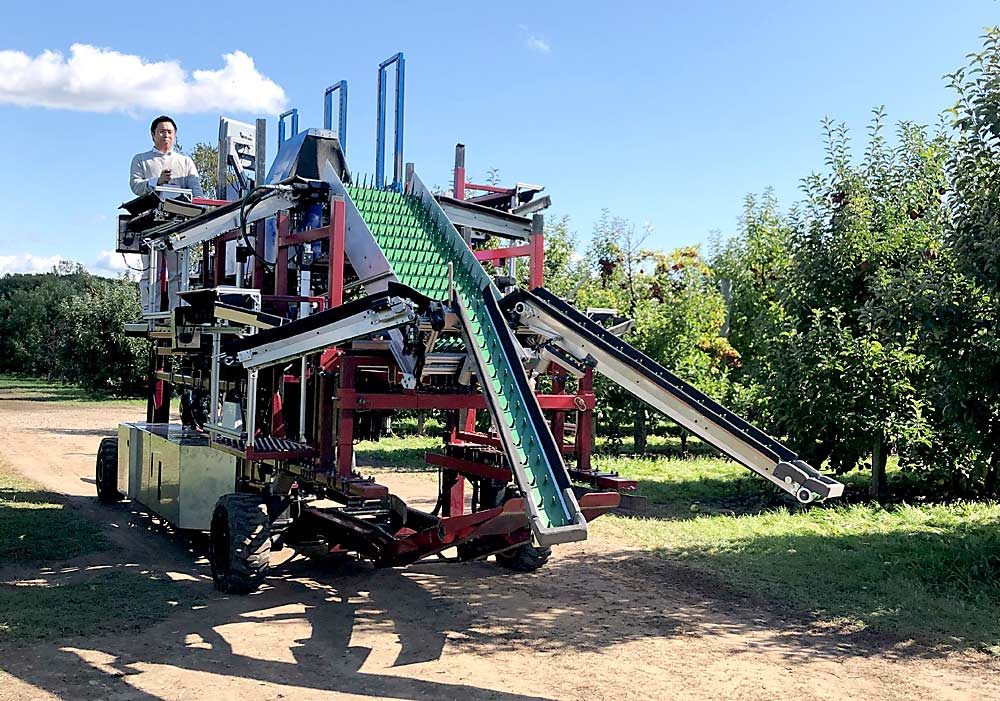
In early October, Renfu Lu conducted a demonstration of an experimental harvester that sorts apples by size and color as they are picked.
The test at Schwallier’s Country Basket, an apple orchard in Sparta, Michigan, displayed the latest iteration of the machine designed by Lu — an agricultural engineer with the U.S. Department of Agriculture — and his research team at Michigan State University.
Orchard owner Phil Schwallier, who’s seen his share of harvest machines, noticed a few unique features on Lu’s model during the demonstration. One was the camera on top of the machine, which evaluates apples before they’re dropped into one of two bins.
“It’s a sorting mechanism I don’t believe any other machine has,” Schwallier said. “It allows you to do in-field sorting.”
Sorting the fresh apples from the culls in the field rather than on the packing line saves growers money, he said.
Schwallier also noticed that the pickers on the machine dropped the apples into a trough, as opposed to a tube or a bucket, from which the fruit was conveyed up to be sorted. The apples then dropped a few feet into bins waiting below — but not before being caught by soft sponge rollers, which spaced the apples to avoid having them knock against each other. Empty boxes were fed from the front of the machine and when full were deposited out the back, Schwallier said.
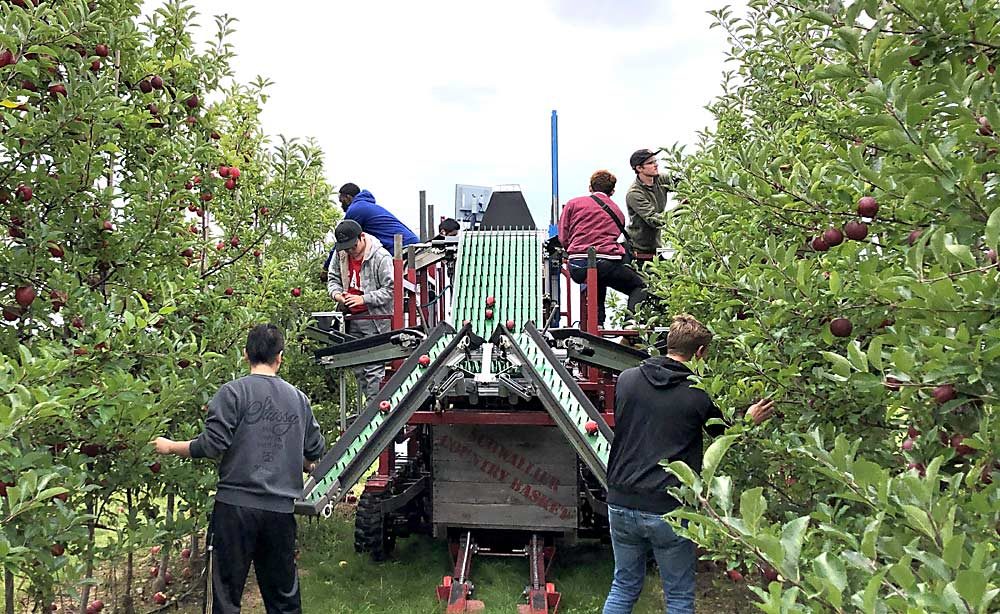
The latest test represented years of innovation. The first prototype of Lu’s machine was built in 2016 — a collaboration with Precise Manufacturing, a Michigan company, with financial support from USDA and the Michigan Apple Committee. Precise Manufacturing built the main body of the machine (chassis, steering and hydraulic systems) based on a design provided by Lu and his team of students and research assistants. Lu’s team designed and built the computer-vision-based sorting system (which is patented) and the automated bin-filling and handling systems, Lu said.
After field testing in 2017, the team made major improvements to the sorting, bin-filling and handling systems. The improved sorting system is simpler and more compact and can sort fruit into two grades, fresh-market or cull, at a speed of up to 12 fruit per second. The redesigned bin fillers handle fruit more gently, thanks to improved automatic controls. The redesigned, automatic bin-handling system reduces downtime, improves harvest efficiency and is safer and more reliable, Lu said.
The team also added adjustable harvest platforms and a new fruit-receiving conveyor. Pickers on the platforms can place apples onto the conveyor with minimum body and hand movements. The new design improves worker productivity and ergonomics, compared to the swivel conveyors commonly used in European platforms, while getting rid of the picking buckets still common with U.S. platforms, Lu said.
“Our sorter can meet more than the picking speed for a harvest crew of six people,” he said.
But perhaps the machine’s most important benefit is the ability to sort apples in the field. Harvest and postharvest handling account for about half of a grower’s total production costs, and the rising cost and declining availability of labor has steadily eroded the U.S. apple industry’s profitability and competitiveness, he said.
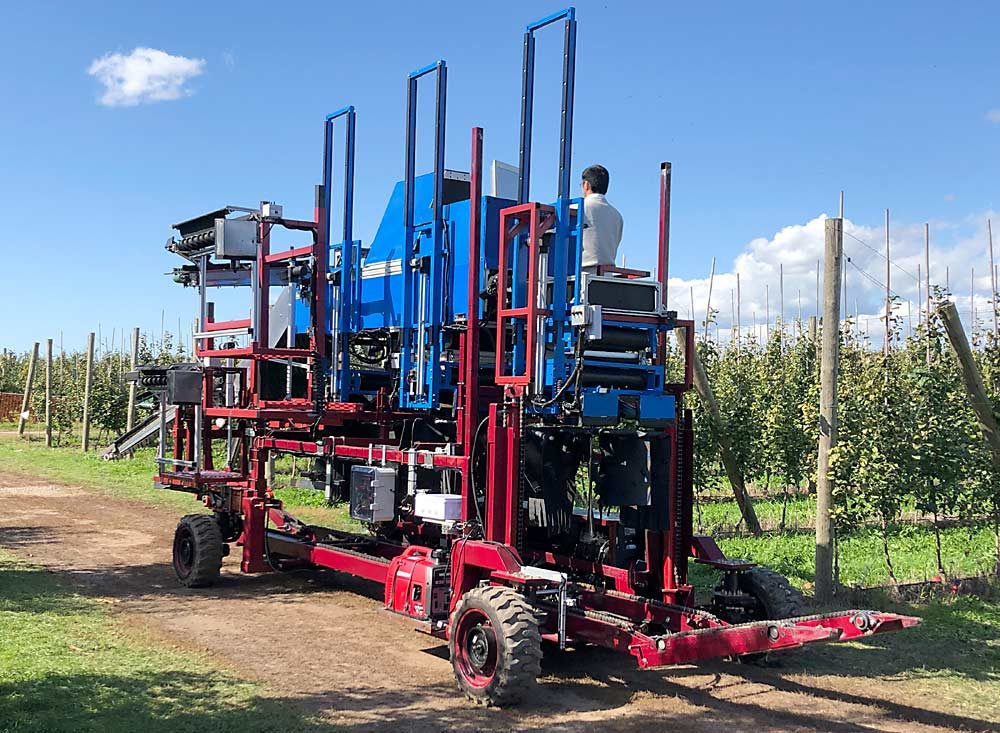
Harvest platforms have been gaining in popularity, thanks to the growing adoption of high-density orchards, but though they improve harvest productivity and worker ergonomics, platforms haven’t reached their full potential in terms of automation. That’s where Lu’s machine comes in.
Integrating in-field sorting with harvest-assist functions not only improves harvest productivity and worker ergonomics, it reduces storage and packing costs, reduces postharvest losses to pests and diseases, and improves inventory management and packout rate. Lu estimated that in-field sorting could improve an operation’s harvest productivity by more than 50 percent.
Lu said the machine is still in an experimental phase but has many innovative features that can be incorporated by horticultural equipment manufacturers into new or existing apple harvest and field-sorting systems.
Schwallier said it will probably be a few years before the machine is commercially available. •
—by Matt Milkovich
Leave A Comment