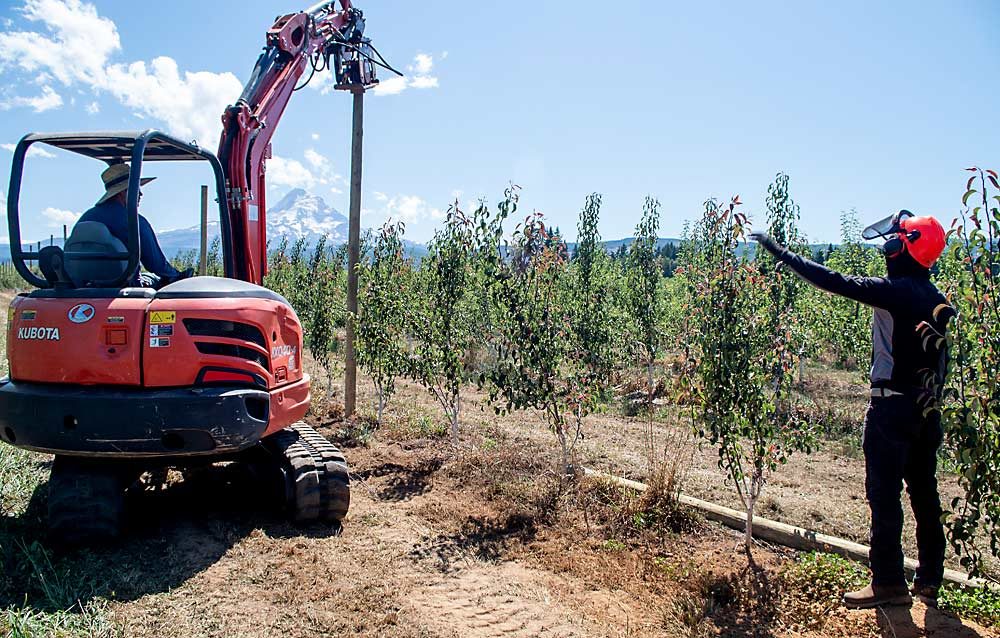
The needs for the pear industry are great — dwarfing cold-hardy rootstocks, new varieties to entice consumers — but that isn’t slowing growers from testing innovative growing methods in their orchards.In Oregon’s Hood River area, growers are experimenting with modern trellis systems that offer the benefits of improving light interception and spray coverage, while increasing the potential for mechanization and supporting more dwarfing rootstocks down the road.
“There is increasing interest in trellising and training pears in the Hood River area,” said Ashley Thompson, assistant professor of horticulture at Oregon State University and a member of the OSU Extension fruit tree faculty for Wasco and Hood River counties.
Thompson organized a tour last August that gave attendees an opportunity to see different pear trellis systems in place at two farms and learn how to install wood and steel trellis systems. Many growers in the Hood River area are putting in trellises — both angled V and central leader styles — when they remove their old pear blocks, Thompson said.
Because pear growers don’t have access to truly dwarfing rootstocks, some growers have also found success using a two-leader system to control vigor, Thompson said.
No matter the system, Thompson recommends trellising young blocks at the outset, rather than installing trellis around an older block.
“It’s really easy to overengineer or underengineer your trellis,” Thompson said. “Keeping (rows to) 500 feet and every 40 feet putting a post in, that’s a really good way to keep your trellis well-engineered.”
More recommendations:
—Use good-quality treated wood (yellow or lodgepole pine), concrete or metal posts.
—For wood trellises, use 5-inch diameter posts. They are 50 percent stronger than 4-inch posts.
—Use 12-, 14- or 16-foot posts. Ten-foot posts are too short, and 12-foot posts are often too short.
—Bury one-third of the post underground.
—Place your anchor in undisturbed soil at a 10-degree angle.
—Install the wire on the windward side of the posts.
—Ensure your end post, wire and ground form an equilateral triangle.
Thompson is currently working with Clark Seavert, OSU ag economist, to understand the economics of high-density pears for Oregon growers by focusing on precocity and production.
“Overall, I see trellises as a technology growers can use to adapt to future challenges ranging from labor issues to climate change,” Thompson said. “We can develop more easily picked and pruned systems as labor becomes a bigger and more costly issue. We can also use trellises to deploy shade cloths or hail nets. They are truly versatile.”
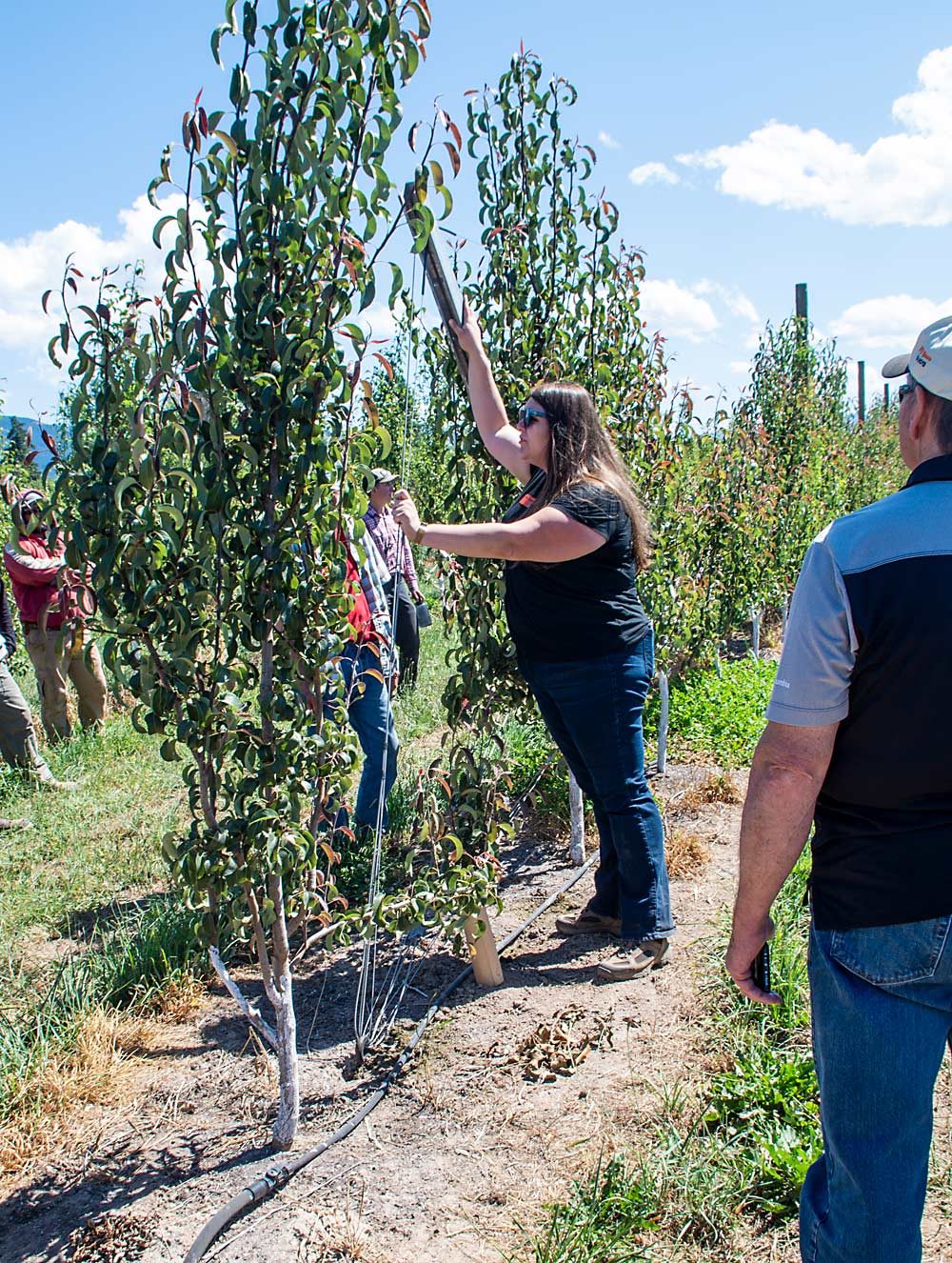
Vertical and V-trellis at McCarthy Family Farm
At McCarthy Family Farm near Mount Hood, Adam McCarthy shared his experiences growing Bartlett and Red Anjou on vertical and V-trellis systems.
From a labor perspective, McCarthy said he prefers the V-trellis. “Everything you’re doing, your people can move faster,” he said. “They don’t have to put the ladder in the canopy. They can reach 60 to 70 percent from the ground in these V systems.”
When asked about tree training, McCarthy said he likes to see a branch at about 6 inches below the wire, coming up at about a 30-degree angle.
“More often than not, those aren’t there, and you have to go with your best option,” he said. Sometimes that means grabbing from behind and bending the limb to the wire, he said. He avoids bending limbs down to the wire, if possible.
On their vertical trellis, McCarthy waits until late May or June to tip the central leader about 3 inches above the wire, in an effort to get the leader to produce the desired limb 6 inches below the wire. And, he said, they normally stub off steep angles near the tip. “They’ll usually throw a branch at a flatter angle the next year,” he said.
In a follow-up interview, Thompson said research has shown training branches at a 30-degree angle can increase flowering and fruit set while controlling vigor for some varieties.
McCarthy now uses 4- to 5-inch diameter 12-foot lodgepole posts set about 3 feet in the ground and 30 to 35 feet apart, after smaller poles failed under a heavy snow load.
When installing a trellis system, McCarthy advised adding at least a year to production expectations. “Everything has to go according to plan,” he said. “As you all know in farming, nothing ever goes according to plan.”
Vertical trellis installation at Dahle Orchards
Down the road at Dahle Orchards, Gabe Dahle showed tourgoers how to install wood and steel trellis posts and attach wires in his father’s orchard. The trellises were installed in existing blocks of Gem pears, planted in 50-foot rows. Dahle, who works for Orchard and Vineyard Supply, said the trees were planted in 2018, before his father made the decision to go with trellising.
“Most people wouldn’t see the benefit of trellising in an existing block,” Dahle said. “It’s just going to help the trees get into production faster.”
For the wood system, Dahle’s crew used an excavator with a Ho-Pac vibratory plate compactor to install 14-foot posts spaced 25 feet apart. “That’s a little close, but it’s not going to hurt anything,” Dahle said.
The posts — blunt, not pointed, Dahle recommended — were measured and marked ahead of time to ensure each was pounded 3 feet into the ground.
With the posts installed, they ran 12.5-gauge class 3 wire and fastened it with 2-inch staples. The trellis had four wires, and they plan to add another when the trees grow taller.
Dahle often recommends growers go with an 11-foot trellis. “I’ve seen too many 9-foot trellises where they could have gone to one more wire and they aren’t able to,” Dahle said. “It doesn’t cost that much more overall to go a little bit higher.”
Thompson said the number of wires really depends on the variety and the desired branch angle. For example, when Anjou branches grow near horizontal, they produce more shoots and not enough fruit buds, so a 30- to 45-degree angle is preferable, she said.
Antonio Quintana with Mount Adams Fruit said that to adjust their tree training to a 30- to 40-degree angle, they needed more wire. They’ve gone with up to nine wires on their V-trellis.
To encourage buds to break near the wire, Thompson suggested scoring the leader. “I know that’s really labor intensive, but Antonio and the folks at Mount Adams, they do a lot of scoring to get those buds to break in the right place, and they’ve been very successful with that,” she said.
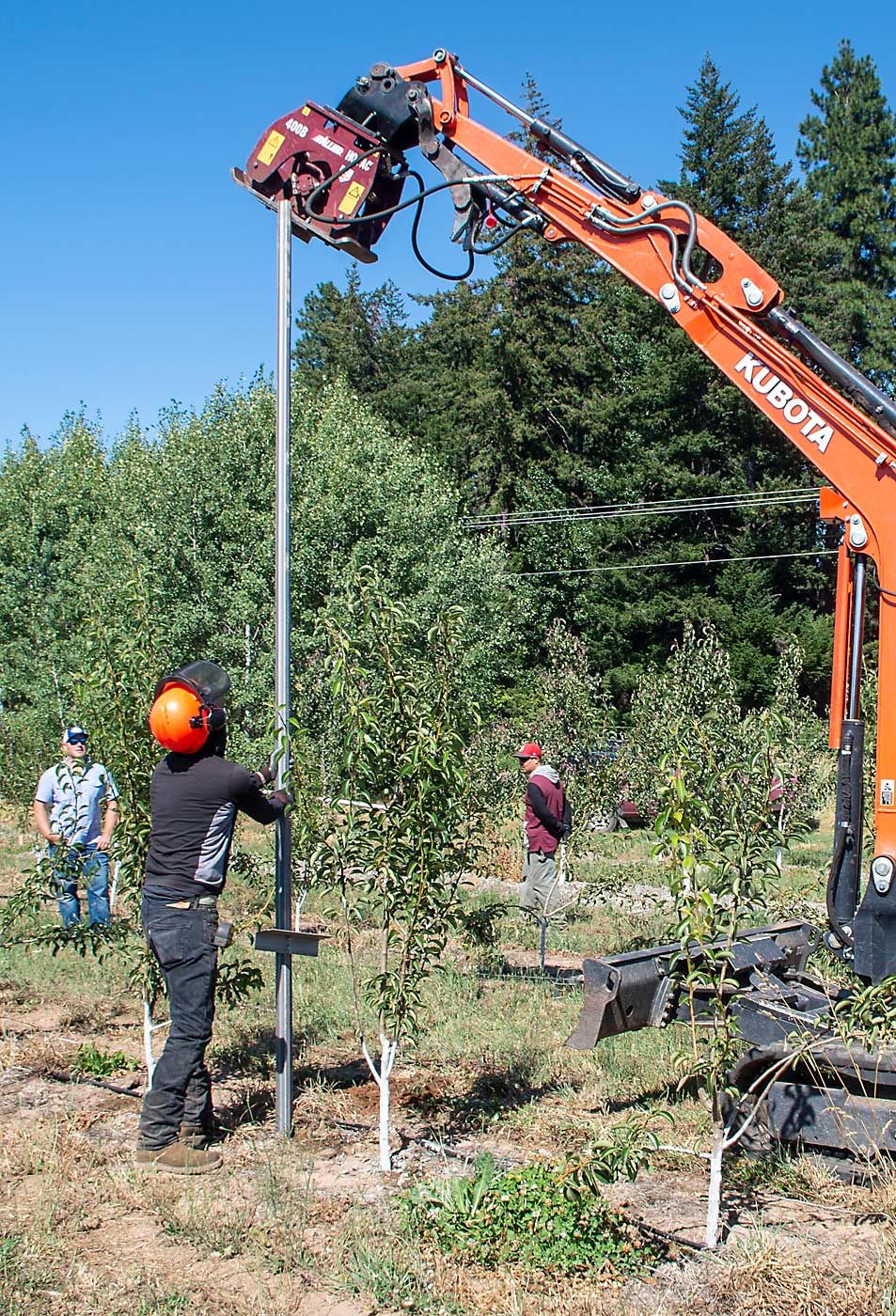
In an adjacent row, the crew installed steel trellis posts.
“The challenge with steel vertical trellis is stability, because it doesn’t have that footprint that wood posts have and it doesn’t have the cross brace a V-trellis has,” Dahle said. With steel vertical trellis posts, he adds foot plates to keep the posts from moving back and forth and ensure the posts go in to the correct depth.
When running metal wire through metal posts, Dahle sleeves the wire with 8 inches of Insul-Tube weatherproof insulation.
For durability, Dahle favors steel trellising. He estimated that about 5 percent of wood poles will fail at 10 years and another 5 to 10 percent at 15 years. “With steel, there just really isn’t much loss,” he said. •
—by Jonelle Mejica
Making an orchard platform-friendly
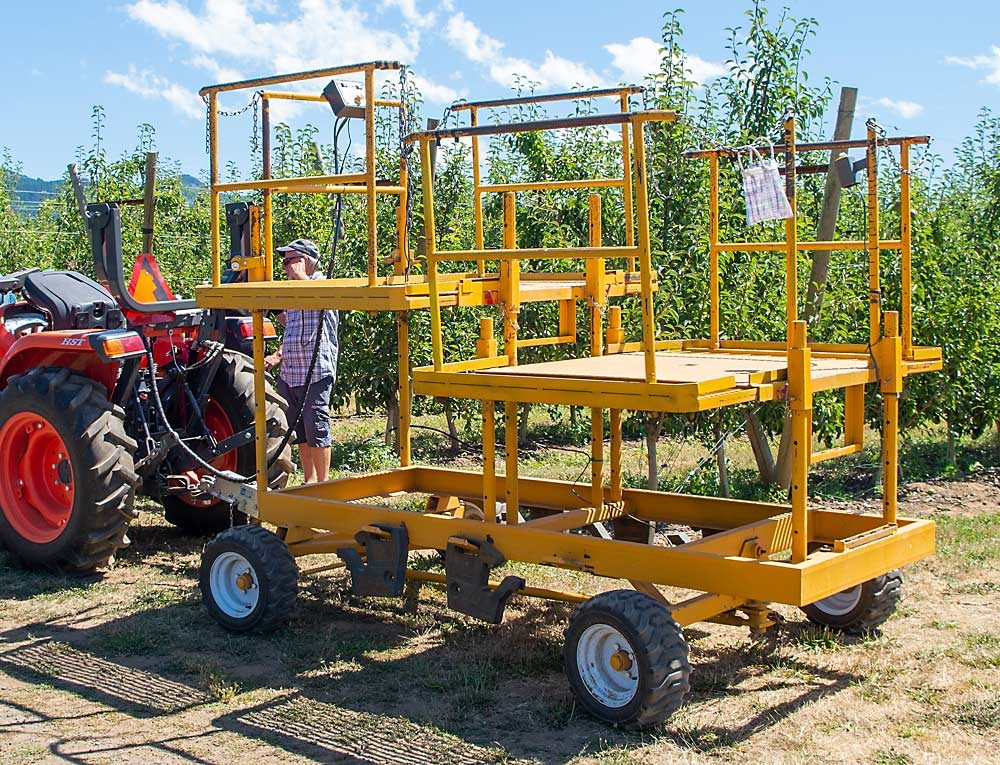
One of the benefits of trellising is increased efficiency, and platforms offer one of the opportunities for reaching better results.
“Platforms mean efficiency,” said Mount Hood-area pear grower Adam McCarthy. “For thinning and tree training in these blocks, I would rather have the platform than the ladders.”
The McCarthy family built its own platform, using a chassis purchased from the Midwest and adding a 12-volt motor to the steering wheel to create an operator-controlled platform.
Using the platform, they’ve almost doubled their pruning and thinning efficiency, McCarthy said. The biggest challenge is getting a consistent travel speed.
He’s working with Oregon State University to develop metrics that will help determine how workers are actually using the new technology to increase their efficiency.
Mike McCarthy, Adam’s father, said their employees are also happy with the platform. “Workers really seem to like it,” he said. “It’s less work than going up and down the ladder and moving the ladder. They get on, and they focus on the task.”
—J. Mejica
Related:
—Tips to build a trusty trellis
—Tips from Trellising 101
—Avoiding trellis failures
Leave A Comment