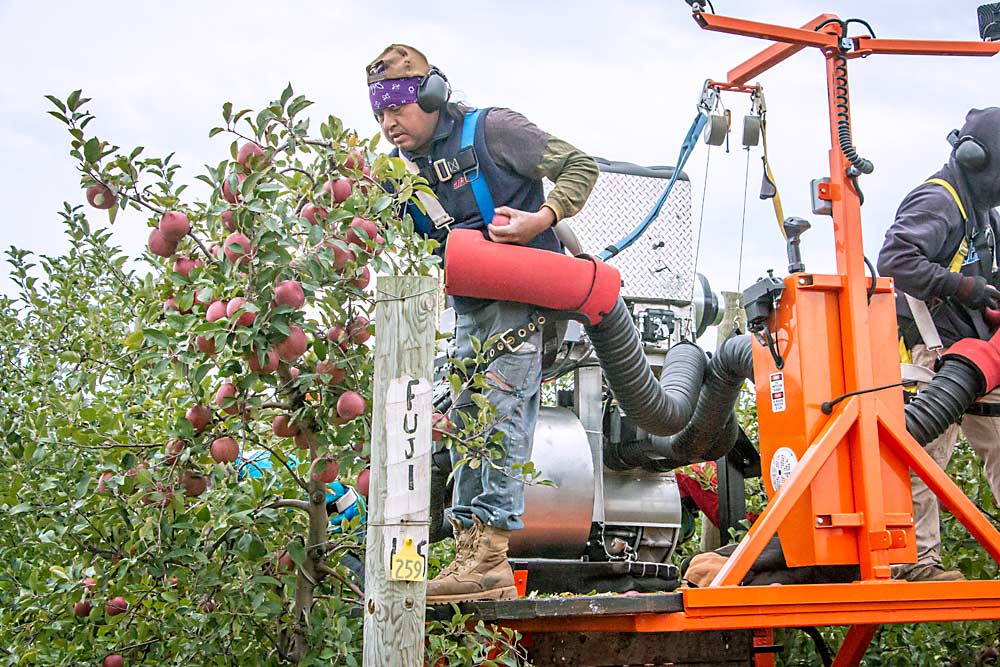
From across apple country, two partners are putting the final touches on a harvest assist machine they hope will be the future of apple harvesting.
DBR Conveyor Concepts of Conklin, Michigan, and Automated Ag Systems of Moses Lake, Washington, figured out how to easily attach and detach the machine, which they named the Apple Vacuum System, to platforms many growers already own. They plan to start selling the latest iteration of the harvester, called the Bandit Cyclone, after the 2020 harvest.
Pickers on the platform place their apples into vacuum tubes that suck the fruit into a rotating dispenser, gently depositing them into a bin underneath. Trials have shown that workers using the vacuum harvester pick apples faster than those on a normal platform, far more efficiently than those using ladders, and don’t bruise apples any more than those using either method.
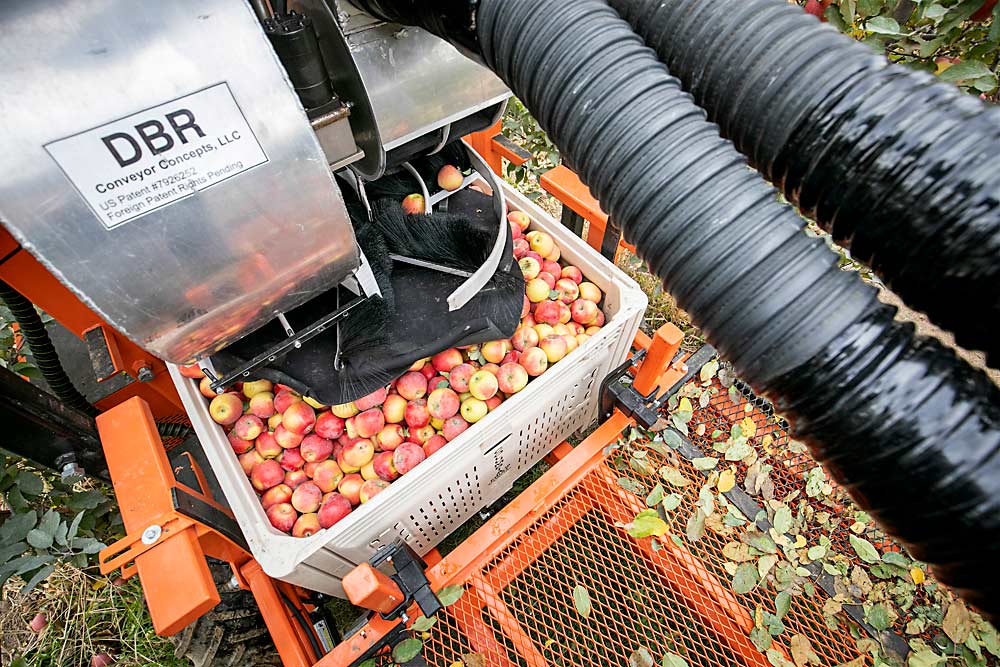
“I think that this type of machine is the future of apple harvesting,” said Justin Finkler, operations manager for Riveridge Produce Marketing in Sparta, Michigan.
Keith Veselka, an orchard operations manager in Washington state who’s also worked with the Bandit Cyclone, agreed. The near future, at least. Fully automated harvesters might be the long-term future of apple harvesting, but that’s still a long way off, he said. A harvest assist like the vacuum machine might be the bridge between that distant future and current harvesting methods.
With increasingly modern orchard architectures and a greater reliance on mobile platforms, Veselka believes the vacuum system would be a good fit for most Washington orchards. After participating in trials, his company is considering purchasing the technology once it’s ready for commercial sale.
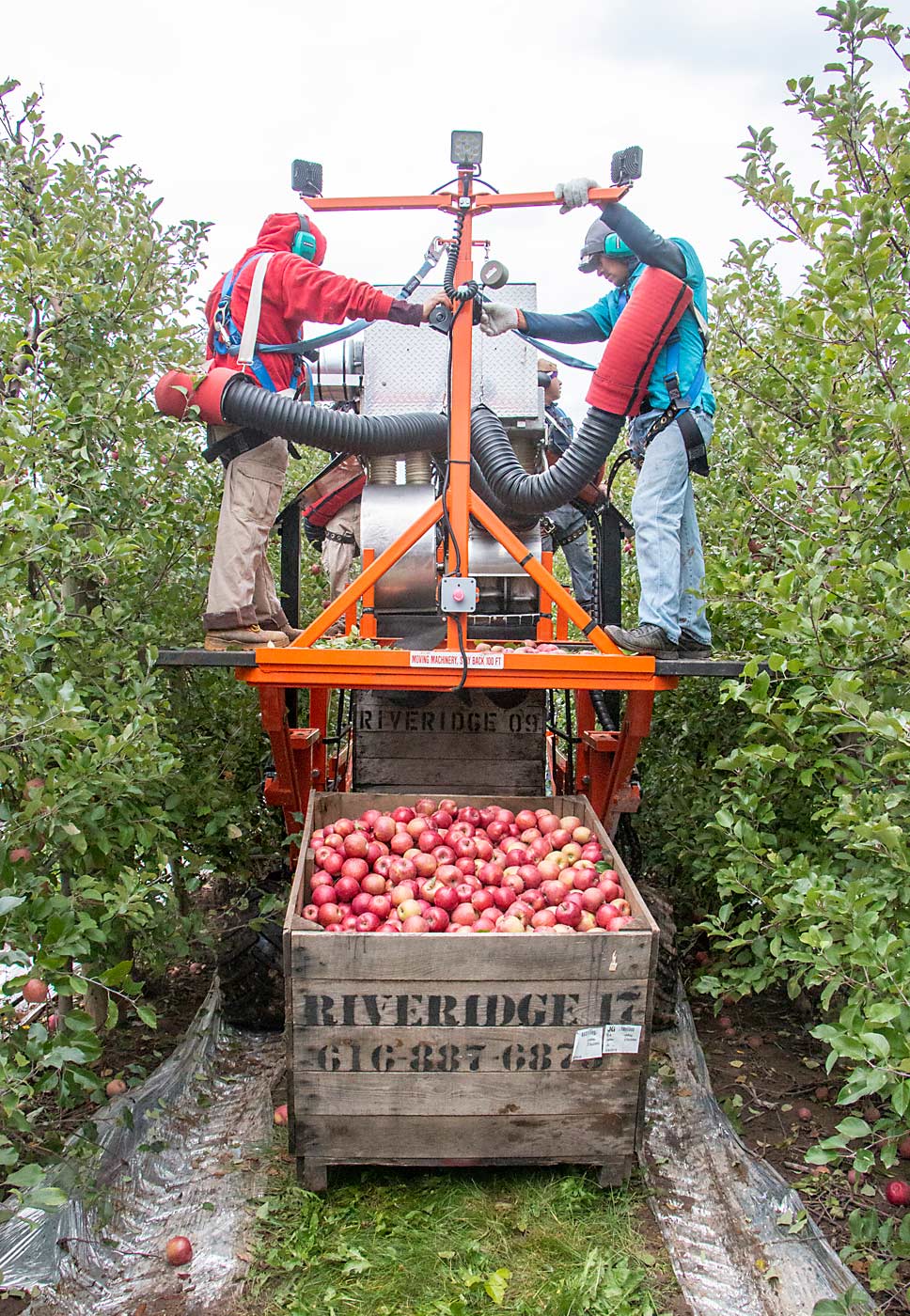
Over a decade in the making, the wait won’t be much longer. The machine’s designers plan to spend most of this year working out the final kinks, or “putting a little lipstick on the pig,” as one of them, JJ Dagorret, put it. The model being developed in Washington state is a little different from the model being developed in Michigan, reflecting the different orchard sizes between the two states and the different approaches of the two partners.
Long evolution
The DBR principals — grower Mike Rasch, welder and manufacturer Phil Brown, and Chuck Dietrich, an engineer and technician with a background in vacuum equipment — have been developing the Apple Vacuum System for a dozen years. They first approached Dagorret, owner of Automated Ag, in early 2018. They had sold a few of their vacuum machines, mounted on Brown’s Brownie Quad platform, to customers in the Midwest but wanted to explore the idea of mounting one to Dagorret’s Bandit Xpress, one of the most popular platforms in the Northwest, Rasch said.
The DBR partners have spent a lot of time streamlining the technology that houses and moves the vacuum system through tree rows, a process that accelerated after the partnership with Automated Ag. The original DBR machine had three pieces (tractor, harvester and bin trailer), which they eventually cut down to two (self-propelled harvester and bin trailer). The latest model features a single piece: a self-propelled platform that can pick up empty bins spaced throughout the orchard and discharge full bins out the back. Many growers prefer to deal with bins using this “pass through” method, though the trailer option is still available, Rasch said.
The machine works best in modern, tightly spaced, two-dimensional fruiting wall orchards. It’s designed for picking the tops of trees, about 6 feet and up. Workers would still pick tree bottoms on foot. Selling workers on the new machine can be hard at first, but eventually they realize that if they’re not constantly walking up and down ladders they can pick two or three more bins per day. And they don’t have to carry a bag that gets increasingly heavy, as they would on a regular platform. LED lights attached to the machine allow for night picking as well, Rasch said.
When he agreed to partner with DBR, Dagorret saw an opportunity to make some changes to simplify and streamline the system.
“He’s had the mindset all along of keeping it simple and user-friendly,” Rasch said.
One thing Dagorret did differently was place a mechanical bin filler from MAF Industries, a French manufacturer of packing-line equipment, on his version of the harvester, replacing DBR’s electrically powered, optical bin filler. Washington growers are more familiar with that type of fruit-handling technology, he said.
“It’s one thing we don’t have to manufacture,” Dagorret said. “They send parts if we have issues.”
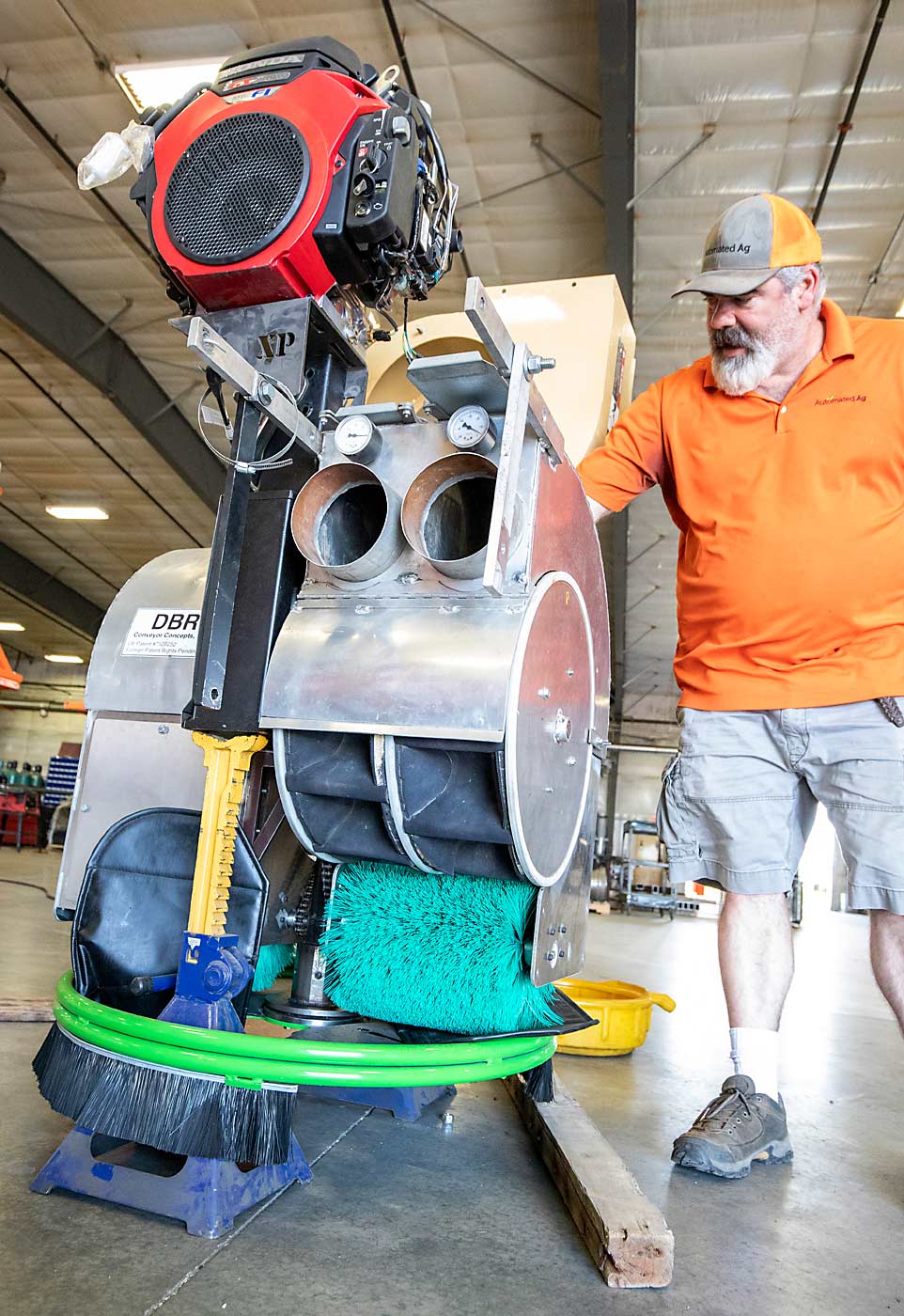
Dagorret wants growers to be able to “plug and play” — easily attach the vacuum system to the platform, easily remove it after harvest to free it up for pruning, thinning and other tasks, and easily repair and replace its parts. He put a lot of thought and work into the machine in the last couple of years, and he thinks it is almost “bulletproof.” One more harvest, some last-minute tweaks, and the technology should be ready for sale.
“We’re at the cusp,” Dagorret said.
One of the last-minute tweaks was reducing the noise level. Rasch said they’ve fitted the harvester in Washington with a higher-torque, fuel-injected motor and a larger blower that allows them to run the unit at a lower RPM, which lowers the decibels and greatly reduces noise. A silencer also can be added, but would increase the height of the unit.
Dagorret also readjusted the ducting vents to blow upward. On top of the noise, high-pressure air was blowing out of the vacuum machine’s housing, hitting tree limbs and knocking fruit to the ground. Readjusting the vents solved that problem. It had the added bonus of blowing cool air on the workers standing on the platform, Dagorret said.
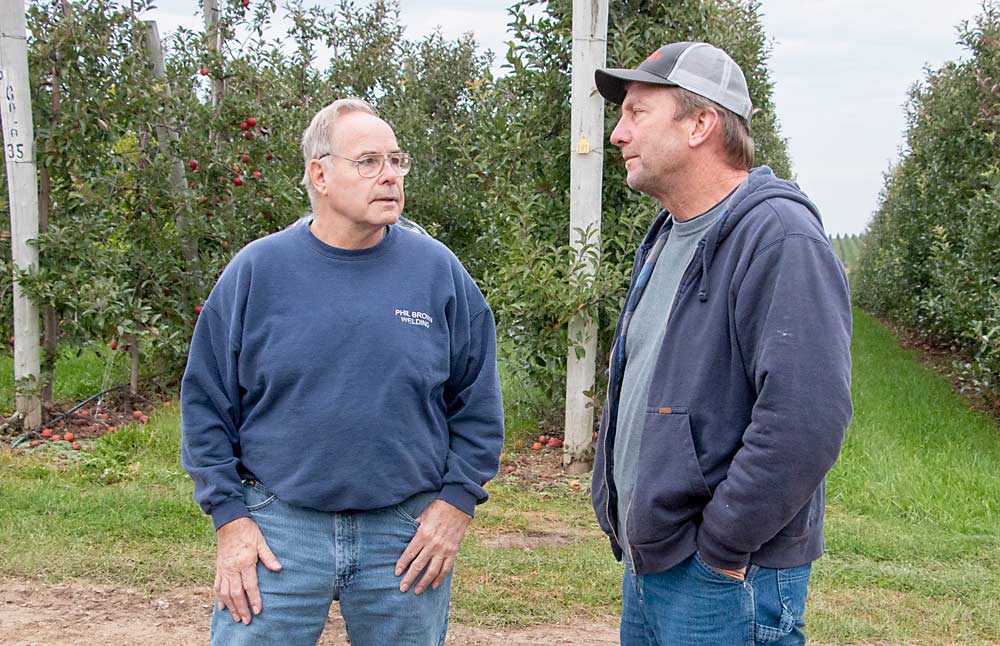
Trials
Riveridge Produce Marketing, one of the largest growers in Michigan, has been trialing the DBR vacuum system for the last decade. The latest version, mounted on a Bandit Xpress, ran through a Riveridge Fuji block last October. Four pickers stood on the platform, in the middle of which stood the vacuum system. Harnesses attached large black hoses, which were connected to the vacuum, to each picker. On the end of the hose, at the picker’s waist level, was an inlet — formerly more of a bucket shape but now more of a trough shape — for pickers to place the apples in. The vacuum system sucked the apples through the padded tubes and into a rotating dispenser that deposited them evenly throughout the bin underneath. When full, the bin was lowered and deposited out the back of the platform.
Riveridge President Don Armock said the DBR/Automated Ag partnership marked a big step forward for the evolution of the machine.
“(The machine) has evolved into a very fruit- and worker-friendly system that also brings efficiency to the entire harvest process,” he said. “We now have a system that is cost-effective and flexible.”
Armock anticipates buying a few of the vacuum machines. Most of Riveridge’s production is on 10- or 11-foot vertical trellis, or 12-foot V-trellis systems, all well suited to the Bandit Cyclone.
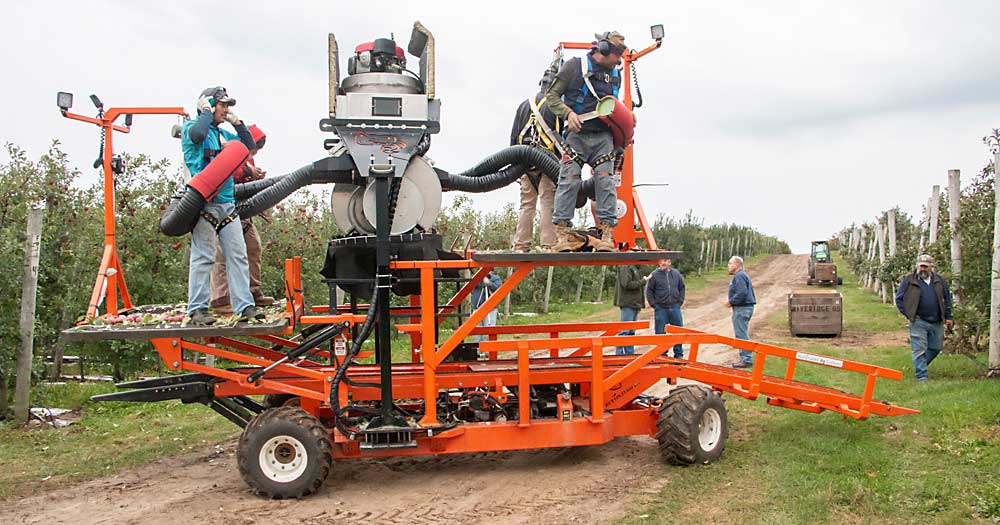
Riveridge will use the machines to pick the tops of trees. The lower parts of the trees will be harvested on foot in the traditional manner, Armock said.
“Workers on the ground are fairly efficient currently,” he said. “The real savings are in the elimination of ladder work and positioning and travel time to the bin.”
At a Stemilt Growers orchard in Quincy, Washington, in 2018, crews using the vacuum system picked 18 bins in six hours, while crews on unaltered platforms picked nine. The vacuum system also led to 2 percentage points less bruising, said orchard manager Bernardo Reyes.
During a second 2018 trial at Occidental Orchards in Zillah, Washington, the Bandit Cyclone was “way quicker” than ladder picking and regular platform picking, filling a bin every 15 minutes, and its rate of bruising was comparable to the other two methods, said Veselka, the operations manager. •
—by Matt Milkovich
Related:
—Prototype picker: Apple Vacuum System tested — Video
—Picking up the pace of picking apples
—Growers try it out
Pennsylvania potential
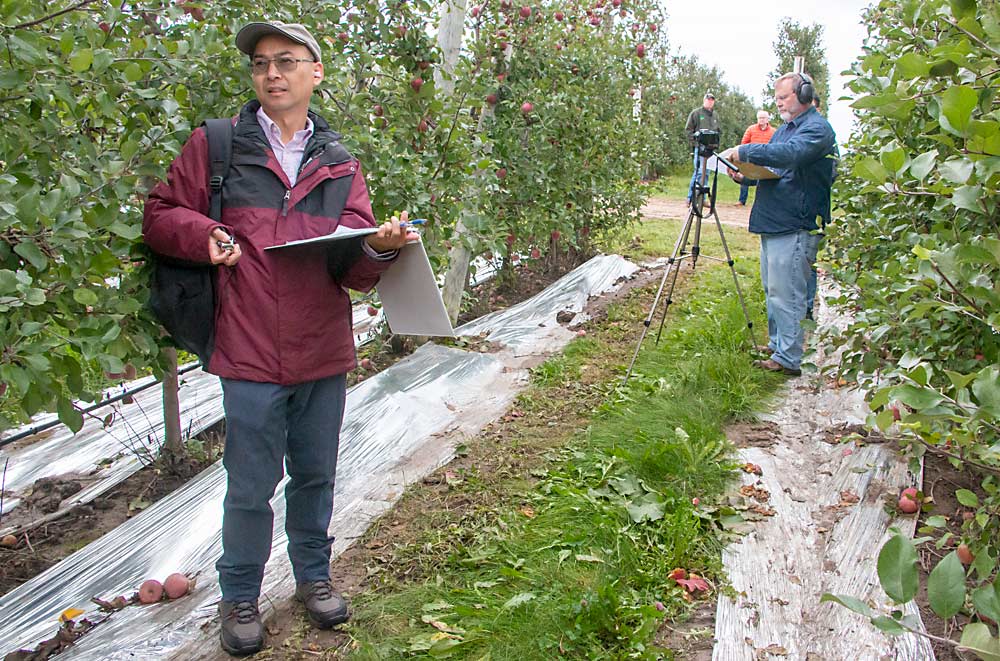
As developers put the Bandit Cyclone through its paces last October at a Riveridge Produce Marketing orchard in Sparta, Michigan, Penn State University researchers gathered data on its performance versus ladder picking.
The researchers plan to test a model at a Pennsylvania farm during the 2020 harvest.
“We are looking for a harvest-assist system that can help Pennsylvania growers improve harvesting efficiency,” said assistant professor Long He, one of the researchers.
Another of the researchers, extension educator Daniel Weber, discussed the Michigan trial’s results with Good Fruit Grower.
“By itself, harvesting from the platform is definitely superior to using a ladder,” Weber said. “By using the platform, bins are filled eight minutes faster than normal, on average.”
But the “killer” is in the bin change-outs and row changes. It takes 2 minutes, on average, for a bin to be released and a new one to be loaded. It takes almost 4 minutes for the machine to turn around and enter a new row, Weber said.
Those row changes would cut into performance gains for orchards with short rows, where frequent turns would be necessary. Some Pennsylvania orchards do not have much space between row ends and barriers such as fences, he said.
However, even including delays associated with bin change-out and row repositioning, the Bandit Cyclone still outperformed ladders by about 3 minutes per bin at the Riveridge trial.
“I suspect there is a minimum row length below which the system becomes too inefficient to operate,” Weber said. “I also suspect that because this system can be operated around the clock due to built-in lighting, the biggest gains may actually be observed by running crews well after dark.”
—M. Milkovich
Leave A Comment