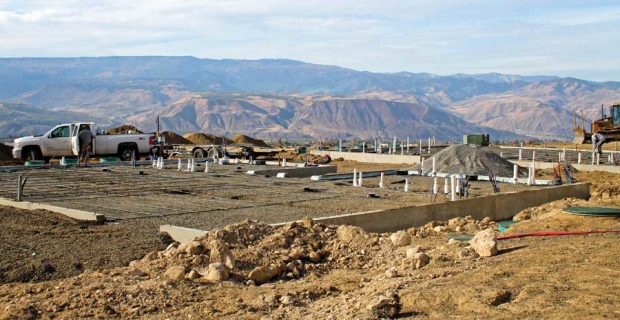
The Legacy orchard has housing for 98 workers. McDougall is constructing more housing to double that number. (Geraldine Warner/Good Fruit Gower)
The Washington fruit grower-packer McDougall and Sons relies heavily on foreign guest workers to harvest its crops.
Hiring workers through the H-2A program required a big investment in housing and transportation, but it’s ensured that the company has a reliable and well-trained workforce.
McDougall said it’s only because of the assurance of getting H-2A workers that the company has been able to invest in planting the new orchard.
Despite advertising for domestic workers, which is a condition of the H-2A program, locally hired people make up less than half a percent of the company’s seasonal workforce.
McDougall and Sons has spent more than $8 million to provide a total of 620 beds for H-2A workers at its orchards in Mattawa, Royal City, Quincy, Monitor, Bray’s Landing and Bridgeport.
That works out to roughly $14,000 a bed. The company’s new Legacy Orchard in East Wenatchee has beds for 98 workers, and there are plans to double that number.
“You have to keep pinching yourself,” said Scott McDougall, co-president of the company. “This whole thing added a lot of cost to our system and another layer of infrastructure to properly manage it.”
They started out using three-bedroom manufactured homes with four bunks in each bedroom and a common eating area.
However, as the price of manufactured homes increased and local builders were looking for more work during the recession, stick-built homes became the most affordable.
Each camp has a full-time housing manager and daily cleaning is provided.
“We take a lot of pride in our camps in keeping them up and keeping them nice for people, and we expect them to pick up a little bit, too,” McDougall said. “It’s not just like a hotel.”
During H-2A contract periods, workers must be paid at least the adverse effect wage rate, which was set by the U.S. Department of Labor at $12.42 for Washington last season.
However, McDougalls’ piece-rate workers average at least $4 an hour more than that for picking apples and can earn $20 to $21 an hour for cherry picking.
A Washington Supreme Court ruling this summer that piece-rate workers must be paid extra for rest breaks will add around $700,000 to McDougalls’ annual payroll.
“We get frustrated with the perception on the outside that these people don’t get paid well,” McDougall said. “It’s hard work, but there’s the opportunity to make decent money.”
McDougall and Sons has about 50 vans to shuttle the workers to places they need to go, including the grocery store once or twice a week. Groceries are the only thing the workers have to pay for during the contract.
Three contracts
McDougall and Sons used to hire H-2A workers under one contract starting with cherry harvest, but they weren’t even able to get the pruning done with local labor.
Now, the company has three H-2A contracts.
The first workers arrived Feb. 1 to help with pruning and planting. The second batch arrived around June 1 to work on fruit thinning and cherry harvest.
The last workers arrived in mid-August for apple harvest. All the contracts usually end Nov. 1, but this year the workers went home a week earlier because of the early harvest.
McDougall and Sons covers the costs for them to travel from Mexico to Washington by bus for the start of the contract and pays their airfare back home at the end.
This is the eighth year that the company has used the H-2A program. Between 80 and 90 percent of the workers return year after year, McDougall said.
“We’re paying the price for this system, but we also feel like we have the most well-trained and effective workforce we could have.” •
– by Geraldine Warner
Leave A Comment