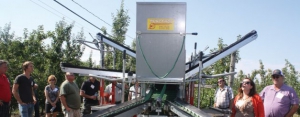
David Guerdin has several years of experience with his Munckhof apple harvester (left) and now owns two.
Apple growers in Canada’s Quebec Province aren’t having the labor problems U.S. growers have. They have access to Hispanic workers from Central America through a federal program, much like the U.S. H-2A guest-worker program, and it apparently functions more effectively.
Quebec growers aren’t complaining about labor quantity or quality, but they are interested in mechanization. They would like to adopt worker-assist machines, like platforms and harvesters, that would reduce their need for imported labor and allow them to rely more heavily on local labor. Orchard operations in Quebec tend to be less than 100 acres in size, and many have local employees who find full-time work there.
Growers are not only showing interest in machines, they are buying them. During the International Fruit Tree Association summer tour to the Monteregie region of Quebec, between Montreal and the province’s border with New York and Vermont, several growers showed off machines they had purchased.
Some showed how they were designing their orchards to adapt to the machines, but others plan to utilize machinery without going to high-density plantings on trellis systems.
Hilliness doesn’t appear to be an issue. Located in the St. Lawrence River Valley, Monteregie is flat as a pancake except for the remains of some ancient volcanic hills that rise more than a thousand feet, sprouting out of nowhere. Some orchardists plant the lower slopes and get great air drainage, but when they do, trees usually run up and down long gentle slopes where machines can travel easily.
Harvester
That was the case at David Guerdin’s orchard, huddled at the base of Mont Yamaska, which rises out of flatness to 1,348 feet. There, Guerdin grows about 50 acres of high-density, fertigated apple trees, and fruit are sold through the farm’s market. The orchard contains 15 varieties of apples and 15 acres of grapes. The market makes and sells cider and wine, along with apples and other products.
The orchard purchased a mobile picking/packing machine, manufactured by Munckhof Manufacturing of Horst, the Netherlands, and called the Pluk-O-Trak in Europe. David said he paid for the $65,000 machine in three years and then bought a second one. A third one is being purchased now.
The machine paid for itself not only by boosting picker efficiency, he said, but by reducing bruising 15 percent and eliminating the need for sorting in the packing shed. The machine has a system for lowering fruit into the bin without bruising it—moving it by soft rubber fingers onto a soft, rotating brush. Another feature that helps the payoff is that the conveyors and bin filler can be removed, the bin filler replaced with an air compressor, and the machine used as a platform to prune or to hand thin.
The machine looks similar to vacuum machines being developed by DBR and Picker Technologies, except that instead of vacuum tubes, it has conveyors with soft fingers and belts of rubber. Apples are picked by hand and laid into six conveyors, two serving workers walking and picking low fruit, and four on platforms picking high fruit. The conveyors can be moved, but are not as flexible as vacuum tubes.
David said the machine works best on 3 by 14-foot plantings, and his are very close to that, at 3 by 15 feet. Workers pick on rows on both sides of the machines. The eight-person crew includes two who sort the fruit, putting discards into a tray that can be dumped periodically into a bin. Four others ride and pick into conveyors, while two walk and pick into conveyors.
A bin hauler is towed behind the self-propelled machine. It takes 8 to 10 minutes to fill a bin, and 35 to 40 seconds to change bins, Guerdin said.
Darwin thinner
The Darwin string thinner is taking off in California and in the Mid-Atlantic states as a blossom thinner for peaches. But in one Quebec orchard, it is being used for the purpose for which it was originally designed, as an apple blossom thinner. It was intended for use in organic apple orchards, where good chemical thinners are lacking.
Conventional wisdom in the United States says that it won’t work without doing massive damage, since apples have both leaves and blossoms at bloom-time, and damaged leaves are magnets for fireblight. But in Quebec, Danny Boileau says the Darwin does not damage his trees when he uses it at 20 percent bloom. Fireblight is a threat in Quebec. The leaves are very small then, he says.
This was his second year using the Darwin. “I’m really happy with the results,” he said.
He runs the thinner at 5 to 10 miles per hour, with the spindle rotating at 180 to 200 revolutions per minute. He counts the blossoms on the tree first, then runs the machine and counts the blossoms again. Usually, he takes off half the blossoms, or a little more.
Tree planter
The Boileau family’s DM Boileau Orchards, which has about 100 acres of land near Havelock, is better known as a packer of apples, but Danny wants to revitalize and further develop the orchard side of the business, planting about 25,000 new trees over the next five years.
It’s a struggle, because the land is so incredibly stony. He spreads lots of manure on the land to prepare it, tills it in, then uses a rock picker to remove stones just before planting. He’s pleased with his heavy-duty Phil Brown Welding tree planter, which works right through the stony soil, he said.
Boileau has also built his own hedger. He wants to use it during the winter to shape the trees, forming them into a tree wall against which the Darwin thinner works well, he said.
Platforms also work well, and he uses them extensively to prune and thin. At his farm during the tour, workers were on his Munckhof machine that had been stripped of its harvesting conveyors and was being used by workers to thin apples.
Platform
Tim Petch has about 75 acres of apple orchards near Hemmingford. At his orchard, IFTA tourists saw an inexpensive platform that is self-propelled and sits on a Kubota tractor. It was built by Dan LaGasse, who owns LaGasse Works in Lyons, New York, where he builds specialized orchard machines.
The simple platform machine, 7 feet wide by 9 feet long, sits over a Kubota L3830 tractor, which is steered by a linkage between the platform and the steering wheel. The platform folds away so the tractor engine compartment can be opened for servicing. The machine costs about $12,000, not including the tractor.
Wind machines
Speakers claimed Quebec is the world’s coldest area for growing apples. No doubt, cold hardiness is an issue in choosing varieties, but the area has done well growing McIntosh and its relatives, like Spartan, and spring freezes are no greater an issue there than in many other places.
Quebec has a normal crop this year, while nearby Ontario, New York, New England, and North Carolina lost more of their apples to spring freezes that followed warm conditions in March.
Still, Quebec growers are interested in wind machines, which seemed to protect some fruit in the areas of New York, Ontario, and Michigan where they were used.
At Ciderie du Minot, visitors looked at a wind machine built by engineer Hubert Philion, who owns and operates Philion Orchards.
While some wind machines operate as a fan on a tower designed to reach up and pull down warmer air, Philion’s machine works the opposite way. It grabs cold air from the orchard and shoots it upward. In theory, warmer air is displaced from above and falls into the orchard to replace the cold air. There are commercially available machines of similar design—one from Shur Farms called the Cold Air Drain.
Philion said the one he built requires low horsepower, about 15, and runs off a tractor power take-off. It cost less than $10,000, he said. The price and power requirements are similar to commercial machines.
The idea is to remove cold air from the orchard by pulling it in from the lowest spot and shooting it up 3,000 feet into the sky at 100,000 cubic feet per minute.
Growers asked whether barriers may be needed to prevent cold air in areas near the machine from sliding in to replace the air shot upward. Philion said he was testing the machine.
Leave A Comment