—story by Matt Milkovich
—photo by TJ Mullinax
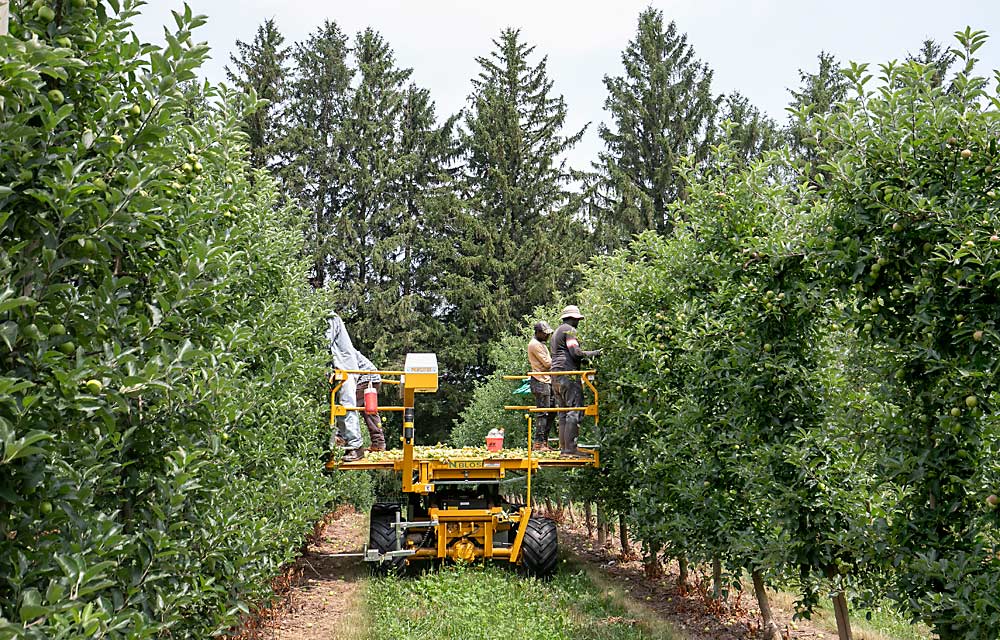
New York growers are wedged between the state’s rising wage rates and a lower threshold for overtime exemptions, which went into effect this year. They’re seeking escape through mechanization and other efficiencies, but it’s getting harder for them to plan for the future.
“Unless the price of apples goes up, I’m not sure what we can do,” said apple grower Shane Nesbitt. “It will get to the point where it won’t pencil out.”
New York’s current overtime threshold for farm laborers is 56 hours per week, which will gradually lower to 40 hours per week by 2032. The state’s minimum wage, meanwhile, is up to $16 per hour in New York City and surrounding areas, and $15 per hour in the rest of the state. New York’s Adverse Effect Wage Rate — the base wage H-2A employers must pay — is now $17.80.
Cornell University agricultural workforce specialist Richard Stup said that as the state’s overtime threshold continues to lower, farm employers will increasingly cap employee hours. And more of them will have to rely on H-2A workers to compensate for the dwindling pool of local and migrant labor. They’re relying more on mechanization, too.
New York is offering farm employers a refundable tax credit for the overtime hours they pay. The tax credit was first offered this year, so no growers have applied for it yet, Stup said.
For the Nesbitt family, with 700 acres of apples growing on the southern shore of Lake Ontario, the current overtime rate of 56 hours per week is more or less manageable. But as the rate gradually creeps downward to 40, it will force some tough choices.
“We’re at a crossroads,” Nesbitt said.
Either they hire more H-2A workers and add more housing to ensure everybody stays under 40 hours, or they cut back on apple volume. Then again, a lot of H-2A workers won’t want to come to New York if they’re limited to 40 hours a week, he said.
In the short term, they’ve cut the number of H-2A workers they hire in spring, from 30 to 20. Hiring fewer workers keeps labor costs down, but it also means some blocks aren’t pruned or thinned on time. They still hired about 100 H-2A workers for the last harvest, Nesbitt said.
The Nesbitts are finding efficiencies where they can: mechanizing hedging, pruning and other tasks. They combined mowing and weed spray passes. They hold more worker trainings to speed up the learning process. They also diversified into growing grain, corn and soybeans, he said.
Whenever Nesbitt talks to other growers, the same subject comes up: It’s hard to plan for the future. Input costs have gone up by nearly a third since the coronavirus pandemic, and the price of apples hasn’t come close to keeping pace.
Farther east in Williamson, the DeMarree family also is adjusting. Kristen DeMarree said they analyze the cost of every labor task and profitability of every block more closely than ever, seeking efficiencies wherever they can find them.
New technology helps: Croptracker software tracks production information; Phytech software tracks irrigation; Orchard Robotics technology aids crop load management; Agri-Trak software tracks worker hours, Kristen said.
They lengthened worker lunch breaks from 30 to 45 minutes. They wrote an employee handbook with more detailed job descriptions and more emphasis on planning and training. And they hired more office help to make sure they adhere to all the new state and federal regulations, Kristen’s mother, Alison, said.
The DeMarrees currently hire 39 H-2A workers each year. By the time New York’s overtime threshold reaches 40 hours a week, they calculate they would have to hire an additional 13 H-2A workers to make sure they can accomplish everything while keeping everybody under 40 hours, Kristen said.
They rely more on platforms, too. The DeMarrees spent the past 15 years replanting their 200 apple acres with high-density blocks more suited to platform work. Four years ago, they had two platforms. This year, they’ll have six. Using a platform, six people can do the job of eight or nine people on ladders. At this point, only about a quarter of their workers use ladders during harvest, Kristen said.
Another way to be more efficient is to remove unprofitable blocks. This also could help solve the oversupply problem, Alison said.
“It’s cheaper to have bare land than orchards that are costing you money,” she said. “All U.S. apple growers should realize that fact.” •
Leave A Comment