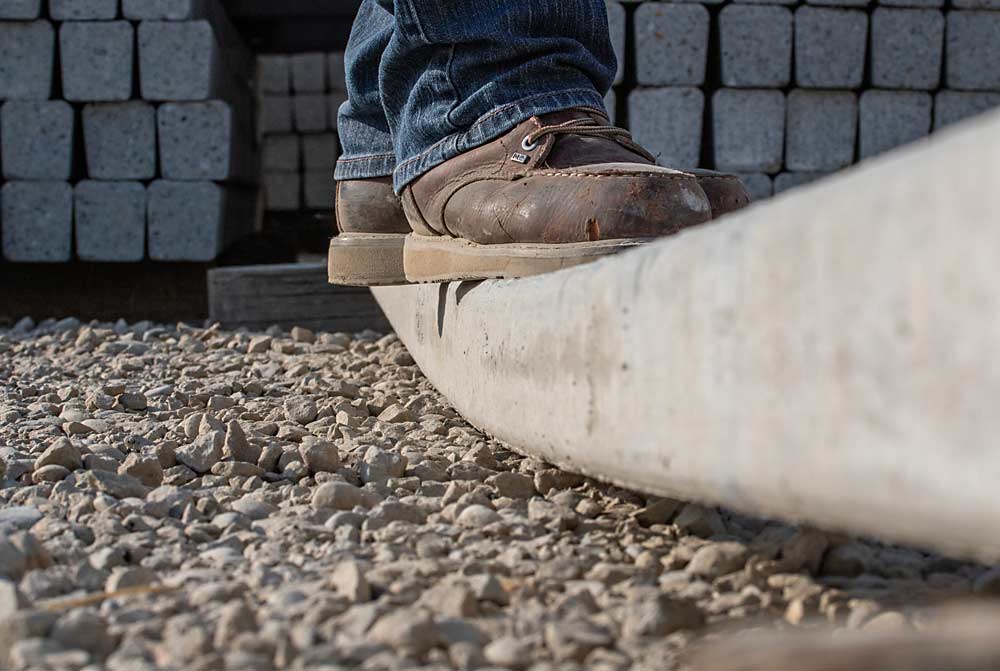
A U.S. concrete company known for municipal projects is getting into the trellis post business, long dominated by European manufacturers.
Jensen Precast, which makes sewer pipes, bridge beams and parking barriers in 17 locations across the country, is ramping up production of prestressed concrete posts for orchard and vineyard trellises, molding the posts at a new facility in Kingsburg, California.
Concrete posts are the norm through much of Europe, especially in Italy, though still rare on North American specialty crop farms. Some backers believe that’s about to change.
“I think the interest is high for another option for trellis,” said Mark De Kleine, president and CEO of TrellX, a Prosser, Washington, company that engineers and installs trellis infrastructure for orchards and vineyards in the Northwest. He works as a consultant for Jensen. De Kleine, once a Washington State University researcher, currently uses wood and metal in his TrellX structures.
Proponents of concrete say the posts last longer than wood, often longer than the orchards or vineyards they support. They can be reused, even moved.
They qualify for organic production right away, without the three-year transition period required for treated wood posts. They also are more uniform in size, making their brackets and other accessories more interchangeable.
Making the posts
Jensen makes the posts — branded as Harvest Pillars — at its Kingsburg plant using two 240-foot prestress beds manufactured by Italian company CONTEC. First, crews stretch four strands of braided cable, also imported from Italy, 18 inches beyond the beds and position them in the molds. Then, they pour the concrete, allow it to cure and cut the cables. All that cable tension then compresses the concrete, giving each post, cut to a desired length, extra strength and flexibility. The same process is used for bridges and parking structures.
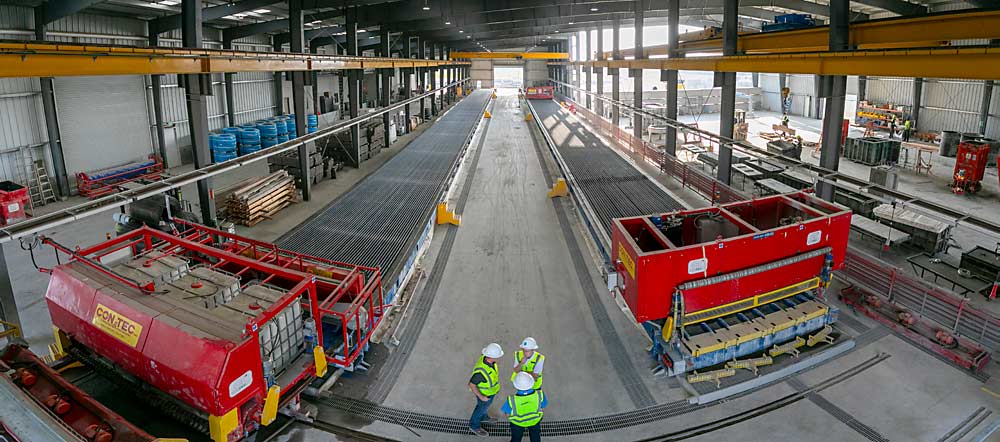
“There’s a ton of stored energy that, once you cut the ends and release the ends, it wants to spring back into its original shape,” said Greg Barner, general manager of the Kingsburg plant. “It gives it tremendous strength and ductility and durability.”
Ductility refers to a material’s ability to sustain being stretched or deformed without breaking. To demonstrate, Barner stands on a post stored horizontally on blocks and bounces on it like a springboard.
Combined, the two beds make 20,000 linear feet per cast. Each cast takes two days now, but the company plans to cut that in half after installing some new heating equipment.
To install the posts, crews vibrate them into the ground using a rubber end protector. The company sells clips, also imported from Italy, for affixing wiring but plans to manufacture those in the United States after production ramps up.
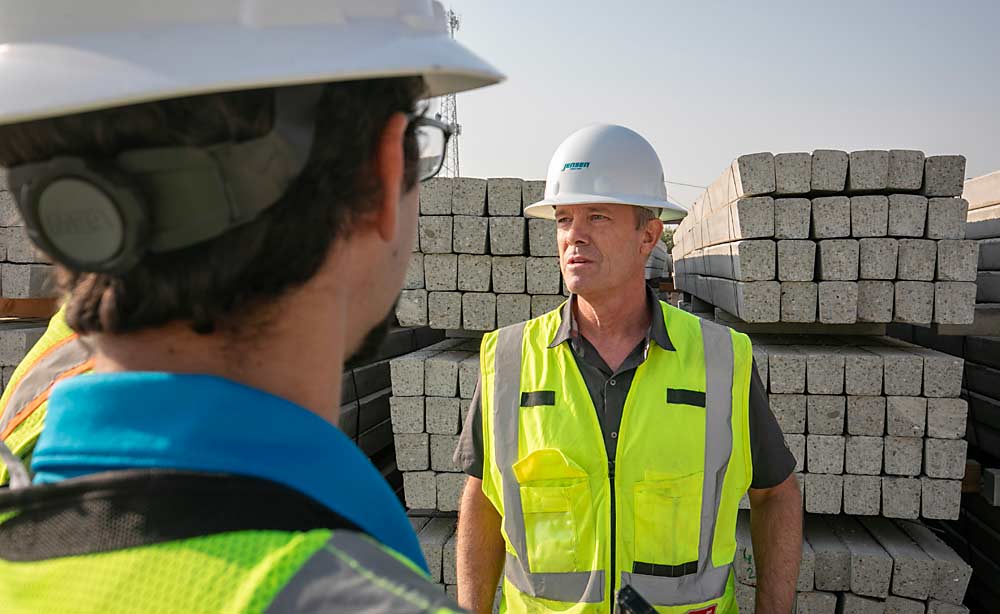
Pro concrete
Some North American growers who have concrete posts love them and don’t plan to use wood again.
“We plan on every post that we plant now is going to be concrete,” said Riley Bruce, orchard manager for Chudleigh’s Farm near Halton Hills, Ontario, Canada.
So far, the farm has 6.5 acres of apples on concrete trellises. Bruce figures the posts will last long enough for three different orchards, either through replanting or topworking.
“If the thought is that you’re going to keep growing apples for 40 years … then it would make sense, because you can pull that pole out of the ground and reuse it,” he said.
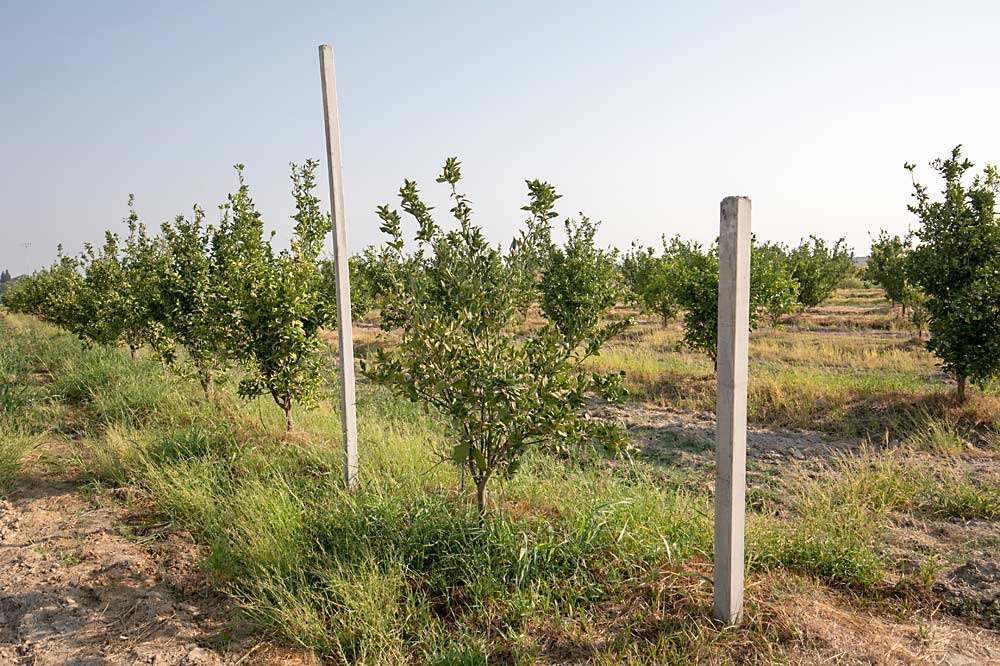
Griffin Berger, an apple grower, fittingly located in Concrete, Washington, has purchased a total of eight containers of concrete trellis posts in four purchases over the past seven years.
“It’s better than having treated wood that’s going to bust and break over time,” he said.
Berger and Bruce purchased their posts straight from Valente, an Italian manufacturer entrenched in the concrete post business. In fact, Berger has acted as an informal resell representative for neighboring small growers. He has visited one of the company’s factories.
“I’m excited that somebody is making them here in the U.S.,” Berger said. “I hope they blow that up.”
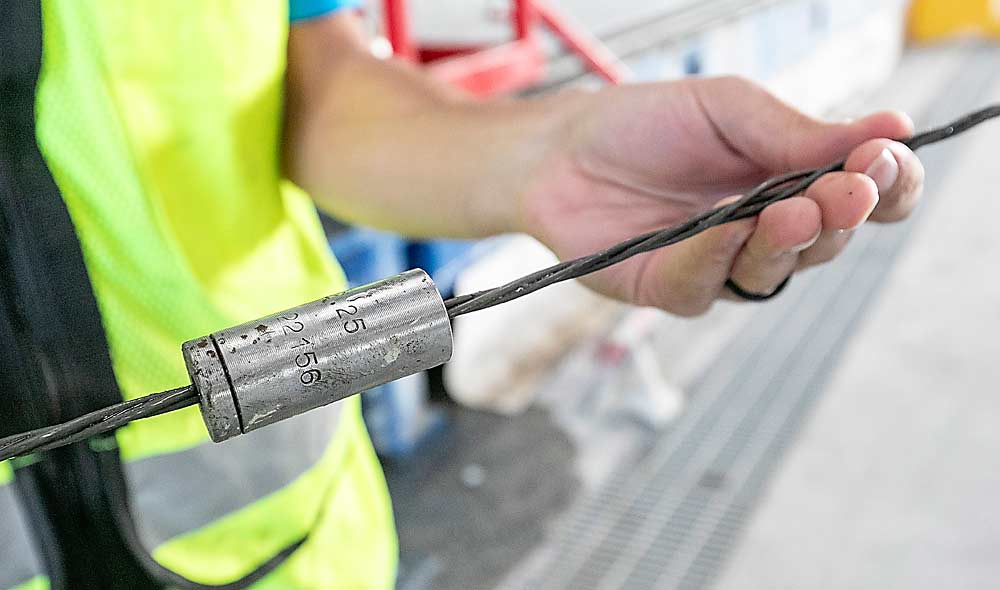
Costs
Manufacturing and shipping costs of concrete make for a more expensive product than wood, but not as much as you might think, said Berger, Bruce and Trevor Hardy, a member of the family that owns Brookdale Fruit Farm of Hollis, New Hampshire.
Brookdale, also a farm supply retailer, sells 3- by 2-inch, 15-foot-long Valente line posts for $18.75 each, Hardy said. Freight costs from Europe and throughout North America would bump that up to between $30 and $40 each. That’s roughly $2 higher than what Brookdale would charge for each treated lodgepole pine post at a commercial scale, he said.
“If you were within a buck or two of wood, wouldn’t you want something you could reuse,” said the seventh-generation grower.
In his experience selling farm products, growers typically are willing to try an upgraded item if it falls within 10 percent of the status quo.
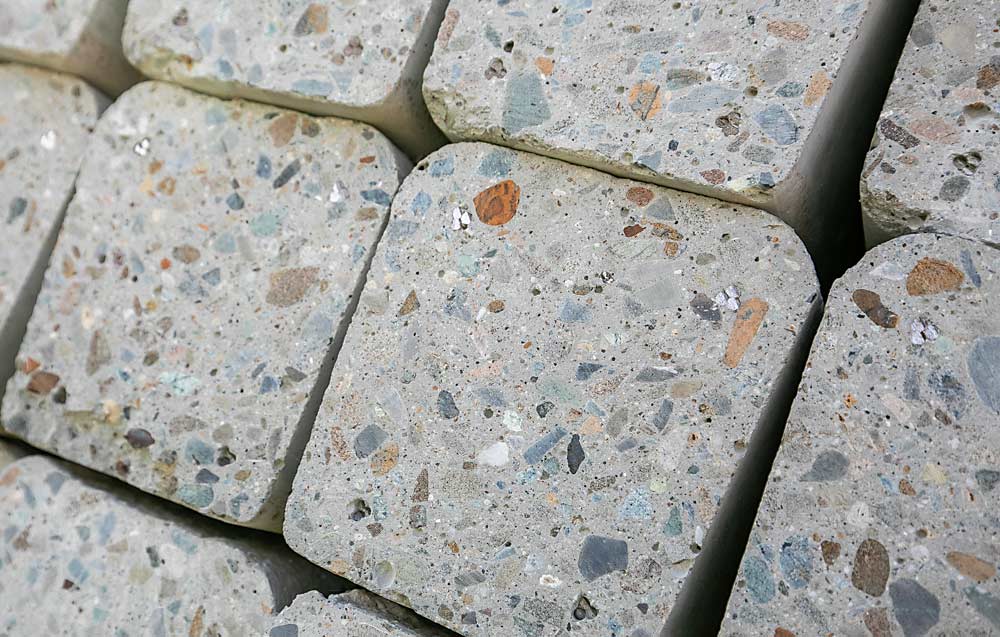
Normalizing of international freight traffic this year has stabilized his concrete post business. In 2021 and 2022, during the peak of the international shipping problems, soaring freight prices left his post business economically impossible, he said.
Hardy, a licensed distributor for posts from Valente and another Italian maker, Agranova, has a master’s degree in engineering and works with both manufacturers to help growers design their orchards with geolocation mapping, weather data and soil information.
He began selling the posts in 2020 after first installing them on his own New Hampshire farm in 2018. He also helped set up a demonstration block with Jon Clements, an extension educator at the University of Massachusetts.
Jensen plans
Jensen Precast, with headquarters in Reno, Nevada, has been making concrete products since 1968, but they’re admittedly new to agriculture.
Currently, the company lists 3- by 3-inch, 15-foot concrete posts for $49 each, before freight, but prices may change some as company officials learn more about the market, said George Kehagias, technical sales manager. For example, he recently learned that longer posts cost a bit less to make because they require less cutting.
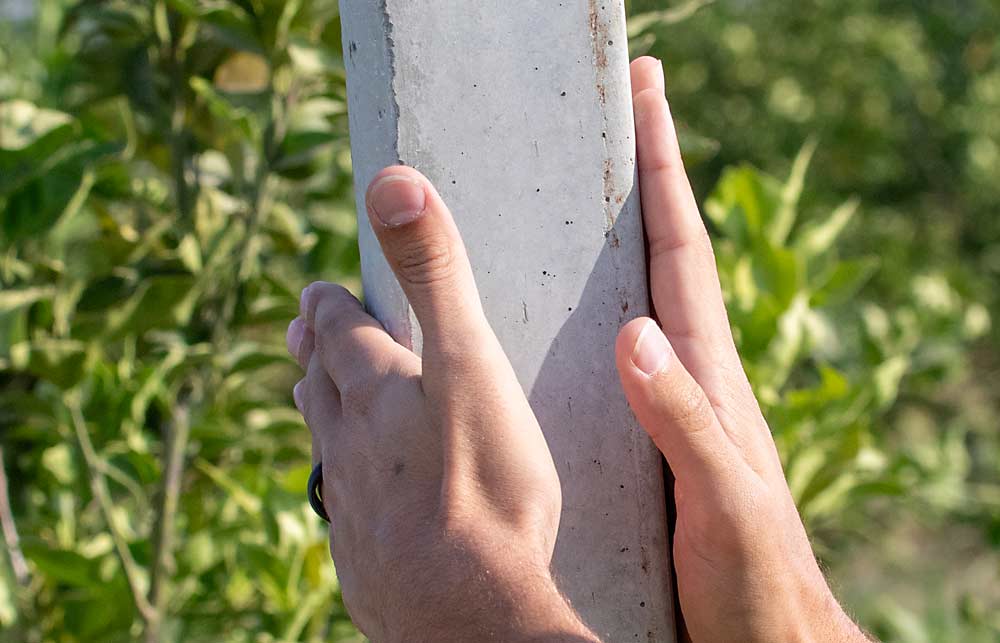
He and other company representatives attended the 2022 Washington State Tree Fruit Association Annual Meeting and plan to return this year. A California hop farmer had committed to a trial purchase. Otherwise, a few vineyard and blueberry farm owners had expressed interest.
Also in September, the company was modifying its website to include a calculator to help growers determine how many posts they might need. They also plan to help growers through the process with their own engineers and in conjunction with De Kleine.
The company may expand production to Puyallup, Washington, where it already owns a facility making concrete water culverts, among other things.
They agree that growers have an appetite for concrete posts, but they also expect a marketing climb to “shake things up” against the status quo of wood and metal.
“We feel like concrete offers upsides that those products don’t, and we hope the growers see what we see,” he said.
—by Ross Courtney
Leave A Comment