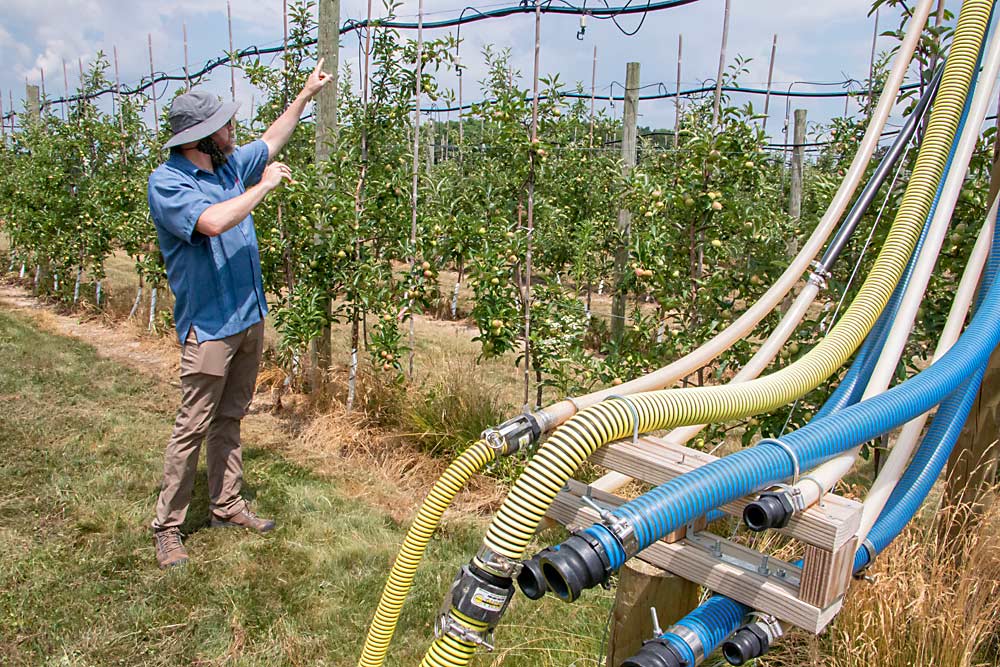
With the solid set canopy delivery system, Matt Grieshop and collaborators sought to create an alternative chemical delivery system for trellised fruit crops, one that minimizes labor, off-target drift, applicator exposure and the need to move tractor-based sprayers through plantings. They wanted the system to perform other tasks, too — such as canopy cooling and freeze mitigation — and to be compatible with future orchard automation technologies.
Based on their research results, Grieshop, the project leader and a Michigan State University associate professor, said they’ve accomplished their goals and have taken the project about as far as university researchers can take it. The next step, if there is one, will have to be taken by a commercial manufacturer.
“We’ve done what we set out to do,” he said. “The next step will require some industrial power.”
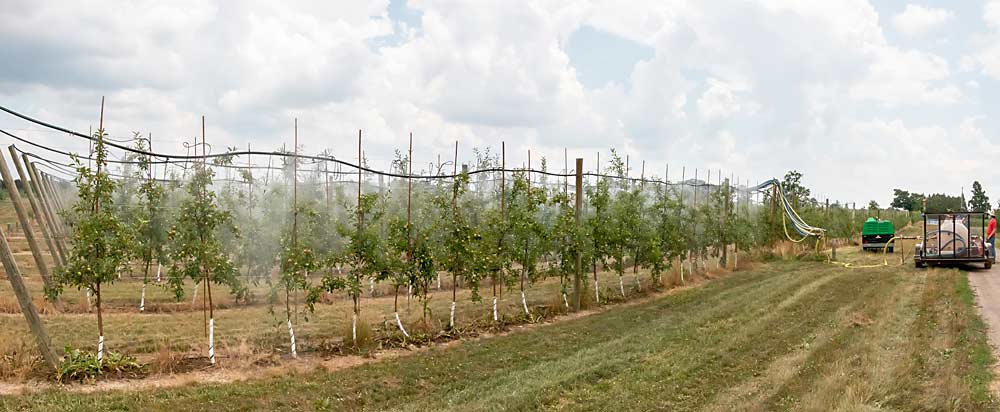
The SSCDS project — running for nearly a decade and funded by U.S. Department of Agriculture grants — will officially wrap up in September. There’s no more field work planned for Michigan, though field trials will continue this year in Washington state, Grieshop said.
Grieshop is writing an SSCDS “extension bible” — complete with assembly instructions, a cost calculator and a lot more information that he hopes to publish before the project comes to an end. He is in discussions with an irrigation equipment manufacturer as well, a company he hopes will adopt the technology if it decides there is a sufficient market for it.
Grieshop listed a couple of SSCDS’ general advantages over traditional airblast sprayers: Without air, it reduces spray drift by 90 percent; and the heavy equipment remains outside the tree rows, allowing for timely sprays even if the orchard ground is soft.
He said the radial airblast sprayer, still the most popular spraying technology in use, hasn’t changed much in the past several decades.
“If we really want to improve our pesticide programs, delivery is something we need to spend a lot more time thinking about,” he said. “There’s an overwhelming focus on what we spray, but not as much focus on how we spray it.”
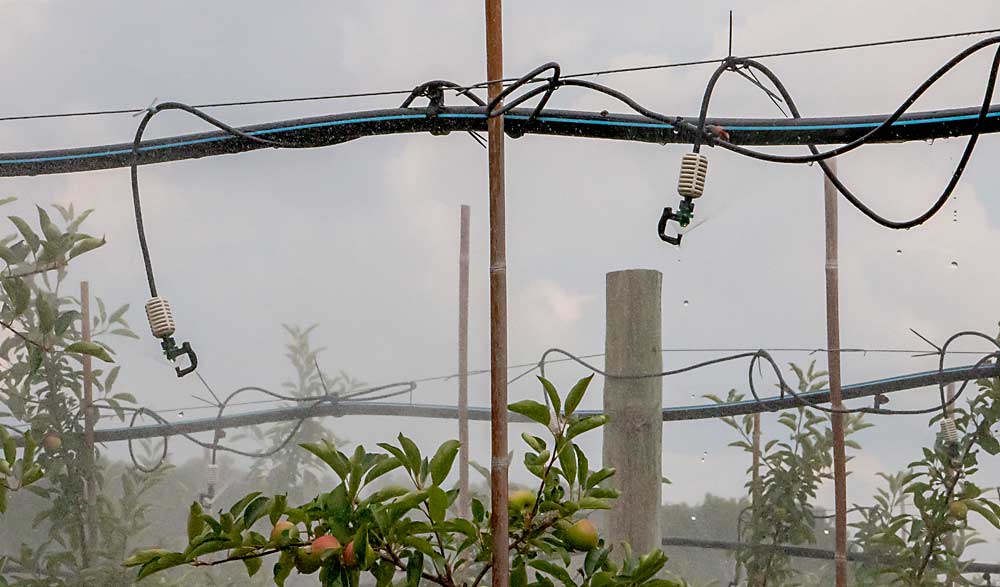
Engineering an alternative
Last summer, Grieshop and project manager Keith Koonter gave Good Fruit Grower a demonstration of the solid set canopy delivery system at MSU’s Clarksville Research Center. They were testing this particular system, engineered by Koonter, on three half-acre research blocks of high-density Gala, Fuji and Honeycrisp planted in 2017.
It works this way: A gas pump pushes liquid (water was used for the demonstration) through flexible hoses placed over the top of the orchard and then through smaller hoses running over each row. Emitters connected to the smaller hoses spray the liquid throughout the tree canopy and, when sufficient coverage is achieved, an air compressor pulls back the residual liquid. It only takes 10 to 12 seconds to apply 50 gallons of liquid per acre, Grieshop said.
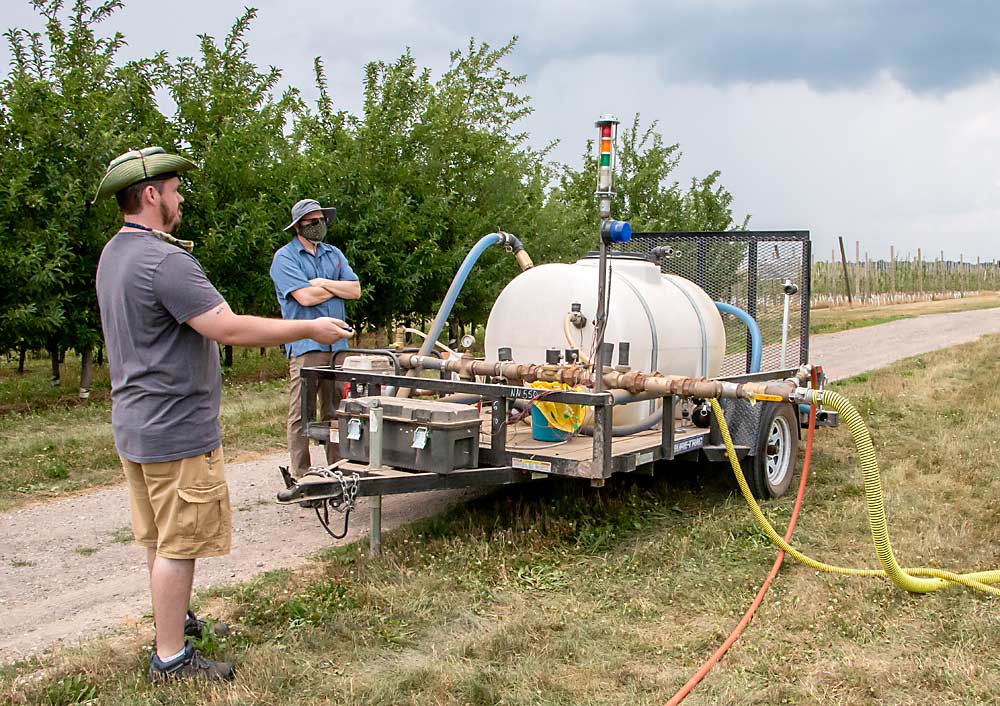
SSCDS has three subsystems: the pump, the pipes and the emitters. Grieshop said his team optimized the pump and emitter subsystems, but the middle subsystem, the pipes (or hoses), pose the “pressure compensation delivery problem.” In other words, maintaining adequate air pressure throughout each part of the system gets more difficult the larger the area you’re trying to spray.
To tackle this problem, the researchers came up with two versions of SSCDS: a canister-based version and a linear version. In the former, they place small canisters at regular intervals along the hoses that run down each row, and the canisters act as small pumps that help reduce pressure loss throughout the system. A Washington State University research team is testing that approach.
The second version of SSCDS, the one demonstrated at Clarksville, is the linear, or direct-injection, version. This version, which uses larger hoses atop the orchard to push liquid throughout the rows, is still in the conceptual stage, Grieshop said.
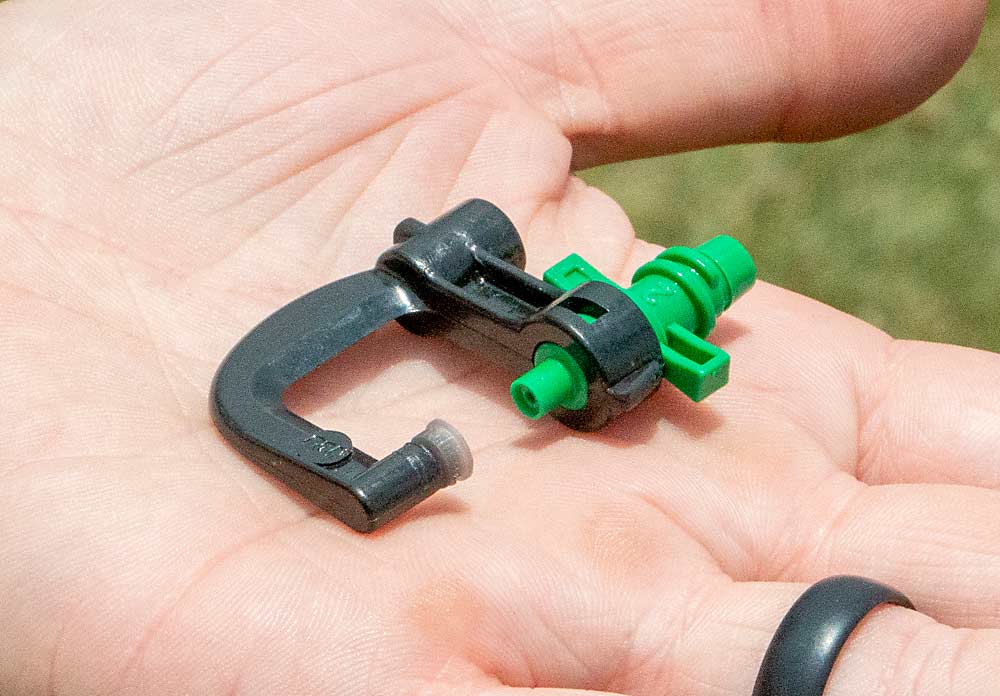
Grieshop began working with SSCDS in 2012, and the concept has since evolved through trial and error. In the original design, the pipes between the pump and emitters were buried underground, which turned out to be a “big mistake,” he said. Any time there was a leaking fixture, broken pipe, gopher or whatever, they had to get a backhoe and start digging.
“For irrigation it’s fine, but when you start dealing with EPA-regulated chemistries it’s not a good idea,” he said.
The project economist, MSU assistant professor Steven Miller, said commercializing SSCDS might be economically feasible within the next several years, but it likely would be more expensive than conventional airblast sprayers. Because of that, he anticipates initial commercial uses of SSCDS will largely be in niche settings and on smaller-scale operations. One of the advantages of SSCDS is its ability to manage pests with reduced contact-threat to workers, so any increase in pesticide regulations might make such a system look more attractive to growers.
Miller said the ability to scale up SSCDS might be limited.
“I don’t foresee strong economies of scale in these systems,” he said. “That is, as farm size grows, I’m not sure the costs per unit of output decrease.”
Washington version
Lav Khot, an associate professor and agricultural engineer at the WSU Irrigated Agriculture Research and Extension Center, has spent the past few years studying SSCDS in tall spindle apple orchards and vineyards. He said the system has great potential in both systems, but he thinks its potential might be greater in vineyards, with their smaller canopies that require fewer spray nozzles. He said Washington vineyards, with their vertical shoot positioning and simple canopies, match particularly well with SSCDS.
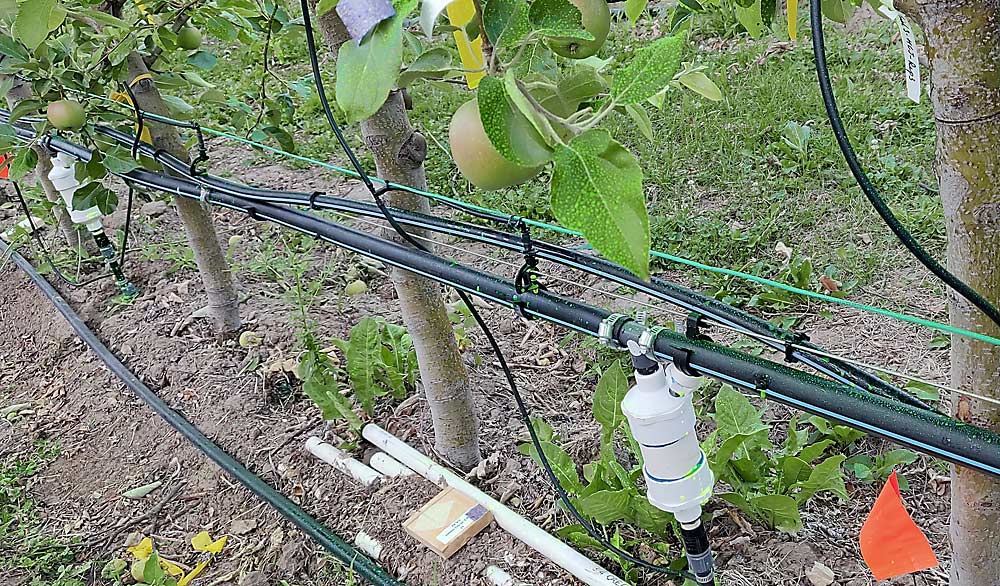
Khot’s team works with the canister-based system. In their VSP vineyard trials, the best results have come from a two-tier system with three emitters per vine, one spraying down from above and two spraying up into the fruit zone. Because the upward-spraying nozzles that they liked best were prohibitively expensive, the engineers used a 3D printer to design a cheaper version, Khot said.
The system’s engineering has improved by “leaps and bounds” in the past four years, said Gwen Hoheisel, a WSU regional extension specialist who’s been part of the SSCDS project from the beginning. It took time and effort, but the system’s thorniest problems — how to maintain pressure, the best nozzles to use, effective dose rates and proper pipe cleaning — have effectively been solved. She believes the system is ready for commercialization.
The WSU researchers are wrapping up their main SSCDS project this year with plans to study the system’s pest control efficacy in a commercial orchard in the coming season. They also plan to test the system’s evaporative cooling and freeze mitigation potential in separate studies. Considering the installation and other costs that would be associated with a commercial version of SSCDS, the more uses growers can find for it, the more it would justify their purchase, Khot said.
“If you show growers that one system can do a lot of things in the installed block, I think they will show some interest,” he said. “If a private player picks this up and takes it to growers, I think it would be awesome.” •
—by Matt Milkovich
Leave A Comment