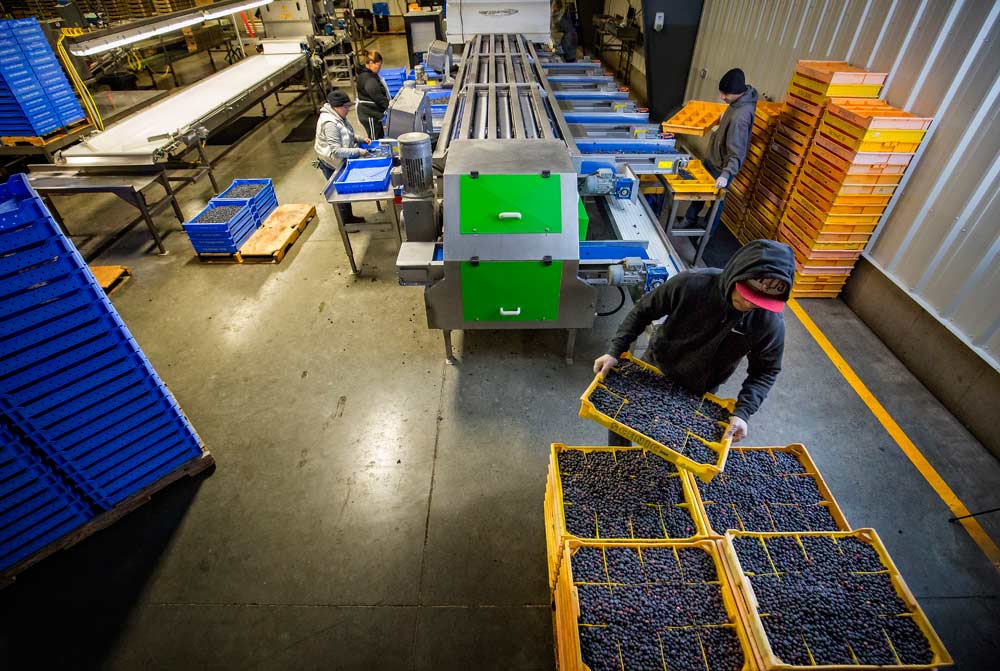
Blue Mountain Farms workers process blueberries on the new optical sorter at the farm’s packing facility in Burbank, Washington on September 7, 2017. The sorter was originally designed to process fresh cherries was adjusted by MAF to accommodate smaller fruit like blueberries and tart cherries. The new line, next to their older line at left, only required six workers to operate from end to end, cutting down on labor needs and costs. (TJ Mullinax/Good Fruit Grower)
Packing line manufacturers are scaling down the powerful optical sorting technology that took over cherry packing lines to accommodate an even more fragile fruit: blueberries.
New sorters promise to lower labor costs, improve export quality through better grading and help growers save quality fruit despite weather damage or bumps and bruises due to mechanical harvest, but manufacturers are still fine-tuning the technology.
At Blue Mountain Farms in Burbank, Washington, the optical sorter installed last year helped hold down labor costs in the packing house, said owner Shirley Lott. Her conventional line requires at least 11 workers, and the new optical sorter can run with just five, she said.
“I think it could pay for itself in three to four years,” said Lott, who employs 30 to 40 seasonal workers in the packing facility and packed 1.3 million pounds of organic blueberries last year.
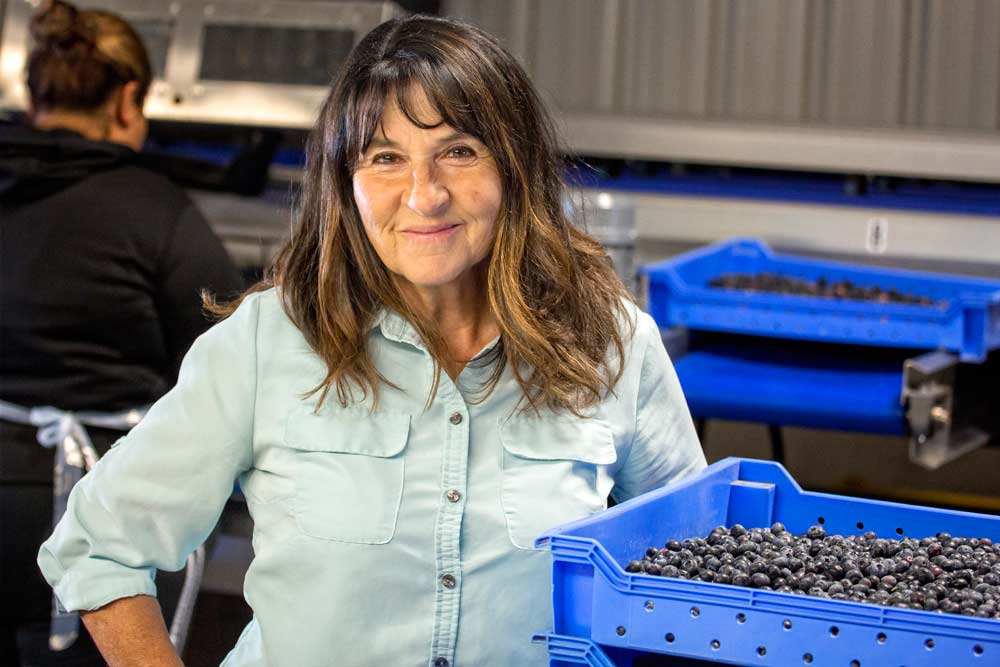
Shirley Lott, owner of Blue Mountain Farms, says investing in the new optical sorter, in the background, will pay for itself in about 3 years in labor savings. (TJ Mullinax/Good Fruit Grower)
The new sorter, with eight lanes each rolling the soft berries single file, is one of the first built by MAF Industries, based on their cherry technology. Other leading manufacturers, including Unitec and GP Graders, are also developing advanced optical sorting technology for blueberries to replace sorting lines that combine hand inspections with a few cameras for color sorting or laser-sorters to detect soft fruit.
“Originally, there were just one or two players, but now many of the companies that have been involved in tree fruit are pushing their technology into the blueberry realm,” said Bo Slack, Pacific Northwest District Manager for Driscoll’s. Driscoll’s, Naturipe Farms and other large berry companies around the world are testing out the new sorting technology, he said. “As a company, we’re seriously looking at it as the future.”
Other packers want to wait to see if the technology proves itself cost-effective and capable of handling the fragile fruit. It’s an expensive investment for a short packing season, with large sorters costing over a million dollars, Slack said.
“Because it’s new technology, a lot of people want to enter in more gradually and let other people work the bugs out,” Slack said.
As with any new technology, there has been a bit of a learning curve for the packer and the manufacturer, agreed Lott and Bryan Brown, the Northwest manager for MAF, which is based in France.
“Blueberries are the most delicate fruit that we handle. We’ve found that we can’t have drops, we can’t run them through again, we have to handle them really gently,” Brown said. Learning from last season, he expects the next generation of sorters available this season to be more efficient and gentle.
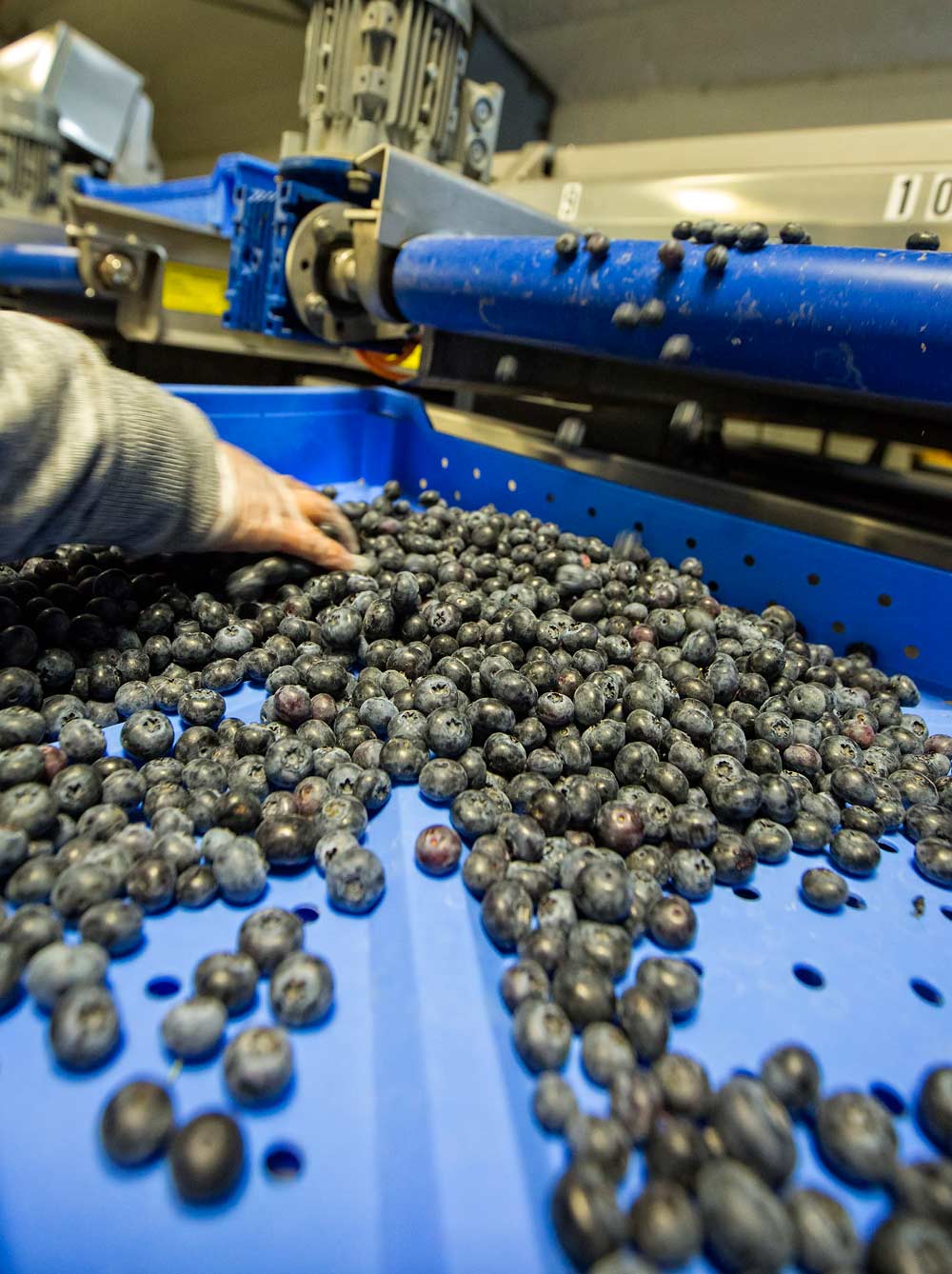
Before the fruit is packed, workers perform a final quality control check of the fruit after it’s passed through Blue Mountain Farms’ new optical sorter. (TJ Mullinax/Good Fruit Grower)
Lott said they had some technical challenges just learning to use the new technology and problems trying to run wet berries, which gummed up the sorter. Blue Mountain continues to run its laser and hand sorting line just as much as the optical line, alternating for cleaning and fruit conditions.
“It’s not going to do everything you need,” she said. But, she said she was pleased with the quality of the sorting. “It can even sort by size, so you can package those larger berries for a specialty market if you have one.”
Lott primarily needs to separate unripe berries used for juice and bruised berries destined for the freezer from the fresh market quality fruit. The sorter performs far more detailed grading if desired, which benefits packers who export, Brown said.
That grading ability could become more valuable for domestic packers as well, as mechanical blueberry harvesters improve and become more widely adopted. Right now, most mechanically harvested fruit goes into the frozen market because of the high rate of bruising, but the hope is that a better sorter could save the quality fruit from the freezer.
“Obviously, a higher tech piece of equipment that can take out more defects will do a better job sorting mechanically harvested fruit, although nothing beats quality handpicked fruit,” Slack said. “The key thing is the industry is exploring all the possibilities” and has technology in development if the labor situation worsens.
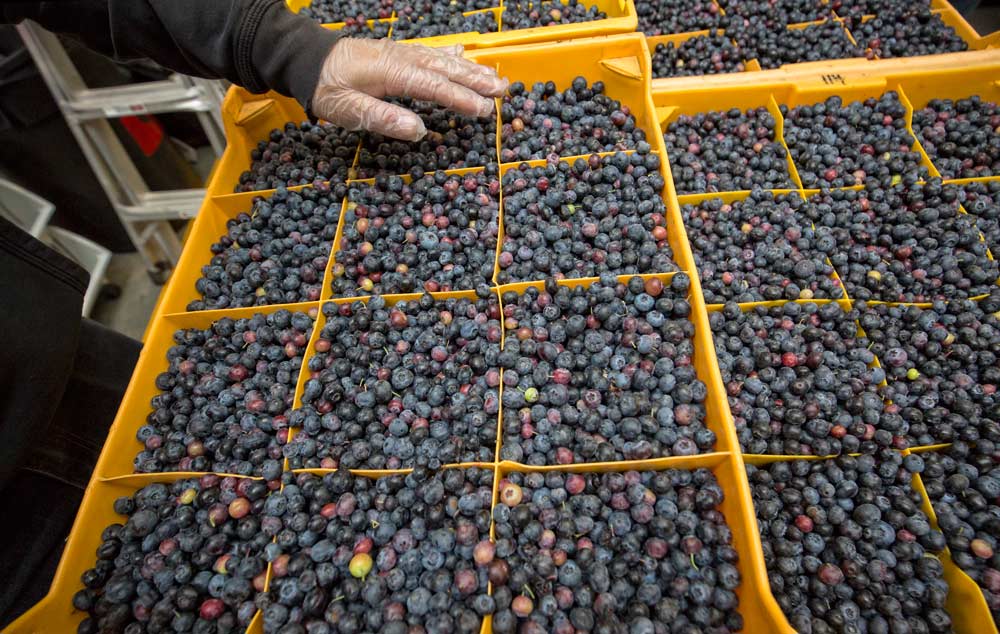
Blue Mountain Farms blueberries designated for processed fruit or juice by the new optical sorter. Many of these berries have noticeable flaws to the naked eye, however the optical sorter kicks fruit into these trays that also contain internal bruising or damage unsuitable for fresh market sale. (TJ Mullinax/Good Fruit Grower)
At Blue Mountain last season, Lott didn’t have a chance to test the optical sorter with mechanically harvested fruit because her crews were able to hand pick until the bushes were almost clean. Some years, she rents a mechanical harvester for a final pick of processing fruit on their 100 acres of blueberries, but thanks to cooperative weather, last year she was able to get it almost all picked for the fresh market.
But in future years, Lott said she wants to see if that capability can benefit her business. And with a new cooler space built over the winter to scale up capacity to packing 3 million pounds of berries each season, she hopes to offer packing services to more blueberry growers in the region. The optical sorter could be an extra selling point, as well as keep her labor needs down as she expands the operation.
“There are just new things happening all the time, and the technology keeps getting better and better,” Lott said. “It’s not that we don’t like workers, but the minimum wage keeps going up, so we have to fine-tune things to find ways to keep costs down.” •
—by Kate Prengaman
Leave A Comment