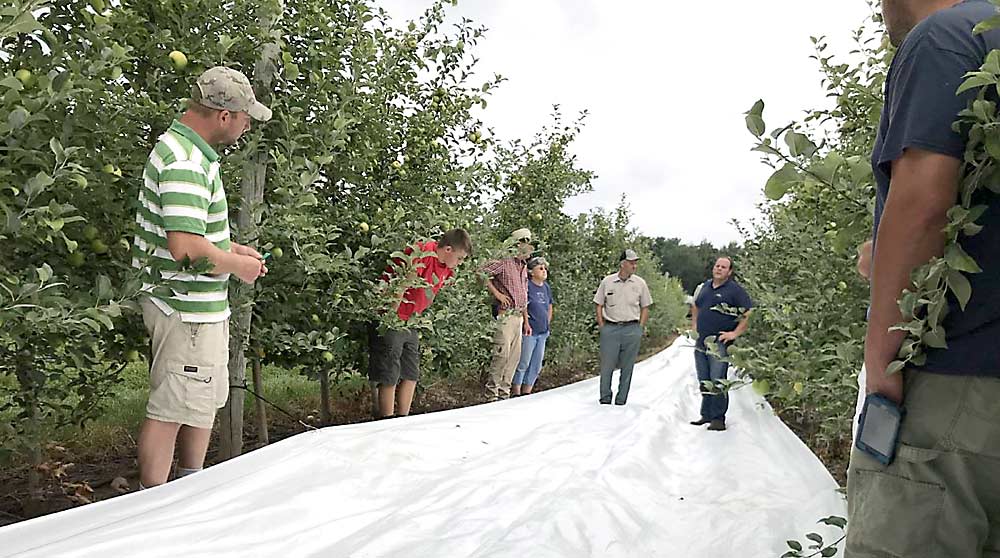
The use of reflective fabric is long overdue in the Northeast, according to researchers with Cornell Cooperative Extension. They discovered the benefits almost by accident, in a study of hail netting’s impact on fruit maturity and color.
“We’ve just begun to use fabric because we started testing nets,” said Mario Miranda Sazo, an extension specialist with Cornell University’s Lake Ontario Fruit Program. “We should have been testing fabrics by themselves years before. They improve color significantly and make a huge difference in the amount of money growers can make.”
Reflective groundcover, which includes fabric products, improves red coloring by reflecting sunlight onto apples hanging from trees. The practice is more common in the Pacific Northwest and New Zealand, but growers in New York state are starting to adopt it.
Growers often use leaf pruning and plant growth regulators to color their fruit, but both methods consume money and time. Use of fabric will get you more color and a greater amount of fruit for the first and possibly second pick, especially with high-value cultivars, Miranda Sazo said.
The Lake Ontario Fruit Program conducted field trials of reflective fabric at two farms in Wayne County, New York, in 2018. Miranda Sazo studied its effects on Minneiska at Cherry Lawn Farms, while program leader Craig Kahlke and business management specialist Mark Wiltberger studied the fabric’s effects on Fuji and Honeycrisp at Donald DeMarree Fruit Farm. Both trials used white reflective fabric from Extenday. Another company, Proline Products in New Zealand, offers a similar product, but the Cornell team studied Extenday because that’s what the growers were already using.
White film and metallic film (Mylar) are other groundcover options. But Mylar, while it can color apples, has its limitations. It can be used only for a year, wind can tear it apart, and it kills the grass underneath it, Kahlke said.
The reflective fabric trials actually started as a study of hail netting. (See related story: Net works for New York Growers.) The researchers added reflective fabrics to the study because of concerns that the hail netting might have negative effects on fruit coloring. The extension team almost immediately saw the benefits of reflective fabric, but the pros and cons of hail netting require more study, Miranda Sazo said.
When Wiltberger compiled the results of the 2018 trials, he found that about 95 percent of the apples colored by reflective fabric were classified as Extra Fancy grade (the most profitable grade), compared to between 49 percent and 74 percent of the naturally colored apples.
Assuming an initial investment of $2,000, the study estimated Extenday’s annual costs (including labor) at $508 per acre over the lifetime of the fabric, which is seven years. But even a 5 percent increase in Extra Fancy grade apples can increase revenue by $500 per acre, nearly making up the annual cost. And, depending on the block, increases ranged from 10 percent to 40 percent at the two farms, Wiltberger said.
Trial details
Most growers place strips of reflective fabic between rows. In the 2018 trial, Miranda Sazo decided to also cut strips in half and lay each half in the herbicide strips on each side of the row. He wanted to find out if he could use less material more strategically.
In 2018, a poor fruit-coloring season in the Lake Ontario fruit region, only reflective fabric placed between rows showed better results than the control trees. In 2019, however, which had almost ideal weather conditions for fruit coloring, results from both the between-row and in-row methods improved coloring. This showed that fabrics can boost red color even under New York’s most ideal natural coloring conditions, Miranda Sazo said.
Donald DeMarree Fruit Farm bought enough Extenday to cover 5 acres in 2018 and to cover an additional 20 acres in 2019. They move the fabric around at least three times per harvest season, which effectively covered more than 75 acres in 2019. The fabric has definitely improved their fruit color, said Alison DeMarree, who owns the farm with her husband, Tom.
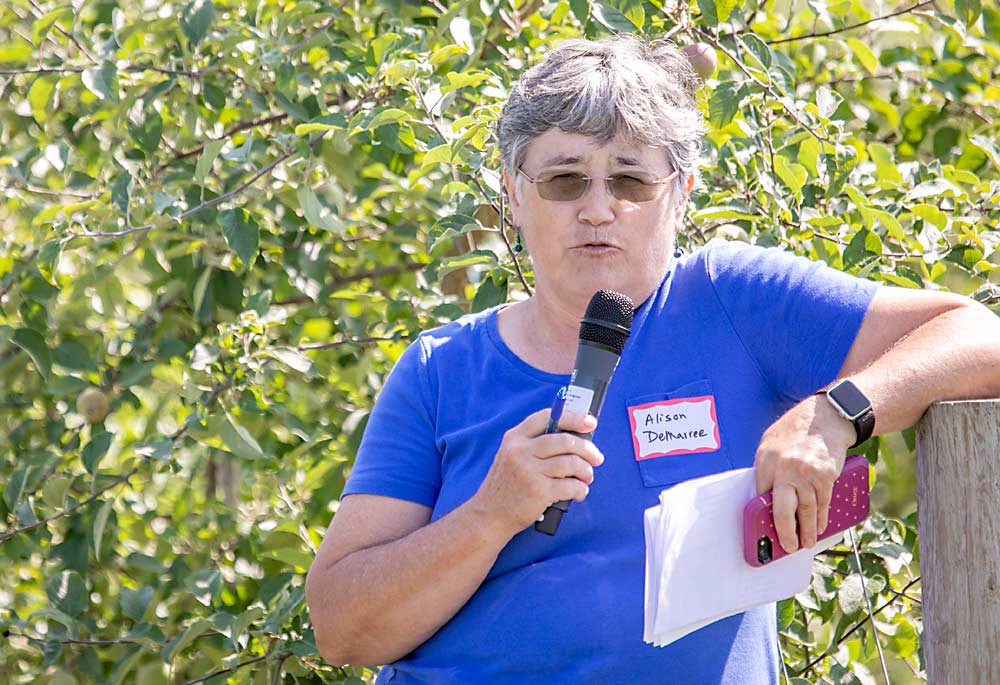
The DeMarrees decided to try reflective fabric on their farm after seeing how well it worked during an International Fruit Tree Association tour of New Zealand in 2018.
“We figured if it works in New Zealand, it should work here, where we have less sunlight,” she said.
That first year, they noticed improved color all season — on varieties picked in late August to varieties picked in early November. The difference was “pretty dramatic,” DeMarree said, and the apples were noticeably redder, despite 2018 being a poor coloring year.
The Cornell team couldn’t get funding for a 2019 trial at the DeMarree farm, so the DeMarrees conducted their own on-farm trial that year.
“Everyone knew we were using reflective fabric, because our fruit was so much redder,” DeMarree said. “It made a huge difference in bicolor varieties, especially late in the season when our day lengths start getting pretty short.”
She said the packers they deal with are now asking other growers to use reflective fabrics.
The DeMarrees lay the fabric between rows two or three weeks before a variety is ready to be harvested, then a couple of days before that harvest they move it to the next variety. There’s a cost to all that moving, however. The fabric has to be unfastened and rolled up, moved, then rolled out and fastened in another row. All that work requires extra labor.
“We had to bring more people in,” she said. “We haven’t calculated the cost, but our labor bill is definitely up.”
They also built a barn to store the fabric over winter — an additional cost to consider for Eastern growers.
“In New Zealand, they leave it out at the end of the orchard, but if we did that it would be full of mice chewing holes in it,” she said.
Growers have to be well organized to deploy reflective fabric the same way from year to year, with a special crew of workers who know how to move the fabric multiple times per season, Miranda Sazo said. •
—by Matt Milkovich
Leave A Comment