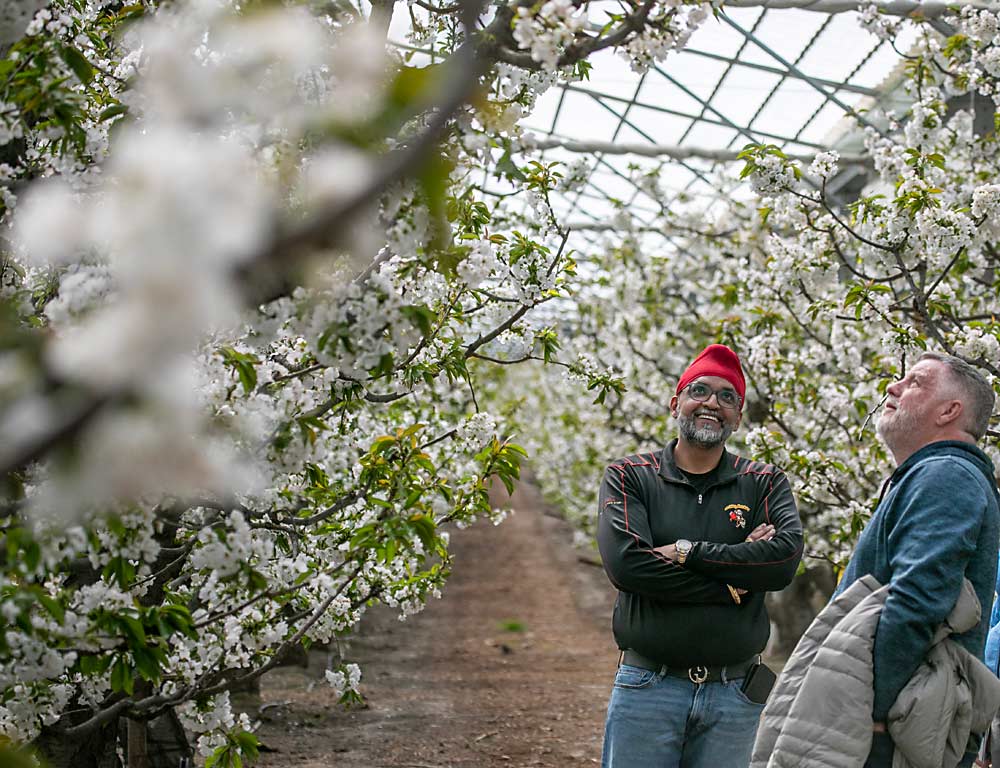
In early April, most of the cherry trees at Cherry Ridge Farms were reaching green tip, but inside its 2.5-acre greenhouse, full bloom was already starting to fade.
The greenhouse puts the Rainier trees about “18 to 21 days ahead of the bloom outside,” said grower Todd Wilmoth, and 10 to 14 days ahead of anything he can grow at his farm in Kennewick, Washington, one of the Northwest’s earliest growing regions.
That three-week head start for Rainiers earns serious money in the Asian market, said Kam Chauhan of FreshPack Export Sales, which markets under the Smiling Monkey brand.
“Rainier is the diamond of the diamond,” he said. “The greenhouse idea is to have the quality from Washington but as early as California.”
Cherry Ridge is far from the first farm to experiment with greenhouse fruit production, but it’s more common in regions where the climate limits production. In prime cherry regions, a new generation of climate control technology offers growers the opportunity to reduce risk and chase new marketing windows — for a price.
Cherry Ridge opted for an automated retractable-roof system, which offers protection and climate control when needed but can also be opened to the natural climate when conducive.
Wilmoth said he likes the system but added that it’s expensive and has a steep learning curve. He lost his crop in 2019 after installing the greenhouse over an existing block of mature trees in 2018.
“It really makes you appreciate Mother Nature, too,” he said.
The greenhouse drives vigorous growth and advances bloom, but Wilmoth said he’s careful not to let the indoor trees get too far ahead or they can become vulnerable to frost events. On a cold night, the greenhouse can only heat to about 15 degrees above the ambient temperature.
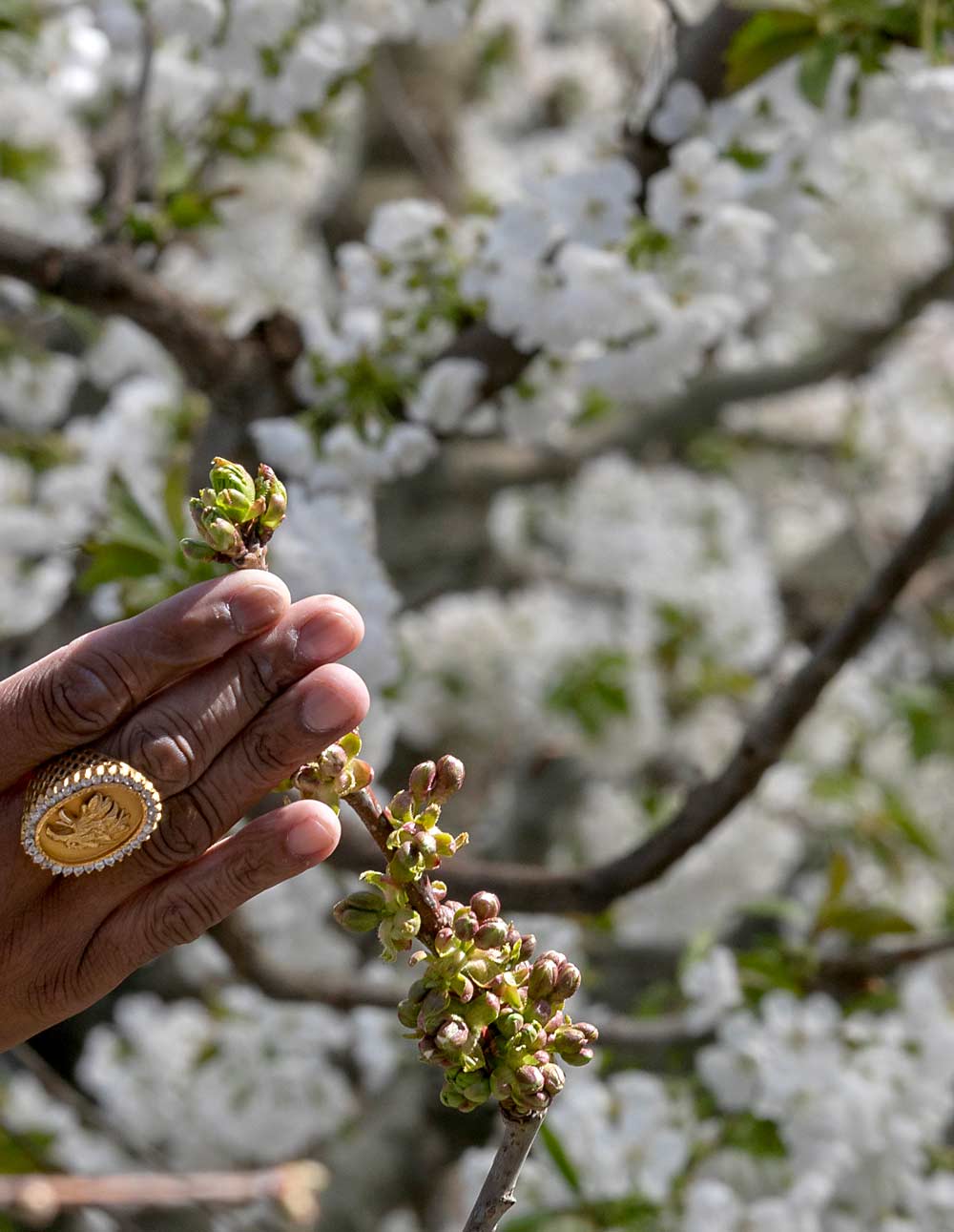
Wilmoth and partner Dewight Hall purchased the retractable-roof greenhouse system from Ontario-based Cravo Equipment Ltd. The roof continually adjusts, in response to climate sensors, to regulate the internal temperature. It also protects the easily bruised Rainiers from wind. The orchard gets a head start when enclosed in spring, but the roof stays open when the growing season has progressed to the point when conditions are perfect for cherries.
Later, as fruit ripens, a layer of bird net is rolled out below the retracted roof, to protect fruit.
The system, which Chauhan estimated at about $250,000 per acre, is very similar to the smaller system Cravo donated to Michigan State University a decade ago for research. Lead researcher Greg Lang compared production in the retractable-roof system to rain cover and high tunnel systems over several years and reported that the system supported high fruit quality, better pollination, reduced disease pressure and could help growers manage weather risks.
But few commercial producers in the U.S. have tried it.
Chauhan said that’s because of the time it takes to learn to use the technology.
“It’s a lot of hard work. I love technology, don’t get me wrong, but you need the people,” he said.

Reid Fruits, a major cherry producer in Tasmania, Australia, also invested in a Cravo retractable-roof system over 12 acres of newly planted Kordia and Regina in 2016. Production manager Andrew Hall said the farm sits at a higher elevation and faces more frost risk, so the retractable roof acts as an insurance policy.
“A guaranteed crop under our covers provides some certainty of covering production costs in the event of crop failure outside,” Hall said in an email.
Unlike Cherry Ridge, Reid Fruits does not want to advance harvest. “We chose this location as it extends our season by 14 days and, therefore, we can still be marketing fruit when others do not have it, including Chinese New Year, when it falls late,” Hall said.
But the automated, retractable-roof greenhouse offers climate optimization to meet that goal, too. For example, they slow bud burst by shading in the morning in early spring. And, during bloom, reducing stress from wind, rain and suboptimal temperatures on the trees — and the bees — has significantly boosted yields, Hall said.
The most outstanding pro has been the yield and quality difference with these hard-to-set varieties under the covers, as compared to a conventional netted orchard, he said. For example, Kordia on Colt rootstock produced 15 metric tons per hectare in the fourth leaf (6.7 tons per acre) while the same-aged trees outside cropped about 7 metric tons (3 tons per acre). “This is a pattern that has repeated, and this sort of quick return on investment is critical to justify any covering system,” he said.
University of Tasmania horticulture professor Dugald Close called the system at Reid Fruits, where he has run trials, “the Rolls-Royce” of cherry covering systems. (See “Protecting the investment in covered sweet cherries.”)
The hefty investment might not pay off for easier-to-set varieties and friendlier climates that just need protection from rain or hail, Hall said.
At Cherry Ridge in Kennewick, the rest of the Rainier block features rain and hail protective netting that can be pulled out along permanent wires to protect the high-value crop.
Chauhan hopes to see Washington growers expand the use of the retractable-roof technology, and he’s working with a few others who are planning such investments, he said. But growers are also on the lookout for alternatives that might reduce the price tag, he added.
In addition to growing great early cherries, the greenhouse serves as a great marketing tool, he said. “Buyers love to come and visit.”
—by Kate Prengaman
Considering the investment?
Reid Fruits production manager Andrew Hall offers a few pieces of advice for growers to consider if they are weighing an investment in climate control:
—What is the planting system, and are you retrofitting or covering a new orchard? The structure may determine the plant spacings and growing system choice. It also may lend itself to be part of the trellis system and could influence the orientation of rows and design of the structure itself.
—Consider site engineering limitations. Some structures may not work well on slopes or undulations. What sort of equipment will you need to spray or mow, for example?
—How will you manage stormwater? Most conventional systems vent rainwater to the inter-row, but under cover, this can increase humidity, soften fruit and cause splitting if rows are not sufficiently drained.
—How will you manage birds under a cover? Will a net rest over or be incorporated into the structure?
—Automated systems require a backup power supply in the event of outage.
—Have an in-house expert — someone on your team who takes ownership and completely understands the build and the operation.
—K. Prengaman
Leave A Comment