Robotic wagons that assist field workers are a new division in the realm of agricultural technology, and two startups are attracting millions in venture capital funding, well-known research advisors and high-powered corporate partnerships.
“Competition is inevitable, competition is good,” said Charlie Andersen, the CEO of Burro, the company formerly named Augean Robotics with headquarters in Philadelphia. The company has made commercial inroads in California’s table grape, blueberry and nursery industries. “What it means is that the market is real,” he said.
Burro recently received $10.9 million in Series A startup funds from a variety of venture capitalists, including S2G Ventures and Toyota Ventures, and plans to use the money to scale up from roughly 90 robots to more than 500, Andersen said.
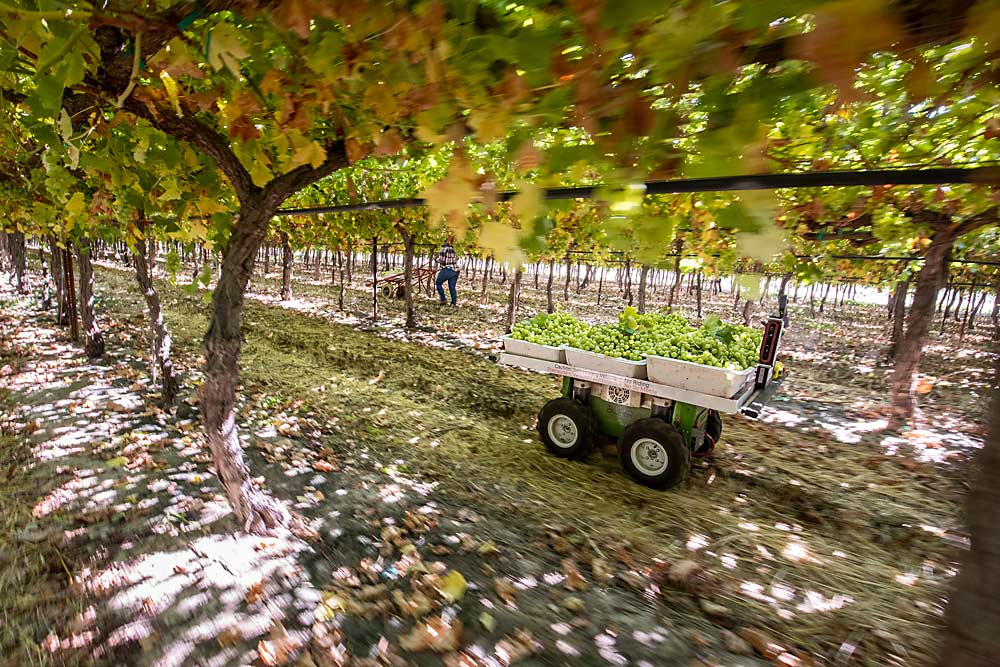
So far, the company has not reached Northwest blueberry growers, but Lisa DeVetter, Washington State University small fruits horticulture professor, considers the tool a good bridge between expensive hand labor and the still-maturing technology of fresh-market-focused over-the-row harvesters.
Harvesters have improved, she said, but “we’re not really there for fully automated for fresh-market, for reasons of fruit quality and storability concerns.”
Meanwhile, the $12,000 price point for Burro is such that growers can buy one just out of curiosity. “It’s a lot easier to dip into that technology, even if your confidence is only so-so,” she said. Over-the-row harvesters run about $250,000 to $300,000.
Burro does not plan to target the tree fruit industry, since its bins can weigh up to 1,000 pounds, Andersen said. At least not for the time being. Apples already have bin haulers that move quickly, he said. The company wants to focus on chores that have no mechanization so far.
Burro’s competitor, Carry, is still a prototype, but it has attracted some well-heeled financial backing of its own. Built by Future Acres, a Santa Monica, California, startup, Carry is backed by a research and development partnership with Sun World International, a plant breeder and genetics licensor based in Palm Desert, California. The collaboration exposes Carry to Sun World’s 2,000 growers farming on 55,000 acres around the world.
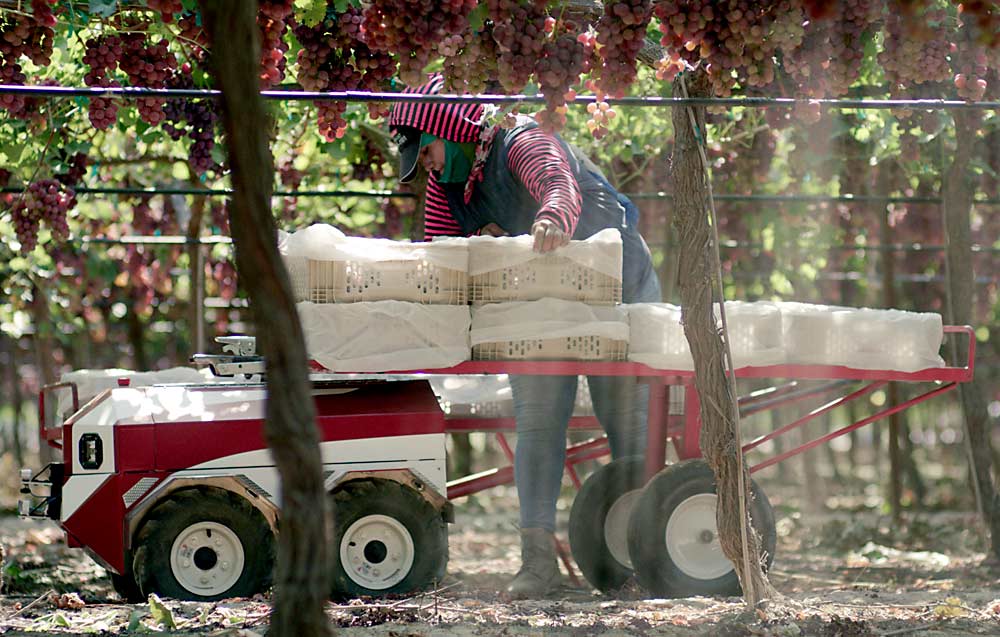
Future Acres recently raised $2 million in funding through SeedInvest, a crowdfunding campaign platform, and expanded its advisory board to include Stavros Vougioukas, a University of California, Davis associate professor of agricultural engineering, company CEO Suma Reddy said. Vougioukas has been developing a collaborative robotic harvest-assist platform for apples.
Future Acres has other ambitious agricultural technology plans, claiming to target solar-powered precision spraying starting in 2023 and automated crop picking starting in 2024, according to its websites.
Both Burro and Carry are examples of collaborative robots, or cobots — machines that learn to adjust to human behavior and assist humans, not replace them. Both carry up to 500 pounds and both have made their first forays into table grapes, a high-value specialty crop that requires hand labor. In addition to the $12,000 machine cost, Burro charges $2,100 per year for software and service. Carry will be priced similarly, Reddy said.
How Burro works
The Burro, which Andersen calls a “people-scale collaborative platform for outdoor work,” functions much like a wagon. Guided by computer vision and GPS, the tool transports totes from picker to checker and back, tracing a preprogrammed path or following a specified person.
Based on tracking of commercial use, Andersen estimates the Burro improves the efficiency of a team of six to eight workers by 15 to 50 percent, offsetting the work of one person per day per unit.
At a table grape farm near Fresno, workers picking Snow Giant table grapes used the Burro in early August, with the cart lugging totes, jackets and water bottles back and forth between the pickers underneath the canopy and the checking tables just outside the block.
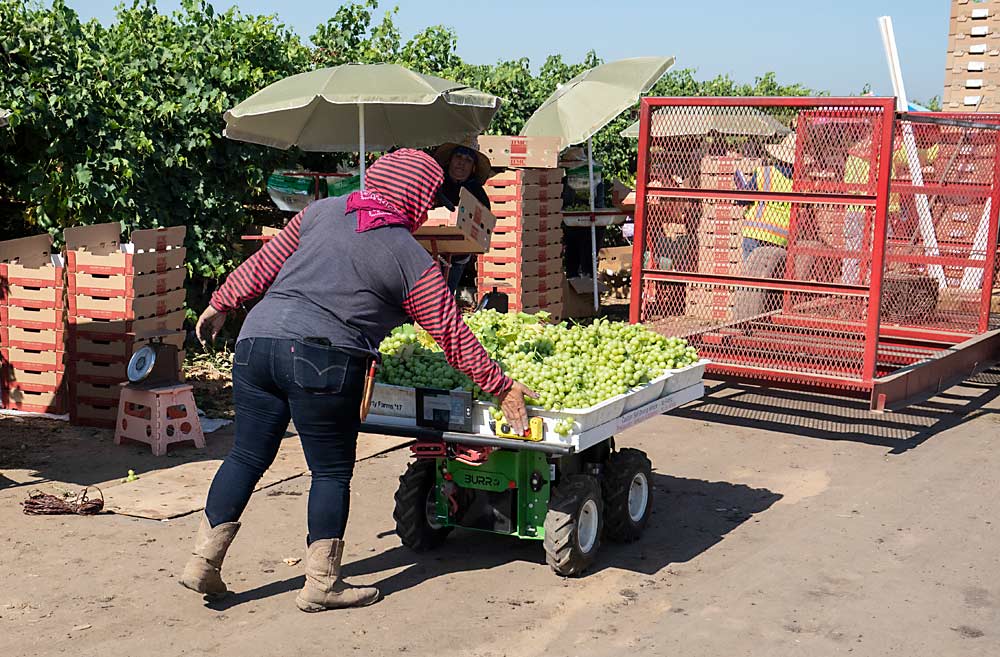
Their supervisor, Cesar Guillen, said the Burro involved a learning curve for his crews. “It took a lot of practice,” he said, but within a week they learned to unload the machine themselves and put it to work without his oversight.
Guillen also supervises a peach orchard. The Burro might work there, he said, but peach farm owners are typically older and may be less willing to change than grape companies.
The company recommends hauling only 12 to 14 totes at a time, to avoid tipping, said Chris Thiesen, head of California sales and service. The company hasn’t used them much on hills, he said. And the company encourages growers to alter some practices to make way for the machine, such as placing bagging stations at one end of the row, instead of both, and modifying the machines to fit their needs.
Burro uses GPS to navigate outside of rows and camera vision to navigate within rows, Thiesen said. In some locations, the cellular network provides enough of a signal for the GPS, but sometimes a farmer will set up a base station on a tripod to make GPS more precise, Andersen said.
—by Ross Courtney
Leave A Comment