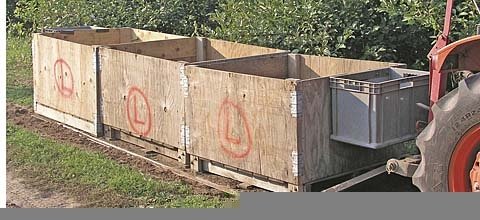
Darrel Oakes uses inexpensive sleds instead of trailers to move bins in the orchard. (Photo by Melissa Hansen)
Sometimes the simplest approach is the most cost effective. An inexpensive sled used for tree fruit harvest has reduced bruising and increased efficiency, says a western New York tree fruit grower.
The sled, a simple steel plate with a hitch to pull it, can be built for around $200, said Darrel Oakes of LynOaken Farms, Lyndonville, New York. He began using the sleds in his orchards several years ago after seeing similar equipment used in Australia.
Not only is the sled cheaper than bin trailers, which run around $6,000, but Oakes believes that they give the apples a gentler ride, reducing bruising. And because the bins are directly on the ground, the workers don’t have to step up on the trailer to empty their bags.
“The sleds glide over the holes and ruts instead of dropping in them,” he said.
LynOaken Farms is a few miles south of Lake Ontario and halfway between Niagara Falls and Rochester. The midsized, family operation grows 320 acres of apples, cherries, peaches, and wine grapes.
In an effort to improve efficiency in all areas of production, Oakes has developed an efficient harvest management system. It involves using sleds and paying workers piece rate for each bag of fruit picked, not a per-bin payment that is divided by the crew. Though the workers are willing to work closely together, they prefer to be paid individually.
Workers use six-foot ladders to reach the tops of trees, which are growing on dwarfing Malling 9 rootstock. The crew picks two rows of trees on each side of the bins as they move down the orchard rows.
Before he switched to sleds, the eight- to ten-member crews picked into the same bin and were paid piece rate. Bins were set out in orchard rows ahead of the workers.
Now, bins are delivered to a central staging area in the orchard, not dropped off row by row. A 60-acre block may have two to three common loading or staging areas. There is then a continual rotation of empty and full bins brought to and from the harvest crew.
“When you reorient your bin delivery system, the bins arrive to the workers just in time,” he said, explaining that his workers know the bin will always be there. “They don’t have to wait for an empty bin.”
Oakes added that there is less bruising and better quality control of color with his harvest system. The crew leader or supervisor can watch closely when fruit is being picked for color.
The work force at LynOaken is diverse and includes migrant Hispanics and African Americans who work in Florida’s citrus harvest. Oakes provides housing for 35 workers and usually has at least three crews going during harvest. Supervisors and crew leaders work year round. Several of their seasonal workers have worked there for more than 30 years and now live in the area permanently.
He estimated that each worker picks an average of 5,000 bushels during the season.
Leave A Comment