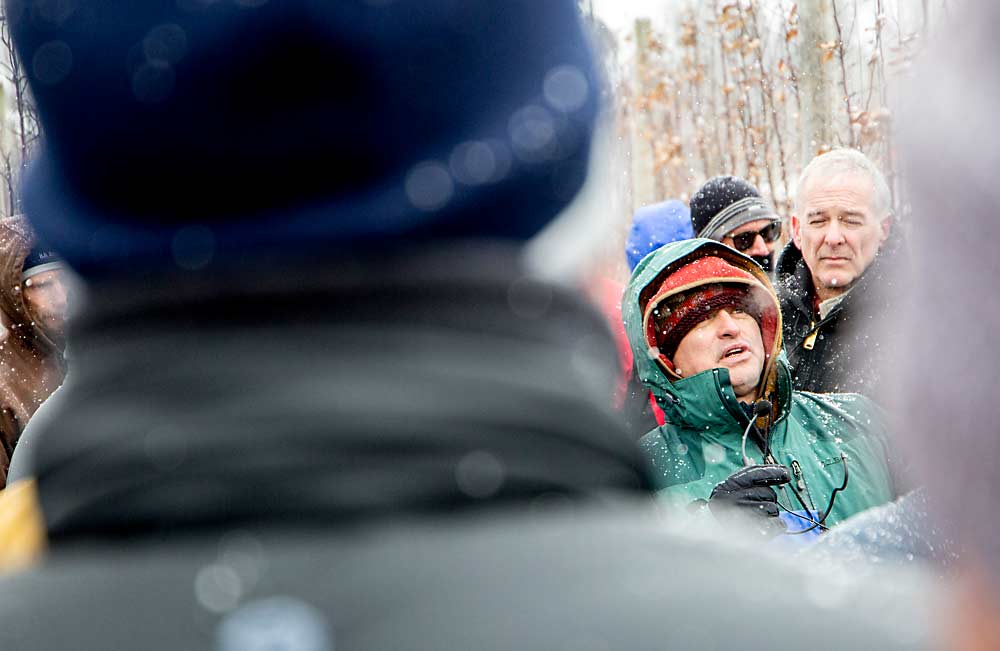
With detailed price estimates, Wells made a financial plea for growers in his state to modernize or leave money hanging from the branches. “There’s money in the maze,” he said, referencing the 1998 book “Who Moved My Cheese.” “It’s out there, you just have to go get it every day.”
For example, using 2018 return statistics, shifting a Honeycrisp packout from 70 percent to 80 percent and the percentage of apples packed in a tray as opposed to a bag from 60 percent to 70 percent bumps up returns per bin from $579 to $680.
“So, serious money here,” he said.
Growers throughout the region are adopting his advice. Everywhere apples hang on young, planar hedges with branches 2 feet apart within 10-foot rows, or somewhere near those measurements. And many growers are not afraid of trying their own paths toward change.
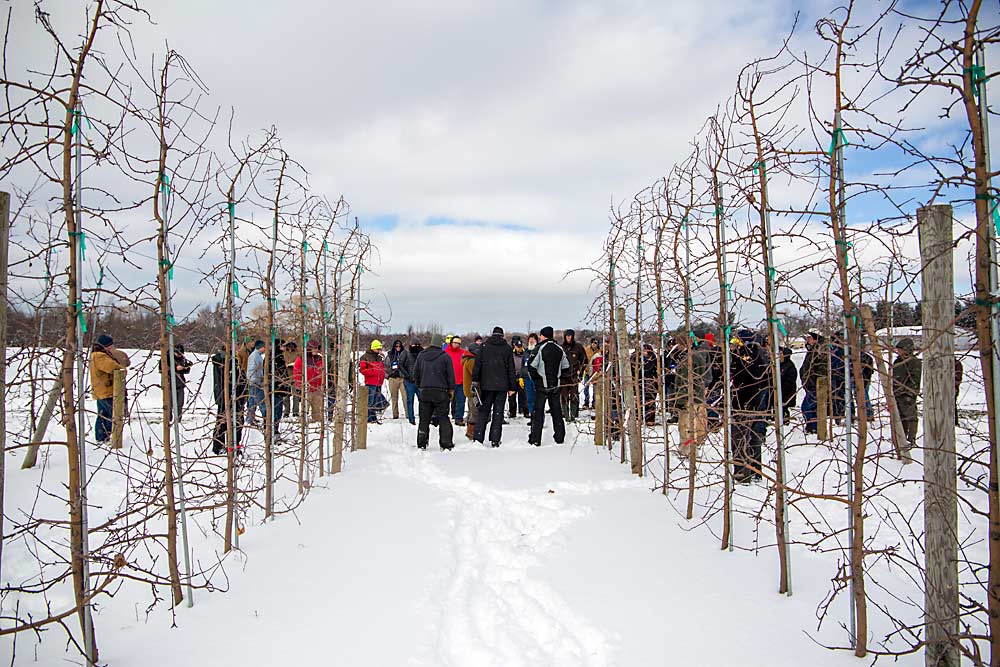
Take Kyle Wafler, a third-generation grower, and his family. In 2010, the owners of Wafler Farms in Wolcott, east of Rochester, developed their own orchard architecture called tall spindle tip, planting spindle trees at opposing angles with a deflection of 1.5 feet for 11-foot trees.
They have found their harvest and work platforms work better when the trees lean just a little inward, Wafler said.
The tops of each row are always 10 feet apart, meaning the floors have alternating wide and narrow rows. Workers run the platforms down every other alleyway, reaching through the skinny canopy to pick and prune the opposite side.
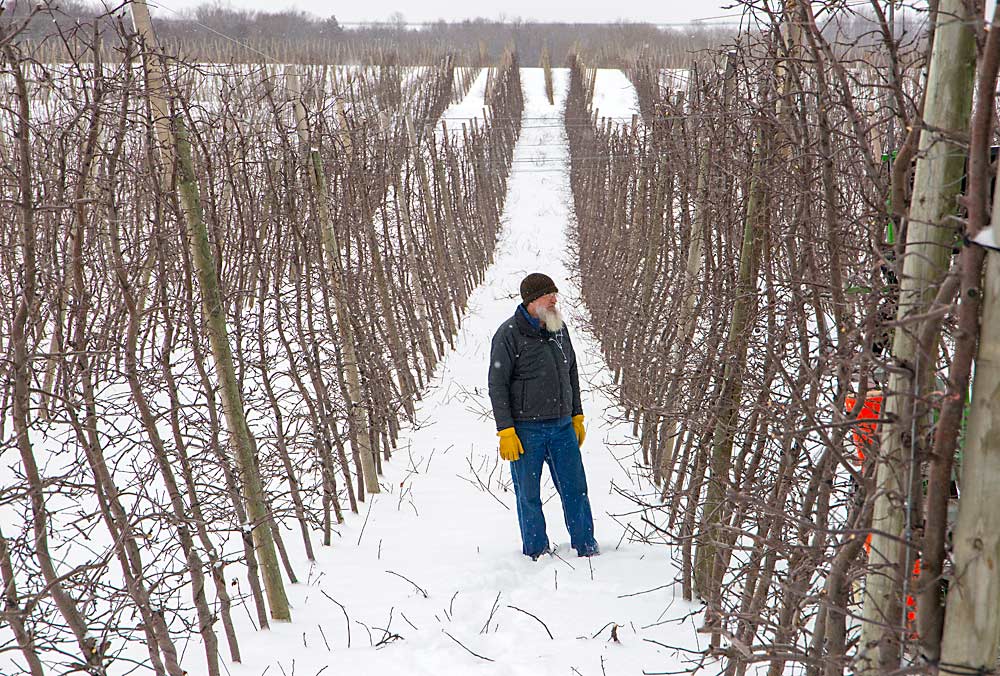
The Waflers are also known for using on-platform cameras to monitor quality and employee efficiencies, designing their own orchard platforms through their company, Huron Fruit Systems, and their nursery.
At Fowler Farms, just a few miles south, managers are working with Helena Agri Enterprise on variable fertilizer rate trials to amend soil with more precision, accounting for the rolling topography. At Excelsior Farms, west of Rochester in Kent, New York, Roger and Christine Bannister are in the process of replacing all their vertical axe trees with multileaders.
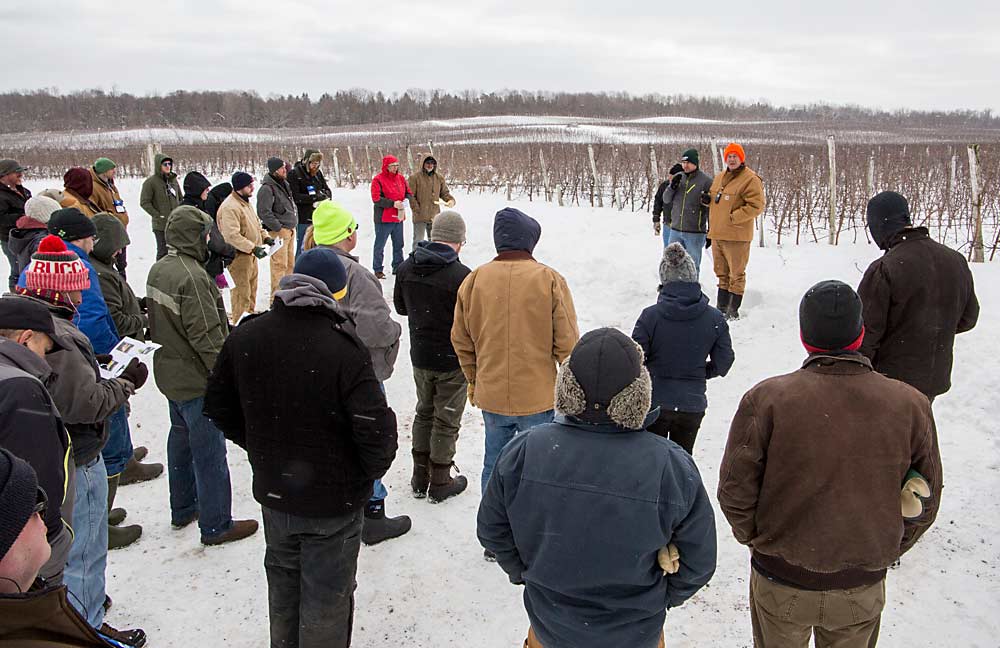
Technology
Meanwhile, everybody is eyeing technology and mechanization.
For example, Michael Sadler, a farm manager from Lyndonville, New York, has invested in a pollen blower to improve fruit set and has affectionately nicknamed it “The Inseminator.”
George Kantor of Carnegie Mellon University’s Robotics Institute encouraged growers who are anxious for robots to save them from labor shortages to similarly invest in mechanical tools already available and collaborate with companies trying to perfect more.
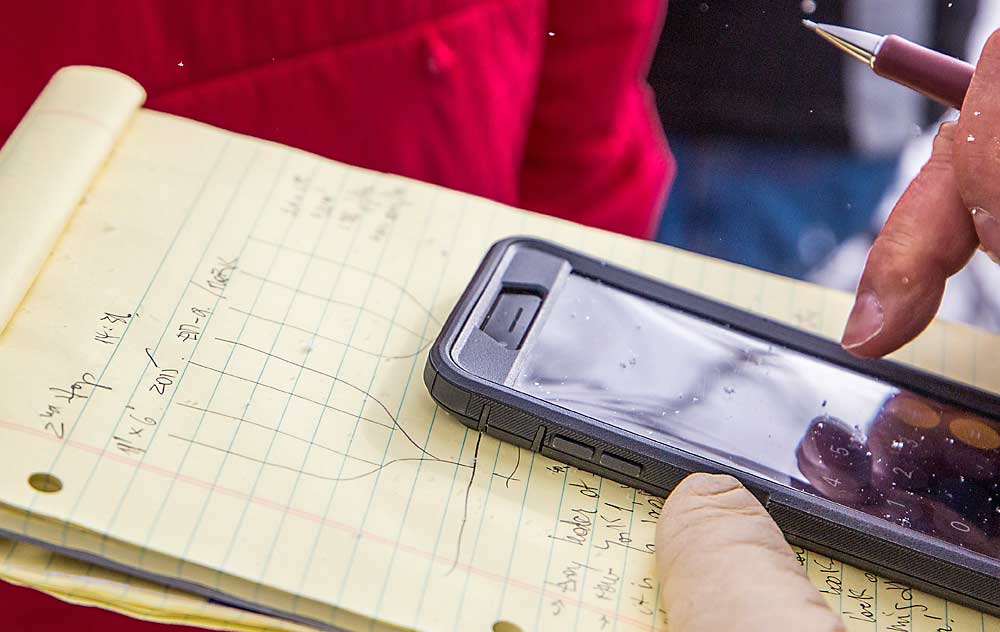
Tech companies have made leaping strides in the mobility and perception legs of the robotic stool but are still getting there on manipulation — the point where robots actually touch and move fruit and plants, such as the robotic harvesters under development by Abundant Robotics and FFRobotics, said Kantor, who presented the IFTA’s annual Robert Carlson Lecture.
“The technologies are here, but they’re not going to necessarily make it into your corner of the world unless you help bring (them) in,” he said.
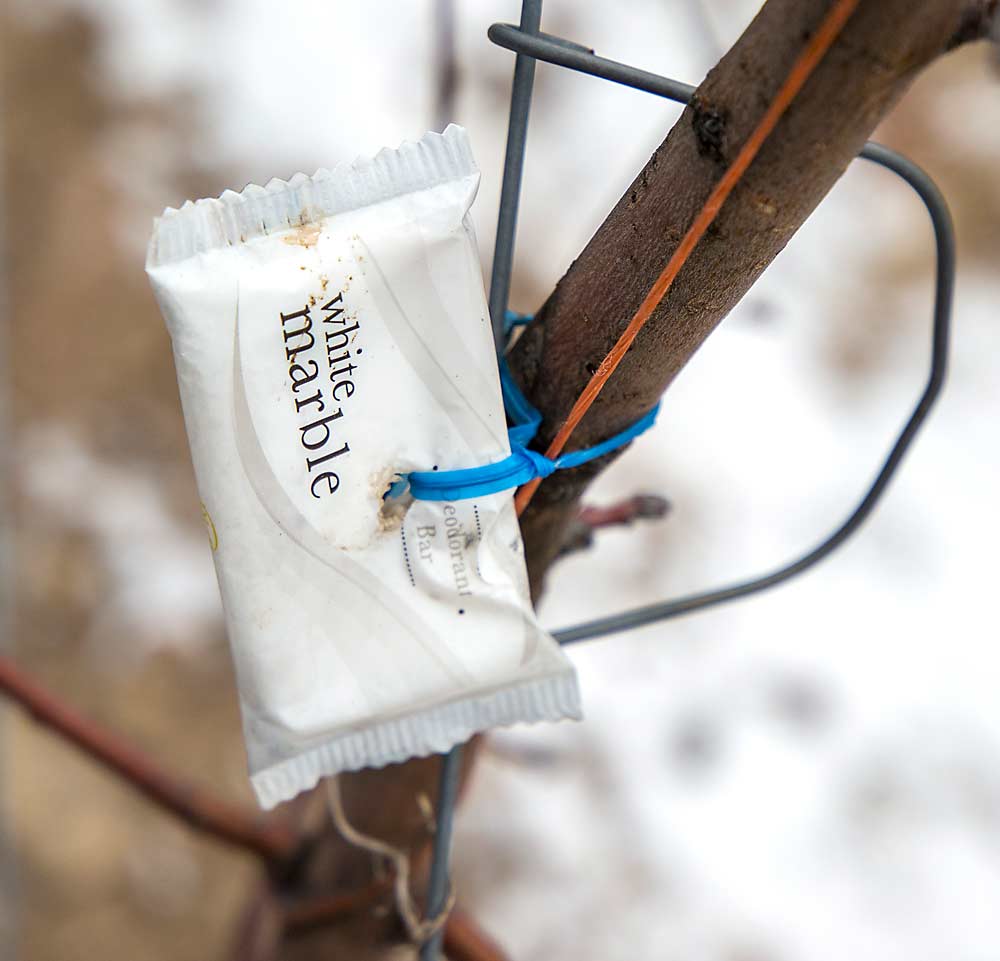
Processing still pertinent
All this change is happening in a region where the processing industry is still relevant.
New York growers send about 52 percent of their apples to processing, compared to Washington’s 18 percent, according to Cornell University researchers. The state is home to six processors, the biggest of which is Mott’s, a subsidiary of Dr Pepper Snapple Group in Plano, Texas. Mott’s New York apple processing facility is located in Williamson in Wayne County, east of Rochester, where growers send nearly 60 percent of their apples to processing.
“Yes, we still have some big trees and the reason why is because they’re still making us money,” said Todd Furber. He and his brother, Ted Furber, who together manage Cherry Lawn Fruit Farms in Sodus, send about 70 percent of their apples fresh, but have other varieties and blocks they would remove before they tear out their processing-only Idareds. Those trees produce.
“If we’re going to play the process game, we gotta have yields,” he said.
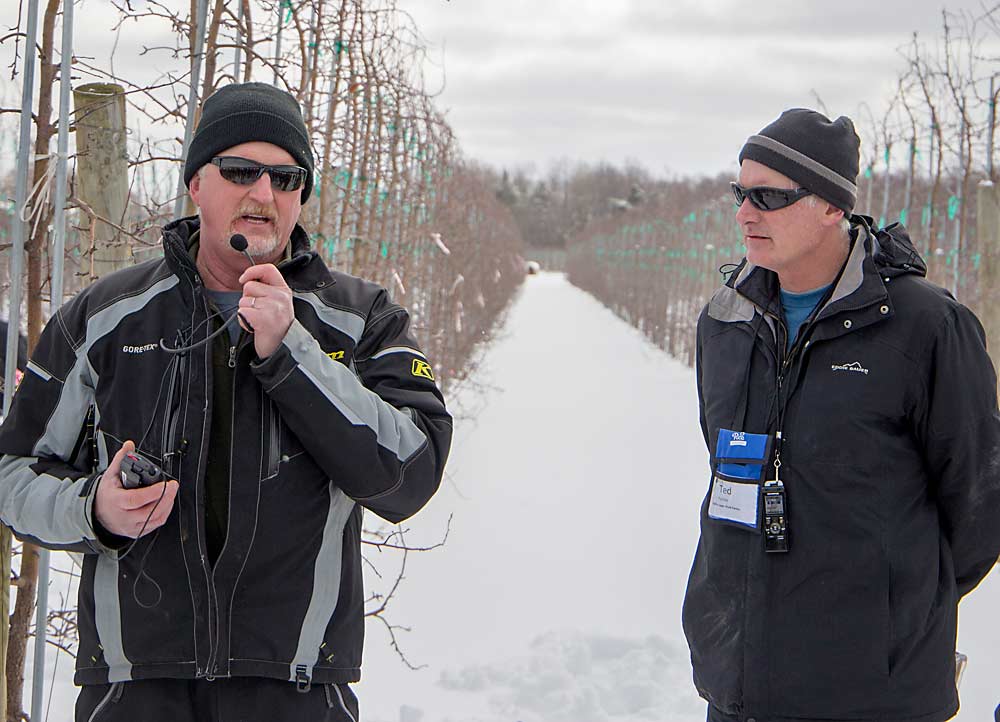
Mott’s takes in about 7 million bushels of apples each year, almost exclusively from their pool of 165 New York growers, said Gary Orbaker, a fourth-generation Wayne County grower.
Some growers still plant new orchards solely for processing, with semidwarf trees 10 feet apart, as opposed to the 2-foot spacing found in so many new trellised orchards.
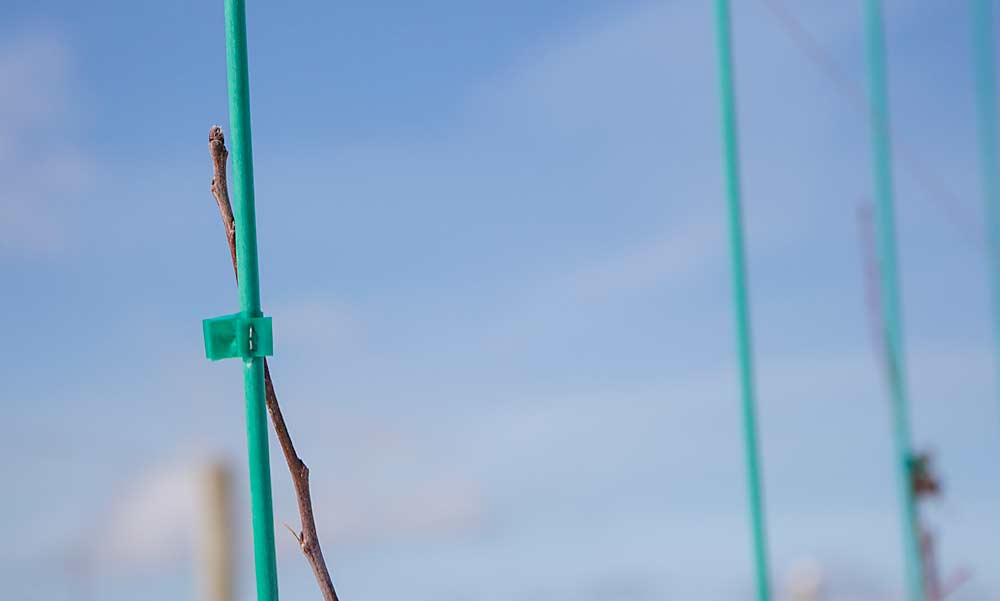
Some growers simply like working with processed apples, which are cheaper to grow, while others are trying to shift gradually as they can afford to purchase trellises and higher-performing rootstocks, Orbaker said. Although, some might try to speed up that transition after 2018, when prices fell by an average of 2.5 cents per pound to less than the cost of production, he said.
That was an unusual year, but the trend is going toward fresh as growers look for ways to make the rising costs of production, namely labor, pay off. “It’s getting harder to grow the apples for the processing market, for sure,” he said. •
—by Ross Courtney
Related:
—Final IFTA tour stop: Grow to replace
—Growers, researchers earn IFTA awards
Leave A Comment