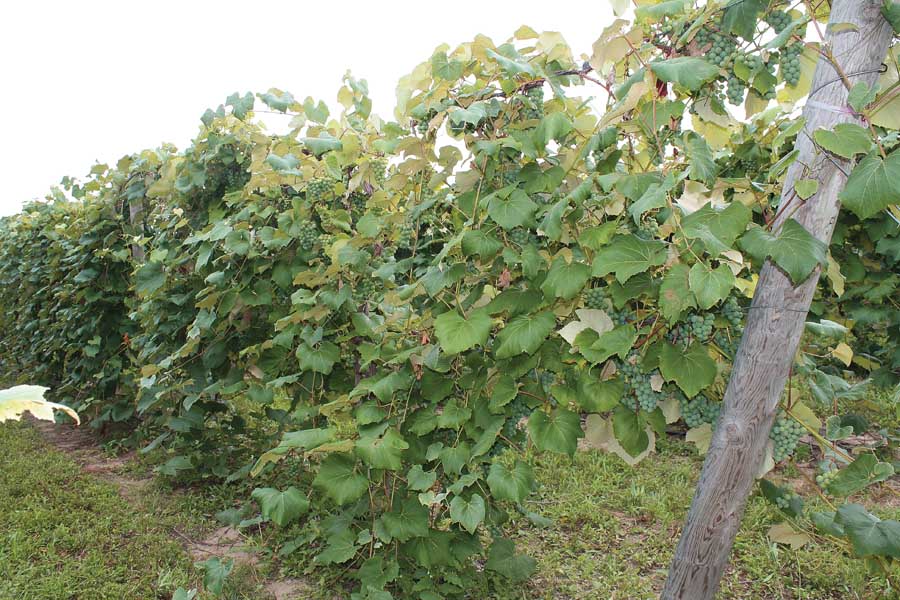
Concord grapes are borne at two levels—from the cordon arms on the top wire at seven feet and from arms on a lower wire, at four feet. (Richard Lehnert/Good Fruit Grower)
Five years after Dr. Tom Zabadal planted his experimental two-tier cordon system for Concord grape production, it seems to be doing what he wanted—producing higher yields without sacrificing quality.
Last year, it produced 8.3 tons per acre, while the system growers conventionally use yielded 3.2 tons. Brix level was 16.2° no matter which system was used.
Speaking to growers at the 26th annual Viticulture Day at the Southwest Michigan Research and Extension Center in Benton Harbor this summer, Zabadal said he started his research after realizing that Concord grape growers were in for a real profitability challenge that might last a long time. Grape prices were headed down to the low $200-per-ton range, while costs were running $1,000 an acre.
“There was no prospect of better prices, so the solution needed to be higher yields,” he said. He set out to change the existing system enough to get those higher yields without changing it so much that existing machinery—sprayers and harvesters—would have to be replaced.
In the standard way of doing things, growers plant vines six to ten feet apart—eight feet on average—in rows about nine feet apart, and develop a trunk supporting a cordon made up of two arms that stretch along a wire at six feet.
They grow plants on their own roots and seldom use grafted rootstocks.
He developed the new model based on three changes. Alley width is somewhat narrower at eight feet. The top cordon wire is raised a foot, to seven feet. A second wire is added at the four-foot level, and two arms there form a second cordon trained from the same root. Each vine has four arms instead of two.
Instead of producing the entire crop on one cordon at six feet, the crop is produced on two cordons at four and seven feet. “I like the Scott Henry training system as a vertically divided training system for wine grape production, and I thought this two-tier cordon training system could be a good fit for Concords,” Zabadal said.
In addition, he planted the vines on the somewhat more vigorous SO4 rootstock. “You need a large vine to produce a large crop,” he said.
In his tests, each change added to yield.
Last year, the top wire-only cordon produced 3.2 tons per acre. When the SO4 rootstock was added to that system, yields increased to 4.6 tons. When the second cordon was added without a change in rootstock, yields went up to 6.5 tons. And when the two-tier system was used with the SO4 root, yields increased to 8.3 tons per acre.
The two-tier system contained more grape clusters per vine, but cluster weight did not change unless the rootstock changed.
The SO4 vines produced clusters that were larger—about 110 grams per cluster compared to about 90 grams on the own-rooted vines. The number of clusters about doubled with the second cordon tier, rising from about 45 to about 90.
The reason seven feet was chosen as the new height was because that’s the height an over-the-row harvester can handle. “At the time we started this experiment, we could not get a taller machine,” Zabadal said. Since then, a taller one has become available, he said.
In developing the system, he also wants to make sure it is adapted for future mechanization. Michigan State University has also developed a mechanical shoot-positioning machine, which is now being commercially produced, that combs the hanging Concord shoots downward. The system also has to fit with mechanical pruning.
Will his two-tier model be sustainable into the future? “We’re pretty pleased where it’s at,” Zabadal said. “It seems pretty decent so far, but its long-term performance is uncertain, and that’s why we call it an experiment.” •
Leave A Comment