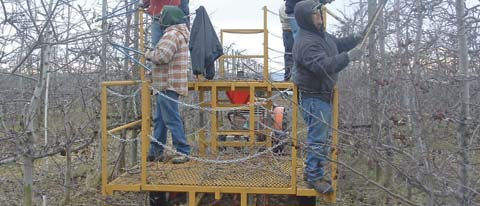
Gilbert Orchards in Yakima, Washington, in their first full season with orchard platforms, will use them for pruning, thinning, training, and pheromone application. They have already combined some orchard tasks into one pass with the platforms, like pruning and tying strings for tree training.
Photo courtesy of Rankin Equipment Company
Orchard platforms, as a tool to reduce the use of ladders to perform tasks like pruning and thinning, are moving from the research and demonstration stages to application as more orchardists adopt their use.
An equipment manufacturer in Yakima, Washington, is making custom-built platforms to accommodate individual grower needs at an inexpensive cost, utilizing equipment already owned by the grower.
Throughout the last few decades, creative and innovative growers have designed their own orchard platforms made out of bin haulers, flatbed trailers, or bin trailers. Some have used cages for workers or safety harnesses attached to a bar in the middle to allow mobility on both sides of the platform, while others are using platforms to help with harvest tasks. European and U.S. manufacturers also make self-propelled harvesting aid equipment for pruning, thinning, and harvesting.
Grower-designed
About two years ago, Larsen Fruit Company in Selah, Washington, tried their hand at making an orchard platform prototype that would fit over a bin trailer and be pulled by a tractor.
“We’re not engineers or manufacturers,” said Dave Jacques, orchard manager for Larsen Fruit. “We just used some farmer knowledge to put it together.”
They showed their prototype to a local equipment manufacturer, and that started the process, he said.
“We were looking for something that wouldn’t cost a lot of money and could utilize equipment that we already have,” Jacques said, adding that tractors and bin trailers sit idle for much of the year. “We thought that if we could clamp it somehow onto a bin trailer, that it would make our equipment more efficient.”
Since their first model, which was built to be stationary and is not adjustable, Larsen Fruit began working with Northstar Attachments, LLC, a Yakima-based manufacturer specializing in tractor attachments, to fine-tune the orchard platform prototype. Northstar, owned by Rankin Equipment Company, also of Yakima, already had proprietary bin trailer products designed for the Pacific Northwest. It was a natural to add orchard platforms that fit over bin trailers to its product list.
The platforms made by Northstar cost around $6,000.
“They tweaked our original design and made wings that can extend out so workers can reach further into the canopy and get into vertical fruiting walls,” Jacques said. Larsen Fruit is using five orchard platforms-their own prototype and four that were built by Northstar-in its orchards this year.
About the same time that Larsen Fruit was tinkering with its own design, another Yakima Valley orchardist had the same idea of trying to utilize bin trailers for the base of an orchard platform.
Tex Reid of Gilbert Orchards said their initial platform concept was to attach plywood on top of bins and move it through the orchard on a bin trailer. “It got the job done,” he said, but they knew they could improve on the idea. They met with Rankin’s Ted Bellamy and Wayne Hahn to design something that could fit their existing orchard structure.
Reid knew that he wanted a platform with two levels-30 inches off the ground for the first deck and 60 inches for the second tier. Pruning loppers are 30-inches long, he explained. Someone standing on the ground can reach the bottom level of the tree. The first platform section, 30 inches higher, allows someone to reach the midsection of the tree, with 60 inches from the ground at the upper deck, allowing one to reach the upper tree section.
He also knew that the platforms needed to be adjustable in width to accommodate their different widths of tree rows. Reid wanted the platforms to be able to go from three feet to eight feet wide with floor treads that could come off for the narrower widths.
“I live in the middle of a hop field,” Reid said, adding that for years he has watched hop workers tie up the vines from platforms. He sees platforms being used for all kinds of orchard tasks beyond pruning and thinning-tying and training shoots to trellis wires, attaching pheromones to tree branches, putting up nozzles and tubing for overhead cooling, and even attaching ribbons and tape for bird control.
Once the Northstar units were delivered to the field, the learning curve began. Several features were improved immediately, like the steel grating on the floors that was enlarged so that thinned fruit would drop through the grating and not bounce back into the tree or be hazardous for the workers on the platform.
Orchard structure
The newer blocks planted at Gilbert Orchards are trained to a vertical axis or V-trellis that have a planar wall of fruit. Platforms work well in those blocks, Reid noted. But their older blocks-with row spacings up to 20 feet wide-aren’t suitable for the platforms, and ladders must still be used.
Jacques said that they are modifying some of their older orchards-cutting out big wood-so that the platforms can be used. Pole saws are used to cut out big branches, with a crew on the platform and a ground crew pruning the trees to achieve a “block” shape.
Larsen’s newer orchards are planted to high density spacings and trained to V-trellis, vertical wall, or central leader systems-orchard systems in which the platforms work well.
Labor savings
It’s been well documented that workers are more efficient when they don’t have to move ladders around the orchard. Data collected by Washington State University, Oregon State University, and the Washington Tree Fruit Research Commission show that efficiencies gained from tasks performed on a platform compared to on a ladder range from 19 percent to 67 percent, depending on the orchard task. Research was conducted in apple and pear orchards where tree canopies formed two-dimensional fruit walls, some vertical and some angled.
“Between the ground crew and platform crew, we’ve essentially eliminated ladders in our orchards,” Jacques said, adding that the elimination of ladders is a major safety advantage, with the potential to reduce accidents and lower workers’ compensation ratings.
At a minimum, he said, they have saved at least 20 percent on average in their blocks by using the platforms instead of ladders for pruning. In some blocks, the savings are even higher. For example, he found that with the platforms, crews can prune a vertical trellis block for 28 cents per tree compared to 40 cents per tree with ladders.
“When you have 1,000 to 1,400 trees to the acre, those savings add up in a hurry,” he observed.
Larsen Fruit plans to use the platforms this season for other orchard tasks like thinning and applying codling moth pheromone dispensers.
Reid is also pleased with the initial savings in pruning costs they have achieved. In a mature Granny Smith block trained to the Tatura system, they pruned the entire block with a ground crew, at a cost of $96 per acre, followed by two platform crews with six workers each, that tied suckers and shoots and pruned the rest for an additional $156 per acre.
“We pruned and tied the block for $252 per acre,” he said. “The cost with ladders would probably be double that amount.”
He is eager to use the platforms this year to tie the pheromone dispensers for codling moth in the tops of trees. “We’ll be able to go three to four miles per hour in a block and get it done in a day instead of two weeks.”
The only major disadvantage to the orchard platforms cited by Jacques is that they can’t be used in all of their orchards. Ladders must be used in orchards that are on sloping ground.
Also, in some of the older orchards, turning at the end of the rows can be tight to maneuver with the platforms.
“There will always be need for a ladder crew because of the different ground situations that we have our orchards on,” he said. “But with our variety of conditions, we can pick and choose where we send the platforms or ladders. If ground is too wet for platforms, we can always fall back on the ladders, or if the outside rows are too steep, the ladders can go there while the platforms are used inside the orchard.”
Leave A Comment