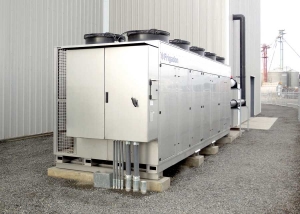
A Frigadon Hycool chiller unit at Valicoff Fruit Company in Yakima, Washington. (Rick Larsen/Good Fruit Grower)
A growing number of controlled-atmosphere storage operators are installing secondary chillers and moving away from storage cooling systems based on direct expansion ammonia or hydrocarbon refrigerants.
A few secondary chilling systems have been installed in apple storages in the Pacific Northwest, and several have been put in across the Northeast. There are more than 25 systems installed in the produce industry in the United States.
These systems are said to be safer to operate, easier to defrost, less complicated and less expensive to maintain, and they keep fruit in better condition with less shrinkage. One big advantage is getting rid of ammonia inside storages, where leaks can damage fruit and endanger the lives of workers. Ammonia is both explosive and toxic.
The system that is being installed is the Frigadon Hycool Secondary Refrigeration System. Manufactured in Sweden, it is owned by SRS Frigadon, located in Stratford on Avon in the United Kingdom.
The sole importer to the United States is the Alternative Energy Group (AEG). Distributors are Versatile Refrigeration in Washington and British Columbia, VanErnst Refrigeration in New York, and Storage Control Systems, Inc., in Michigan.
Jim Schaefer, an owner of AEG and president of Storage Control Systems, Sparta, Michigan, and Eric MacGregor, general manager of Versatile Refrigeration in Wapato, Washington, described the features of the systems they are installing for growers and packers.
The key is in the coolant and the way it is handled. In the Frigadon system, the heat-transfer solution is based on potassium formate, a non-toxic, biodegradable organic salt that can be moved at relatively low pressure, about 40 psi, through ABS (plastic) piping. In conventional systems, ammonia or Freon is used, at higher pressures, and moves through steel or copper piping.
“The primary refrigerant is confined to the chiller, utilizing a very small charge of refrigerant,” Schaefer said. “The secondary fluid is chilled and pumped through the storage at a much lower pressure.”
Similar technology is used to freeze ice in skating rinks and heat floors with under-floor heating systems.
The chiller is a self-contained unit that sits outside the storage and contains all the pumps, compressors, and controls. The unit is connected to a power supply and a pair of flow and return pipes that carry coolant into and out of the storage.
The amount of ammonia or Freon that would typically be used in a conventional system is reduced from 3,000 pounds to about 30 pounds per compressor unit, or 120 pounds in total for a storage holding 200,000 bushels of apples.
Auvil Fruit
Versatile Refrigeration installed two Frigadon chillers at Auvil Fruit Company in Orondo, Washington, two years ago. Last year, they installed a system in a new six-room CA storage at Valicoff Fruit Company in Wapato, Washington.
The cooling at Auvil is provided by twin 260-kilowatt Frigadon chillers, which cool the rooms using Hycool, which circulates between the chillers and cooling coils in the rooms.
Walt Hough, Auvil’s plant operations manager, said secondary refrigeration is not new, but there was some sacrifice in efficiency in the older systems. However, new technology is available to help make it work better, and the new system allows for some significant improvements in how the fruit is handled. He can run the coil temperatures at above dew point, so that water does not condense out of the fruit, cutting weight loss by about half.
Although the system is a little more expensive up front, Hough said that’s more than compensated for with the added value of the fruit and better fruit quality, and he’s planning to install another system this year.
Valicoff Fruit
Brett Valicoff, son of Robert and nephew of Ric, who own Valicoff Fruit, said an advantage of the system is in defrosting. It requires no water, so there’s no water tank to keep free of algae and scale or dispose of periodically.
Ammonia systems need to defrost once or twice a day, MacGregor said. The Frigadon system requires defrosting once every two weeks after initial pulldown.
Valicoff said the Frigadon unit operates on five 50-horsepower compressors compared to one in ammonia systems. “If one goes out, we can shut down a circuit and run the others,” he said. It’s easier with five motors to match chiller capacity to cooling demand, which he thinks will translate into lower energy bills.
The fact that there are no compressors inside the storages means more space for fruit, he said.
In the eastern United States, many systems have been installed including Crist Brothers Orchards in Walden, New York; Dressel Farms in New Paltz, New York; Gunnison Orchards in Crown Point, New York; Blue Hills Orchards in Wallingford, Connecticut; Ridgetop Orchards in Fishertown, Pennsylvania; Russell Farms in Burt, New York; and Lake Breeze Fruit Farms in Sodus, New York.
Among the 40 rooms under construction this year using the new chillers are Rice Fruit Company in Gardners, Pennsylvania, and H.H. Dobbins of Lyndonville, New York.
In British Columbia, chillers have been installed at Cawston Cold Storage in Cawston and B.C. Tree Fruits in Kelowna. •
Leave A Comment