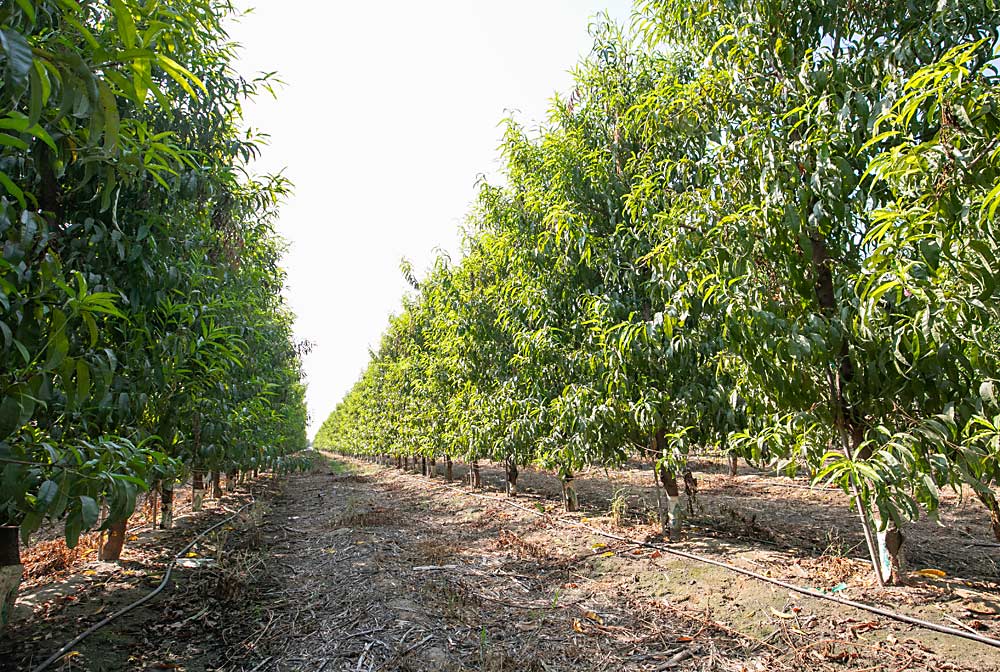
Robots can pick peaches too, thanks to Central California stone fruit growers’ march toward the two-dimensional growing systems that make automation and mechanization possible.
HMC Farms of Kingsburg has gone all in.
The vertically integrated producer has planted no freestanding trees since 2018. Everything new is on a planar trellis at high-density spacing.
“We’re finding it to be successful, and still believe it’s the future and what we need to be doing,” said Drew Ketelsen, production manager for HMC, which grows peaches, plums and nectarines, as well as table grapes.
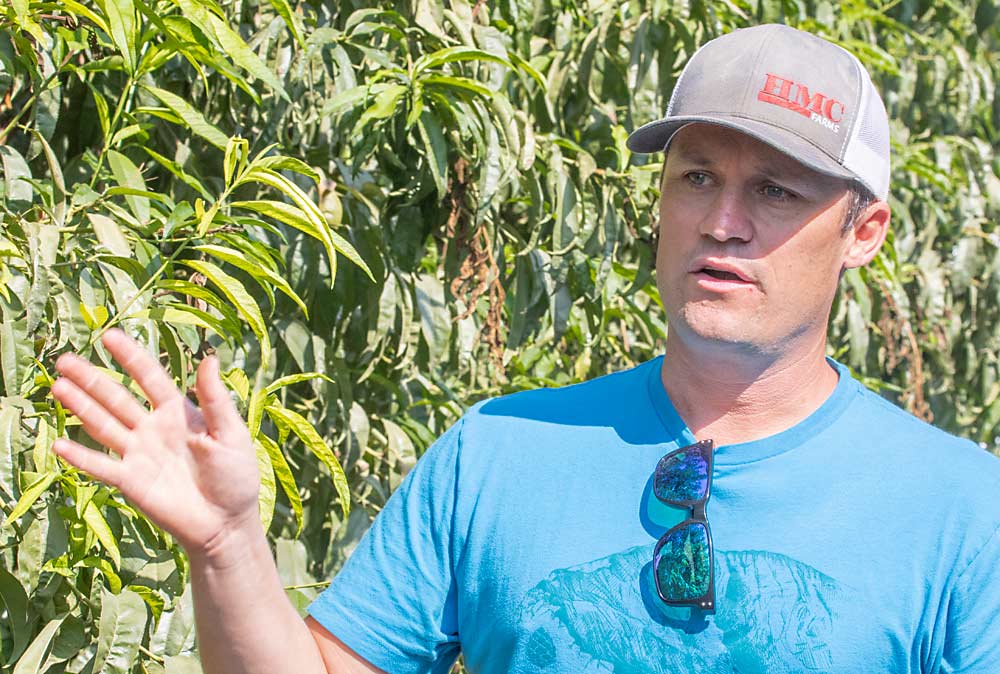
For the past two years, the farm hosted trials for two robotic fruit harvest startups: Israel’s Tevel and the Bay Area’s advanced.farm. When Good Fruit Grower visited in September, the crop had been harvested and the robots were gone; the orchard systems that enabled robotic harvest remained. (See “Automation advancements in apple harvesting.” )
But the top driver for the trellised systems is labor efficiency, he said.
Workers move faster and more safely and comfortably up and down planar rows than among the freestanding trees of yesteryear. The new systems allow for standardizing spacing, training and pruning, simplifying instructions for crew members.
Mechanization and automation are bonuses, Ketelsen said. “We’ve got the structure set up to gain all those efficiencies, and then the whole technology side of things is kind of just the byproduct.”
HMC uses worker platforms, hedgers and mechanical thinners.
To thin, HMC uses the Eclairvale, a French-made mechanical thinner with a system of bristles that knock away blossoms and small fruit. Unlike the Darwin mechanical blossom thinner, the tractor-towed Eclairvale is not powered but spins from the drag of the brushes against the trees.
HMC mechanically tops trees with rotary blades. Most preharvest color pruning is done by hand, but the farm has experimented with some sickle bar side hedging.
Combining high-density horticultural practices with new varieties creates challenges, said Jon McClarty, president of HMC Farms. HMC grows more than 100 different stone fruit varieties, some of them proprietary, and they all develop unique quirks when training into planar systems.
“Not all varieties react the same way going from old to new,” McClarty said.
McClarty and his sister, Chelsea Ketelsen — Drew’s wife, are part of the fifth-generation owners and operators of the family farm.
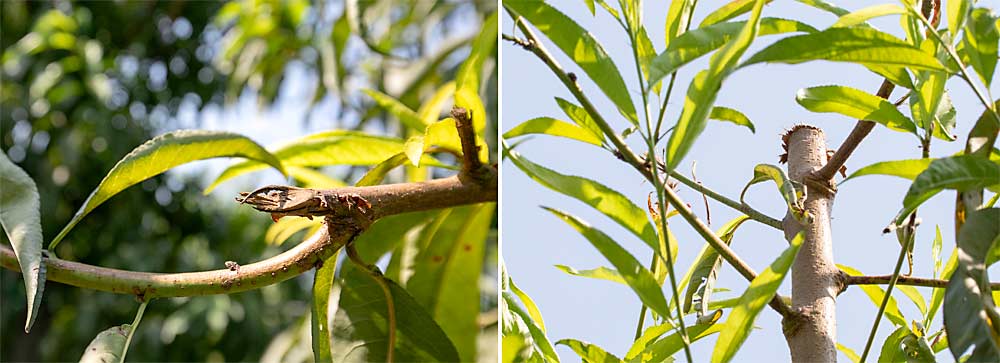
Peach design
To achieve those efficiencies, HMC has aggressively adapted its orchard design. They replant about 10 to 15 percent each year. Everything is on drip irrigation.
The planar systems allow trees to crop earlier. Their peaches, for example, reach a partial crop in the second year and nearly a full commercial crop by the third year.
Peaches and nectarines are usually spaced at 5 feet by 13 feet, trained to vertical trellises on Nemaguard, a nondwarfing rootstock resistant to nematodes. Ketelsen is not satisfied with the industry’s dwarfing options so far.
Each tree stands between 10.5 and 12 feet tall, with a single leader and 45 or so “hangers,” or fruiting branches. Crews color pick between three and five times each season, down from four to six on the old freestanding trees.
Plums
Plums are trickier, Ketelsen said. Training is more labor intensive, horticultural traits vary more by variety, and pollination struggles cause more inconsistent crop loads. On the other hand, plums have a more forgiving harvest window.
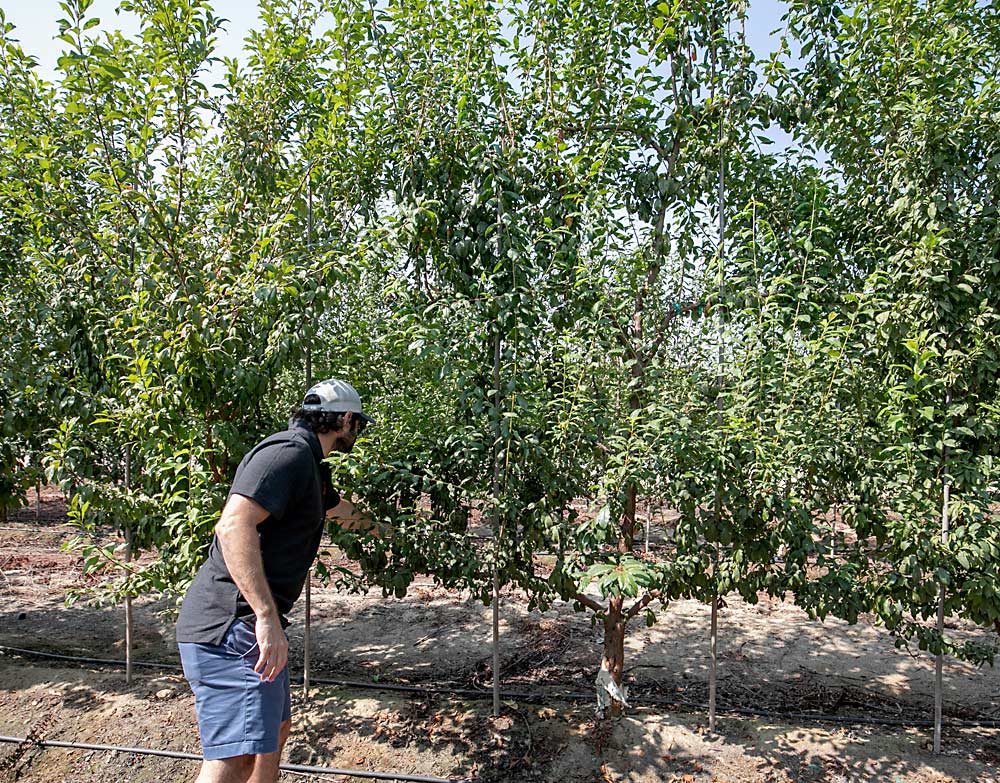
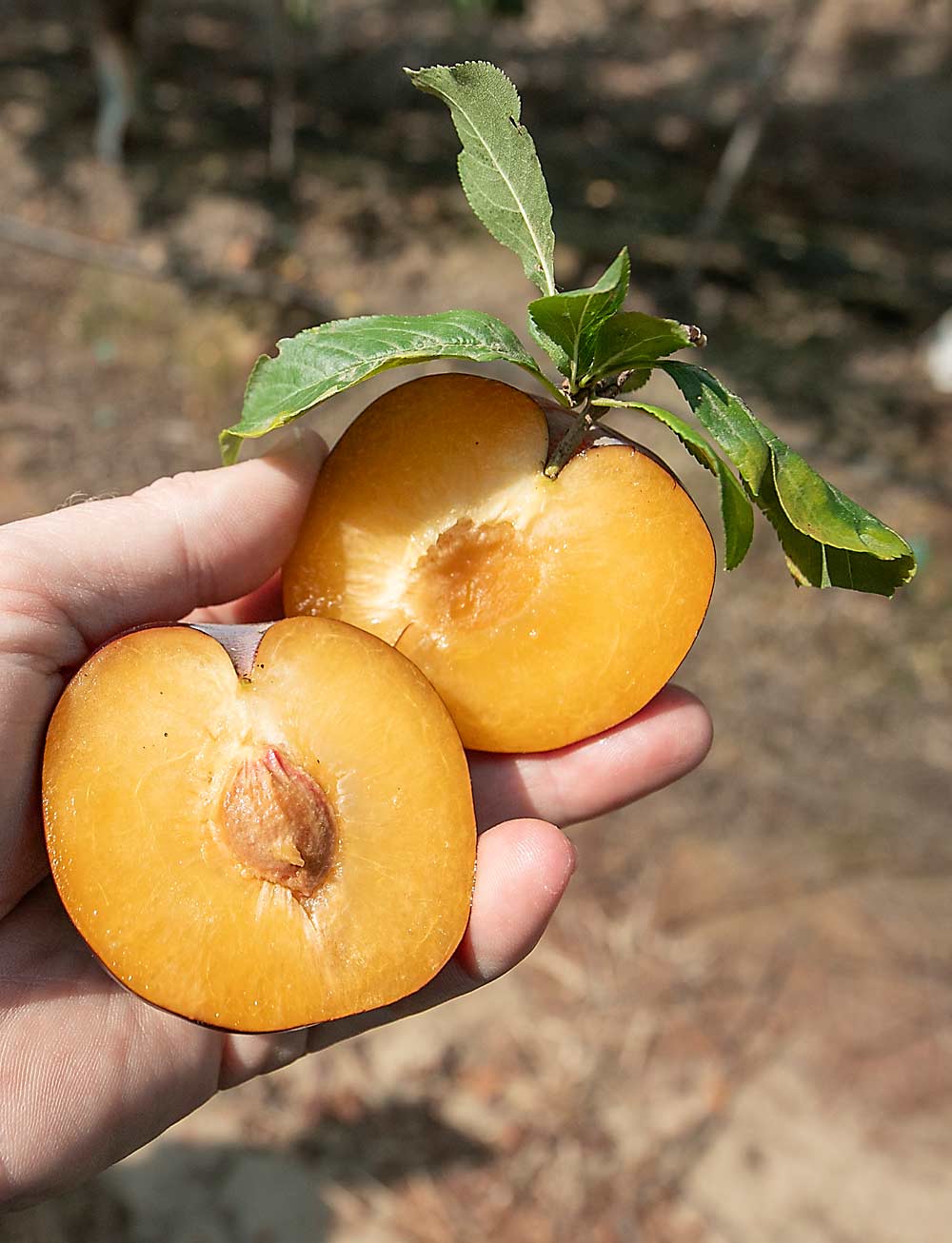
“We have a few ways of doing plums and haven’t settled on the perfect system for each variety yet,” he said.
Normally, they train plums into two vertical leaders with horizontal hangers. Spacing is 6 feet and rootstocks are normally Citation, an industry standard, or Viking, for heavy soils. HMC also uses Nemaguard for plums sometimes.
In winter, crews renewal prune up to 30 percent of bearing wood each year, Ketelsen said. Plums prefer to grow on 2-year-old or older wood, sturdier and more lignified than the first-year branches that peaches prefer. They also color prune by hand in the summer.
Black Magic, one of the farm’s proprietary plum varieties, struggles to set fruit. So, HMC trained leaders along four horizontal wires on each side. Fruiting wood grows up. It’s too soon to tell if it worked, Ketelsen said.
The high-density decisions go beyond one year, Ketelsen said. Labor was relatively easy to find in 2023, but it will get tight again. If they don’t plan ahead, they’ll be too late. Few peach growers in the Central Valley use H-2A workers, he said.
“It takes years to get to this point,” he said.
—by Ross Courtney
Leave A Comment