Planting a vineyard requires more than just planting vines. There are vine stakes and trellis posts to plant, too, plus drip lines and wires to run.
Portugal-based Vinomatos promises to do it all in one pass with GPS-powered precision: Enter its planting machine, the Révolution.
“The difference is that instead of having the planting crew followed by the trellis crew followed by the irrigation, we do it in one pass,” said Leandro Tomás, who leads the company’s planting services in the U.S. “There’s no marking ahead. We bring our own crew and do everything.”
The company planted Washington State University’s newest research vineyard — 4 acres to host soil health studies — in early June and invited interested industry members to watch the mechanical planter in action. Riding along behind the tractor driver, two crew members loaded potted vines and stakes while a third loaded posts. Additional crew members followed to ensure everything was running smoothly and to reload the vines and supplies as needed.

Vinomatos managing partner Georges Mandrafina was on hand to talk about the company’s evolution from early GPS-enabled planting machines in the 1990s to the Révolution, launched in 2020.
“It’s a big innovation,” he said of the machine’s ability to manage different stakes and two different types of posts at one time, at two different depths. The latest iteration can also correct for slopes on hills, Mandrafina said.
Vinomatos launched its contract planting services in the U.S. in 2019 and, after pandemic-related travel restrictions imposed a temporary speed bump, now has four machines in the U.S. The company brings them to Washington after the California planting season, he said.

Tomás said that with a team of five, each machine can plant between 5,000 and 8,000 plants per day, depending on the layout of the site and the challenges of the terrain. Each vine is mapped within a 1-centimeter margin of error, thanks to real-time kinematic (RTK) technology that increases GPS accuracy. The tractor carries a water tank to give vines a drink at planting, and the drip lines simply need to be hooked up.
Tomás said the company charges a fee per plant, but he declined to share specifics, as the fee depends on the scale of the project and challenges such as terrain and trellis complexity.
It’s compelling technology, but growers looking to save labor by contracting their planting need to be prepared for the hiccups that come with adopting any new technology, said Brittany Komm, vineyard operations manager at Sagemoor Vineyards.
After being impressed by a trial in 2022, Sagemoor hired Vinomatos to plant nearly 50 acres this spring across three different sites in Walla Walla and the Columbia Basin, some with challenging terrain and rocky soils. Scaling up, they encountered more challenges, which pushed planting into less-than-optimal weather conditions.

“Overall, I think this machine has great capabilities, but it never fully hit the plants per day I was told it could hit,” based on the 2022 trial, she said.
She chalks up some of the challenges to learning experiences for her team — such as how to design and simplify the trellis system to work more efficiently with the machine. Others, such as the wait time for a specialized mechanic or parts, reflect Vinomatos perhaps being stretched thin on customer service as it expands into Washington.
Layers of basalt rock also posed some problems.
“At Southwind (in Walla Walla) there is a lot of rock, and when you are trying to get 2 to 3 feet of a post into rock, it doesn’t bode well for the post or the machine,” she said. “Growers will have to know their ground and the limitations of the machine.”
Successful use of the labor-saving machine may require more site prep than Washington growers typically do, WSU extension specialist Michelle Moyer said during the demonstration. For example, the machine’s precise stake placement may require more thorough ripping in rocky soils, while crews that hand plant on such sites may just opt to move a vine or post a few inches to work around a rock.
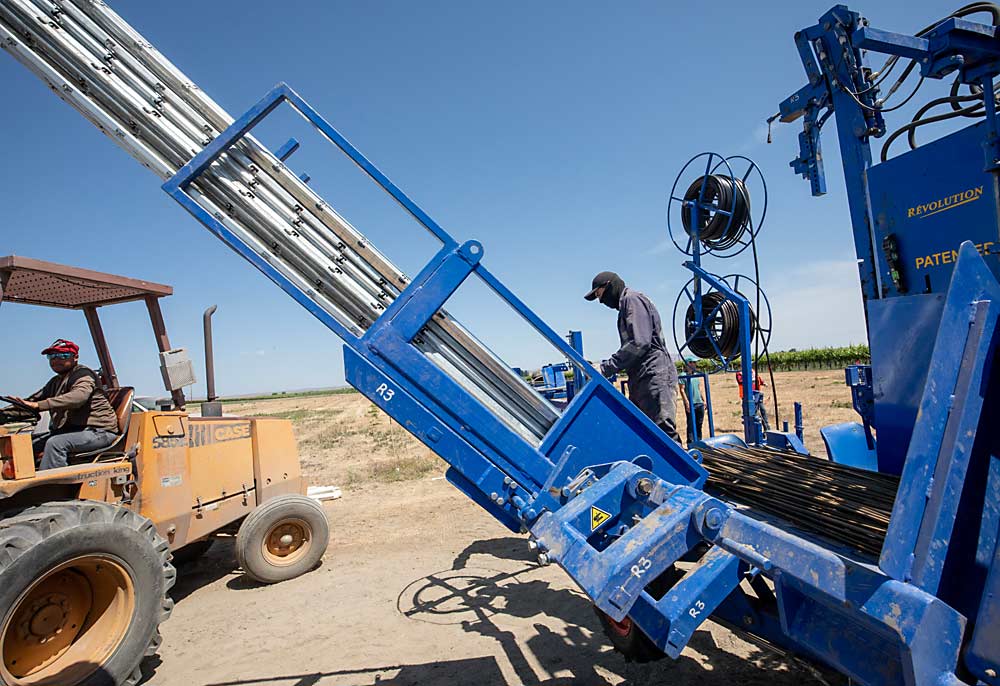
Chris Banek, owner of Banek Winegrower Management, has worked with Vinomatos for the past two seasons, and he said the site prep resembles his hand planting prep.
“We’ll cultivate right before they plant, since you don’t want weeds and debris” in the way, he said.
Vinomatos first rips the vine rows down to 3 feet to open the space for the posts, Tomás said. That’s the first pass, done with a different tractor, and it “guarantees that the posts are at the same depth” and gets the stones safely out of the way before the crew follows on the planter.
Ripping, rather than digging holes, also reduces compaction and makes it easier for roots to start growing, Tomás said.
As for the sites, Banek said he watched the machine work well in the cobblestone soil of the Rocks District in Milton-Freewater, Oregon. Broken basalt layers at the Southwind site Komm mentioned, however, required shifting the block edges, he said.
Banek said contracting with Vinomatos allows him to develop more acreage for clients in the spring while his crew is busy managing existing vineyards.

“I don’t have the resources, meaning the crews, at planting time because we have to stay 100 percent focused on growing the crop,” he said.
He’s planning another project with Vinomatos next year and advised other growers who want to do the same to simplify their trellis system and keep up the pace of plants per day. Vineyards with long runs, good layouts and good ground are key, as is having a plan to stage everything and be ready.
“It does 6,000 plants a day, with posts and tubing and wire and 2 quarts of water, and away you go,” he said. “And it’s straight as heck.”
—by Kate Prengaman
Leave A Comment