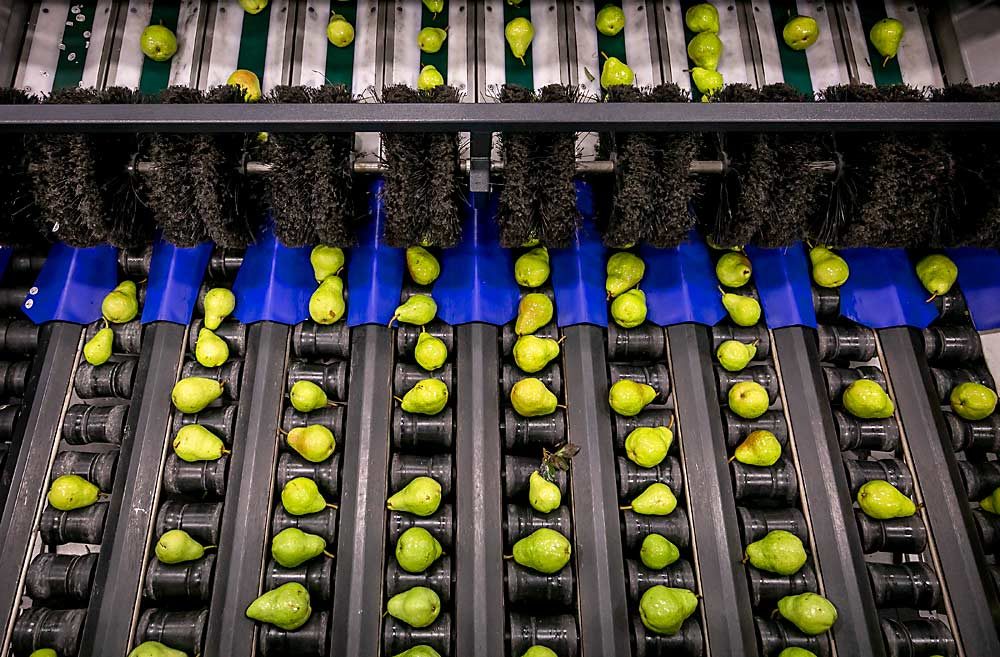
Handwashing stations with turnstiles. Rollers that line up pears for infrared sorting. Automated refrigerated storage retrieval.
Mount Adams Fruit has all that and more, as the Bingen, Washington, fruit company moves ahead with a new pear packing facility that replaced the one destroyed by fire in 2017. Meanwhile, other pear packing houses are following suit with similar investments.
New technology, the kind that has boosted efficiencies and improved consistency and quality in apples and cherries, is on the wish list and business plans of many a pear packer. In fact, Mount Adams had installed a new line, which was lost, about 18 months before the fire and had been contemplating a new building within the next 10 years.
“I would have phased it in over time,” said Don Gibson, company president, of all the new equipment in the new facility.
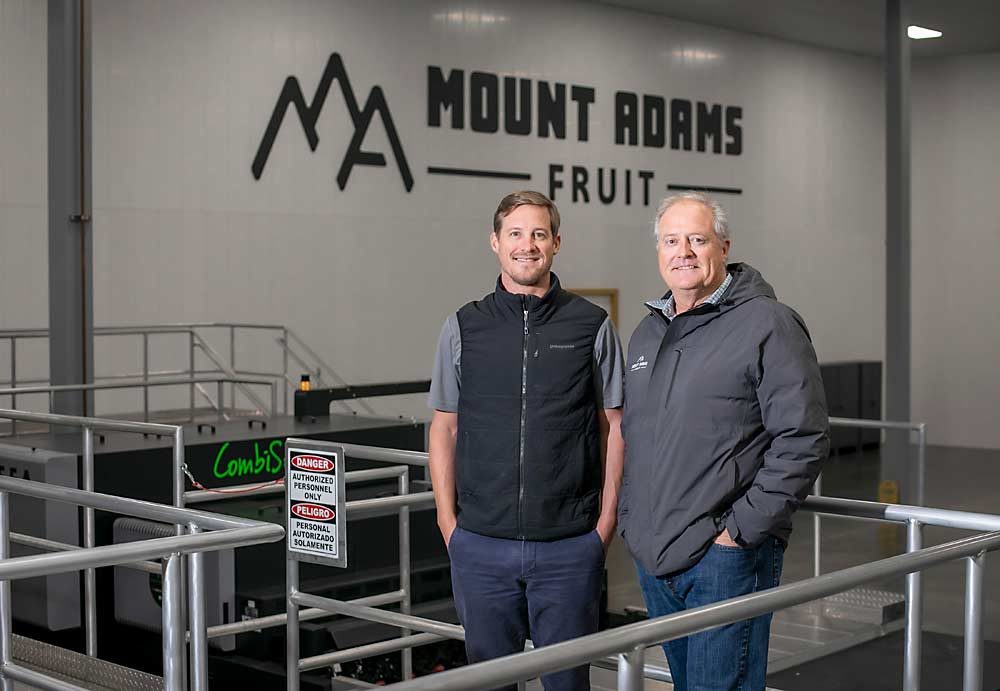
Manufacturers have just begun making pear-specific optical and infrared sorters, a challenging task due simply to pears’ oblong shape. They don’t roll as easily as apples and cherries do, to allow imaging on all sides.
Mount Adams opted to install three CombiSort lines by Dutch manufacturer Greefa. The lines use rollers that rotate off-center and in opposing directions to line up each pear horizontally and spin it so cameras take pictures from 360 degrees. The computer system learns to better assess sizes and spot internal and external defects over time, so Dutch programmers still fine-tune the algorithms overnight every few days.
The equipment allowed the company to go from 36 human sorters to 12. Instead of laying off those displaced sorters, however, the shipper expanded its capacity and moved them to packing stations at the end of the line. Overall, the company has 270 full-time employees in the apple and pear warehouse — similar to before the rebuild.
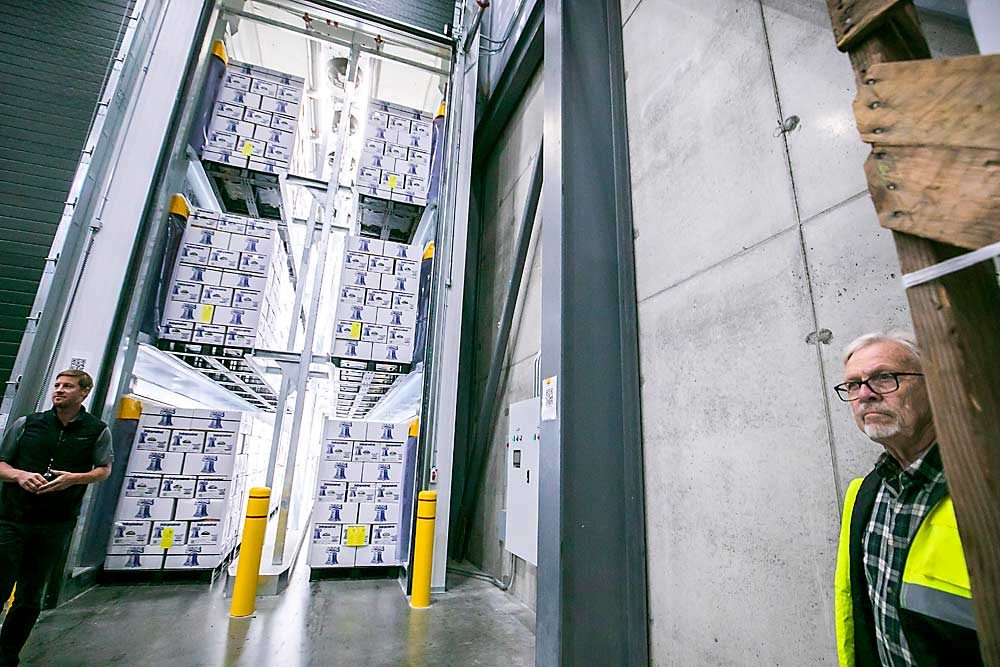
Terry Beckwith, who has worked for the packer since 1969, was involved in much of the design. Even 10 years ago, he couldn’t have imagined the types of technology available today, he said.
The company began operating its new line in January 2019, about 14 months after the fire.
Upgrades
Mount Adams also went high-tech in other areas of the facility, which was built three stories high to adjust for the small property along a steep hillside on the north bank of the Columbia River.
Two multilevel conditioning rooms replaced the four small, dated ones from before. In the new rooms, crews heat fruit, treat it with ethylene and cool it all in one place, instead of removing it to cool. The process is not only faster, it leads to better fruit because the company has more control over temperatures, Gibson said.
Conditioning rooms have become a staple in the pear industry. Some large retailers now insist on conditioned pears, which studies show have a higher demand from consumers because they are reliably ready to eat within days of purchase.
“It’s the present,” Gibson said. “It’s not the future. It’s here.”

The company even used the opportunity to reinvent its image. Officials consolidated its subsidiaries — The Dalles Fruit Co., Underwood Fruit and Warehouse, and several orchards — under the single name Mount Adams Fruit and released a new logo.
The changes modernize the farming side of the company’s 2,000 acres, too. PickTrace and FieldClock, examples of labor management software, are integrated into the central computer system, so managers can track the pace of their workers in real time.
“It’s faster for our crew bosses to keep track of what their workers do,” said Antonio Quintana, orchard manager.
Meanwhile, sales representatives in Yakima — 110 miles away — can trace fruit from picker to packer to customer through Salesforce, cloud-based computer software also used by NBC and Coca-Cola, said Sara Sherrell, senior operations analyst.
The fire, though frustrating, positioned the company to integrate all the new technology under a single, connected system.
“It really gave us the opportunity to have the best of everything,” said Ed Ing, a longtime manager at Mount Adams.
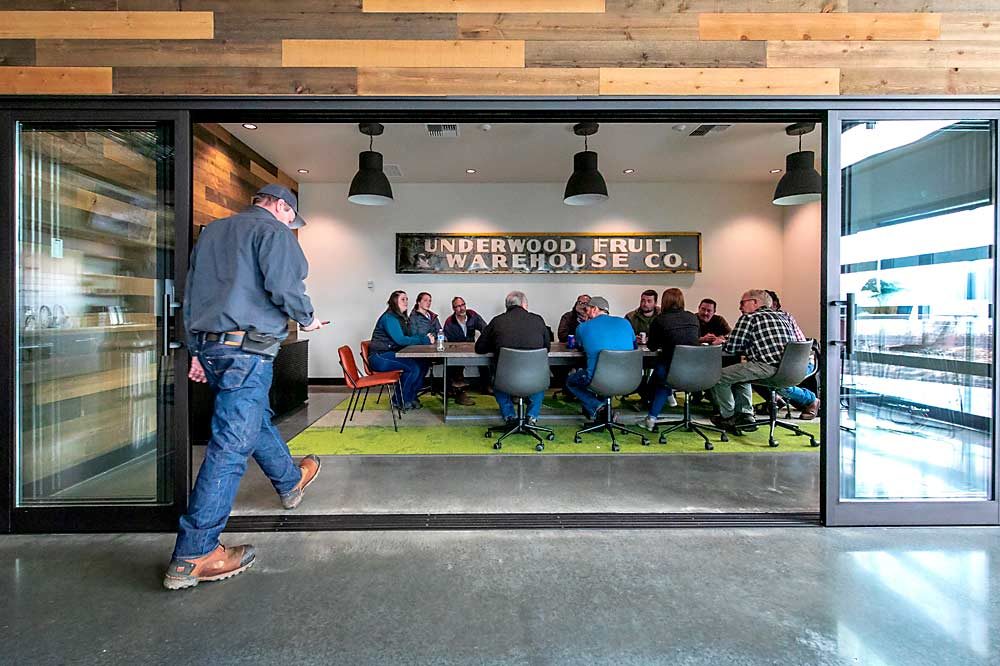
Growers
Outside growers are also excited about the technology to reduce labor costs and improve packout consistency.
“(If) my packing costs go down, that’s more money in my pocket,” said Erick von Lubken of von Lubken Orchards, a fourth-generation pear grower in Hood River, Oregon.
He likes watching packers run his fruit. Even workers trying to be consistent will inevitably stumble, especially if the grower is standing over them. A camera is objective. “It doesn’t care what lot number it is,” he said.
Third-generation pear grower Jon Riggleman of Hood River echoed that. He suspects optical sorters drive down packouts but that should boost prices in the end by delivering higher quality.
“It does pull more fruit out, but I think definitely in the long term it will be more consistent,” he said.
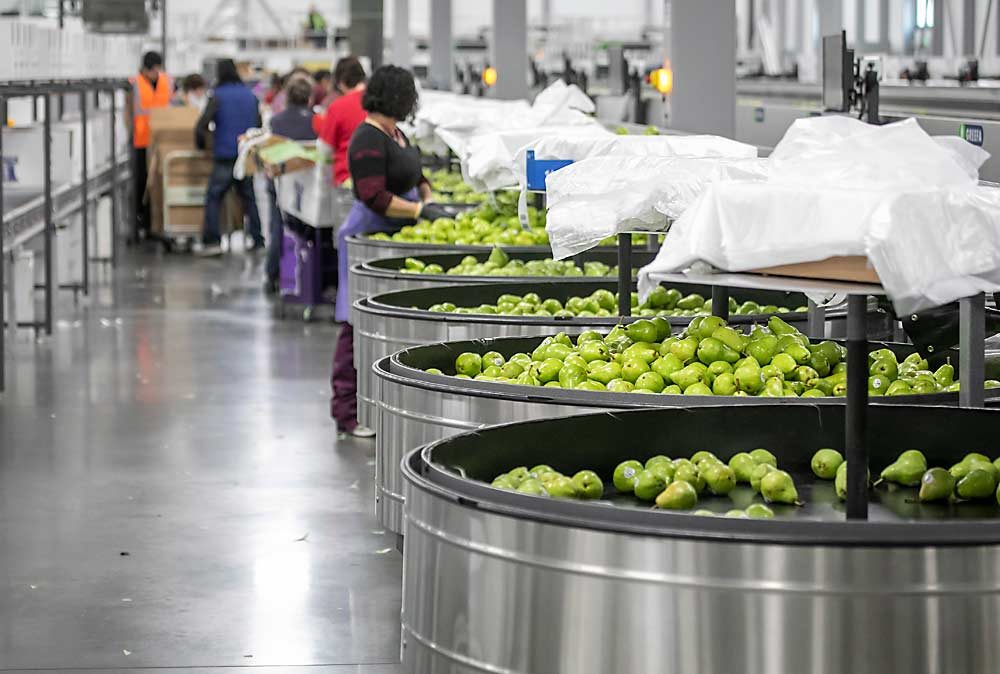
Ripple effect
Mount Adams’ investments are part of a ripple effect in the industry, as one packer upgrade inevitably leads to another.
It’s more than keeping up with the Joneses, though. Pear packing technology is new and shippers are sometimes reluctant to be the guinea pig. When one company finally installs one, others have an example to check out before making their own decisions.
“It gives us an opportunity to look at what we can do and should do,” said Ray Schmitten, a horticulturist with Blue Star Growers, a pear packer in Cashmere, Washington. Blue Star has recently added an automated palletizer and upgraded its conditioning rooms, first built 15 years ago.

Just across the Columbia River from Mount Adams, Duckwall Fruit of Hood River is installing a Unitec optical sorter that uses pear-shaped cups to flip fruit over, exposing the entire pear to infrared and optical sorting cameras, said assistant production manager Nathan Duckwall. It’s scheduled to be ready by August, for the 2020 harvest. Diamond Fruit, another Hood River neighbor, started using the same flip-cup Unitec sorter in 2018.
Duckwall plans to upgrade its conditioning rooms, too.
Upgrades such as these are commonplace in the cherry and apple industries and really should be in the pear industry, too, Duckwall said.
“It’s exciting to see the pear industry catch up a little bit,” Duckwall said. •
—by Ross Courtney
After the fire
A 2017 fire forced Mount Adams Fruit, a Bingen, Washington, pear packer, to make major technology investments all at once in its new facility. New tools and technology include:
—Handwashing stations linked to turnstiles, so workers can’t even enter the packing line without washing their hands. Before, supervisors had to police workers and sometimes discipline them over handwashing, said Doug Gibson, company vice president.
—A drying room with walls that can be disinfected, replacing tunnels that were difficult to clean.
—Positive airflow between the packing line and the dump tanks, sometimes called the “wet” room, so when someone opens a door, air rushes out, not in.
—An automated storage and retrieval system with a computerized shuttle to fetch pallets. Mount Adams is only the third installation of the system, and the first for the fruit industry, by Advance Storage Products of Huntington Beach, California. Overall, the company has nearly eliminated the use of indoor forklifts.
—A security system that checks people in through facial recognition and a bar code.
—R. Courtney
Related:
—Advances in automation pump up pear packers
—Underwood Fruit plans to rebuild after fire
Leave A Comment