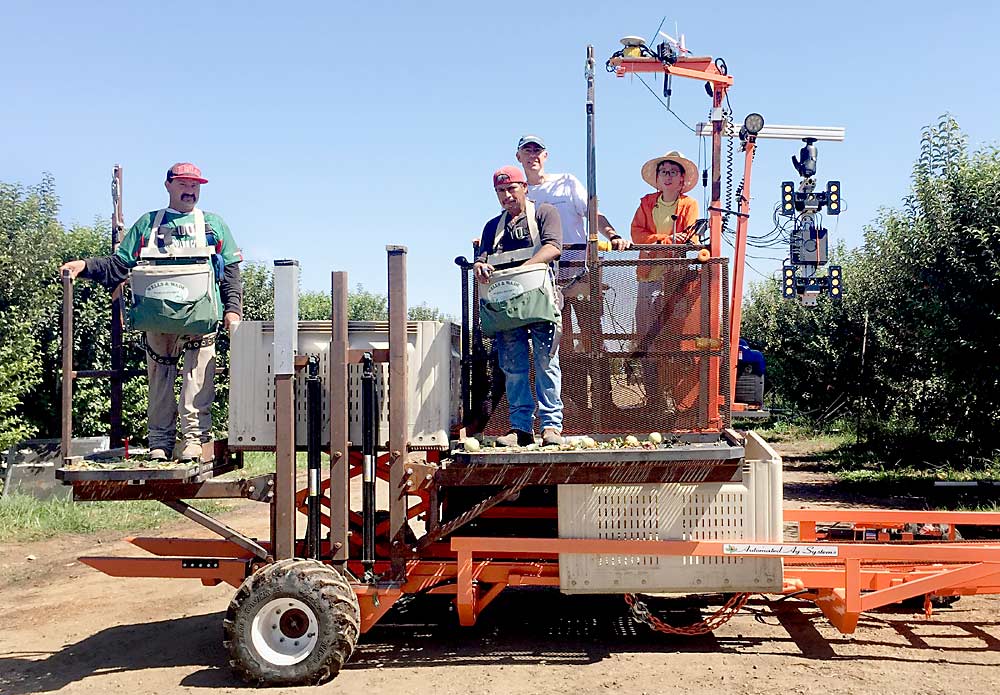
Worker-assist platforms are already prevalent in the tree fruit industry. Meanwhile, robotic harvesters loom but remain an expensive leap from widespread adoption.
There might be benefits growers can gain from a middle ground, said Stavros Vougioukas, a University of California, Davis associate professor of agricultural engineering.
Vougioukas and his team of engineers and computer scientists have developed a prototype of a “co-robotic” platform that automatically adjusts speed and platform height on-the-fly to put pickers in the most advantageous positions.
“I see automated harvest aids as one stepping stone which is easier to adapt to,” Vougioukas said.
The term co-robot — or cobot — is techie shorthand for collaborative robot, a category of automated technology that aids humans operating in the same space, instead of replacing them. In the relatively new arena, programmers “train” robots to work with and adjust to people in all their nuances, mood swings or levels of fatigue.
“Collaborative robots really need to be programmed in light of human behavior, and we are just scratching the surface,” Vougioukas said.
In his platform’s case, a computer measures how fast pickers are working and where the most apples hang, adjusting both height and speed accordingly and finding the most efficient place and pace to operate.
For the opposite example — stand-alone robots — think of a packing house robotic palletizer. Turn it loose and it moves as fast as preset limits allow, making decisions based on its own efficiencies, not those of people around it. It works for people, not with them.
Method, trials, results, reaction
To build the co-robotic platform technology, Vougioukas mounted a computer vision system, developed by a Carnegie Mellon University robotics team led by George Kantor, to a Bandit Xpress platform tricked out with two hydraulic decks. Commercial platforms usually have four decks, two on each side, but the research budget was limited, Vougioukas said.
Zhenghao Fei, a doctoral student, designed the computer software and electronics, and UC Davis engineer Dennis Sadowski designed the hydraulics.
The computer system generates a fruit density map and then moves the platforms up and down, based on the workers’ heights and picking speeds, to put them in the most efficient spots. Engineers enabled the computer to register the pickers’ progress by fitting them with instrumented picking bags — commercial bags modified with scales.
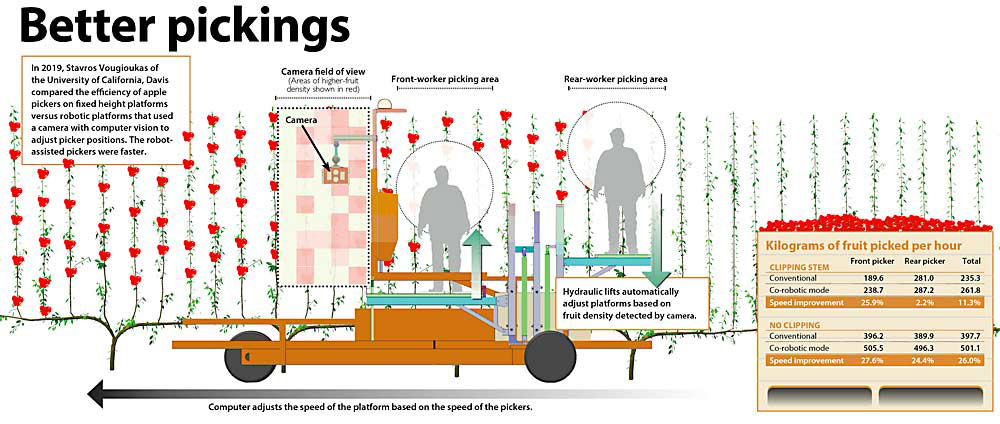
Vougioukas tested it for two years in a V-trellis Fuji block near Lodi, California. His second-year statistics show that the automated platform boosted picker efficiency by 11 percent when clipping stems and 26 percent when not clipping stems.
Vougioukas was not sure why clipping made that big of a difference, though it’s possible one of the pickers skewed the results because he just happened to be slow at clipping.
Vougioukas’s trial, which ended in 2019, was funded by a four-year grant of $1.2 million under the National Robotics Initiative, driven by the U.S. Department of Agriculture’s National Institute of Food and Agriculture. He’s open to future trials to test safety and efficiency if financial support becomes available.
Automated Ag Systems, the Moses Lake, Washington, manufacturer of the Bandit Xpress, helped Vougioukas’ team retrofit the platform with hydraulic decks. Company owner JJ Dagorret called the development “crazy awesome.” It will save pickers time, energy and strain on their bodies.
“It’s like bending over to pick up something off the ground (compared to) picking up something off your kitchen counter,” Dagorret said.
The current commercial version of the Bandit Xpress has a deck in front of the bin and a deck behind. The back deck is hydraulically controlled to allow the crew to discharge a full bin. Hydraulics on the front deck are optional, but most growers leave their pickers at a set height on both decks.
Automating the decks’ height adjustment with the UC Davis co-robot would maximize workers’ efficiency in real time, without giving them another decision to worry about.
“Their focus is to pick fruit,” Dagorret said. “They don’t want to be messing with it.”
Grower Jeff Colombini, who hosted Vougioukas’ trials, is open to the idea but wants to see more commercial results before he endorses it.
Colombini currently uses nine Bandit Xpress platforms. His crew members use a forklift to set the height of the front deck at the beginning of the season. They manually control the hydraulics of the back perch, as needed.
Vougioukas’ team also asked the pickers for their opinions on the system. They reported they appreciated the adjusting heights, which prevented them from stretching or bending as much.
“They really liked that,” Vougioukas said. •
—by Ross Courtney
Leave A Comment