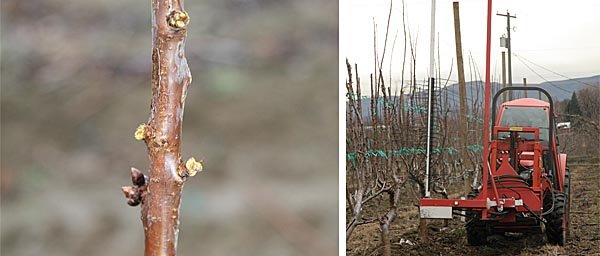
Soft fruit growers in the United States are catching on to what seems to have been a well-kept secret in Germany. With three years of data by U.S. researchers showing that German-made mechanical string thinners increase fruit size while dramatically reducing labor costs, interest is growing in the orchard implements now sold in North America.
Pennsylvania State University initiated the research project that has been looking at ways to reduce thinning costs in peaches, but university collaboration spread like wildfire across the United States to involve other regions—California, Washington, Georgia, South Carolina, Illinois, and Maryland. Led by Penn State agricultural engineer Paul Heinemann, the Innovative Technologies for Thinning of Fruit project received a $2 million federal grant under the Specialty Crop Research Initiative, along with support from universities and industry groups, including the Washington Tree Fruit Research Commission.
Presenting the results of the peach thinning project during the Washington State Fruit Commission’s Soft Fruit Day in Buena, Penn State horticulturist Dr. Jim Schupp said the mechanical thinner known as the Darwin string thinner has been consistent in removing from 35 to 50 percent of blossoms, increasing fruit size, and reducing labor.
You can’t always use the word ‘consistent’ in thinning trials,” he said, adding that the mechanical thinners have performed well in several different orchard systems, in both the perpendicular V and open center vase styles.
The net economic impact for fresh peaches ranged from $185 to $934 per acre; for processed peaches, it ranged from $236 to $1,490 per acre.
The project has been evaluating the Darwin string thinner as well as a drum shaker machine developed by the U.S. Department of Agriculture. The German-made Darwin, which has a ten-foot-tall rotating spindle that sits inside a frame, comes in two models: the vertical 300 and newer PT 250 that can go vertical or horizontal to target the tops of tree canopies. The Darwin thinners, manufactured by Fruit Tec, are commercially available in North America through the licensed dealer N.M. Bartlett, Inc., in Ontario, Canada, and several growers have purchased them. The Darwin 300 retails for around $11,000.
The drum shaker, still under study, has been used to remove green fruit in peaches and may have benefit when used in combination with the mechanical thinners, Schupp said. The drum shaker was originally developed for citrus harvesting in Florida.
Schupp said mechanical thinning works best in well-pruned trees; unpruned trees have too many blossoms and too much structure. Operating the spindle close to the structure so the strings reach deep into the canopy reduces the risk of overthinning. Strings that don’t penetrate the canopy hit the outer branches too fast.
Longer window
Karen Lewis, Washington State University Extension educator, has collected Washington data the past two seasons using two mechanical thinners (Darwin 300 and the Bonner string thinner that has three rotating spindles). Both machines were purchased by the Washington Tree Fruit Research Commission and have been used in apricots, nectarines, cherries, and apples. Lewis is also cooperating with New Zealand’s tree fruit industry to gather data in the off-season.
Lewis is enthusiastic about results thus far in soft fruits and believes that the mechanical implements, which attach to the front of tractors, will be valuable additions to a grower’s crop production toolbox.
“We’ve learned in the first two years that we have a wider window to use the string thinners than we originally thought,” she said. “The good news is that we can use them from pink all the way through petal fall and they are still effective.”
She notes that in Washington, they tend to run the string thinners faster and at higher rpms—from 2.5 to 3 miles per hour and 200 to 240 rpm—than some of the trials in other areas. Much of Penn State’s trials have been from 1 to 2.5 mph and 120 to 200 rpm.
In addition to dramatic labor savings of 40 to 60 percent in hand thinning costs in an apricot trial, another benefit was the excitement of workers who did follow-up thinning. “The workers loved getting into the prethinned blocks,” she said, adding that they could rapidly go through the orchard for touchup thinning.
This year, in late February, the mechanical thinners were tried for the first time during the dormant period to thin cherry buds.
A demonstration of prebloom thinning was held during Soft Fruit Day as Lewis used the Darwin string thinner to knock off buds in Mark Hanrahan’s dormant Early Robin, Rainier, and Santina cherry blocks. The Yakima Valley orchardist wanted to reduce the number of buds in the middle of his fruiting zone where he knew he would have thinning issues because of dense blossoms.
Hanrahan’s blocks are planted on Gisela 5 rootstock and trained to the new Upright Fruiting Offshoots system, called UFO, developed by WSU’s Dr. Matt Whiting. Hanrahan is targeting the Japanese export market with his cherries, and size is critical. The location is on a warm site, so he doesn’t have frost risk.
It took a few minutes to adjust the string thinner so it would target the middle fruiting zone, removing strings from the top and bottom of the spindle. A pass on both sides of the canopy was made so that bud removal would be uniform. Lewis estimated that about 15 percent of the buds were knocked off, and she believes more will fall off later from buds that were damaged by the mechanical thinner but not initially knocked off.
“This is the first time that anyone has thought of doing prebloom thinning,” she said.
Leave A Comment