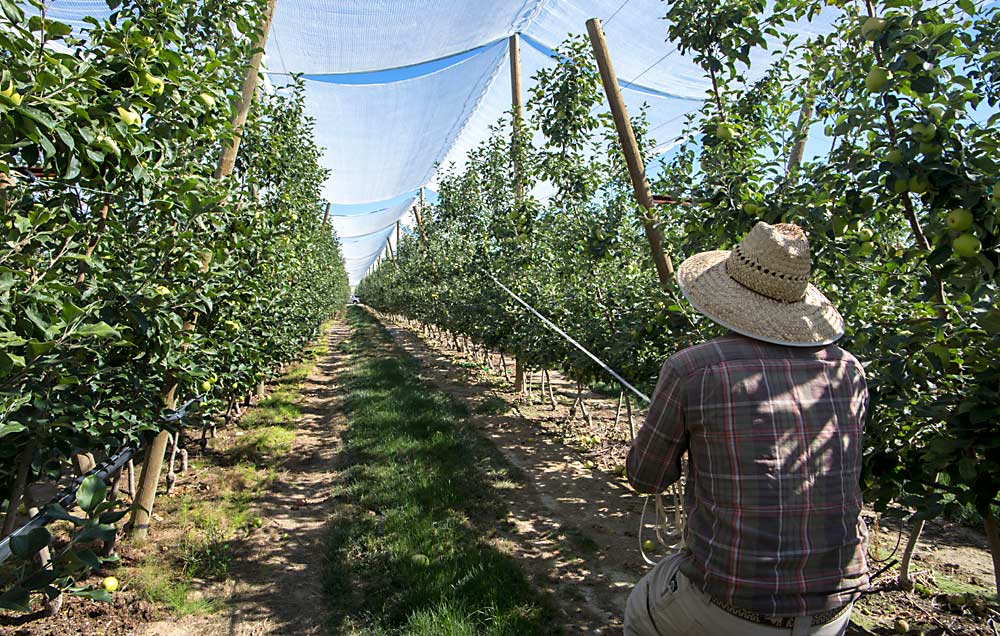
In a sun-scorched apple block in the heart of Washington’s Columbia Basin, where temperatures soar and hail pelts, orchard crews open and close protective netting panels much like drawing a household curtain.
By way of demonstration, worker Octavio Lopez tugged a rope attached to an interconnected system of carabiners and cables to open nine panels of mesh shade cloth in a matter of seconds at Sweet Note Orchard near Quincy. He and two co-workers could knock out the task for 11 acres of covered Premier Honeycrisp in three hours, a chore that previously required a dozen workers three or four days using ladders and scissor lifts, said Matt Jeffery, assistant manager of orchards for McDougall and Sons, the company that owns Sweet Note.
“This solution is both time-saving but also safer for our team,” Jeffery said.
The on-farm innovation incorporates the ingenuity of a neighboring orchardist, the construction background of an assistant manager, the engineering from netting supplier Extenday and a willingness of industry colleagues to share ideas and tinker with them.
History of Central Washington innovation
McDougall and Sons installed the netting about three years ago but got the idea from nearby Quincy-area farmers, Bryan Jones and Steven Bierlink, who rigged up similar scrolling nets a few years earlier. The system uses netting hung from overhead cables stretched across trellis posts by carabiners that slide back and forth with the pull of a rope.
“Basically, it’s just like a giant curtain,” Jones said.
Over beers, the two friends spent hours discussing retractable netting and came up with a plan in 2014. The design required new manufacturing from Extenday, which added belts to reinforce edges and adjusted the size of mesh to slow down hail but still possibly let it through to avoid adding undue weight to the mechanisms. They first installed it in 2016 and experimented with bigger sections after that. They have not had any hail since, to put it to the test.
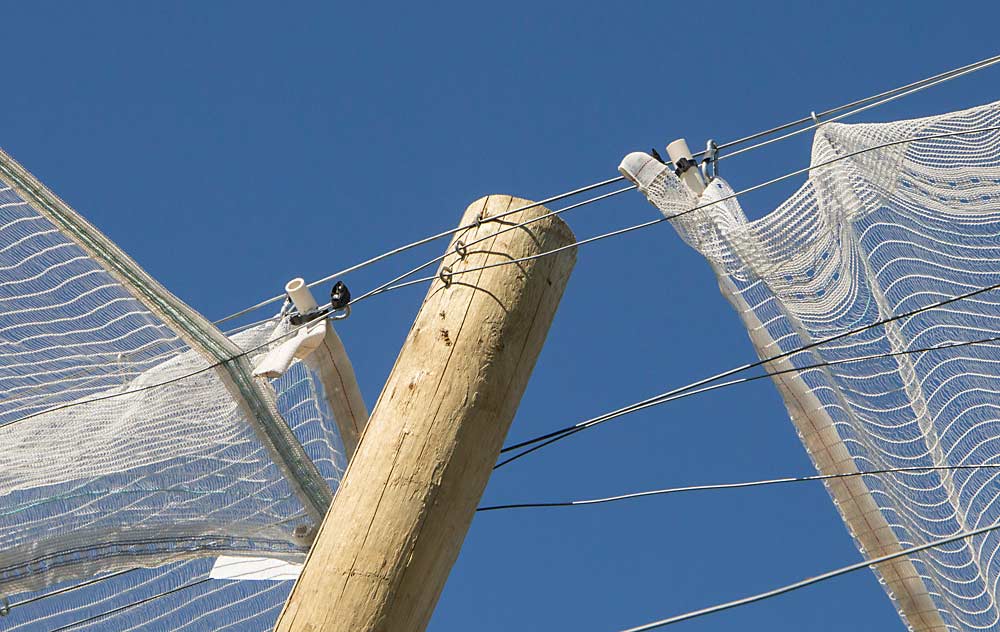
They’re learning and tinkering as they go and plan to do more, Bierlink said. They may even rig up an electric motor to mechanize the retraction.
He likes the setup at Sweet Note but wonders if the movement will cause wear and tear on the netting.
“Longevity is a really big concern for retractable nets,” Bierlink said.
Jonathan Toye, CEO of Extenday, called retractable netting a story of Washington growers working together for solutions to common problems. The New Zealand company has a number of patents on their nets, which are custom engineered for each orchard block. The innovations specific to the retractable nets include a few construction features and chemistry used in the fabric, but much of the installation and use of the nets has come about from word-of-mouth among several growers in the area.
The Extenday company started in 1994 and began selling reflective fabric in Washington in 1999, entering the shade netting business within a couple of years. About eight years ago, company engineers and some growers came up with their first retractable system. Improvements were made over time, although not every customer opted to publicly share how they’ve adapted the approach, Toye said, and the mechanisms have since been adopted by several production companies, large and small, throughout the state.
Such gradual improvements are common in the fruit industry, which is known for sharing techniques, Toye said. “There’s always another way to solve a problem,” he said.
Savings at Sweet Note
Connecting panels together with one rope was the work of Martin Gil, McDougall and Sons’ assistant manager for Sweet Note Orchard and a former construction supervisor. He maxed out at nine panels before ripping the netting.
“Individual panels take more time with more people,” Gil said.
The system requires high orchard posts to accommodate roughly a foot of height difference between the cables, so they overlap without catching on each other. The posts are independent of and higher than the tree trellises.
The only time the workers climb ladders or get on lifts is to put the netting away each winter, rolling it and tying it like sausage.
Besides saving time and money, the netting system allows for more precise coloring, Jeffery said. On relatively cool sunny days, the orchard team opens the panels. When things get too hot, they close them.
Meanwhile, they no longer have to worry about overwatering their Honeycrisps with overhead cooling, Jeffery said.
The upfront costs are lower than fixed netting, too, Jeffery said. Gil’s version ran about $9,000 per acre, while fixed systems have cost more than $10,000 per acre, he said.
The company may cover more acres with the netting but also is testing out a mister that employs evaporative cooling. It might be even cheaper, he said. •
—by Ross Courtney
Leave A Comment