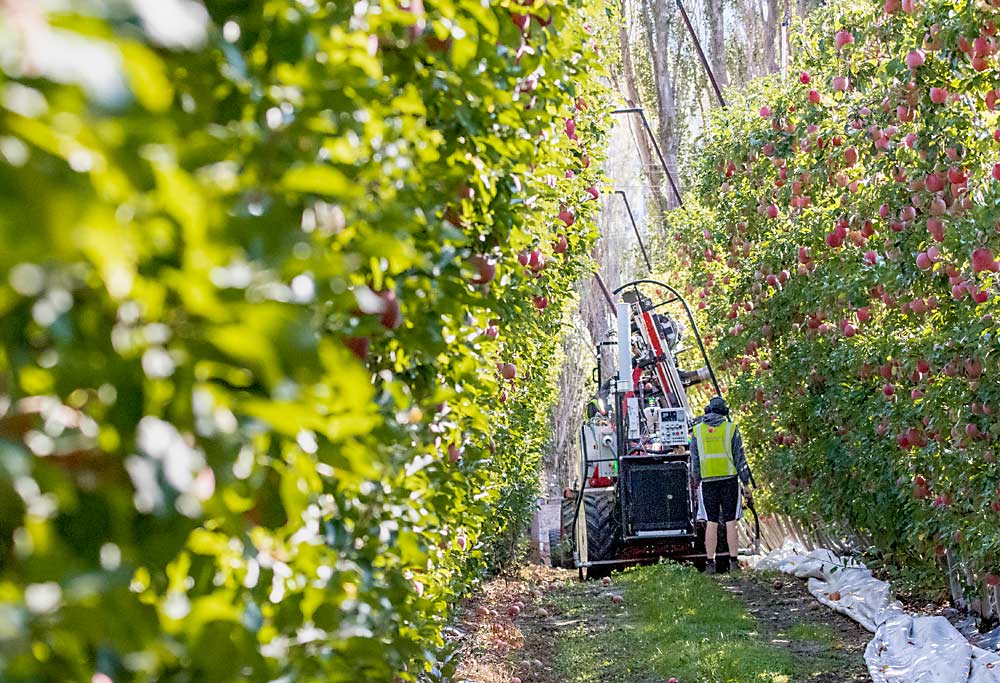
Two companies building robotic apple pickers continued their march toward commercialization, though the coronavirus slowed the pace of one of them.
One company, Abundant Robotics of Hayward, California, says it has the kinks worked out of its prototype and is ready to build a fleet for commercial use. Meanwhile, its Israeli competitor, FF Robotics, spent the year making improvements to its machine but has been grounded from U.S. trials by coronavirus travel restrictions.
In 2020, Abundant continued small-scale commercial trials in Washington and New Zealand and experienced few of the equipment breakdowns that plagued its prototype in 2019, when the machine struggled to maintain a consistent harvest due to broken parts and machinery, said company CEO Dan Steere. Initial reports show packouts similar to hand-picked fruit.
The company considers itself ready to scale up. Soon —though Steere wouldn’t specify when — Abundant will begin manufacturing more robotic pickers in hopes of sending fleets of them, perhaps hundreds, to orchards around the globe. That’s the vision.
“The next step for us is to start to build up a fleet of these,” Steere said.
The company is banking on a business model of custom harvesting, much like what Abundant has been doing the previous few years on a small scale with its commercial trials. Growers would not purchase their own robotic pickers but instead would contract with the robotics company, which would send multiple machines with an operator.
The self-steering robotic picker uses computer vision and a vacuum end-effector to identify, select and remove fruit, transferring it down a path of padded tubes to a bin carried on the machine. The robot can clean pick trees or color pick, Steere said. It also has four-wheel independent steering, enabling the machine to turn around at the end of the row and head back down the same row.
Abundant estimates its machine can access between 50 percent and 90 percent of fruit on trees, depending on canopy management.
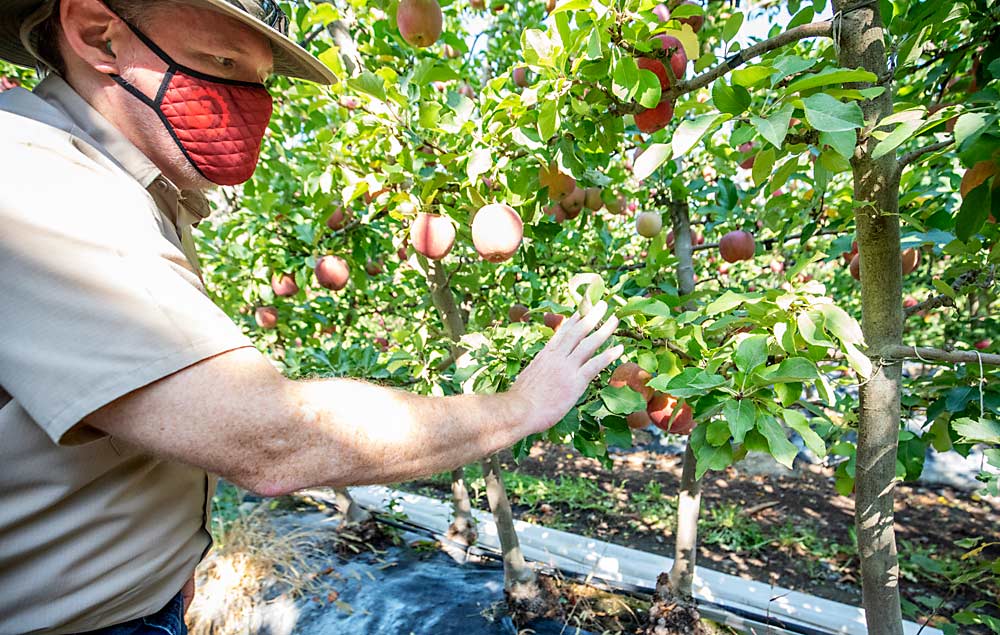
Customer reaction
Abundant picked five different varieties for eight Washington companies, but as of early October, this issue’s press deadline, only Zirkle Fruit of Selah had packed any. The packouts were about the same as hand-picked fruit, said Aran Urlacher, Zirkle’s Mattawa-area manager.
To the naked eye, hand-picked bins appeared to have better color, but the packout reports were equal within statistical differences, Urlacher said, though he declined to share any actual numbers.
The only differences were punctures, the most common cause of culls on the machine-picked fruit, with the machine-picked fruit having more punctures than hand-picked. Punctures occur when the vacuum system drags apples across rough branches, though they often happen with hand picking, too, Steere said.
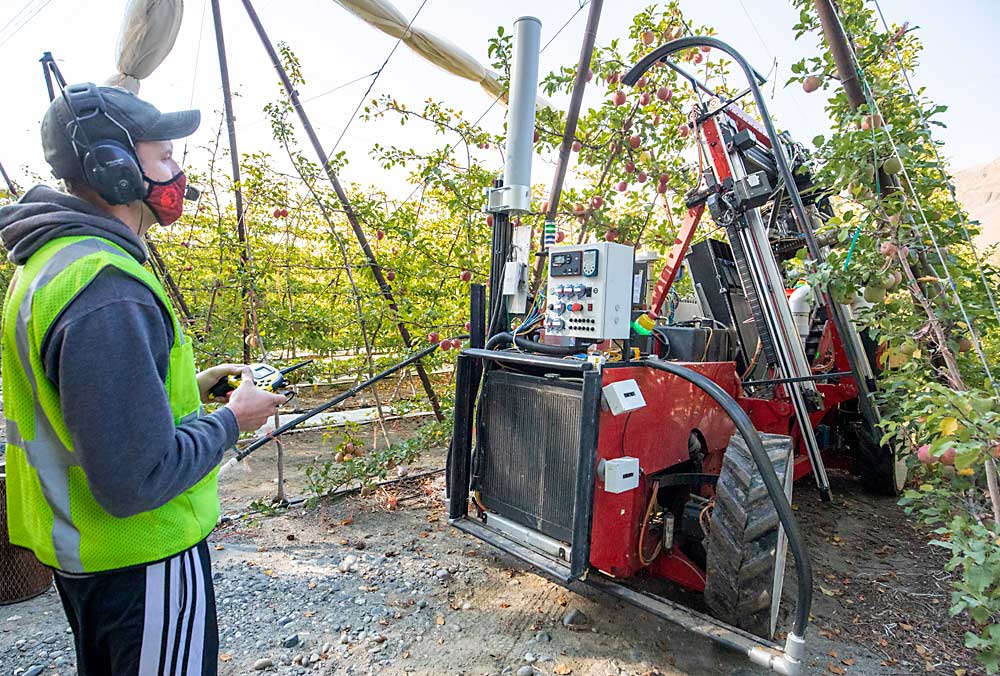
Abundant picked about 50 bins of Brookfield Galas for Zirkle. By early October, Zirkle had packed about 20 of them, leaving the rest in storage for more packing trials later.
That’s not a big sample size, but Urlacher has seen enough of Abundant’s performance progress over the past several years to be willing to scale up with the company in the future, he said.
“I know they’re just going to keep getting better,” Urlacher said.
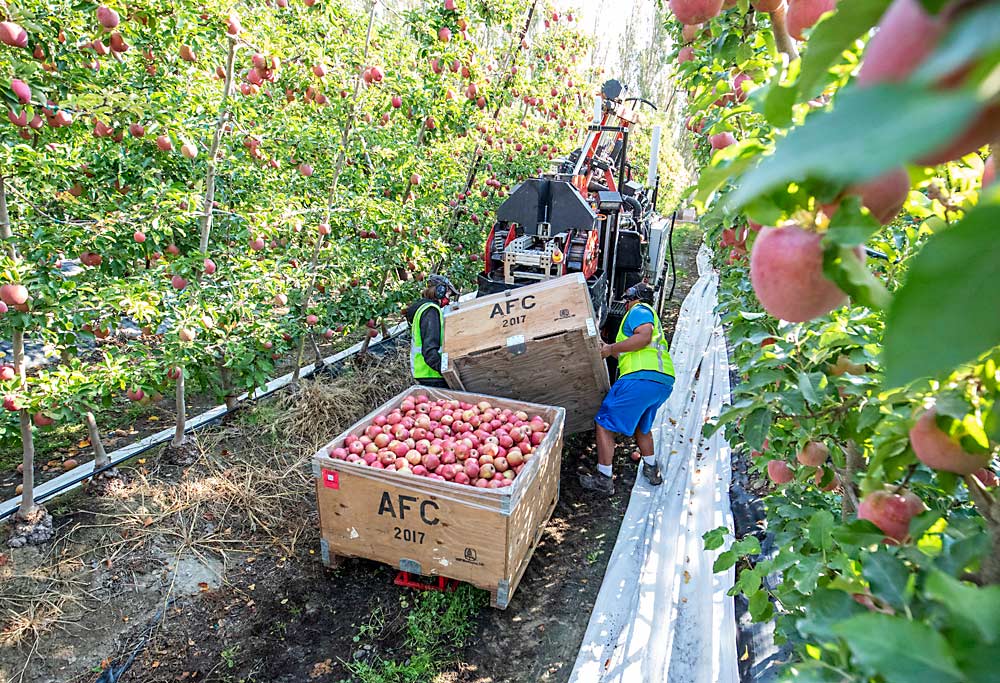
Besides, hand labor is just going to get more problematic, with rising wages, smokier skies and, heaven forbid, another pandemic, he said. “I only see us going forward on this (automated harvest),” Urlacher said.
FF Robotics
Israeli company FF Robotics continued improvements on its robotic picker, which uses multiple arms with pronged “fingers” to grip, twist and pull fruit from trees, but was grounded from any trials outside the country due to the coronavirus travel restrictions, said Avi Kahani, CEO.
“COVID-19 impacted us a lot,” he said.
Israel was hard-hit by the virus and spent a lot of time in lockdown with airports closed. The company had planned to take one of its robots to Washington for trials and deliver a second to a potential customer in France. Kahani and his team had to cancel both of those plans.
Instead, the team spent the year in their Haifa warehouse making improvements and designing a smaller version of their machine, which will more easily fit inside apple rows and mount on a picking platform made by Automated Ag Systems of Moses Lake, Washington. They even hired a few extra workers.
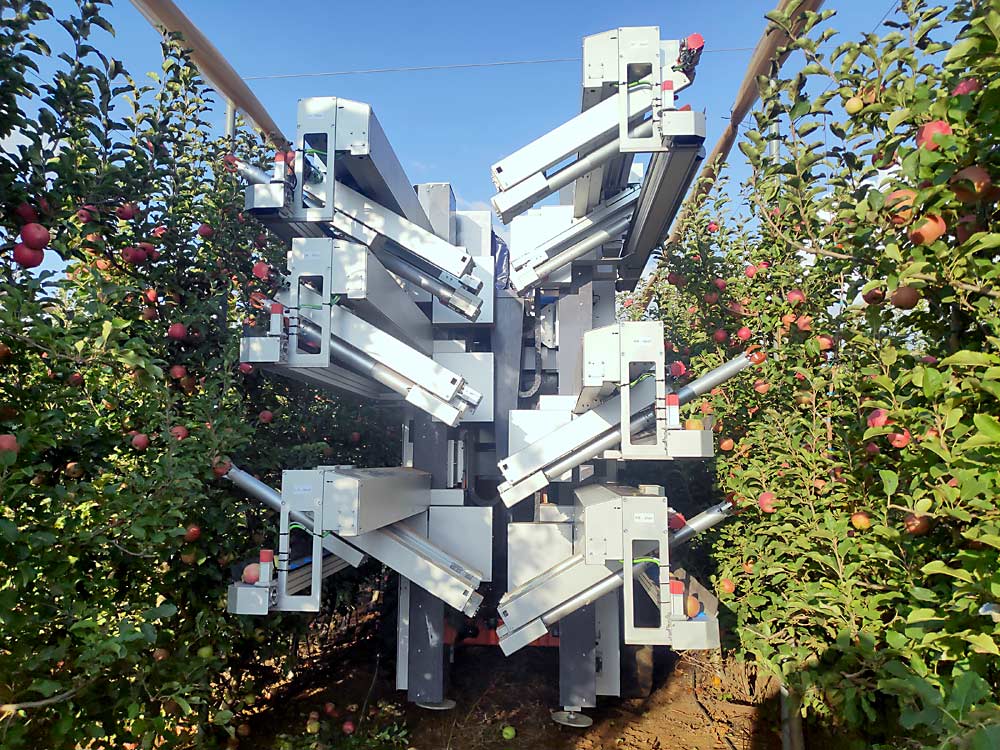
Engineers also improved other elements. They:
—Eliminated tubes from its conveyor system, after apples sometimes clogged them.
—Added a three-dimensional movement to the end-effectors’ existing twisting motion, to pick apples more cleanly.
—Integrated with Automated Ag’s bin system that automatically loads empty bins and discharges full ones.
The company, funded in part by a Washington Tree Fruit Research Commission grant, plans to ask for an unfunded extension on their work, due to the coronavirus, Kahani said.
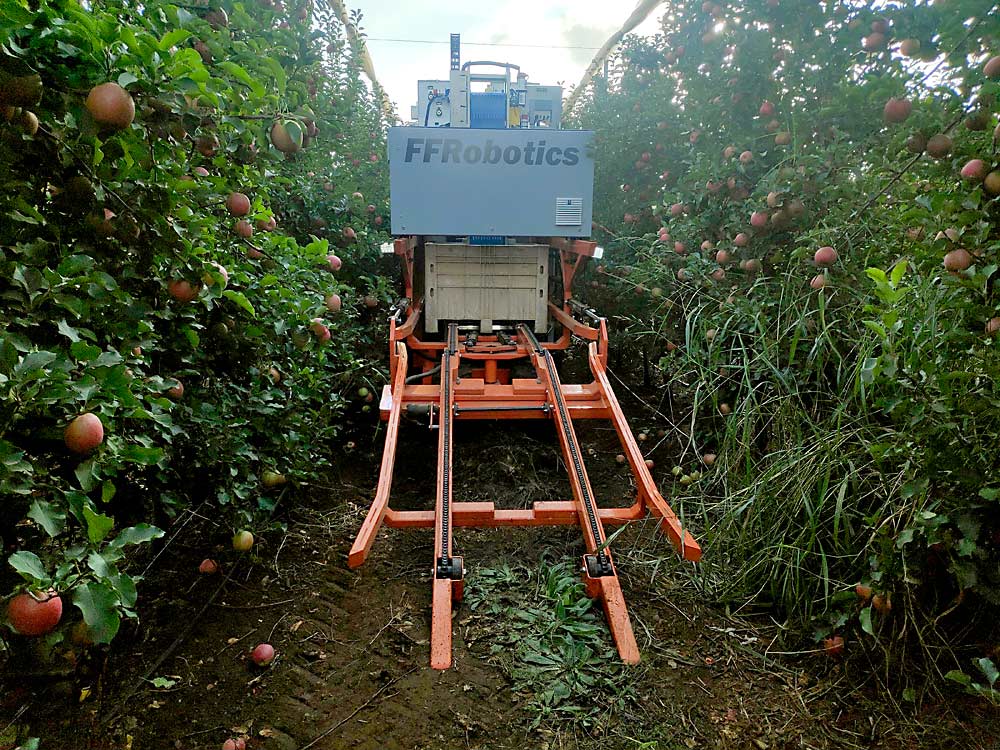
Unlike Abundant, FF Robotics plans to sell robots outright to growers, who will eventually be able to use them for pruning, thinning and training as the company improves the technology, Kahani said. He declined to share a potential price tag, but said his goal is a three-year return on investment.
“For the long term, I believe the machine should be owned by them,” he said.
—by Ross Courtney
Leave A Comment