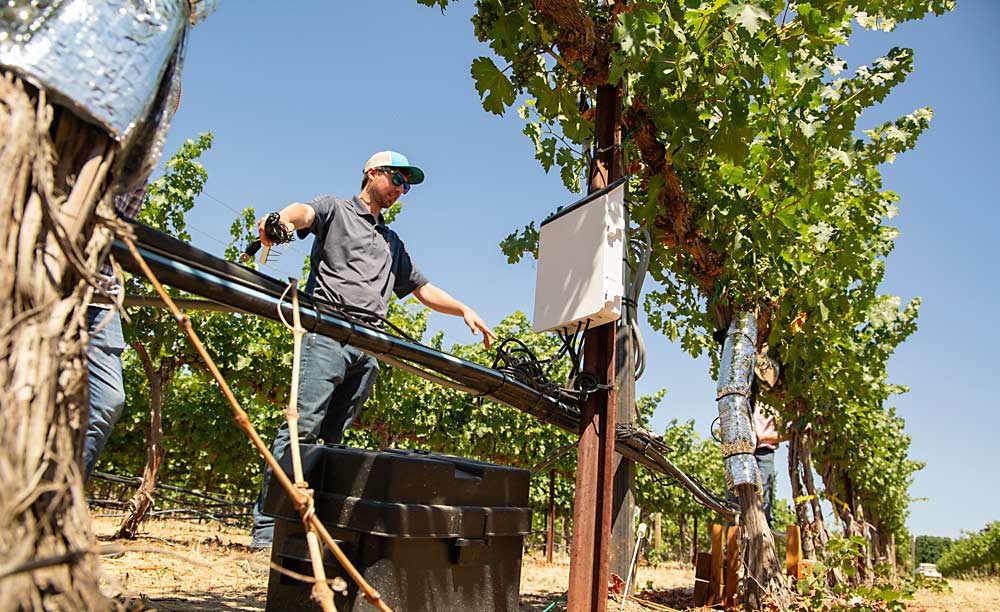
Automating vineyard irrigation requires a network of sensors, solar panels, wires and data loggers that can be at risk of run-ins with equipment.
That’s one of the first lessons the engineers learned at Washington State University’s Smart Vineyard demo farm in Prosser. Sprayers bumped sensors out of position. The prepruner sliced through wires. Solar panels had to be taken down before over-the-row harvesters could head into the block.
“There is a whole bunch of machinery that goes under the canopy, so you have to put up protection for your soil moisture wires,” said Jake Schrader, the technician for the demo farm and an agricultural engineering graduate student. “Another big frustration was that anything that was mounted over the canopy was susceptible to being knocked down.”
He shared this insight — and the advice to consider in advance the interaction of sensor placement with equipment operations — with growers who visited the Smart Vineyard field day in late July. The demo farm is funded by the AgAID Institute, a consortium of agriculture and technology researchers led by WSU, and the Washington State Wine Commission.
Schrader said the goal of the farm is to collect data for a team of artificial intelligence researchers who are working to develop better irrigation recommendation models. It also offers growers a chance to see the sensors in action.
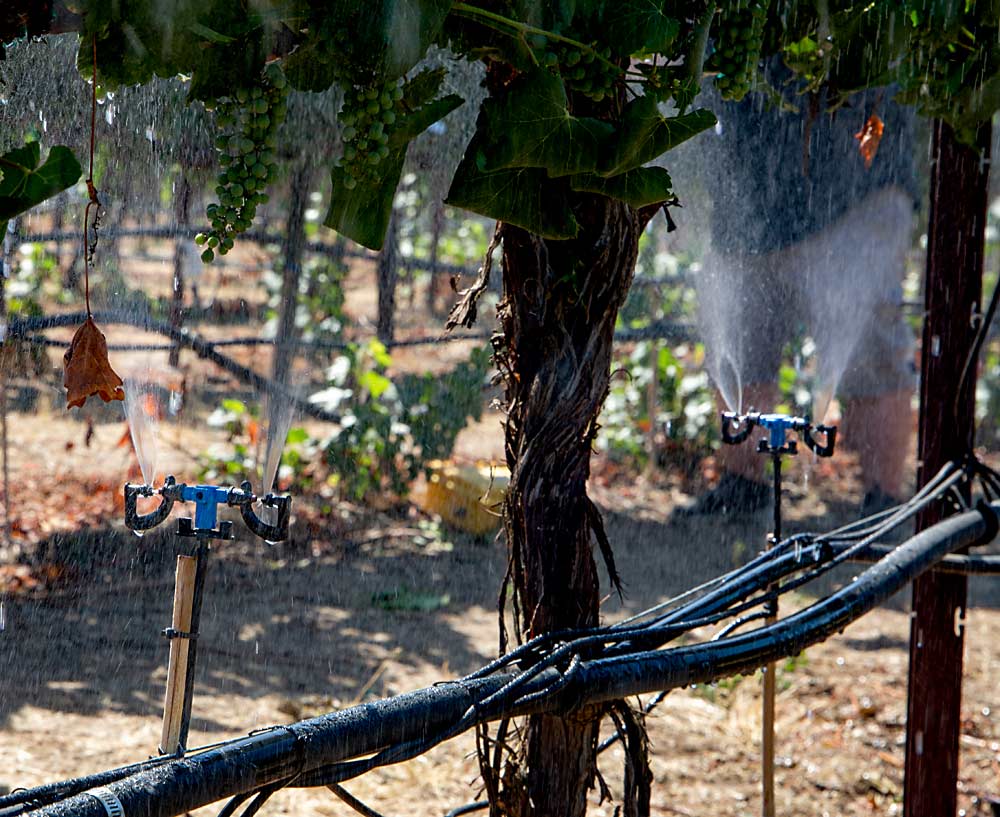
Growers need this research because, while they all employ deficit irrigation in Washington, they also all have different definitions of the term and different approaches to it, said WSU viticulture professor Markus Keller.
“It’s a line you are walking without knowing exactly where you need to go,” he said at the field day. He recommends water stress between bloom and veraison to shut down canopy growth and convince the vines to focus on fruit growth.
For many growers, it’s an art based on the evidence of experience. Making it a science requires measurements of plant stress and soil moisture — and a model of the relationship between the two. That’s where the AI comes in, to find patterns in the pile of data Schrader and his colleagues are collecting.
Some companies offer their own systems of sensors and proprietary models to guide irrigation decisions, while other companies just send sensor data to an app for growers to interpret. Carrying all that data in the cloud carries significant subscription costs, Schrader said. The Smart Vineyard team built its own connectivity system to reduce the costs of transferring data and is working toward a tool to host it all in one platform.
Meanwhile, growers want to know what sensors they should try. “The best sensor,” said WSU soil scientist Troy Peters, “is the one that’s already in your field,” with a history of soil moisture data.
Hot grapes, cool grapes
The demo farm also hosts a head-to-head comparison of two cooling systems, both triggered by thermal imaging sensors.
The first system is a mist cooling approach developed by Keller’s lab to target the fruit zone.
“Keeping the whole canopy cool is not the goal. The leaves can cool themselves down very effectively, but the berries can’t,” Keller said. He favors a mist approach to minimize water use.
The alternative approach, developed by researchers in the lab of agricultural engineer Lav Khot, was designed as a fixed spray system to deliver pesticides with no drift. The system uses pressurized air and emitters placed along the drip line and on trellis posts to get sufficient coverage while being compatible with mechanized operations, said doctoral student Datta Bhalekar.
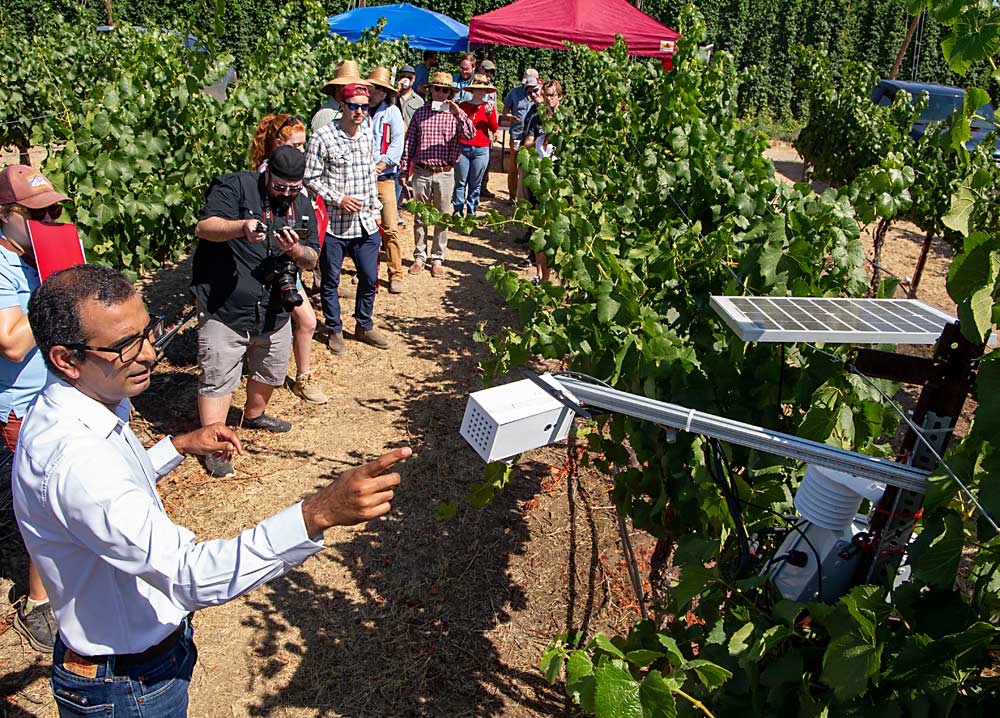
Khot said his lab has finished configuring the system and hopes there will be interest in commercializing it to serve both cooling and pest control needs.
“If growers are investing in new cooling systems, now that heat stress is a bigger concern, why not take a serious look at fixed spray?” he said in an interview after the field day.
A field day demo showed that the fixed spray system used more water than the misting, because of the droplet size. Data collection this season will show how much water each system used and how effective the cooling was.
Leaf wetness sensors, once saturated, trigger both systems to stop.
Both systems are activated by a thermal imaging sensor Khot’s team developed in apple orchards. Mounted over the vines, the sensor can be thought of like a camera taking a photo of a field of view encompassing canopy and clusters. Each pixel in the image translates to a temperature, he said. That’s a marked improvement over the point-specific thermal sensors Keller’s team initially used.
“With the data we capture, we can correlate the canopy temperature and the berry temperature,” Khot said.
Delivering that data, taken every 5 minutes, along with air temperature data from weather stations, should help the AI team to refine grape berry heat stress thresholds. Eventually, Khot hopes the data will lead to models that can predict berry temperature risks based on weather station data, so individual growers can use those instead of their own heat stress sensors.
—by Kate Prengaman
Leave A Comment