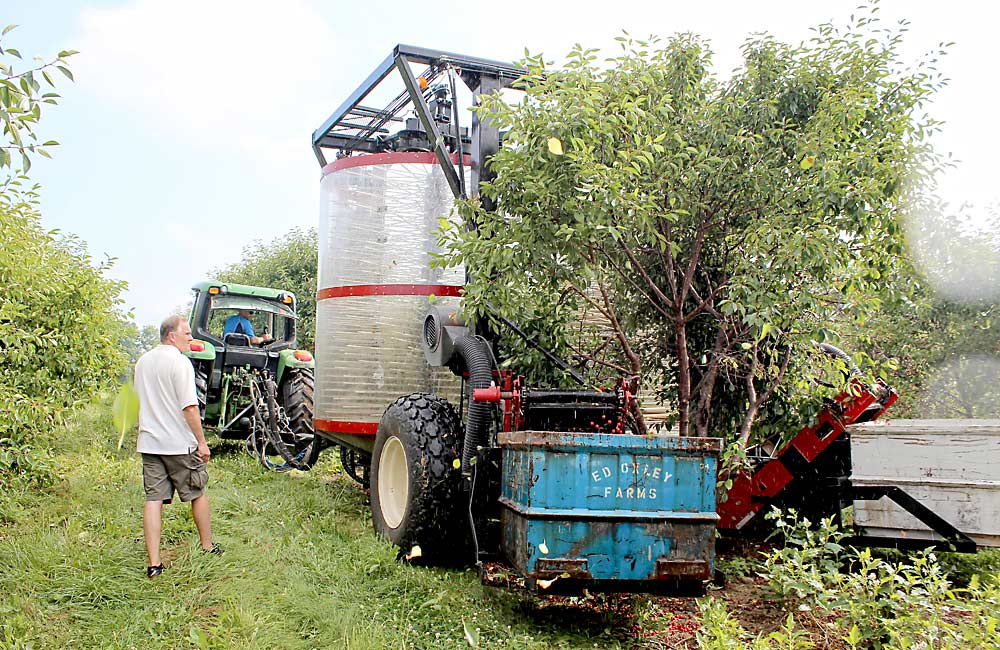
The tart cherry industry has achieved its long-sought goal of over-the-row harvest of high-density trees — in theory, at least. There are dwarfing rootstocks for sale, though not in large amounts. Over-the-row harvesters can be built or modified to harvest fruit, though not cheaply or uniformly.
Laid over these obstacles is the dire financial state of an industry battered by imports and spotted wing drosophila. Most growers are too busy trying to stay afloat to even consider the luxury of investing in higher-density plantings and harvesters.
“The industry is so strapped financially, even before COVID-19, that transitional costs are difficult to overcome,” said Ron Perry, a retired Michigan State University horticulturist.
Perry spent years developing over-the-row harvest methods for tart cherries, a project he has since passed off to MSU horticulturist Todd Einhorn. He said the advantages are obvious: Using the traditional method, mechanical trunk shaking, growers have to wait until trees are 7 or 8 years old before they’re big enough to tolerate shaking — and long-term damage from shakers still ends up shortening tree life. Over-the-row harvest, on the other hand, allows growers to start harvesting by year three, without fear of trunk or canopy damage.
Perry worked closely with harvester manufacturers over the years, renting over-the-row machines and testing their performance on tart cherry trees. The results were impressive. A prototype from Littau Harvester, for example, gathered 20,000 pounds of fruit per acre in a 2017 trial, more than twice the average of trunk shakers. But because of the small size of the industry and its current financial predicament, manufacturers are reluctant to mass-produce cherry harvesters, he said.
The other half of the high-density harvest equation — dwarfing rootstocks — also shows both promise and limitations. Amy Iezzoni, MSU’s tart cherry breeder, said the dwarfing, precocious Gisela rootstocks are an option. There’s also MSU’s new Corette series of dwarfing rootstocks, now commercially available from Sierra Gold Nurseries, Gold Crown Nursery, ProTree Nursery and North American Plants. Because the Corette rootstocks are still considered experimental, there is a volume restriction on purchases, to encourage growers to do trial plantings first.
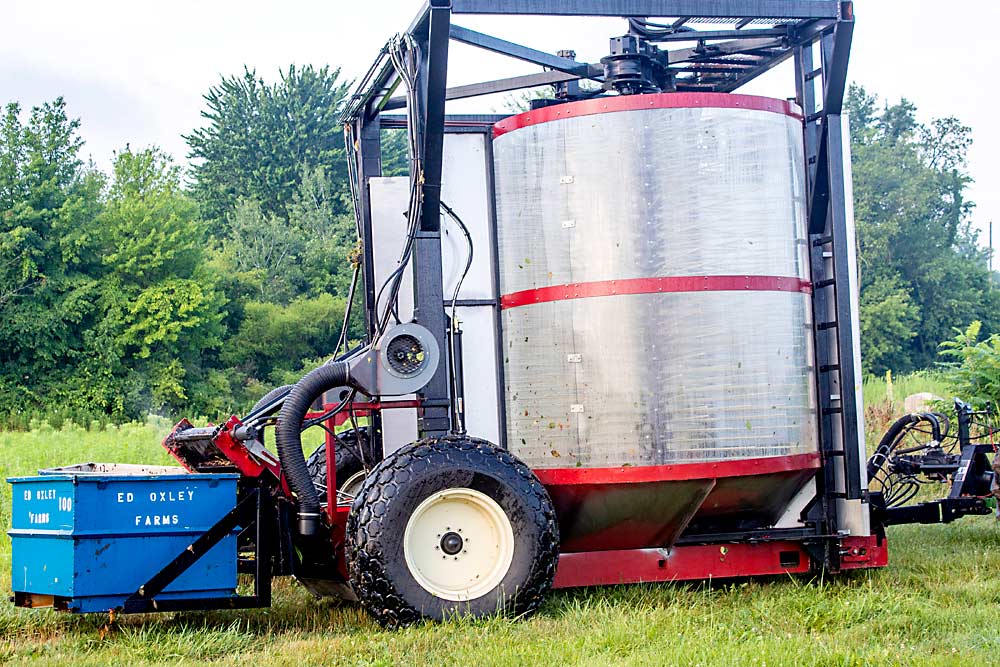
Going their own way
Most growers in Michigan, the state that produces the bulk of the nation’s tart cherries, can’t afford to radically alter their harvest methods. But at least two are moving in that direction, though in fits and starts.
For Oxley Farms in Southwest Michigan, the path toward high-density harvest started more as an accident, said Chris Oxley, a member of the family that runs the farm.
It began with a hailstorm. In 2010, hail destroyed a 50-acre block of 1-year-old tart cherry trees. The block was the industry standard: the Montmorency variety on Mahaleb rootstock, planted 19 feet by 21 feet and destined for harvest by mechanical shaker.
With advice from Perry, the Oxleys decided to cut the damaged trees off just above the graft union, to see what would grow back. They also decided to plant two new trees between each surviving tree, with the goal of keeping each tree small enough for some form of high-density harvest.
“It started as the world’s largest test plot,” Oxley said. “As the trees grew, we had to figure out a way to harvest them.”
They started by buying an Oxbo over-the-row blueberry harvester. The harvester worked well as long as the trees stayed small, but at a certain point they realized Montmorency/Mahaleb trees needed to be larger in order to reach adequate yields. That meant they needed a larger harvester.
After a deal with a manufacturer to build a specialized harvester fell through, the Oxleys decided to build one themselves. They’ve been building their own equipment, mostly for harvesting juice grapes, since the 1960s, he said.
The Oxleys modeled their tart cherry harvester, built in their farm shop during the winter of 2018–19, on an over-the-row blueberry machine. As the harvester — pulled by a tractor and powered by its power take-off — encompasses a cherry tree, its thousands of rotary tines shake fruit off individual limbs.
The cherries drop onto two conveyors that carry them rearward to two water-filled bins (to keep the cherries cool), one on each side of the machine. When a bin is full of cherries, the harvester automatically drops it on the ground. A forklift, following behind, places another bin on the harvester — all in continuous motion. The Oxleys designed the machine themselves, borrowing elements from blueberry, grape, raspberry and coffee harvesters.
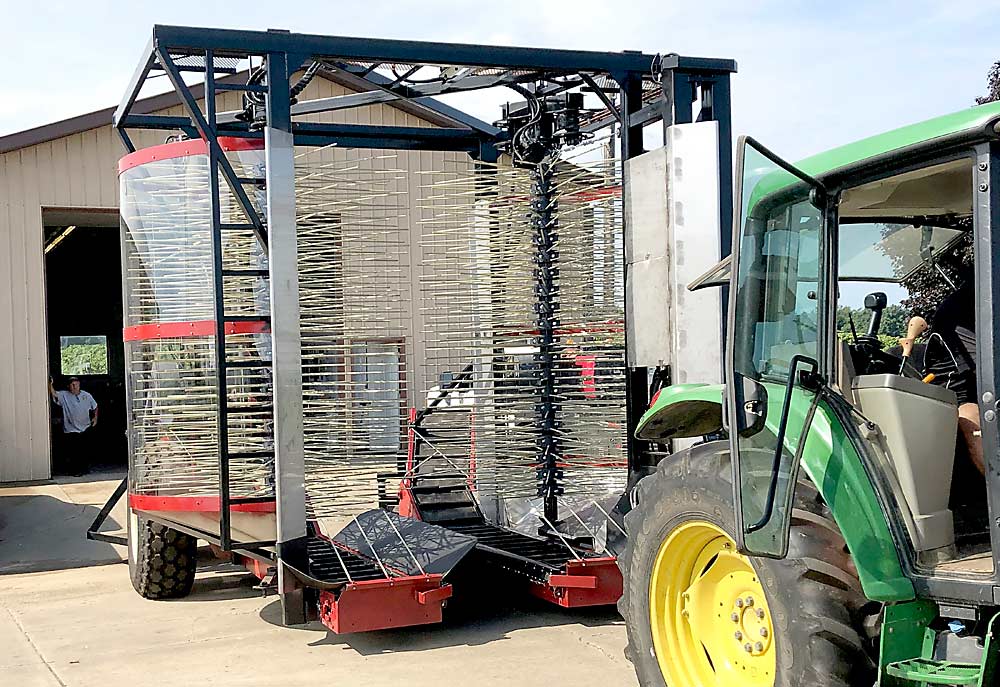
They first used the machine to harvest cherries last summer, and it performed “flawlessly,” Oxley said. It’s gentler on the trees than a standard trunk shaker, and it’s about three times faster because it doesn’t have to stop at every tree. The fruit quality was excellent, he said.
Building such a machine isn’t cheap, however, and would only make sense for larger growers who plan to stick with tart cherries long-term. If another farm wanted a harvester, the Oxleys would consider building one, but they don’t plan on becoming manufacturers.
“We’re farmers at heart,” Oxley said.
The Oxleys do plan to continue on the high-density path, though it won’t be straightforward. Access to dwarfing rootstocks is limited, and they’re having a hard time keeping the Mahaleb trees dwarfed properly. They planted an additional 75 acres of Montmorency/Mahaleb last year, on 9-feet by 20-feet spacing. They plan to harvest those trees for three or four years with the over-the-row machine, then remove every other tree and harvest the remainder with standard trunk shakers. That will help them generate revenue off the field earlier, instead of waiting seven or eight years for the trees to be big enough for shakers, Oxley said.
Smaller trees, bigger harvesters
A few years ago, the Oxleys sold their old Oxbo blueberry machine to the Lutz family, who grow cherries in Northwest Michigan. The Lutzes modified the harvester, making it wider and taller, so it could encompass tart cherry trees, and replacing its lower conveyors with full-size cherry conveyors, said Calvin Lutz III.
The Oxbo machine harvests about 40 acres of high-density tart cherry trees grown between Lutz, his father and brother. The high-density blocks are Montmorency on Mahaleb, planted between 2012 and 2015 on 15-feet by 5.5-feet spacing.
The Lutzes’ goal with the over-the-row harvester, same as the Oxleys, was to get into production earlier. The machine allows for a smooth and continuous harvest, compared to mechanical shakers, and fruit quality is comparable, Lutz said.
Challenges abound, however. Due in part to the financial state of the tart cherry industry, Lutz is selling his farm, though he plans to continue to farm with his father and brother. And, he does not think the Montmorency/Mahaleb combination works well enough for commercial high-density production. Keeping the trees dwarfed requires a lot of hedging and pruning, but if they’re too small, yields are inadequate.
The Lutzes will continue to experiment with over-the-row harvest. In 2017, they planted a small block of Montmorency on Gisela rootstocks, which are typically used for sweet cherries, and they’re studying different pruning strategies.
Lutz said that if the right variety and rootstock combination is found and growers ever get good prices for their fruit again, high-density cherries have tremendous potential. •
—by Matt Milkovich
Related:
—The art of tart
—Watch: Over-the-row cherry harvesting
—Small trees, big cherries?
Leave A Comment