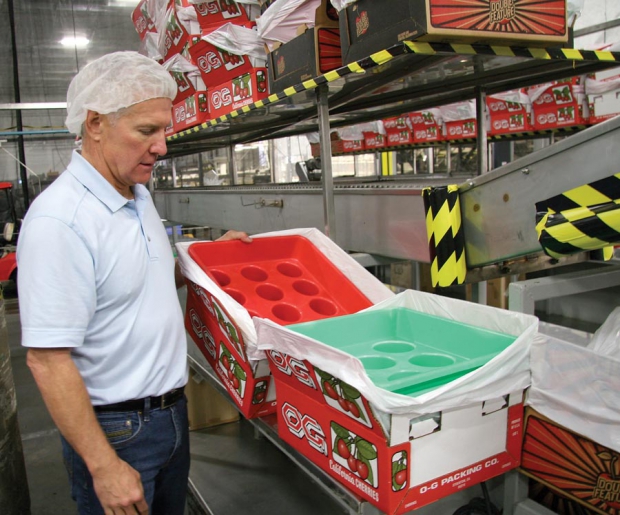
These red and green plastic molds are berry baggers, a device patented by O-G Packing. The molds come in three sizes and reduce the handling needed to fill catch bags and place in shipping containers. Bags fit on the bottom of each funnel hole. When the mold is lifted off the box, all the bags are nicely nestled in the shipping container. Photo by Melissa Hansen
California’s cherry season normally runs fast and furious for about eight weeks. Growers usually have other crops to farm, but what do California packing houses do once cherries are through?
At O-G Packing and Cold Storage in Stockton, California, the Gotelli and Gogna family partners have diversified into other operations to spread out overhead and maximize operating efficiencies. Cherry growing and packing is their core business, but in the last decade or so, they’ve expanded to include blueberries, cold storage rental, walnut cracking and packaging, and one of the most recent additions, early season apricots.
“We have the brick and mortar, and we have the people,” said Tom Gotelli, O-G Packing plant manager. “Our goal is to utilize every inch of our property and facilities.”
The Gotelli family emigrated from Italy and settled in the Stockton area in the early 1900s. Today, fifth-generation Gotellis work in the business during summer while home on break from college. The family has grown cherries for more than 100 years.
Tom’s great-grandfather was an early cherry pioneer. He planted his first cherry orchard in 1901. The Gotelli family were also innovators. They developed and patented the first mechanical cluster cutter used on packing lines to separate the stems of cherries. The Gotellis also patented the “berry bagger” that makes it easier to fill bags of cherries. The berry bagger is a preformed mold that fits inside the shipping container. The mold funnels cherries into bags, eliminating the need to handle individual bags.
It’s a family affair at O-G Packing. Del Gotelli, Tom’s uncle, is president. Tom’s brother Pat is responsible for orchard production and his cousin Paul oversees blueberry production. Brother-in-law Guy Cotton is also involved in the family business.
The “O” in O-G Packing stands for the Oneto family that initially partnered with the Gotelli family to start the company. Oneto is no longer involved, but the Gogna family is now a partner.
Year-round
All of the activities at O-G Packing make for one busy place.
“Our goal is to utilize every inch of our property and facilities.”
—Tom Gotelli
There is some overlap of activities—cherries and blueberries are packed at the same time—but for the most part, the diverse operations fit key windows of opportunities.
When Rainer cherries, which have a separate line, red cherries, and blueberries are all being packed, nine work shifts are run in a 24-hour day, said Tom. However, with the short cherry crop this year, he’s running only about half of normal.
At one time, hundreds of employees were needed in a 24-hour period during their peak cherry season. Fewer are needed now, thanks to new optical sorting technology used on two of three cherry packing lines.
One line was remodeled last year, and another remodeled this year, giving O-G Packing 72 lanes of optical-sorted cherries. According to the equipment manufacturer, this makes it the largest cherry-sorting installation in the United States.
The sorting technology significantly improves size, defect, and color sorting accuracy while reducing some of the labor needed.
Electronic optical sorting is also used for defect sorting on their blueberry line.
“Blueberries were added to our mix about 15 years ago,” said Tom, noting that blueberries usually run a week or two longer than cherries. “They’re a small part of the business compared to cherries.”
Blueberry acreage was rapidly expanding in California until about four years ago, he said, when prices softened. “Blueberries have now reached a plateau in California.”
Monster Cots
While cherries and blueberries are being packed, Gotelli’s apricots in Arvin, California, are also being picked. The apricots are sold under the trade name Monster Cot, and said to be one of the earliest and reddest apricots from California.
Monster Cots are a series of proprietary apricot varieties with similar characteristics bred by plant breeder Dr. Steve Southwick, former University of California researcher. Southwick was hired as O-G Packing’s director of research and development in 2005.
“Monster Cots have a three- to four-week season,” Tom said. “We saw an opportunity for a niche market with early apricots. It’s a team effort and we’re always looking for opportunities and innovations.”
Renting out empty cold storage rooms was another opportunity they capitalized on. When cherries are finished, several large buildings totaling more than 140,000 square feet are rented by canneries from July through October to store peaches and pears before processing.
Not wanting to see another corner in the 70-acre facility sit idle, O-G Packing installed walnut-shelling equipment several years ago which enables them to crack and package shelled and in-shell walnuts. A small crew of about 25 works mostly year round to package walnuts in clamshells and bulk packaging.
It takes management and coordination to run so many different business components, Tom said, but each family member is responsible for different areas. “The biggest advantage of having so many activities is that we can keep our key cherry people employed year round. A lot of our cherry guys can shift to forklift driving, quality control, and other supervisory roles in the walnuts or cold storage operations.”
Leave A Comment