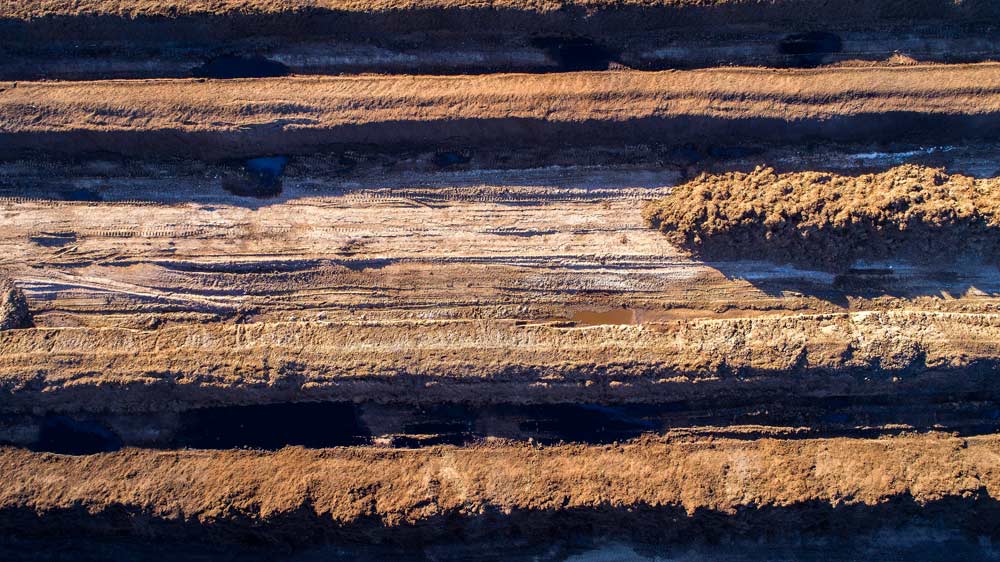
Will increasing scrutiny of food safety practices in orchards push more growers away from using raw manure?
It’s unclear at the moment, as the U.S. Food and Drug Administration is conducting a risk assessment on raw manure before it settles on a preharvest interval that will best protect crops from contamination. This risk assessment replaces the initially proposed 9-month preharvest interval, said Faith Critzer, produce safety extension specialist at Washington State University. That proposal had received much criticism from farmers.
For now, the agency has said that growers can continue to use manure in compliance with the U.S. Department of Agriculture’s National Organic Program standard, which requires a 90-day interval for crops not in contact with the soil and minimizing potential for contact with the produce, which is far easier for tree fruit than, say, vegetable crops.
But treated compost won’t be subject to the same regulations, since it’s already been through a process to control pathogens. That’s one of many reasons, including the horticultural benefits, that more growers are now opting for compost, said crop consultant Dan Griffith of G.S. Long.
“Most operations see the future being compost,” he said. “There’s even more conventional guys using compost now. It’s becoming more common all the time.”
Compost providers say that the carefully managed high temperature process of composting ensures a safe final product, but most tree fruit growers seek out compost for its benefits in terms of improving the soil health, water retention, and increasing organic matter and fertility.
“What it comes down to is what is creating the best fruit,” said Nate Fleming of Dirt Hugger, a Dallesport, Washington-based compost provider that works with Columbia Gorge cherry growers among others. “We work with a lot of orchards, and what we’ve seen is by and large people trying to rebuild their soils.”
Food safety regulations aren’t sending him customers, he said, but it’s an added benefit. Recently more customers have been requesting documentation of the compost’s certification and testing to share with their own certifiers and regulators, he said.
So how do commercial composters certify their products and what should growers look for when shopping for compost?
A proven process

Certified commercial composting facilities must ensure that the heat-loving bacteria that drive the decomposition process are doing their job well enough to kill pathogens and weed seeds. Known as the Process of Further Reductions of Pathogens, PFRP, it requires maintaining temperatures above 131 degrees for 15 days in traditional turned piles.
At Natural Selections Farms in Sunnyside, Washington, workers walk row after row of compost windrows, taking temperatures to ensure that the process is working correctly. If the compost is too wet, too dry or too densely packed so the bacteria can’t breathe, temperatures provide the clue that something needs fixing, said Nehemias Chalma, the compost operations manager. His role is basically farming the beneficial bacteria that do the decomposition work — which requires feeding them the right ratio of carbon to nitrogen.
“My job is just to keep them happy, to keep the right conditions for them to do the job,” said Chalma, who started on his compost career more than a decade ago as a truck driver for Natural Selections with lots of questions. Owner Ted Durfey recognized his curiosity, sent him to compost school, and today, he frequently leads trainings. “The temperature checks allow us to have a one-on-one connection with a row. We can really see what each row is doing and what it needs.”
Each 800-foot long windrow represents a different compost recipe — a mix of hop waste, prunings, culled fruit, winery and brewery waste, and other feedstocks — selected to work together well to make the microbes happy and result in compost that meets the exact nutritional needs of a customer. For example, blueberry growers need to lower soil pH, so recipes for them include more acidic ingredients like grape pomace, Chalma said.
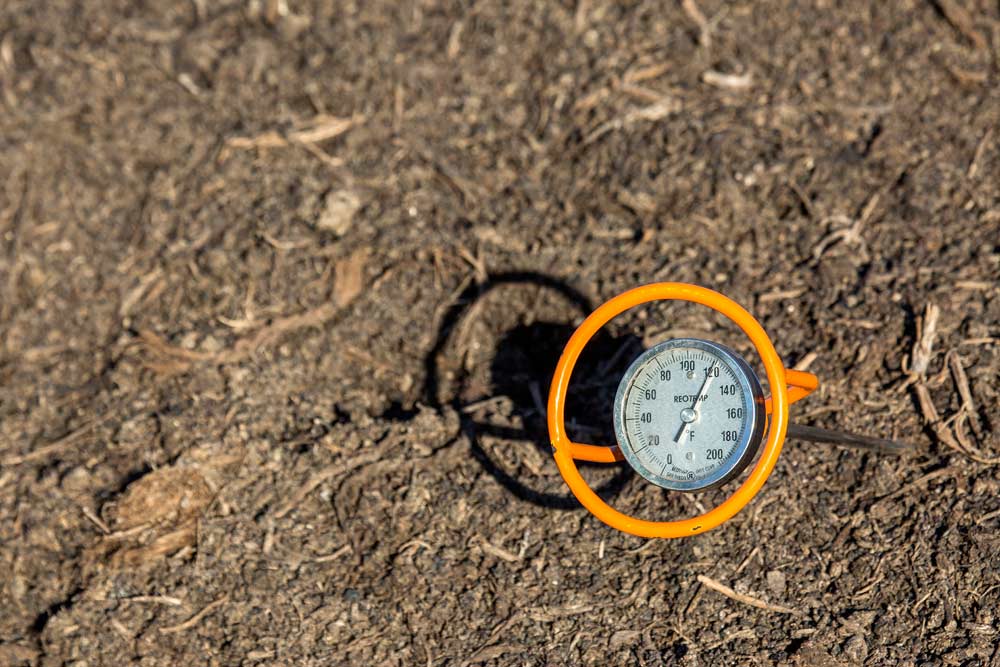
In a freshly mixed pile, the temperature heats up rapidly as the bacteria get to work. Those first 15 days during the pathogen reduction process, staff turn the piles five times. Once that phase is complete, no untreated material can be mixed in with the compost and it starts to cure. Piles shrink almost in half as the organic matter is processed, the smells and textures change, and the temperature slowly cools.
“It’s a roughly four-month process to where it’s stable enough to go out,” to customers, Chalma said.
The process is the same for organic compost as it is for conventional compost, although certain feedstocks can only go in the conventional compost. Natural Selections’ production is about 80 percent organic, said co-owner Chelsea Durfey.
At Dirt Hugger, the site looks a little different. Compost piles sit on top of an aerated pad — buried pipes that blow air into the compost piles — which speeds up the hot composting process, Fleming said. The blowers can adapt to temperature readings in real time to maintain optimum temperatures and large compost turners regularly mix and fluff the material, which is more time and space efficient than using front-end loaders, he said.
Neither Natural Selections or Dirt Hugger regularly use manure in their compost process. Chalma said that despite the high nutrient levels, dairy manure can have high salt and is generally not consistent enough to work well in his carefully crafted recipes and overall system.
Many dairies and other livestock operations do compost their own products and sell those to growers as well.
No matter how the compost is made, all finished products should be sent to third-party labs for testing for pathogens, heavy metals and nutrient analysis. In rare cases, that documentation can come to the aid of a grower or other customer if there is a concern about contamination down the road, Chalma said.
What growers need to know
Compost is great for soil, but don’t expect it to be an immediate source of nitrogen to your trees the way manure is, Griffith said.
“Compost has nearly all its nitrogen in the organic form,” he said, which a good nutrient analysis will tell you, as opposed to free nitrate or ammonia found in manure. He also recommends checking the C:N ratio. “That carbon is the food source for the microbes you are trying to keep alive when you put compost on the soil. True compost is alive and manure is dead, in terms of beneficial microbes.”
Fleming agreed.
“We don’t sell it as a fertilizer, but as a soil amendment to the living soil system,” he said. “We make a humus-based product that’s undergone the PRFP process and has been thoughtfully and scientifically made, so a little bit can go a long way.”
Dirt Hugger also offers farm services, including spreading compost on-site or renting out the necessary equipment, to help growers make the most of their product in their orchards. That’s where business is growing the most with conventional and organic growers, Fleming said.
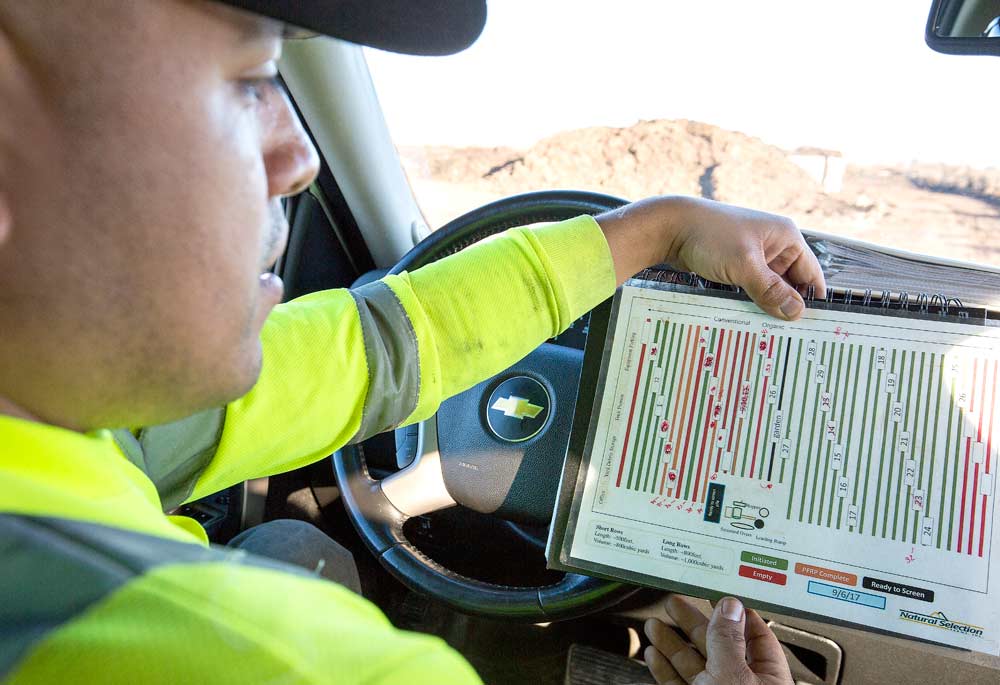
At Natural Selections, tailor-made compost blends are the norm. Some piles, with a large percentage of culled apples, can smell like apple pie baking when the temperatures heat up, Chalma said. And when it’s finished and cooled off, it just smells like good dirt.
“There’s so much science to this and it’s also such an art,” Durfey said. “Look at this; it’s 80,000 tons of waste that becomes a nutrient source.” •
—by Kate Prengaman[/fusion_builder_column]
Leave A Comment