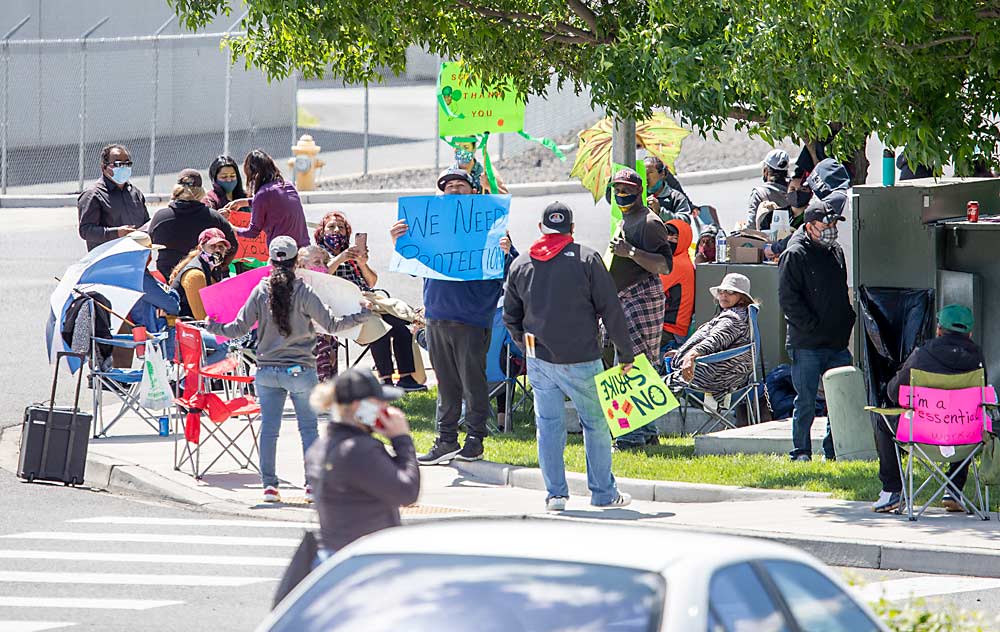
Despite coronavirus risk-reduction adjustments made among fruit packers, workers at seven facilities in the Yakima, Washington, area walked off the job in May demanding safety improvements, better communication and hazard pay.
Only two protests stretched into June, with workers at Columbia Reach Pack in Yakima and Matson Fruit in Selah reaching a resolution with their employers early in the month.
Wages were one of the main sticking points of the protests. Columbia Reach started a bonus pay program on June 14 that will continue through Dec. 31, though protesting workers wanted more. Matson Fruit planned to continue evaluating wages this month.
Though wages dominated the conversation, communication problems often lurked beneath conflicts, said Jon DeVaney, president of the Washington State Tree Fruit Association in Yakima.
Company officials said workers never voiced concerns before the walkouts, while the striking employees accused their companies of not meeting with them. Employers had trouble obtaining protective equipment; employees assumed their bosses didn’t try. Federal health privacy laws prohibit employers from naming workers who test positive for COVID-19; employees accused the supervisors of keeping such information a secret. Health authorities also were limited in how much they could share with employers.
DeVaney advised packers to exercise extreme and proactive transparency with staff, as much as is allowed, communicating in advance what they can and cannot discuss with workers. He also advised telling employees about the difficulties to procure masks and hand sanitizer, sometimes on back order for months with the increased demand throughout the world, he said.
Several packing houses in Washington, some with strikes, some without, granted bonuses or “appreciation” pay, DeVaney said. However, he advised companies to keep payment discussions clearly separate from safety considerations. “You can’t trade money for resolving safety issues,” he said.
At Matson Fruit, many employees thought they were fired after walking off the job, said Jordan Matson. That wasn’t true and several workers returned once they learned that, he said.
Matson and Columbia Reach, like other packers, made many of the safety improvements sought by the protesters as the pandemic unfolded, long before the walkouts. They installed barriers between work stations and added more hand sanitizing stations, and they began distributing as many masks as they could get and taking worker temperatures.
The strikes, calling attention to the health risks facing essential food and agriculture workers, began after two agricultural labor unions, the United Farm Workers of America and Familias Unidas por la Justicia, withdrew requests from a lawsuit they filed against the state of Washington seeking stricter rules governing agricultural worker safety practices under the pandemic. The unions supported the Yakima-area strikes.
At Columbia Reach, workers walked out on May 14. The company instituted most of its safety changes on April 6, said Kerri Lovelass, the packer’s human resources manager, after closing the plant for six days in the wake of positive tests.
Among the changes, Columbia Reach doubled the size of its sanitation crew, staggered shifts to allow more cleaning and suspended the attendance policy, giving employees the freedom to skip work with no questions asked. Normally, the company tracks unexcused absences and disciplines workers for having too many, Lovelass said.
The company also put up plastic barriers on two sides of each line worker: one between them and their face-to-face neighbor and one between them and the apples. Managers opted not to add a third barrier, between back-to-back employees, because they thought it would create an egress hazard in the event of an emergency, creating a bigger safety problem than it solved, Lovelass said. Also, Yakima Health District representatives told her back-to-back proximity was a low transmission risk, she said.
However, that third barrier was under consideration, she said.
The striking workers wanted that third barrier, or reduced employee density, said Rosalinda Gonzalez, a 19-year employee at Columbia Reach. If one worker sneezes or coughs, he or she will naturally turn away from the apples, potentially exposing the neighbor behind, she said.
The workers also wanted more communication about workers who had symptoms or tested positive, Gonzalez said. She doesn’t expect company officials to name them, just tell workers when they have been exposed.
“It is my right to know,” she said.
Stefanie Valazquez of Yakima, who has worked for the company for two years, said safety improvements were more important, but said workers needed extra pay because during the pandemic they were more likely to visit doctors or have spouses stay home with children. “We deserve it more than anyone else,” she said. •
—by Ross Courtney
Related:
—Tree fruit groups respond to walkouts with crisis management advice
—Pandemic packing pivot
Leave A Comment