family background / Josh is the fourth generation of his family in farming and is the production supervisor at Columbia Fruit. He graduated from California Polytechnic State University, San Luis Obispo. Josh is the son of Susan and Gus Heinicke.
grower / Wenatchee, Washington
age / 27
crops / Apples
business / Columbia Fruit Packers Inc.
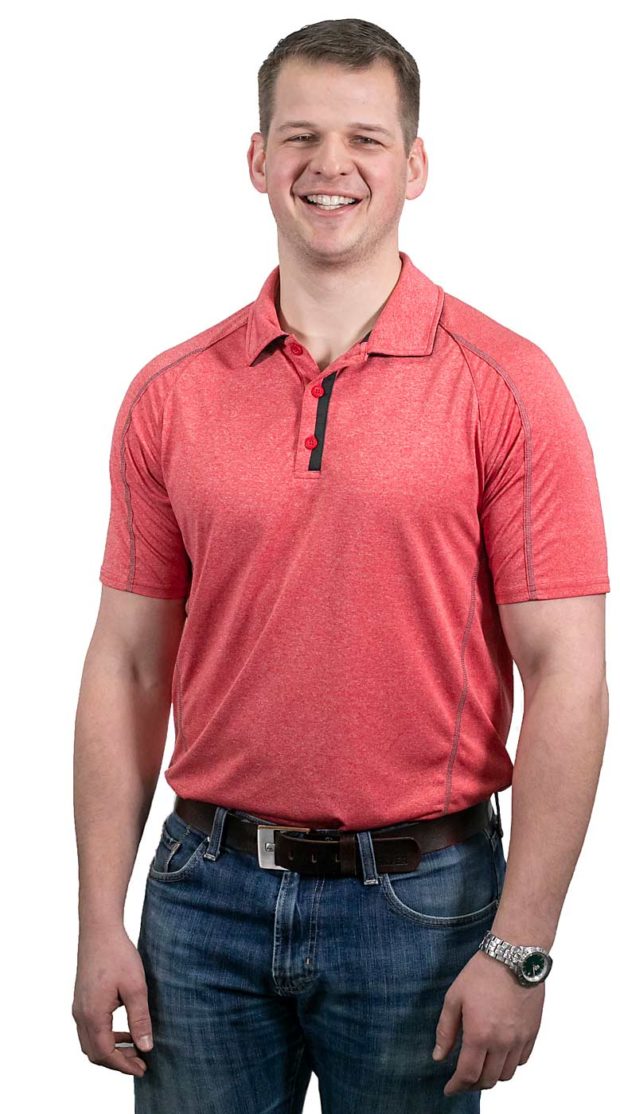
How did you get your start?
My first jobs were in our family orchards, working in cherries in the summer. That work provided a great motivation to go to college.
While at college, I really fell in love with ag — not just the processes but the people — and it’s why I pursued it as a career.
After college I jumped into banking, working at Northwest Farm Credit Services, learning what not to do and what things to do regarding ag finance.
What helped you figure out what you wanted to do?
Before I went to college, I talked with a few leaders in the industry and I asked them, ‘If you were to do your career over again, what would you want to learn?’ On different occasions, people said, ‘I wish I understood the finance part of the business more.’ They said it was something they had to learn and was valuable.
Being able to be knowledgeable about business right out of college is a huge step up. Thankfully, I took that route. The other benefit is that if I understand money, then I can do just about anything.
What have you found since joining a packing house?
The packing house has a unique spot in ag because we are the link between the field and the customer. We immediately get to see the store demands that are driven predominantly by customers, and we also have an obligation to our growers to get a good return to them.
In doing that, we really try to stay in the middle of the road, working to please customers and farmers. Currently, the packing side of ag is also getting an influx of new personnel and is experiencing a lot of change. It’s very fast-paced, and I really enjoy that.
What are the most interesting changes going on?
The first area of change is in food safety. Food safety is something where we have a lot of regulation and very little direction. We have to be very creative and nimble when it comes to finding solutions.
The second change would be working with new varieties. Our family has been growing apples for a very long time and some of these new apples may have postharvest issues that we’ve never seen before. The third thing would be new packaging.
We’ve been looking at finding ways to pack more efficiently to get a good return to the grower while providing what the consumer wants.
Everyone would like the latest pouch bag or the new pack style to market their fruit on the grocery store shelf, and we get the opportunity to figure out how to make it happen efficiently.
What is the biggest need?
What we need on the packing end of the industry is advancement in technology. As we run into labor shortages or food safety issues, it’s important to have someone who understands the flow of fruit and how fruit is handled.
With that knowledge they can better design equipment around those challenges. I’ve spent hours going around and around with engineers who may or may not understand the difficulties that we inherently have, all the while balancing how to improve efficiencies in the packing house.
There’s a lot of new developments in food safety, creating opportunities for people to join the industry. A young person starting out can find just about any type of skill in this industry — that doesn’t necessarily get their hands in the dirt every day.
What are some of the new things you are excited about?
One thing that we’ve done is bring new technology to the packing line. Any time there’s a new packing style, one solution would be to throw labor at it and pack it by hand.
The other way would be to put that investment into automated packing equipment. Recent examples would be with the introduction of pouch bagging machines and robots that can orient apples in a tray to get the color side up or all the stems in one direction.
There are big leaps in the packing and storage areas as well, with equipment that can automatically stack and palletize cartons as well as store them. Regarding food safety, I’m seeing developments in packing line design and engineering.
We’ve put a few things in place, like bin washers, so bins are cleaned before they enter dump tanks. We also created a drying room at this facility that essentially is a large room that dries the apples after they are waxed.
This room is large enough where we can walk in and physically clean instead of crawling inside of a small dryer that’s difficult to sanitize. We aren’t necessarily changing the job — we’re just making it easier.
Leave A Comment