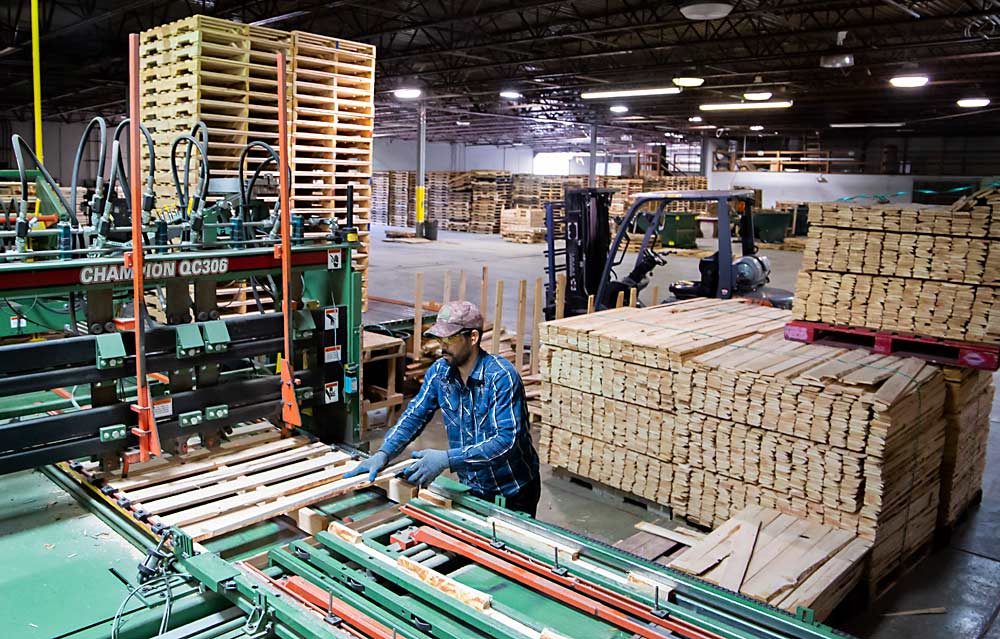
A lack of containers has delayed apple orders by weeks. Pear processors can’t get enough aluminum cans. Pallets cost triple what they did last year.
The lingering economic effects of the pandemic and tangled webs of global trade have left the tree fruit industry short of critical packaging and shipping supplies for 2021.
“There’s not much that’s not in short supply,” said Steve Reinholt, export manager for Starr Ranch Growers in Wenatchee, Washington.
Industry groups have chimed in to raise awareness of the problems and warn their members to brace themselves; some of the shortages and high prices may continue for the rest of the year. Even Janet Yellen, the Treasury secretary, predicted a similar timeline. At the end of May, the consumer price index showed an increase of 5 percent over the previous 12 months, a jump in inflation not seen since 2008.
All the supply shortages raise the cost of production, said Kyle Mills, packing manager for Apple King of Yakima, Washington.
“Everything is getting inflated right now except for one thing, and that’s the price of apples,” he said.
Pallets
The pandemic caused a spike in demand for lumber and other building supplies, as consumers spent would-be vacation money on home renovations or new houses. That leaves less lumber and nails for pallets.
“Mills just can’t keep up,” said Jobhan Randhawa, operations manager for A-1 Pallets, a Kent, Washington, company with facilities in Yakima, Auburn and Portland, Oregon.
Prior to the pandemic, new pallets ran $9–$13 each. Those same pallets in May were about $24–$35 each, depending on materials, Randhawa said. Rebuilt pallet prices have risen proportionally.
Though many pallets are custom-made, A-1 has been restocking its inventory to meet demands. Managers received some price pushback from shippers earlier in the year, but people have become used to it already, Randhawa said.
“There’s no one out there with a secret stash that could sell it cheaper,” he said.
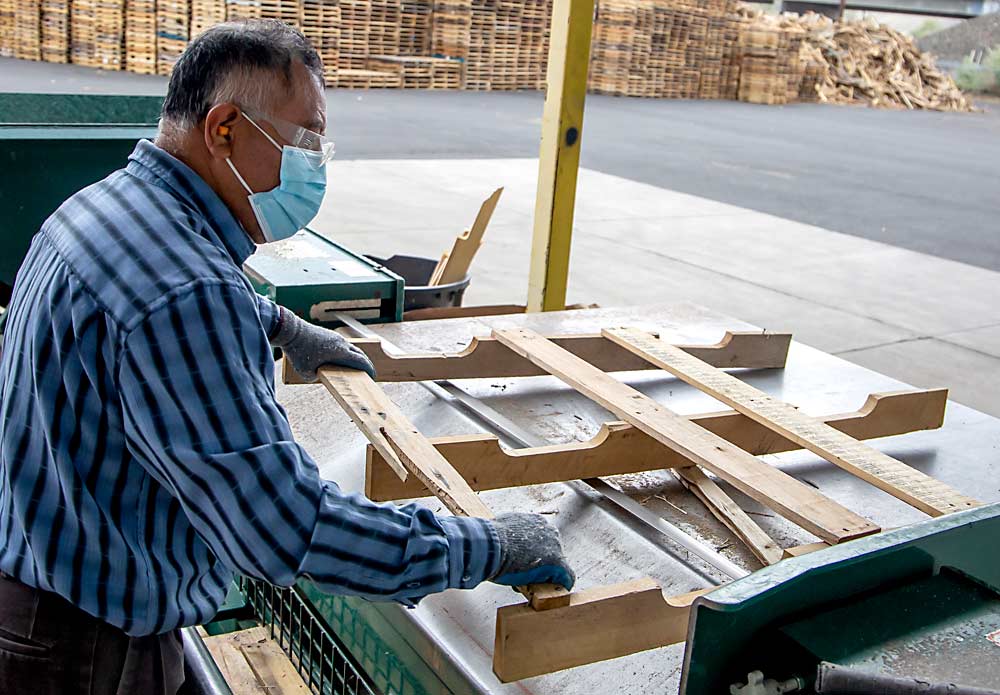
Tree fruit shippers use 75 percent new pallets, as opposed to rebuilt ones. New pallets completely dominate in export markets, which break them down and use them for other things. They never come back.
The United Fresh Produce Association also blames a rise in fuel costs, labor challenges and a shortage of available trucks and resin used to make plastic containers and pallets.
“At this time, expectations are that the pallet shortage will continue for months, perhaps for the balance of 2021,” the organization said in a May news release.
Lumber prices also affect bins. Ray Keller, one of the owners of Apple King, said his company paid $52 per plywood bin in 2020. By March, that price had jumped to $72. In late May, that was up to $148.
“We’re not going to buy any this year,” Keller said.
Shipping containers
In late April, freight industry newsletter American Shipper predicted a shortage of shipping containers will continue into 2022.
A lack of production of new containers in China and pandemic-related bottlenecks at U.S. ports are causing the shortage, as well as demand for consumer goods so high that shipping companies off-loading electronics and clothing at U.S. ports prefer to return to Asia empty-handed rather than make the usual stop in Washington or British Columbia for a load of apples or wheat.
“Everything is a really big mess right now,” said Reinholt of Starr Ranch.
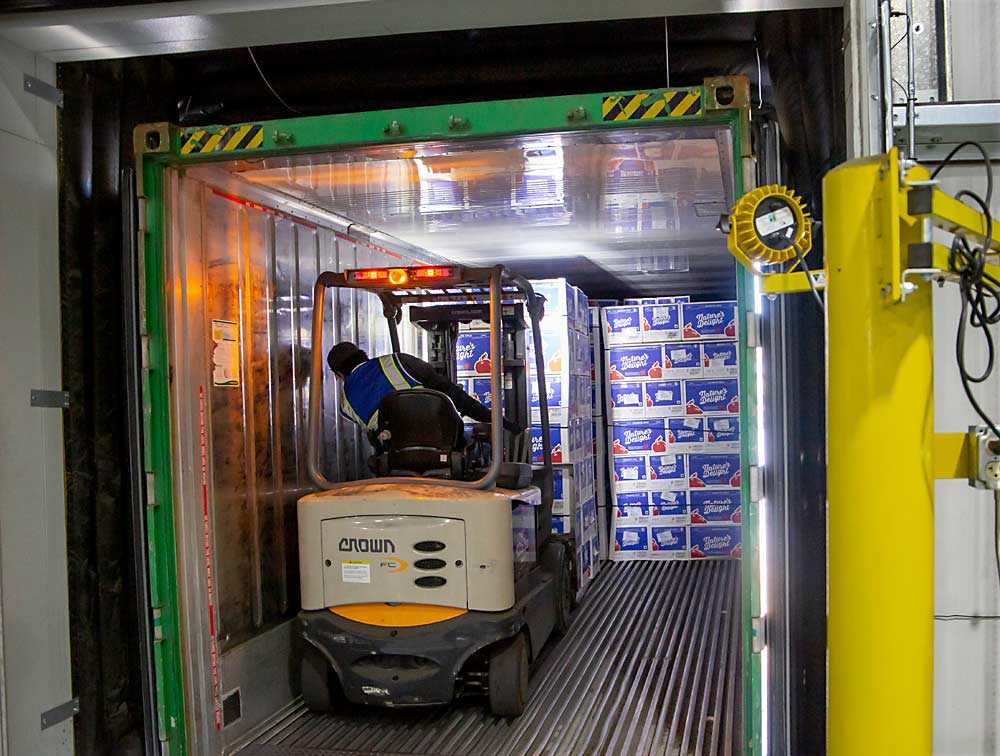
When containers become available, shippers often receive little notice and must scramble to line up a trucker, build loads and pay thousands more in freight costs. If they miss the short window, vessel companies impose financial penalties, according to a letter from nearly 300 agricultural commodity groups to Pete Buttigieg, the Transportation secretary. They estimate losses of $1.5 billion.
The letter asks Buttigieg and other federal authorities to investigate what they consider a violation of maritime agreements. The Washington State Tree Fruit Association, the Northwest Horticultural Council, Western Growers Association and the North American Blueberry Council were among the signers.
Dispatching truckers to available cargo containers this year is a lot like coaching children’s soccer, said Stu Johnson, owner of Four Ports Transportation near Seattle, Washington: Throw out a ball and let the whole swarm chase it.
“That’s kind of what we do, we just jump from ship to ship to ship,” he said.
He’s lost some drivers to other industries, such as waste disposal and construction, where loads are more predictable and consistent.
However, he suspects the ship backup will ease by September or October, once ports have had more time to clear congestion. Last year, as the coronavirus spread, longshoremen up and down the West Coast called in sick. Contracts prevent dock operation companies from hiring temporary workers, leaving fewer people to unload the surge of incoming vessels. At one point, 41 freighter ships were waiting in line outside the Los Angeles harbor. That has eased, but the backups have just rippled to other ports since then, Johnson said.
Among them are Seattle and nearby Tacoma, where most of the country’s export apples go. In late May, Donna Feltrup, sales manager for L&M Cos. Inc. of Union Gap, Washington, had spent weeks trying to find a container for a load of Apple King apples headed to Guyanavia Seattle. No luck.
Lingering tariffs in India and China still play a role in export challenges, too. In early June, year-to-date Washington apple exports were down by 17 percent from the previous season. About 26 percent of apple shipments were exports at that time, while the historical share of exports is about 30 percent. Making matters worse, several freight lines increased prices by up to $2,000 per container, effective June 1.
A relatively small 2020 apple crop has been the only saving grace. “If we have a big crop year and we need that export outlet, I don’t know what we’re going to do,” Feltrup said.
Cans
Short aluminum production overseas, namely in China, have left the two Pacific Northwest pear processors lacking in 300-size cans, said B.J. Thurlby, president of the Washington State Fruit Commission and the Washington-Oregon Canning Pear Association.
“It’s been a bit of a mess to find cans,” Thurlby said at a May industry meeting.
Some retail chains have turned to stocking Chinese pears. While the industry has long competed with Chinese imports for contracts at correctional facilities and other wholesale buyers, Northwest growers have not previously faced this competition on retail shelves, Thurlby said.
For many processors, the pandemic shift away from wholesale customers, such as schools and food service suppliers, to retail increased the demand for cans. However, food service demand appears to be coming back, said Susan Renke, promotion director for the Pacific Northwest Canned Pear Service.
The industry needs to double down on American-grown messaging going forward, said committee chair Jon Holt of The Neil Jones Food Co. K–12 schools are federally mandated to purchase American-grown food if they participate in the federal National School Lunch Program.
—by Ross Courtney
Leave A Comment