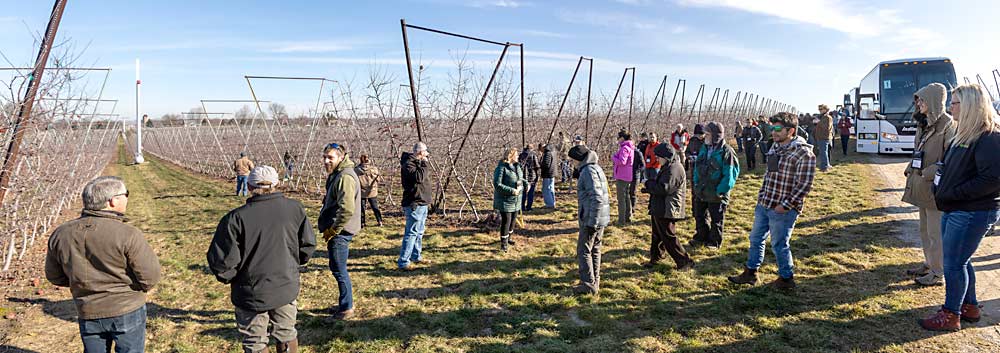
The International Fruit Tree Association held its 66th annual conference and tours in Grand Rapids, Michigan, in February, where it witnessed firsthand how Michigan orchards are building their resiliency and adapting to face future challenges.
Greater Grand Rapids is home to most of Michigan’s apple trees, packing houses and sales desks. There are more than 22,000 apple acres in the region, which produces about 80 percent of the state’s fresh crop. IFTA’s bus tour concentrated on what’s known as the Fruit Ridge, a series of gently rolling hills that stretch 22 miles north of Grand Rapids and 8 miles across. Tempered by Lake Michigan, about 25 miles to the west, the Ridge offers a unique climate for growing apples, said Amy Irish-Brown, sustainable solutions sales specialist with Valent and a former Michigan State University Extension educator.
IFTA visitors stopped at four fruit farms, all adapting in different ways to mounting industry challenges, reflecting their scale and target markets.
At Riveridge Produce Marketing, the largest fresh apple packer in the state and now one of the largest growers, they saw a vertically integrated company that continues to diversify its business operations. First, there was the cider-making facility, where Riveridge Cider Co. can press up to 50,000 gallons of cider per day, sold in all 50 states. The company’s priority is to source its cider apples from local growers, but if Michigan has a short crop, it will source from other U.S. growing regions, said account manager RJ Simons.
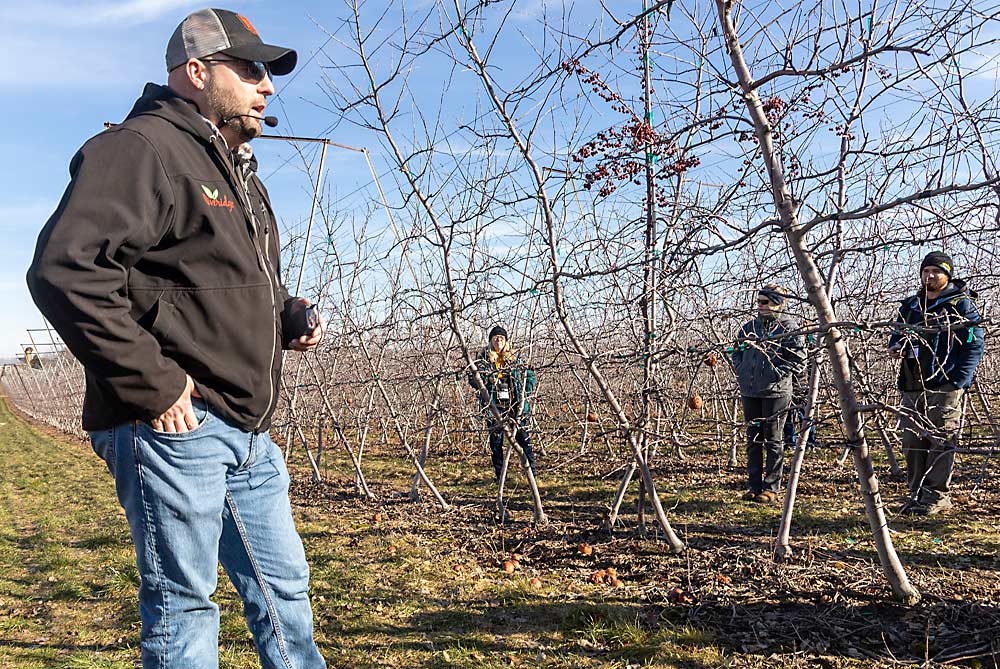
At the Riveridge facility in Grant, IFTA saw blocks of V-trellis apples and covered sweet cherries. Operations manager Justin Finkler said the blocks of V-trellis Aztec Fuji and Premier Honeycrisp visited by IFTA are spaced 12 by 3 feet and 12 by 2 feet on M.9-337 and M.29 rootstocks.
Finkler said Riveridge’s V system, probably the only one in Michigan, lends itself to uniformity and mechanization. Tying, training, pruning and other tasks are done by mobile platform, and Riveridge is moving toward mobile harvest, too.
The initial investment in the V system is heavy, but the company is working out the kinks and the trees are growing well. Future apple plantings will be on V-trellis, Finkler said.
Just across from the V-trellis apples, IFTA saw a block of fresh sweet cherries on V-trellis covered by nets from German company VOEN Covering Systems. The Skeena cherries on Gisela 5 rootstocks were planted in 2018. With the nets, they aim to protect the cherries from rain cracking, but mitigating frost and improving pollination also are factors, Finkler said.
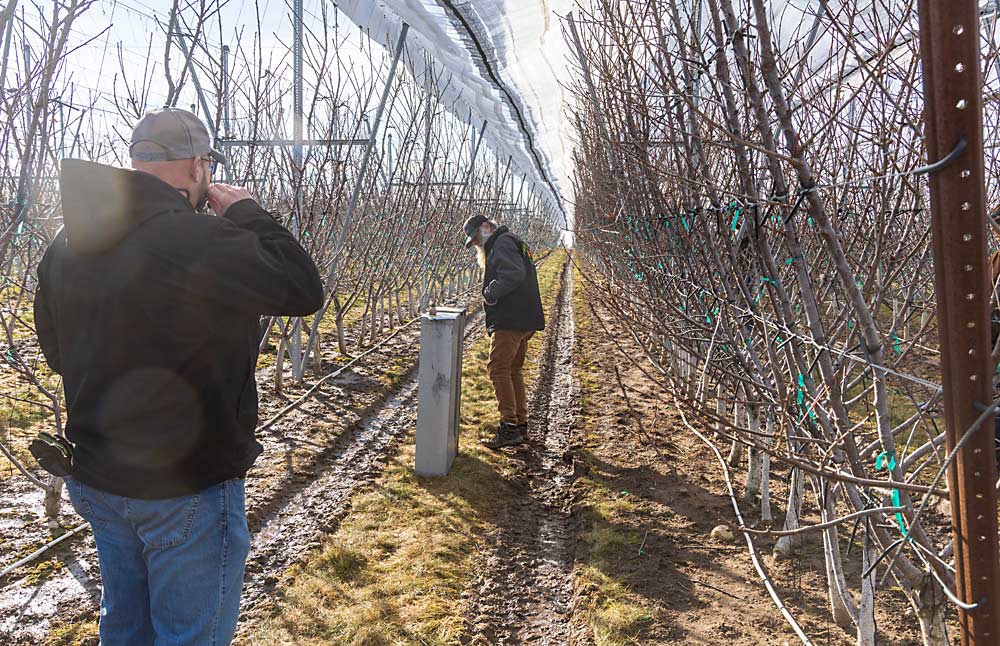
“Anybody that grows cherries in our area, rain is the biggest factor,” he said. “You can have the best crop that you’ve had in 10 years, but after half an hour of rain, it’s gone.”
MSU horticulture professor and cherry specialist Greg Lang said the narrow planar canopies of the V system allow greater sunlight penetration, which is essential if you’re going to grow covered cherries in the cloudy Midwest and East.
Infrastructure, cover and installation costs for VOEN netting range from $25,000 to $28,000 per acre, depending on orchard layout and features selected. The covers normally pay for themselves within three years, based on the European market, and have a roughly 10-year lifespan, said VOEN sales representative Jakob Fausboell.
IFTA visitors also saw two blocks of Riveridge’s certified organic apples, MAIA1 (marketed as EverCrisp) on G.41 and Ambrosia on G.41 and M.9-337.
To supply the growing demand for organic apples, Riveridge has partnered with organic grower Kyle Rasch to boost volume and offer the consistent supply local retailers need, Simons said.
“When customers go in and they see local organic products one week, and then next week it’s from another region, that’s just not great,” he said.
Organic apples generally fetch prices 25 to 30 percent greater than conventional apples in the fresh market — and can fetch double the price in the processing market.
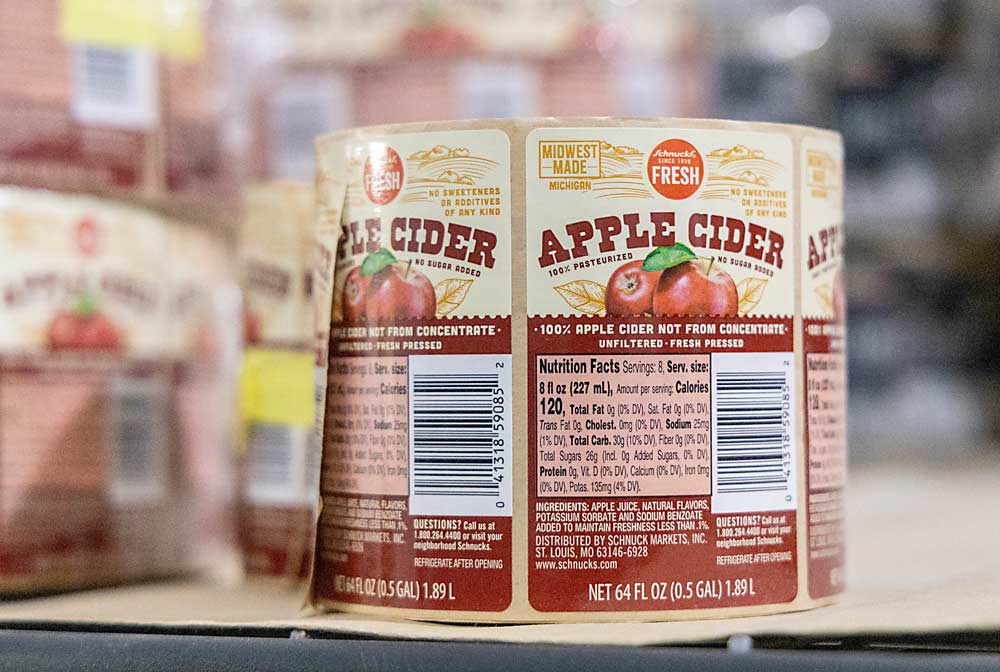
“It adds up, as long as you can maintain your packouts and get that finished product across the line,” Simons said.
Another company, Rasch Family Orchards, shared its efforts to modernize peach blocks. Growers Jake and Nick Rasch showed the IFTA tour their in-row V and perpendicular V growing systems, which they established to cut labor costs and improve fruit yield and quality.
IFTA visitors saw a block of in-row V peaches on a hill a little more than 1,000 feet in elevation, one of the tallest points in the surrounding region. The Bellaire peaches on Bailey rootstocks were planted 12 by 6 feet (with 1,210 leaders per acre) in 2020.
In the in-row V system, tree scaffolds are angled within the row, creating a planar fruiting wall, Lang said.
Jake Rasch said fruit size is more uniform using the in-row V system, and it saves labor: The number of pickings has gone from eight or nine down to five or six.
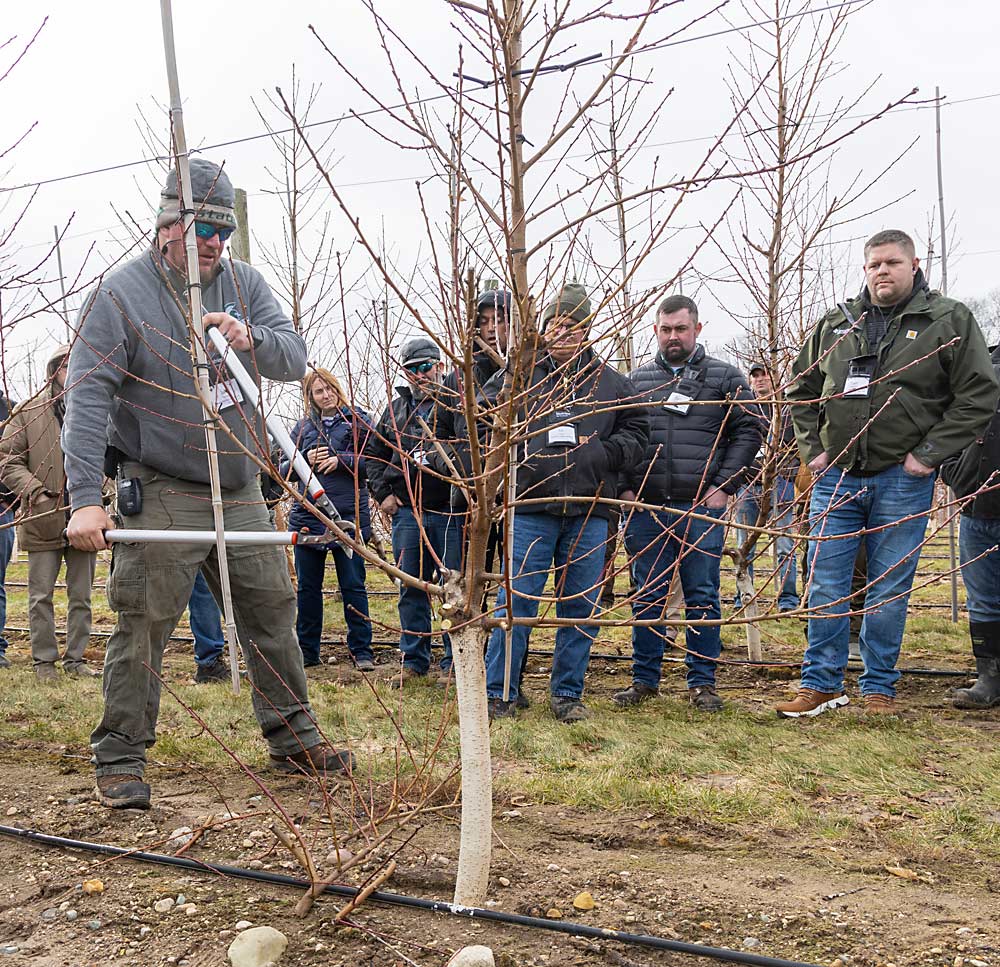
“Peaches are nothing but labor,” he said.
Applying the new plant growth regulator Accede (1-aminocyclopropane-1-carboxylic acid) as a chemical thinner reduces the number of pickings to four or five in the V system, and it also gives them less mixed maturity and more fruit per harvest, Jake said.
“For the last 10 years or so, we’ve been using string thinners for blossom thinning, but I’m really excited about using Accede now for all my blossoms,” he said.
Their average peach harvest on older systems is 350 to 450 bushels per acre. Using the V system and Accede, he anticipates an average harvest of 500 to 650 bushels per acre, depending on the variety.
IFTA also got a look at pruning and rootstock trials at a high-density orchard owned by LTI Ag Research, a private research company founded in 2021. LTI manager Tye Wittenbach said the company purchased the 80-acre orchard from grower Peter Nyblad last August.
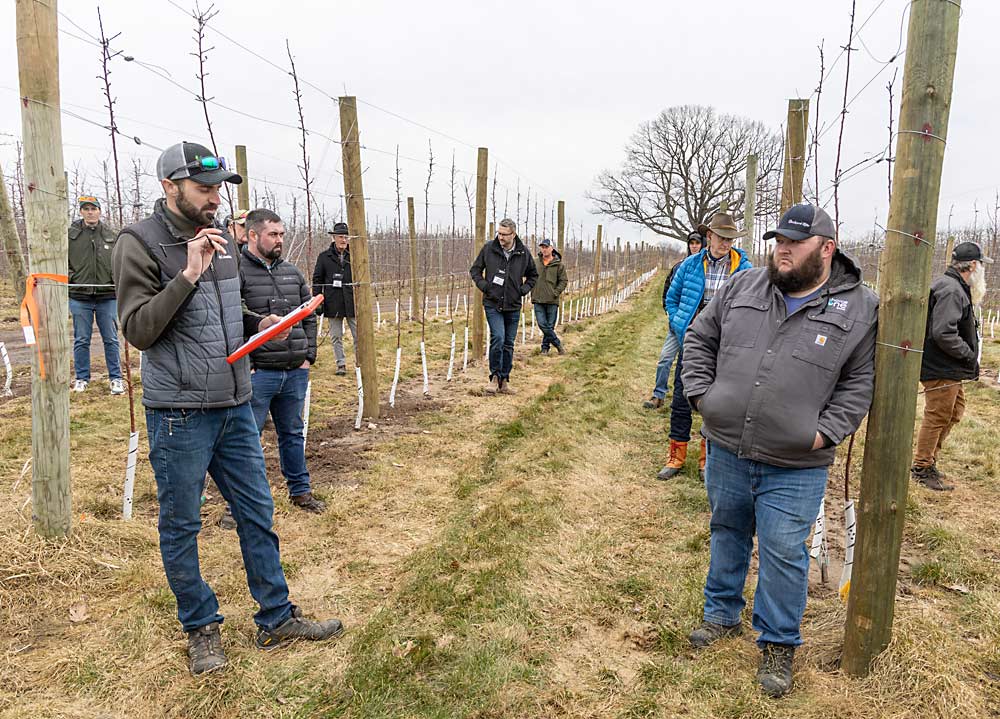
LTI conducts research trials for its grower-members, who pay a subscription fee to have exclusive access to the results. The company also conducts contracted research with manufacturers. LTI is always open to suggestions from its members, who help steer its trials in practical directions, Wittenbach said.
At the Engelsma family orchard stop, IFTA members saw modern, high-density apple blocks and an award-winning cider mill. Jim Engelsma Jr. and his daughter, Bridget, hosted.
The Engelsma family, which has been growing fruit on the Ridge since the 1920s, has 75 acres of apples, most of them drip irrigated. Sixty-eight of those acres are trellised Gala, Honeycrisp, Ambrosia and Jonagold grown for the fresh market. The other 7 acres are freestanding Gala, Golden Delicious and Jonathan grown for the cider mill’s use. They also have 2 acres of fresh-market peaches.
The cider operation, called Engelsma’s Apple Barn, has won the Michigan Apple Cider Contest a record eight times. The cider-making facility, which runs September through December, can produce up to 2,300 gallons a day. They mostly sell the cider at farm markets and stores in greater Grand Rapids, Jim said.
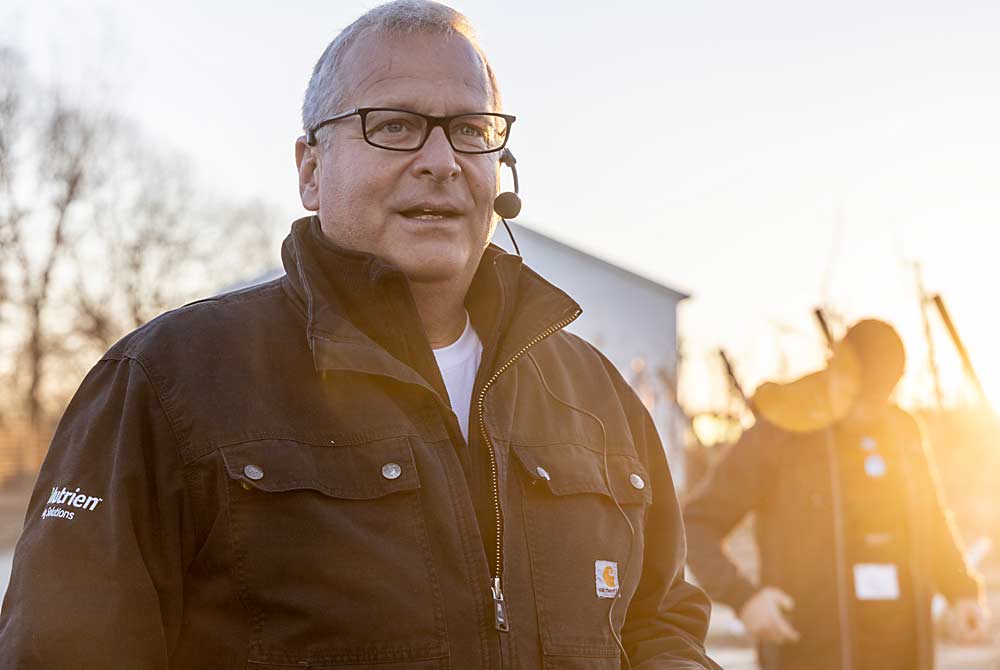
The family operation has remained resilient by diversifying and adopting efficient technology, Jim said.
“By being in the field monitoring all aspects of the growing cycle and implementing more technology into our system, we have been able to micromanage our production to promote higher yields and more consistent fruit quality,” he said.
—by Matt Milkovich
Leave A Comment