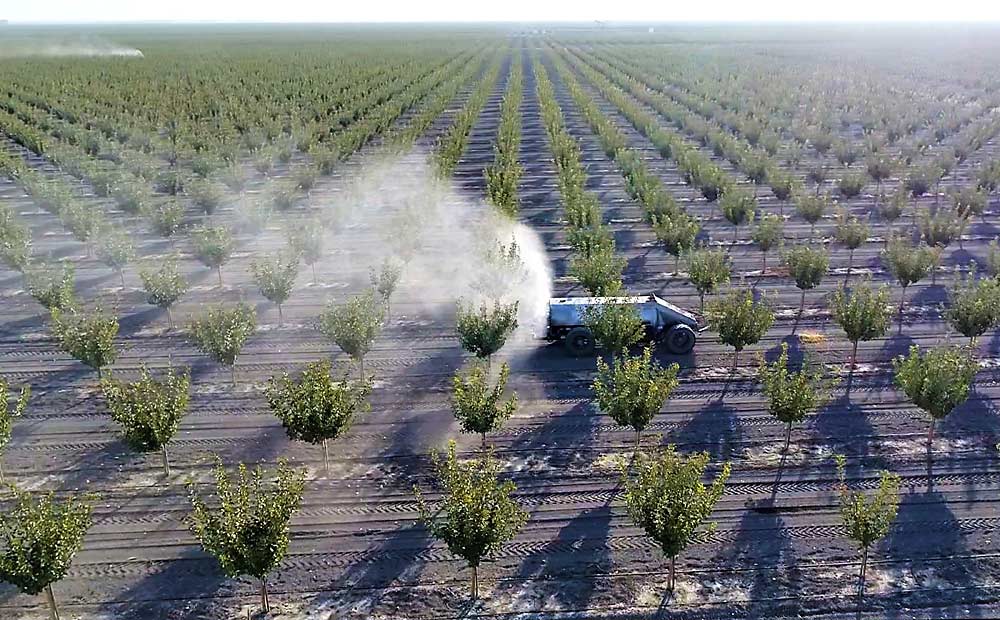
The makers of an autonomous sprayer used in California nut orchards are eyeing tree fruit as their next market.
GUSS, a self-driving sprayer, has made commercial headway in the almond, pistachio and walnut groves of California. The Kingsburg-based company so far has sold 46 units, each at a price of $285,000.
That alone impresses Karen Lewis, a Washington State University tree fruit extension specialist known for her understanding of mechanization. She has seen ideas come and go, with few customers actually buying. For GUSS, farmers seem to be writing checks.
“It doesn’t happen every day in our business,” Lewis said.
The company’s engineers are currently building a smaller prototype, called Mini GUSS, to fit in the narrow rows of trellised tree fruit and wine grapes. Almond rows, by contrast, are usually 20 feet wide.
Developers are about 80 percent done with the Mini GUSS and have scheduled trials in California grapes and trellised stone fruit this winter near Fresno, said Gary Thompson, chief operations officer of the company. They plan to bring a prototype to Washington next year.
“The next big market we want to target is the Pacific Northwest,” Thompson said.
The Mini will be 6 feet wide, 5 1/2 feet tall and 20 feet long with a 400-gallon spray tank, powered by a 3.8-liter Cummins diesel engine. The company has not yet decided on a price for the Mini GUSS, Thomspon said.
GUSS, which stands for Global Unmanned Spray System, uses a combination of GPS, lidar and computer vision to guide itself through orchard rows. One person with a laptop can operate up to eight sprayers remotely.
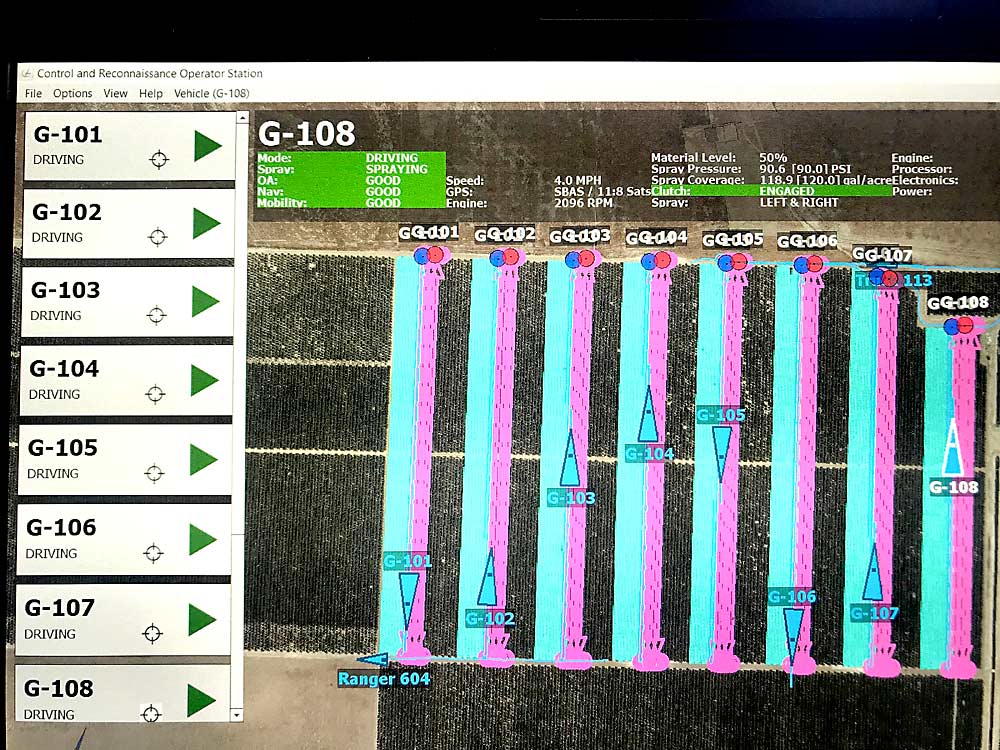
The biggest challenge is programming the vehicle to operate in areas of unreliable GPS connection, such as under a V-trellised tree canopy, Thompson said. That’s where the lidar and computer vision kicks in.
The company still does some custom spraying, which is how it got its start in 1982. However, for growers who purchase the machine, return on investment happens between one and three years, Thompson said, based on the company’s own internal estimates and reports from about a dozen growers. Those return projections take direct labor into account but leave out yield and quality increases due to better spray timing and reduced risk of liability. Those are harder to quantify, Thompson said.
Gwen Hoheisel, a WSU Extension specialist, calls the GUSS just one of several exciting “intelligent” forms of spray tools. GUSS steers itself, others modulate pulse width, still others provide more precise operator control. Growers will have to decide for themselves what is most important. As time goes by, many of these functions will work in tandem.
“Eventually these technologies may all be offered on different machines,” said Hoheisel, who specializes in sprayer education.
Others
GUSS is not the only piece of self-driving equipment with potential for the fruit industry. Lewis also has been eyeing Burro, an automated platform currently used in California’s table grape industry. A few blueberry growers have been running trials with the Burro in California and New Jersey.
Growers typically use the Burro to haul trays or small buckets of picked fruit from worker to weigh table and back again. The system uses computer vision, with help from GPS, steering itself around buckets, bushes and other obstacles. It also can be commanded to follow a single person, usually the crew boss setting up the work rows in the morning.
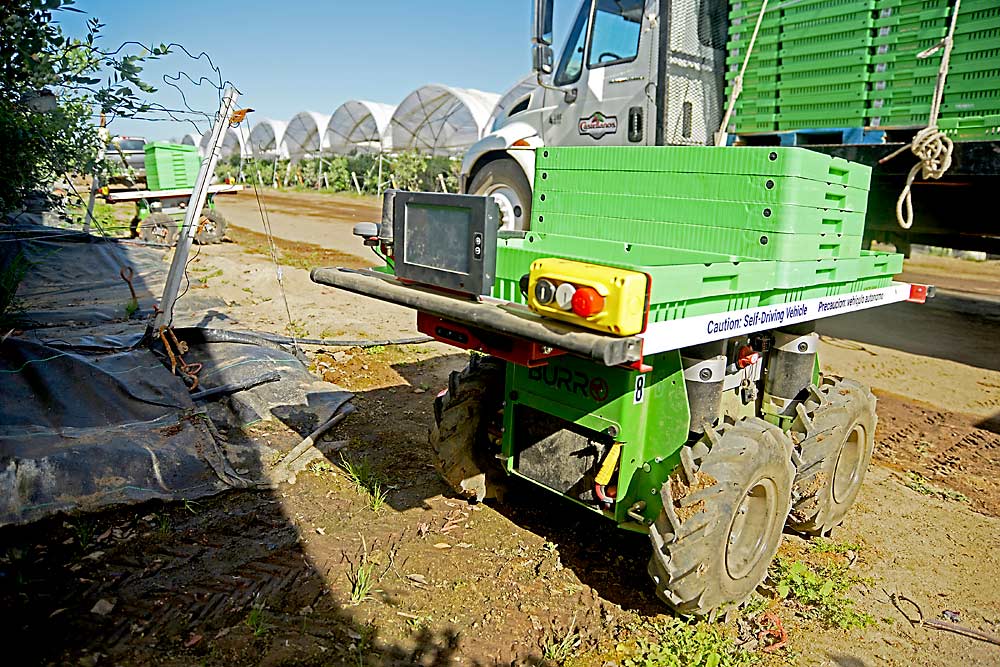
The Philadelphia manufacturer, Augean Robotics, has about a dozen customers, said Charlie Andersen, CEO. That’s a mixture of service customers who hire between six and 10 units for a matter of weeks and some who have purchased the machines outright. For purchasers, the Burro costs $10,000 each, with a $2,000 yearlong service fee.
Return on investment is about one year, Andersen said. That’s based on the company’s own analytics working with customers who have seen a 10 percent to 35 percent boost in picking efficiency in the same blocks of the same variety at the same time. One robot usually supports between six and 10 pickers.
The company has not yet tried to enter the tree fruit industry. “We’ve struggled to address the demand as it is,” Andersen said.
Getting the machine to move around the vineyard is relatively easy, Andersen said. The company may try to add data collection and, later, dexterity functions, such as pruning, to the platform as they progress, he said. Those are trickier in the robotics world.
Lewis was unsure how the Burro would fit into the tree fruit industry, though growers need something autonomous and small to fit between rows. Perhaps it could help on some pick-to-pack specialty harvests. She also sees some research utility in Burro, helping scientists and research aides collect data more efficiently.
When it comes to mechanization, growers typically prioritize a quick return on investment, reliability and functionality, Lewis said. They want to know if the tool will really work for them. Even in good times, growers are reluctant to write big checks.
Thus, she warns prospective technology companies to conduct robust, impartial and honest return-on-investment studies that factor in all costs and expenses, even those hard to quantify. And she recommends field validation trials, even if they are expensive. •
—by Ross Courtney
Leave A Comment