—story and photos by Ross Courtney
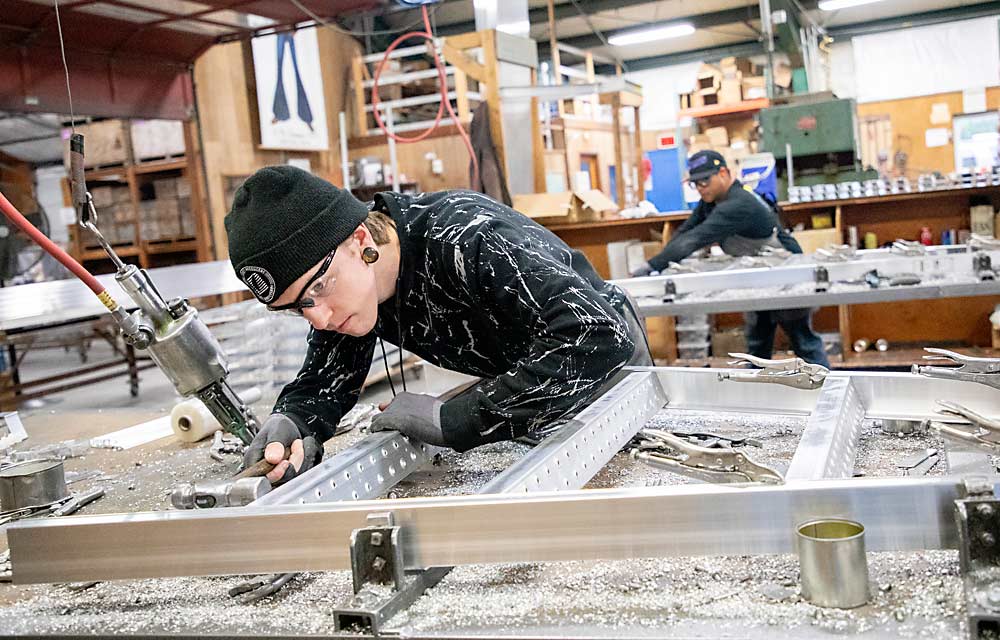
Richard Shenyer first learned of his company’s pending demise in the 1990s.
A fruit company field rep told him dwarfing trees, trellises and platforms would make his tripod orchard ladders unnecessary.
“I remember him walking in and saying, ‘Boy, we’re gonna put you guys out of business, everything’s gonna be picked from the ground,’” said Shenyer, owner of Grandview Ladders in Washington’s Yakima Valley. “And I remember being alarmed by that. And, of course, it never came to fruition.”
Last year, Shenyer had to table repairs to keep up with new orders, and he was due to move into a new shop this spring.
Business is still pretty good for Grandview Ladders and the handful of other U.S. companies making ladders for the tree fruit industry, despite the dire forecasts they’ve heard for decades. Good Fruit Grower interviewed six across the country to hear about the state of the original orchard technology. Ladders got shorter, but sales have stayed relatively steady. Most companies have made recent capital investments in precision tools and shop space.

“Until they master the art of levitation, there’s always going to be a need for some ladders,” said Greg Panella, third-generation owner of Stokes Ladders in Kelseyville, California.
Growers agree.
For one, not all trees are planar enough to accommodate platforms, and not all growers have the scale to budget for them.
“For us to offset the cost of the platform, we just don’t have the acreage,” said Eladio Gonzales, farm manager for G.S. Long Co.’s two orchards in Naches and Cowiche, Washington, which are each about 25 acres.
Platform efficiencies don’t always manifest evenly, either. They cause speed imbalances between employees, sometimes inflating the federally mandated piece-rate earnings of the faster workers beyond economic sense for their employers, said Dan Plath, president of orchard operations for Washington Fruit and Produce Co. in Yakima, one of the state’s largest vertically integrated growers.
Washington Fruit uses platforms for pruning and thinning but is still trying to make them work for harvest, he said.
“It seems like a no-brainer to all of us,” Plath said. “In practice, it just hasn’t played out that way.”
Orchard ladders are a small segment of the total ladder market, said Michael Van Bree, vice president of the trade group American Ladder Institute.
Orchard ladder companies top out at roughly 12,000 ladders produced per year. The largest companies in the trade group, which don’t typically make orchard ladders, ship 10 or even 100 times that, said Van Bree, also director of product safety and engineering of Louisville Ladder in Kentucky.
Historically, ladders have been regional industries, partly because they don’t ship well. Orchard ladders, most made by people from orchard families, are even harder to ship because they flare at the bottom. Manufacturers have overcome that to meet demand and distribute all over the world through dealerships, but they tend to stick with the customer base they know.
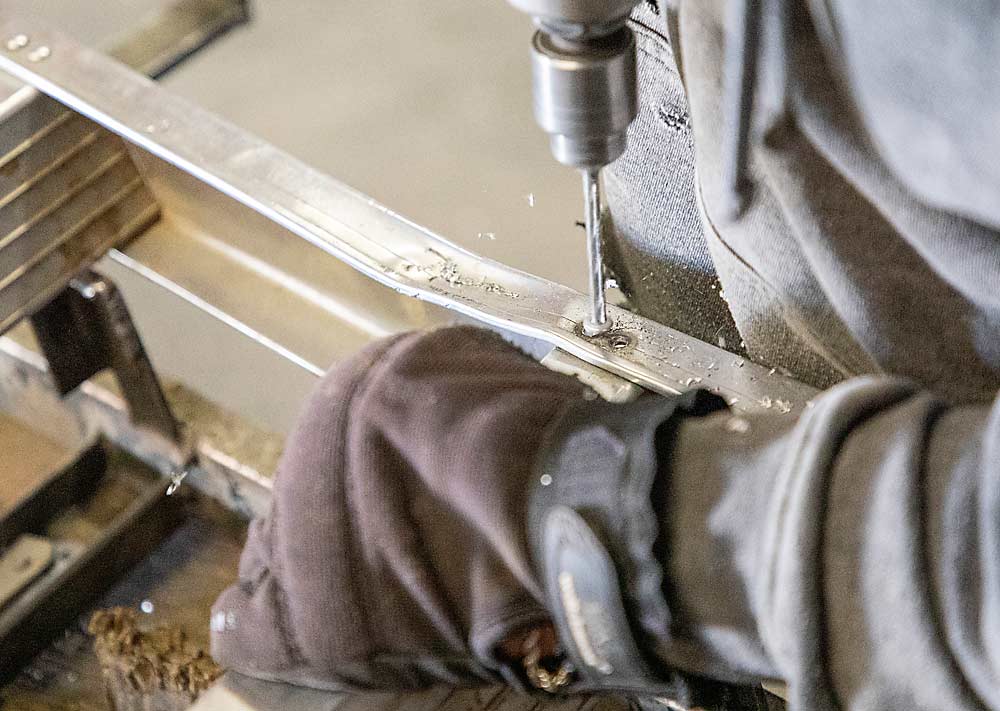
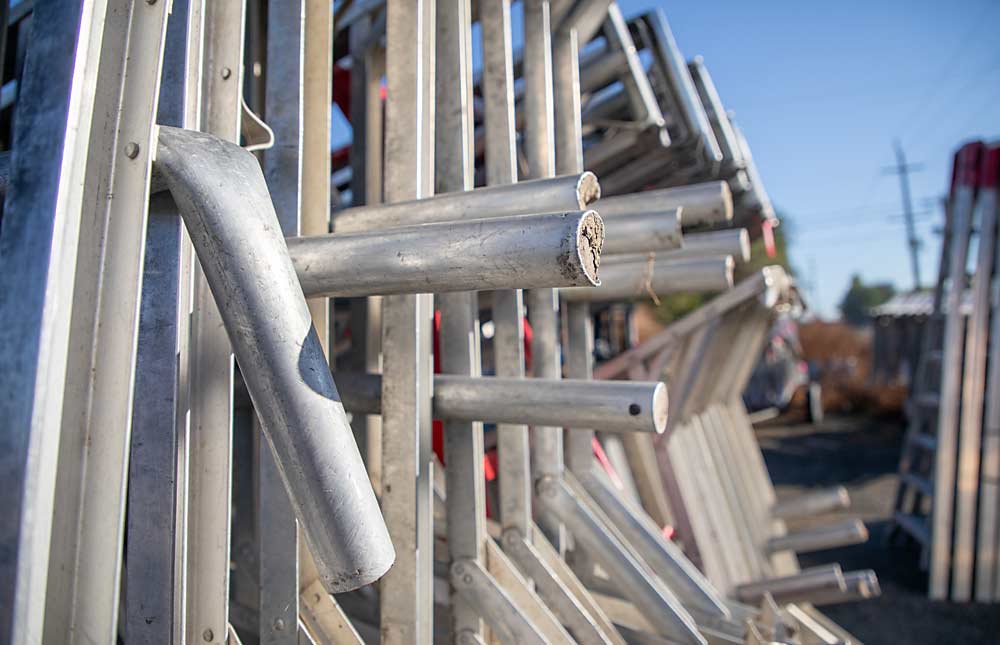
Hand labor
Like the industry it serves, ladder construction involves mechanized tools but still requires a lot of hand labor.
Tallman Ladders of Hood River, Oregon, has new saws and a new pneumatic rail punch, but they still bend their own brackets and fasten their own rivets on jigs and tables they built themselves.
“We’ve been doing it so long that way,” said Brenda Tallman-Kaiser, vice president and a third-generation owner.
She met last year with an Oregon automation company but walked away unsure if the proposed robot could accurately fasten a step to a side rail. It also seemed cost prohibitive.
The company usually employs about eight full-time workers, including a few ladder builders paid per ladder, after training.
Tallman-Kaiser’s grandfather, orchardist Bob Tallman, started the business in 1954. Within a few years, he expanded to the rest of the Northwest, nation and even overseas. Today, the Hood River Valley makes up only about 5 percent of the company’s sales.
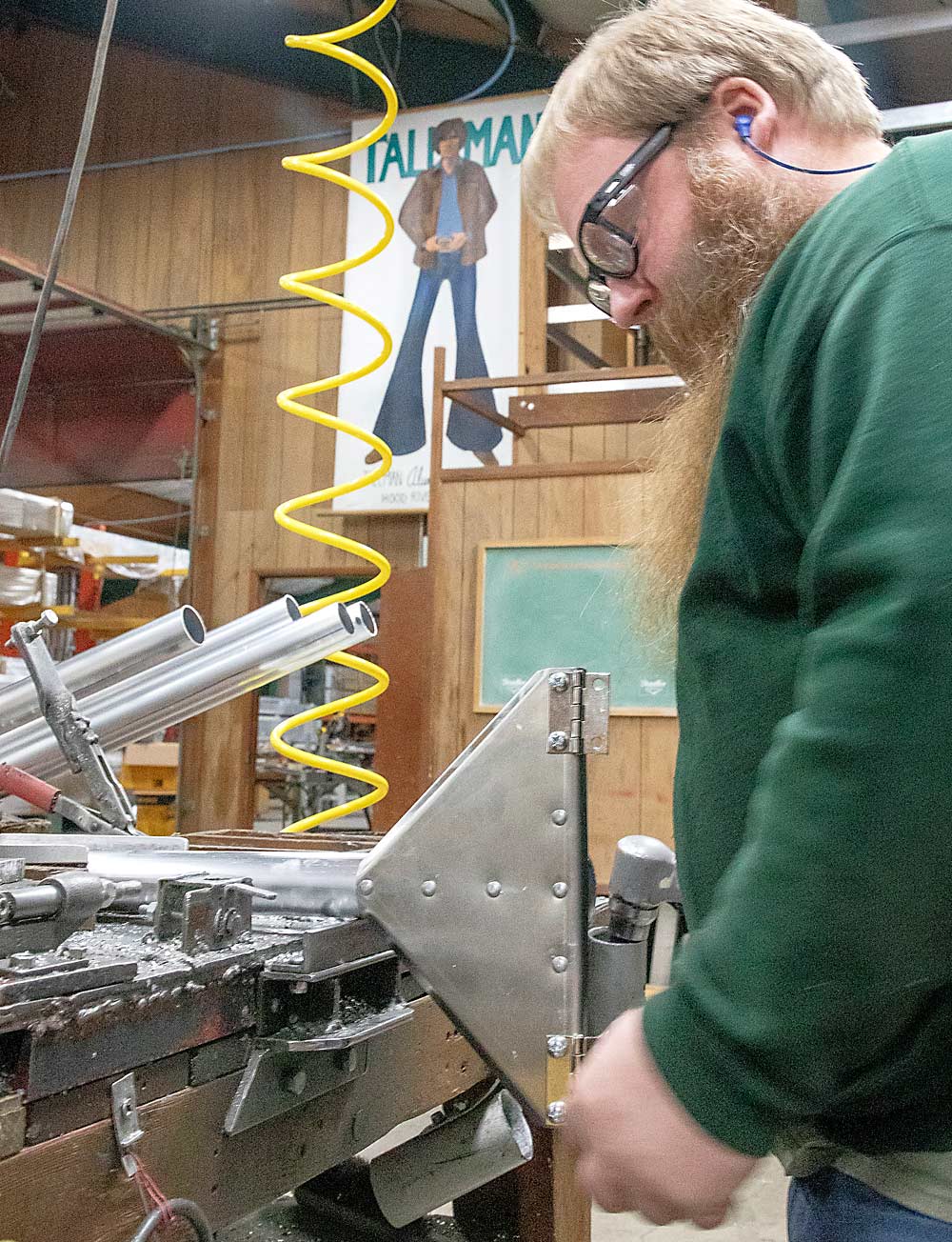

Dependable Ladder in Yakima has seen a slight decline in ladder orders over the years but not the end of demand some predicted, said Brad Nieman, who took over in 2003 from his father, Bryce, an orchardist who bought the business in 1991.
Today, Brad spends more time repairing ladders than building new ones. But orders have skewed larger in the past five years or so, a reflection of consolidation in the orchard business, he said.
Baldwin Apple Ladders of Maine builds only wooden ladders, about 1,000 per year.
Aluminum is expensive and slippery, said founder Peter Baldwin, who grew up on a New York orchard. He also considers treated wood more resilient. Baldwin and his younger partners spend winter months collecting and drying timber — bigtooth aspen for rectangular rails and ash for rungs.
His niche within a niche business has shrunk roughly 10 percent since the heyday of the 1990s, he said.
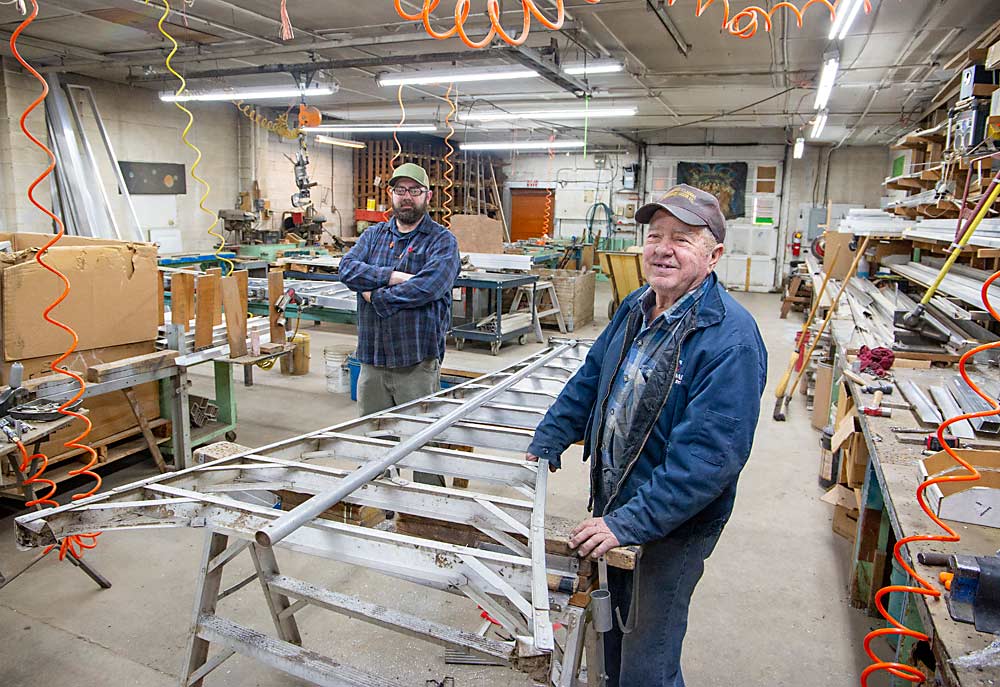
California
In California, where labor contractors purchase orchard ladders by the thousands, the leading companies are Stokes and Strathmore Ladder, which both share history with Grandview Ladders in Washington.
Stokes was founded in 1966 by Russ Stokes, a North Coast pear grower and engineer. He started selling to neighbors but expanded through the 1970s, licensing his design to Strathmore, near Tulare, California, and establishing the shop that would eventually be named Grandview Ladders.
Today, Stokes’ grandson, Greg Panella, owns the Kelseyville, California, business.
Ag sales have slowed some over the years, Panella said, but he has branched out to other types of ladders, including rolling winery ladders. The company makes about 10,000 orchard ladders per year, shipping to farms in the United States, Chile, Saudi Arabia and elsewhere.
As for Strathmore, they have their own ladder design now. Owner Garry Wilson has made his own capital investments in production space and automated saws, and he keeps more year-round workers instead of spiking with the season — to reduce the cost of training.
Wilson notices ups and downs that follow the economic cycles of farming, but he doesn’t blame platforms. He has shifted more to citrus, where growers use ladders mostly just for harvest, he said. The southern Central Valley stone fruit industry uses ladders for pruning, thinning and picking, causing more wear and tear and, therefore, more need for replacements.
Robotic harvesters have now started trials in California’s stone fruit orchards, but Wilson downplayed that for now, too.
“That will be a problem for the next generation,” he said. •
Ladder safety caveats
Ladder falls top injury list, but look closer.
—by Ross Courtney
General wisdom says platforms are safer than ladders.
“The most injurious object in our program is the ladder,” said Jeff Lütz, safety director for the Washington Farm Bureau.
But when you dive into the data, it’s hard to prove the theory that removing those ladders and replacing them with platforms would reduce injuries.
Washington orchards see more than 800 ladder falls per year, according to the state’s Department of Labor and Industries, accounting for almost one of every four injury claims between 2012 and 2021. That’s by far the biggest source of claims.
But there are caveats to those stats, said Todd Schoonover, industrial hygiene research manager for L&I.
“There is a category for falls from ladders,” Schoonover said. “There is no category for falls from platforms.”
Each L&I claim report contains a narrative text that may or may not use the word platform. For example, an investigator or physician might report a fall from a “scaffolding” as a synonym for platform, while platforms themselves usually have ladders.
Even if claim reports did count platform falls, those would have to be compared to hours of use, said Dan Plath, president of Washington Fruit and Produce Co. in Yakima. Ladder injuries could be more common than platform injuries just because ladders are more common, he said.
Anxious to cut down on all injuries, orchard ladder manufacturers are seeking more active roles in safety trainings and standards.
Brenda Tallman-Kaiser of Tallman Ladders in Hood River, Oregon, has offered to help orchardists and industry groups with training. For example, her ladder safety stickers warn users to keep their belt buckle within the side rails to prevent tip-overs, one of the more common causes of ladder falls.
Tree fruit growers and industry groups have provided ladder training for decades. Some states, including Washington, Oregon and California, require ladder safety training.
In 2022, in response to grower requests for a modern version, the Washington State Tree Fruit Association released a free video titled “Above the Trees,” covering safe ladder use. Certified and grant-funded by L&I, it’s available in English and Spanish. It covers tips such as inspecting ladders for broken parts, keeping three points of bodily contact and not jumping down to save time.
It covers platform safety, too.
Greg Panella, owner of Stokes Ladders in Kelseyville, California, recently discussed representing orchard ladder manufacturers with the American Ladder Institute, a Chicago-based trade organization that helps write American National Standards Institute safety standards. That list currently includes categories for portable wood, aluminum and fiberglass ladders, but tripod ladders are not addressed.
The goal is to keep everyone safer, but getting involved might also help rein in escalating insurance costs, Panella said.
Accident claims often list ladder makers as defendants, he said. Even dubious accusations drive up premiums when parties choose to settle.
“It’s becoming an untenable position,” he said.
Peter Baldwin of Baldwin Apple Ladders in Maine recalled paying $600 a year for insurance in the 1980s. Today, it’s $25,000.
“For a small business, that’s pretty crippling,” he said.
Michael Van Bree, vice president of the American Ladder Institute, has investigated thousands of accidents with all kinds of ladders in all kinds of workplaces, including orchards. Almost always “pilot error” is the root cause, not a failure of the ladder, he said. There are times when a ladder is missing a rivet or has a clumsy welding joint, but “that is far and away the exception,” he said. •
Leave A Comment