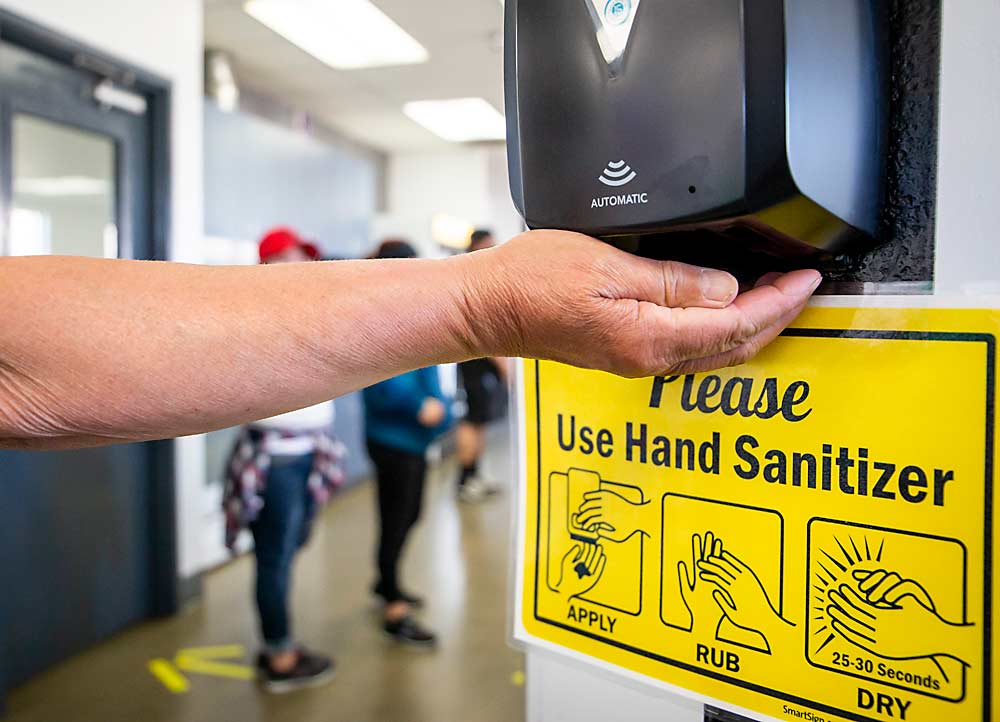
The sweeping global crisis exacted by the coronavirus has yet to show signs of ebbing and, approaching a year in, the financial toll on the fruit industry can be calculated in myriad ways: packing facility modifications, reduced worker hours, unfilled isolation housing and market losses.
The U.S. Department of Agriculture puts the impact on U.S. apple growers alone at $174 million in lost sales, and another $6 million for pear growers, but experts agree that cramming all of the costs of the pandemic into a single dollar figure is impossible. Anecdotally, it was bad in some places, though not always as bad as feared. For others, it was more of a logistical challenge than a financial one.
Those challenges in no way lessen the health and economic suffering experienced across the globe in 2020. As of mid-December, the coronavirus had killed more than 1.6 million people worldwide — nearly 20 percent of them in the United States — with agricultural workers among them.
Fruit producers, part of an industry deemed “essential” by the federal government, had to make safety and health changes, even if they were expensive.
However, those financial costs still matter to an industry working hard to produce food and protect workers, said Mark Powers, president of the Northwest Horticultural Council of Yakima, Washington. Tree fruit groups need accurate figures to lobby for aid, push for policies and answer questions from the public.
“Having confidence in what you are saying is really important when you are speaking for the industry,” Powers said.
Teasing the coronavirus away from other economic factors is difficult, Powers said. Every year has challenges, and 2020 was beset by frosts, wildfires, smoke, windstorms and early freezes in the Northwest. Meanwhile, the fruit industry still is adjusting to international trade changes over the past few years.
However, officials did come up with some hard figures based on surveys, including anonymous examples.
In the surveys, growers estimated increased production costs ranging from 2 percent to 10 percent due to the virus. Packers put the increase at between 2 percent and 6 percent. One packing company reported in the surveys spending $125,000 on coronavirus-related adjustments. Another dropped $13,700 on HVAC upgrades alone.
Not everyone took a hit.
“I personally just don’t know of any in the valley here that had to (spend) more than they were already doing,” said Lesa Bland, a Cashmere, Washington, bookkeeper for about 30 small family-owned orchards.
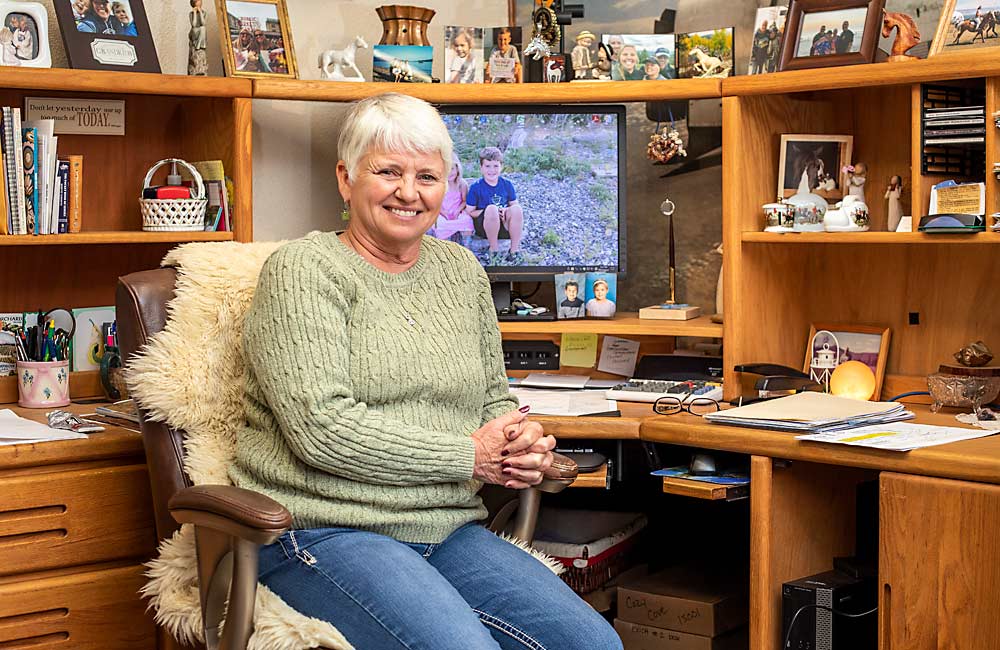
On the other hand, packers spent tens of thousands of dollars renovating lines to create barriers and allow social distance. Jordan Matson of Matson Fruit in Selah, Washington, eventually stopped counting because the expenses weren’t optional. “It doesn’t matter how much it’s going to cost us because it has to happen,” he said.
For growers, time is money
Time was one of the biggest complaints. Managers spent anywhere from 15 percent to 50 percent of their time on COVID-19 issues, according to the NHC surveys.
That’s what Bland, the Cashmere bookkeeper, noticed, too.
“The expense was management,” she said.
She spent a lot of time helping her clients apply for federal aid, while one grower said his wife worked on the farm more than ever just to make sure the company was following all the right protocols.
Aside from that, pandemic costs were often backfilled by the federal and state governments, Bland said. “The small farmer could not have done it without the governments’ help,” she said.
The few of her clients who hire H-2A workers did not report a spike in housing costs due to bunk bed limits, she said. The federal Coronavirus Food Assistance Program and government purchases helped offset the drop in revenue from schools, while the Paycheck Protection Program helped growers keep workers. In fact, Bland’s own family orchard used federal money to hire extra thinners, who happened to be out of work due to a smaller cherry crop and the coronavirus. “Because of that extra money there, we could say, ‘Yes, we are able to hire you.’”
Packers experienced sizable capital costs
In the spring, Matson Fruit publicly committed to $75,000 worth of workplace modifications in the packing house as the company navigated a walkout. That figure roughly covers physical improvements, such as plastic barriers and new concrete slabs for outdoor break rooms, Matson said, but leaves out the extra labor costs for employees to take temperatures, wipe down surfaces and monitor handwashing. Nor does it include the loss of production, as the company slowed the line to make more room for social distancing.
Consumer preferences changed more rapidly than the company could adjust for at times. Demand for bagged fruit shot up, causing logjams because packing companies usually have only about one-third of their lines set up for bagging, Matson said.
Getting bags, masks and other supplies at any price was difficult at times, said Brett Valicoff, president of Valicoff Fruit in Wapato, Washington. In August, a fungicide supplier called him and said a manufacturing plant had to shut down for two weeks due to a coronavirus outbreak, requiring him to negotiate for a substitute product.
Before the pandemic, Valicoff Fruit had been ordering bags from overseas, with a six-week lead time in normal economic conditions. With shipments disrupted, Valicoff shifted to Shields Bag and Printing of Yakima, at a higher cost, he said.
At times, masks and hand sanitizer distributed by the state through tree fruit organizations was the only available source of these critical supplies, with some on monthslong back order. “That was huge, just to be able to keep our essential workers going and working safely,” Valicoff said.
Processors got pros and cons
The processing side of the industry has experienced mixed reactions from the market and in their costs.
Tree Top Inc. of Selah has seen a modest boost in sales. There was an uptick in retail sales early, with consumers buying more products such as applesauce and juice to eat at home, but things eventually leveled out. There was a modest increase in donations to school districts as well, said Allison Arnett, director of corporate communications.
The pandemic has created extra labor and other operating costs for Tree Top, but those costs have been partially offset by a decrease in employee travel, Arnett said.
In its seven plants scattered across Washington, Oregon and California, Tree Top increased cleaning and sanitation of common areas and touchpoints and also retrofitted processing lines to increase social distancing. In areas where 6 feet of distance couldn’t be maintained, the company installed plexiglass separators, she said. Some of the changes will probably become permanent, such as the greater emphasis on teleconferencing, as well as the increased cleaning and sanitation, Arnett said.
Peterson Farms in Shelby, Michigan, supplies bulk frozen fruits and other fruit products to food service institutions and grocery stores across the U.S. and Canada, said Grant Boring, communications manager.
The company’s food service sales have been down during the pandemic, with much of the reduction coming from school districts teaching virtually during the crisis. Even though many districts now offer grab-and-go meals, demand dropped with students not in buildings. Hospital sales held steady. However, grocery store shoppers have been buying more shelf-stable products such as applesauce and juice.
The purchase of personal protective equipment for employees has been one of the company’s main pandemic-related costs, Boring said.
Peterson Farms had food safety management practices in place before the pandemic, including handwashing, hairnets and other hygienic requirements. It has added practices such as social distancing, masks, and staggered shifts and breaks, said Amy Baker, director of quality and regulatory compliance management.
“From a regulatory compliance standpoint, it was a shift in our program, but not a huge shift,” she said.
Many of the new practices will probably stay in place because they’ve worked well, Baker said.
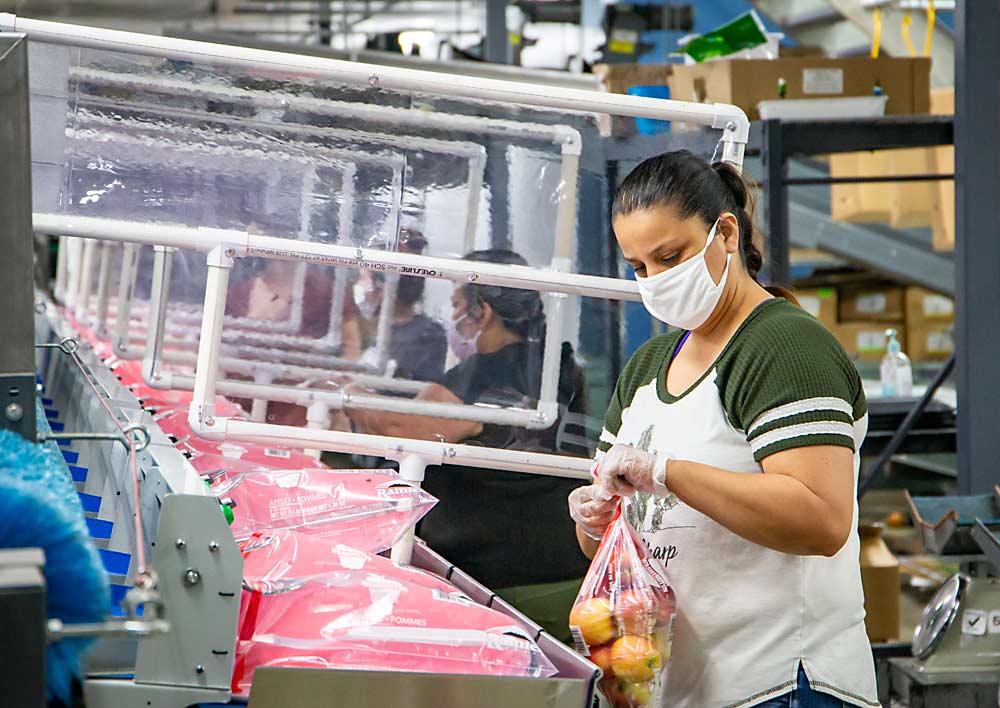
Farmworkers feel the pinch
Orchard workers felt the pandemic in their pocketbooks, struggling to make ends meet with fewer hours. To help, the UFW Foundation gave out $5 million in cash assistance cards to agricultural workers in Washington alone this year.
The foundation, the charity arm of the California-based United Farm Workers advocacy group, has been collecting testimony from workers as its staff and volunteers distributed meals, masks and $500 gift cards throughout the West Coast, said Zaira Sanchez, the Pacific Northwest emergency relief coordinator.
Workers reported lost income because of reduced hours when warehouses needed to cut back on capacity. Others said they had to take unpaid time off when companies closed due to an outbreak.
“It’s impacting farmworkers’ lives,” she said. “Mental health is being impacted. Family dynamics are being impacted.”
The UFW Foundation staff helped Good Fruit Grower interview a few Washington aid recipients — all orchard workers. They did not share their names or identify their employers, to avoid risking their positions.
All said they faced shortened hours, struggled to keep up with their utility or rent payments since the pandemic started and faced price hikes in child care, if they could find it at all. They have adjusted by shopping for cheaper food, stocking their cupboards with fewer snack items and scaling back on activities such as picnics, zoos and swimming, even when they could find such things open. For some, Thanksgiving and Christmas came and went with little fanfare or extra meal trappings.
In November, a 35-year-old mother of six from the Tri-Cities area missed some work and wages due to a routine cold. Meanwhile, her husband’s construction hours have been reduced. So, this year, she plans to continue orchard work through the winter. Normally, she stops working until spring to focus on home life.
The woman said many of her fellow workers, mostly mothers, had to stop work in September this year to help their children with online school, something her 17-year-old son now manages. Her supervisors have been gracious to her and her fellow workers, granting more days of leave than usual, without discipline, even if it was unpaid, she said.
Fortunately, she said, her family is used to living economically.
“I’m a really good saver, so we know what to do,” she said.
—by Ross Courtney and Matt Milkovich
Price of the pandemic
The Northwest Horticultural Council used surveys of growers and packers to tally the financial costs of the pandemic to the tree fruit industry in Washington, Oregon and Idaho.
The council enlisted the help of Washington State University agricultural economist Karina Gallardo to crunch the numbers and analyze the data.
Growers representing about 22 percent of the Northwest’s acres responded to the surveys, while packers representing 39 percent of apples by volume, 51 percent of pears and 30 percent of cherries responded. The answers were anonymous. The Horticultural Council planned to launch follow-up surveys in December 2020.
Here are a few of the findings:
—In September, just as pear harvest started to ramp up, apple and pear growers projected additional losses of $11 million to $23 million in work left undone or done too late, due either to sick workers or fewer workers because of temporary housing restrictions that prevented the use of bunk beds.
—In July, one packer estimated an average cost of $83 to equip one worker with personal protective equipment and sanitation supplies required during the pandemic. Another put the figure at $167 per employee.
—One grower reported roughly $2,000 per week to hire two extra cleaning employees, while most growers paid a few workers extra to enforce social distancing.
—Managers spent anywhere from 15 percent to 50 percent of their time on COVID-19 issues. One farm’s human resources manager spent about three-fourths of his or her time on the issue.
—One packing company spent an extra $204,000 on a $1-per-hour “appreciation pay” increase.
—Some growers and packers built barriers and used other methods to allow social distance. One reported about $125,000 on barriers, lunch space renovations, signs and tape.
—One grower estimated a cost of $15,000 for unused rooms, just to be ready for quarantined workers. Another put the additional housing costs at $100–$200 per acre.
—One packer that has its own clinic spent nearly $2,000 on testing and over $18,000 on COVID-related treatments, billed to insurance. Others estimated $25,000 to $30,000 in extra health care costs.
—R. Courtney
Pandemic disrupts Michigan tree fruit supply chains
The COVID-19 pandemic caused “dramatic shifts” for Michigan agriculture, initiating abrupt changes in consumption patterns that disrupted supply chains. According to a Sept. 24 report written by Michigan State University researchers, the pandemic decreased Michigan’s overall agricultural output by 18.6 percent, or more than $1 billion.
The report — written by Steven Miller, director of MSU’s Center for Economic Analysis, and assistant professors Trey Malone and K. Aleks Schaefer — studied the way supply chains were disrupted and estimated the economic impact compared to a normal year, Miller said.
The report estimates that the pandemic cost Michigan’s tree fruit industry $46 million, a decrease of 8.4 percent from a normal year. Some fruit and vegetable producers opted not to harvest at all, in order to avoid increased labor costs and limitations on labor supply.
The pandemic’s effects were different for each commodity and for each supply chain. U-pick growers saw a massive increase in demand, but that’s a relatively small fruit category. In grocery stores, the demand for fresh blueberries stayed fairly strong. The closures of restaurants and bars hit some commodities, such as tart cherries and hard cider, fairly hard, Malone said.
“Hard cider demand took a huge nosedive,” he said. “Twenty-packs of Busch Light were selling great, but six-packs of craft specialty items were not moving.”
Federal agricultural purchasing programs mitigated the damage somewhat, but it’s not yet clear how much, he said.
“It’s going to take a long time for us to understand how well those federal programs worked at mitigating demand disruptions,” Malone said. “My hypothesis is that those federal programs didn’t really get the job done for tree fruits.”
For David Smeltzer, an apple and cherry grower in Manistee County, the pandemic didn’t cause too much of a financial burden, but he was frustrated and disappointed by the way state rules were administered.
Last spring, at the beginning of the crisis, Michigan’s governor laid down new labor-camp rules in an attempt to separate farmworkers as much as possible. Luckily for Smeltzer, his camp was structured in a way that he didn’t have to change much. Unlike a bunkhouse where a bunch of workers sleep in close quarters, he has separate living units designed for individual families, which the state camp inspector deemed “isolation units” that didn’t need to be altered. He had to add extra portable toilets, but that was the only real pandemic-related expense.
“A lot of my neighbors had bunkhouses and had to do the isolation thing,” he said. “We were fortunate in that regard.”
In August, the Michigan Department of Health and Human Services issued an order requiring migrant housing camp operators to provide more stringent COVID-19 testing for their employees. The order was given in response to outbreaks at Michigan farms and food processing plants.
With backing from the Michigan Farm Bureau, Smeltzer, a blueberry grower, and six farmworkers filed a lawsuit arguing that the order singling out migrant farmworkers for testing infringed on their civil rights. The lawsuit was dismissed in September, but the situation left a bad taste in Smeltzer’s mouth. He felt migrant workers were being unfairly targeted by people with preconceived notions regarding migrant labor, who “feel that a labor camp can be the source of all kinds of nefarious things.”
“Why are we isolating and segregating Hispanic people?” he asked. “That really ruffles me.”
—M. Milkovich
Leave A Comment