
Mark Zirkle above one of the apple packing lines at Zirkle’s Selah facility. (TJ Mullinax/Good Fruit Grower)
When Bill Zirkle’s father, Lester, was running the company, one of his primary customers was a Portland, Oregon, retailer that had one store with a large grocery department: Fred Meyer.
Bill and Mark Zirkle, Zirkle Fruit
“It’s an exciting time to be in the fruit business. We’re trying to find as many niches as we can.” Mark Zirkle.
“They had a unique relationship. Whenever Dad had a load of 280 boxes of exceptional stuff, he’d say, ‘Bring it down, Lester,’” Bill recalled.
Communication with the customers is just as important today as it was then — perhaps more so. Success requires meeting the demands of an ever-changing market.
Flexibility at the packing house level is crucial. “We never pack the same thing two days in a row anymore. That cuts into the packing house’s profitability and effectiveness probably, but that’s the way it is now,” said Mark Zirkle, Bill’s son.
At the same time, Zirkle Fruit’s sales desk, Rainier Fruit Co., has given the company front-row seats for watching industry trends and allowing the company to act on them, he said. “We’ve made our share of mistakes for sure, but it’s simply planting what the consumer wants.”
Zirkle and the growers it packs for all take a long-term look at the market, he said. “How we pack, what we pack, when. The customer doesn’t care if you are waiting for the market to go up on a specific variety. They just want it now. They want a supply. That takes a lot of teamwork, a lot of trust in each other.”
Earlier this year, Rainier Fruit signed on as a multi-year sponsor to the Boston Marathon, supplying some 75,000 organic apples to the event, and has since worked to expand the marketing effort to the entire running community with additional events and a #RunWithRainier social media campaign.
Roughly 85 percent of the company’s business is in the domestic market.
Zirkle Fruit has worked to stay ahead of consumer demand in part by installing the latest in packing technologies in its warehouses.
A dedicated organic line, built in 2015 and featuring an eight-lane sizer and color and defect sorter, reduced the potential for cross-contamination from conventional fruit.
A year later, the company built a new cherry warehouse that includes 85,000 square feet of packing area, a 48-lane sizer with defect sorting, and flexibility for different packaging options.
The warehouse with the organic line also has increased energy efficiency with insulated concrete walls, upgraded roof insulation, LED lighting and 336 solar panels that generate over 134,000 kilowatt hours annually.
Meanwhile, the cherry warehouse features 483 LED light fixtures for roughly a 40 percent reduction in watt usage, as well as 15 miles of underground conduit and piping and an underground glycol refrigeration system for a safer, cleaner work environment.
Several years ago, Zirkle Fruit replaced propane-powered forklifts with electric ones.
However, the new buildings were designed to eliminate forklift traffic from the floors entirely, both to improve food safety and employee safety.
Box-making equipment also now sits in a mezzanine above the packing room or off to the side — a decision that also improves food and employee safety, but was market-driven.
“I don’t think, 15 years ago, we would have envisioned that because, frankly, we didn’t need it,” Mark said. “Then, we had a box and maybe two or three lids. Now, there’s 15 different boxes, different-sized cartons — not only ours, but other private labels. We’ve had to face that this is a lot bigger operation and it needs to be in a much bigger area, not just on the packing room floor.”
Building a food safety team
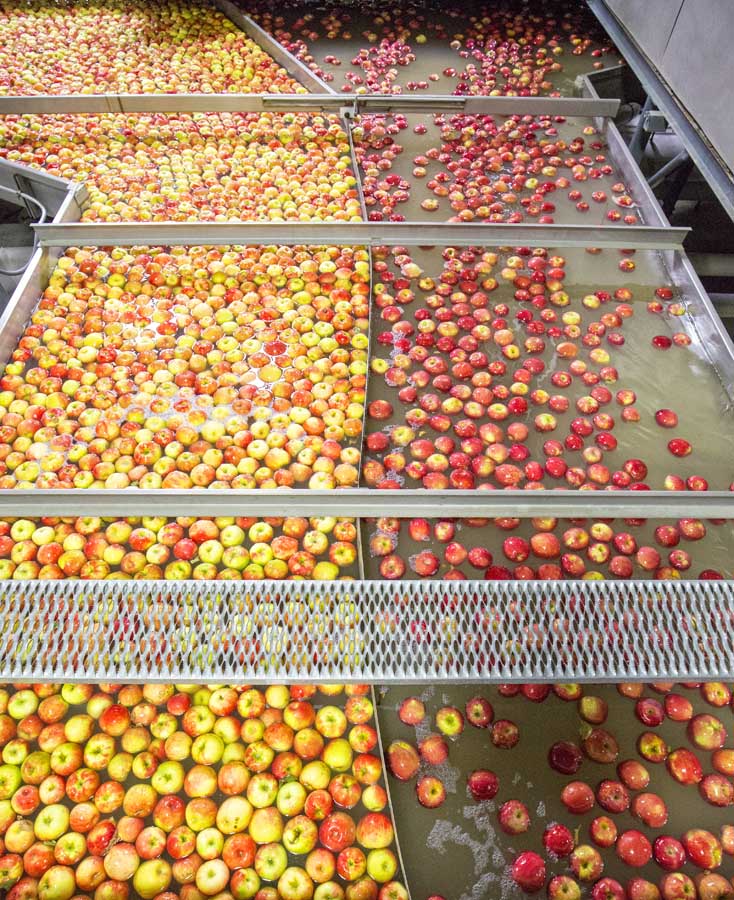
This Zirkle packing facility in Selah can run multiple varieties at the same time. (TJ Mullinax/Good Fruit Grower)
In terms of food safety, the company’s focus over the past year has been on improving practices and training, said Will Strand, director of regulatory compliance.
Particular areas of concern: brush pads, sort tables with soft surfaces that can be tough to clean without damaging them, and the water quality within the dump tanks, where water is changed daily.
The company has also recognized the need to recruit sanitation workers — a difficult task that requires communication, higher pay and rewards for experience and time on the job.
“The best way to recruit, and we’re still practicing and improving, is demonstrating the importance of the function to the whole process,” Strand said. “You can remove some of the human touches in packing, but sanitation is still one of those areas that takes a lot of hands-on work. You need workers who take pride in the work and know they’re part of the team.”
Mark agreed. “Cleaning the lines at 1 in the morning is probably not the most glamorous job in the industry, and until the last few years, we didn’t really give it much thought. Now that person is almost the most important in the company,” Mark said. “We have recognized it as a very critical position and are staffing for it.” •
– by Shannon Dininny, photos by TJ Mullinax
Leave A Comment