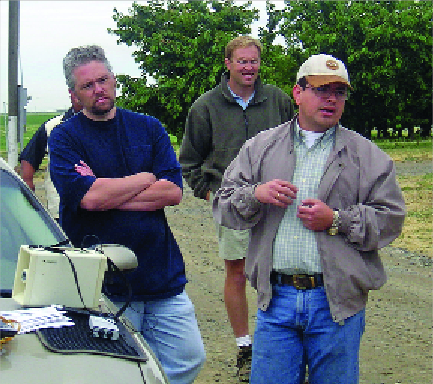
Todd Elliot (left) and Jose Chavez (right front), both of WSU’s Center for Precision Agriculture Systems, demonstrate a remote irrigation monitoring and control system.
Photo by Anne Sampson
By Anne Sampson
A variety of new technologies and products were on display in Prosser, Washington, this summer when the Irrigated Agriculture Research and Extension Center held its annual field day. Attendees saw demonstrations of a computerized irrigation monitoring program and a trellising system uniquely designed for mechanical harvesting, and heard about an adaptation of a product originally made to protect apples that could have a significant impact in cherry orchards.
Remote irrigation
Jose Chavez and Todd Elliott of the Washington State University’s Center for Precision Agricultural Systems presented a comprehensive software and hardware system that enables a grower to monitor an orchard’s irrigation from anywhere in the world. The system consists of radio sensors positioned so that a base retrieves data on water pressure and flow from remote stations located throughout the orchard.
The data is immediately transmitted and downloaded to computers in the IAREC building about three miles away, where it can then be made available on the Internet. The new system represents an advancement in the AgFrostNet software program, originally developed by the Center for Precision Agricultural Systems to protect fruit from frost by monitoring real-time air temperatures.
The group is working on more software adaptations that will enable a grower to send a weekly irrigation schedule to stations in the orchard, fine-tuning controls down to the level of individual solenoids along irrigation lines. Also in the works is software that will integrate water flow data with data from weather stations and soil moisture stations to create geologic maps of irrigation needs.
“You’ll be able to see pressure distribution along each irrigation line,” Chavez said. WSU Research horticulturist Dr. Matt Whiting noted that the system represents important advances in orchard management. “In a drought year, you can’t afford to make any mistakes with water,” he said.
Mechanical harvester
Visitors to IAREC walked up and down rows of trees, comparing trellising systems and their suitability for the mechanical harvester parked nearby. After trees are treated with Ethrel (ethephon) to promote abscission at the stem, an operator drives the machine up and down the rows, thumping the limbs to displace the fruit, which falls to a conveyor belt on the harvester.
The process requires trees are trained to a trellis in either a Y-shape, or a V-formation, with trees growing in a single direction, alternating by row, so the fruit on the limbs is more visible. The mechanical harvester is not widely used yet because few orchards have the right trellis configuration.
But it is a topic of interest to researchers working to improve orchard profitability. It also creates a new twist on traditional fresh cherries. One of the characteristics of mechanically harvested fruit is that they leave the tree without their stems attached. Whiting said there are important advantages to eliminating stems. “It extends the fruit’s postharvest life,” he explained.
“We know that stem-to-fruit contact causes pitting.” And because fresh green stems turn brown long before the fruit has lost its freshness, a stemless cherry has a longer shelflife in the marketplace.
No more cracked cherries?
Dr. Larry Schrader from WSU’s Tree Fruit Research and Extension Center in Wenatchee reported on RainGard, an adaptation of a product he developed to protect apples from sunburn. About three years ago, Schrader introduced Raynox, a waxy emulsion that shields apple skins from the sun.
“I tried it on cherries to see if it would prevent cracking, and it seemed promising,” he said. The new product, called RainGard, is made primarily from carnauba wax in an emulsion applied with standard sprayers three to four weeks before fruit maturity. Schrader said it’s similar to Raynox, but is clear instead of opaque.
“It gives the cherries a nice luster,” he said. The product won’t prevent all cracking, but Schrader said tests at 13 different sites in Washington and Oregon show RainGard can reduce the amount of split fruit by as much as 50 percent.
“With labor costs as high as they are, if a crop is 25 percent cracked, some growers won’t harvest it,” he said. “If you can reduce cracking from 30 percent of a crop down to 20 percent, it can mean the difference between harvesting a crop or losing it entirely.”
Leave A Comment