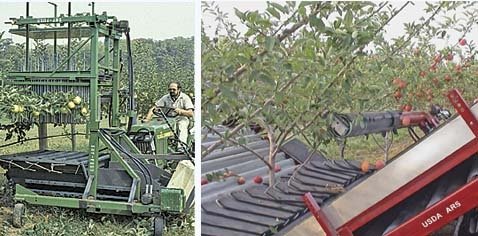
Left: This rod-press apple harvester was designed for the New Zealand T-trellis. Apples were detached by parallel rods, with rubber tips, which pressed down the canopy. Right: Apple harvesting in 2002, using a rapid displacement actuator to snap branches
My first experience with mechanization research was in 1970 at the University of Hawaii, where I was an agricultural engineering student working towards a masters degree. My assistantship was partially funded by the U.S. Department of Agriculture, Agricultural Research Service, and concerned the feasibility of shake-catch harvesting of macadamia nuts. Mechanization research had been on the rise for about ten years, intensified by the loss of the Mexican bracero program in 1964.
The ARS hired me in Hawaii, and then transferred me to the Southeastern Fruit and Tree Nut Research Laboratory, located in Byron, Georgia. At the time, the ARS had six mechanization units throughout the country with ten engineers conducting research on fruit harvesting. There were 11 state university locations with 16 engineers conducting similar research.
The harvest of crops like prunes and tart cherries for processing had been mechanized with shake-catch harvesters. The thinking was that the tree fruit industry would go to high-density plantings and need higher harvest rates. We developed a continuously-moving two-piece shake-catch harvester for peaches. The shaker was automatically positioned and clamped around the trunk. After the trunk was shaken, the shaker was unclamped, withdrawn, and returned to its initial position ready for the next tree.
We were able to more than double harvest rates over commercial harvesters. Fruit damage was not a serious problem since fresh-market peaches in the Southeast are very firm when harvested. The most serious limitation to commercialization was nonuniformity of maturity. Fruit removal by shaking was not selective.
Antimechanization movement
In 1979, after completing my doctorate at Michigan State University, I was selected to lead the engineering research at the newly opened Appalachian Fruit Research Station, Kearneysville, West Virginia. My assignment was to “develop mechanized harvest systems for fruit crops while maintaining fruit quality, improve labor productivity, and reduce costs.” Coincidental with my arrival there, the U.S. Secretary of Agriculture, Bob Bergland, announced that USDA would not fund any research that improved labor productivity. The University of California had been sued for “doing research that only benefited large corporate farms, and for displacing workers by mechanization.”
A significant antimechanization movement swept the country, and in the next 20 years would nearly eliminate federal and state funding for mechanization research. However, I was advised to keep a low profile, and continue.
In a cooperative project with Dr. Steve Miller, research horticulturist, we tried to develop a training system for freestanding apple trees to be compatible with an over-the-row continuously moving shake-catch harvester for the fresh market. Extensive studies on tree designs, fruit detachment techniques, catching surfaces, and fruit handling components resulted in fruit quality better than with commercial harvesters, but still not good enough.
In cooperation with Dr. Galen Brown, ARS engineer, and other Michigan researchers, the over-the-row continuously moving shake-catch harvester was tested on experimental high-density plantings of tart cherries. It demonstrated harvest rates up to 360 trees per hour with fruit quality that was acceptable for processing.
New Zealand research
In the early 1980s a researcher in New Zealand developed a T-shaped trellis for the production of high-quality apples. Apples were positioned under fruiting branches and were supposed to be compatible with machine harvest. I got the idea for a rod-press harvesting concept where a panel of parallel rods, with soft rubber tips, would be pressed through the canopy to detach apples.
The technique worked great with almost no damage when apples were to the side and below branches. However, in order to get high productivity on this system, apples had to be positioned everywhere, and this harvest technique caused severe damage to apples on top of branches and trellis members.
A unique spiked-drum canopy shaker was developed for small fruits that delivered more uniform acceleration and larger displacements than conventional canopy shakers. In cooperation with the Florida Department of Citrus, we demonstrated our canopy shaker to be very effective in removing oranges for the process market. Three companies, borrowing from our success, developed commercial canopy-shaking harvesters that increased labor productivity by 15 times, reduced harvesting cost up to 50 percent, and had very high capacity.
The development of narrow-inclined trellises for efficient production of high-quality tree fruits also presents opportunities for mechanical harvesting. Cooperation with a Danish research engineer Dr. Bent Bennedsen led to the development of a robotic bulk apple- harvesting concept.
Imaging software was used to determine apple and branch locations in the canopy. Control software was used to position a rapid displacement actuator to snap branches upward causing apples to be detached with little initial movement. The narrow canopy allowed apples to fall directly to a soft catching surface. Initial results looked promising. Loss of our software engineer back to Denmark, and the idea that a human could more efficiently control the harvesting sequences, led to a person using a pair of joysticks to position the rapid displacement actuator.
Addition of a padded-pocket conveyor and automated bin filler completed the harvester. Tests demonstrated the ability to harvest apples with up to 85 percent U.S. Extra Fancy grade, and increased labor productivity by five times, but results were not good enough to prompt commercialization.
About the same time as we were developing the RDA harvesting concept, Bob Harris and Denny Hayden, Washington State orchardists, were developing the stemless sweet cherry concept in anticipation of mechanical harvesting. Fortunately, we discovered we had mutually compatible ideas. With the assistance of the Washington Tree Fruit Research Commission, we developed a complete sweet cherry harvester using the RDA concept. Extensive tests under commercial conditions yielded fruit quality as good as hand harvesting, increased labor productivity by 15 times, and had the potential to reduce harvesting cost by half. Obstacles to commercial acceptance are the industry embracing stemless cherries as marketable, and compatible tree training. Dr. Matthew Whiting, Washington State University horticulturist, is cooperating to solve the tree-training issue.
Narrow-inclined trellises may also enhance the commercial potential for harvest aids. We developed concepts tailored to apples on narrow trellises that increased picker productivity by 20 percent. Manual sorting of defective fruit was possible, and may improve economics if unwanted apples are left in the orchard. Cooperating WSU Extension educator Dr. Dana Faubion has demonstrated that by using our continuously moving self-steer harvest aid as a labor platform, labor productivity for pruning and thinning can be increased by 30 percent and 19 percent, respectively.
Progress
When I started my career with ARS I was told that the fruit industry would not have a reliable labor force in five years. We certainly are closer to that prediction coming true now than ever before. As of December 2005, I was the last federal engineer (and had been for 15 years) conducting research on mechanical harvesting of fruit crops. One poorly funded state university project has been initiated to do robotic harvesting research on citrus.
I am glad to see the industry’s renewed interest in mechanization and automation. In my opinion, cooperation and mutual understanding between plant scientists and engineers are the most important components to insure success in orchard automation.
Leave A Comment