Whole Foods Markets accepted apples treated with carbaryl for the last time Sept. 25, marking the fifth carbamate chemical it has banned from use on products sold in its stores.
Whether Whole Foods’ actions become a trend for other supermarket chains — or if the federal government or states consider canceling the registration for carbaryl — remains to be seen. Regardless, new research shows the promise of mechanical thinning as an alternative.
“I’m not sure that its loss is imminent, but it seems to be a threat every year,” said Rod Farrow, a Waterport, New York, apple grower and vice president of the International Fruit Tree Association.
It would be a tough loss for Northeastern U.S. fruit growers — nearly all chemically thin in the early part of the year using NAA (naphthaleneacetic acid) plus carbaryl or BA (benzyladenine) plus carbaryl.
“If carbaryl were removed from the market, apple growers in the Northeast would not achieve adequate thinning with NAA or BA alone,” said Mario Miranda Sazo, a fruit extension specialist in Cornell Cooperative Extension’s Lake Ontario Fruit program.
That’s why Farrow approached Miranda Sazo three years ago with a request to look at mechanical thinning as an alternative to using carbaryl.
After securing funding from the U.S. Department of Agriculture Sustainable Agriculture Research and Education program and New York Apple Research and Development, Miranda Sazo set about the three-year study.
First-year results were not encouraging because fruit size ended up being too small. However, Miranda Sazo reported to growers who attended the 2016 IFTA New York Study Tour in July that he and Lamont Farms personnel have since been able to employ techniques that didn’t reduce fruit size and produced fruit at rates comparable to standard chemical thinning programs.
The proper rpm
The Lamont Farm canopies form a very rectangular tree, with a compact box and shoots no more than 12 to 14 inches from the trunk. “We believe they are the right canopies for using the thinner,” Miranda Sazo said.
Trees were 7 to 9 years old and trained to a super spindle system. All were planted on Bud 9 rootstock in 2-foot tree spacings with 11 feet between rows.
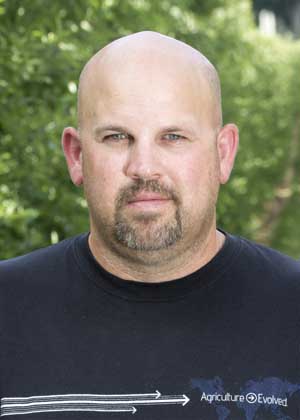
Jason Woodworth
In May 2014, the first year of the trial, Jason Woodworth, one of Farrow’s Lamont Farm partners, ran a Darwin thinner through four rows of Gala and Honeycrisp trees at 240 rpm at 5 mph. King flowers were at 70 to 80 percent bloom and balloon stage for the laterals.
It was too hard on the cultivars. “When we evaluated it, it was a lot harder on the apples, especially the Honeycrisps. We lost shoots and broke spurs,” Miranda Sazo said.
So, in 2015, on the rows they tested the previous year at 240 rpm, they reduced thinner speeds to 220 and 200 rpm.
When Miranda Sazo measured the return blooms, he found the reduced speeds were appropriate for Honeycrisp, but that Gala might respond better at an even lower speed.
For this year’s trial, Miranda Sazo and Woodworth further reduced the speed in the Gala rows, from 220 to 200 rpm and from 200 to 180 rpm in the respective blocks.
They also applied the Darwin thinner closer to the trunk so that when its cords hit the canopy, some also hit the trunk or the wire, retracting when they struck those surfaces. “They were much less invasive in the canopy that way,” he said.
Thus far, they have determined the optimal operational speeds in super spindles lie within the 180- to 200-rpm range. “In a heavier canopy, you could go to 220, but in this one, it would have been too invasive,” said Miranda Sazo.
Follow with MaxCel
In 2014, they ran the string thinner through the rows on May 17 and applied MaxCel (benzyladenine) on June 1 at one gallon per acre. The results were very disappointing, with a 30- to 40-gram decrease in fruit weight in Galas, largely attributable to the string thinning treatments at high rpm.
Last year, in addition to dropping the Darwin’s speed, they applied MaxCel at the same rate when fruit measured 7 to 9 millimeters. The change in speed reduced tree damage, and fruit regained the weight that had been lost in the 2014 trial, which is the result they wanted.
This year, Miranda Sazo is doubling down on the MaxCel applications. He’s repeating the Darwin thinning followed by a single MaxCel treatment on some rows, while on others, he’s following with a second MaxCel application seven days after the first one.
“We expect to see an even better improvement on fruit size from the second application on Gala at harvest,” he said.
Getting there
At a stop on the IFTA summer tour in July, Farrow related how he and his partners have built the farm’s success by producing and marketing fruit of a consistent size and quality. “We like to peak in 88s,” he said, “but we target the sizes where the greatest value lies in each variety.”
So far, he likes what he sees in Miranda Sazo’s trial, though there is one last glitch he’d like solved. “The apples tend to clump on the branches,” he said, “which means they don’t color as well.”
In mid-June, Lamont Farms personnel laid reflective mulch material down along the rows, thinking it might improve fruit set and color, at a cost of $600 per acre.
“You can get 10 years of use if you don’t drive on it,” Miranda Sazo said. He said they initially placed it between the rows and then, three years ago, moved it within the rows. “Color is improved easily by 20 to 30 percent minimum, if not more, in the lower part of the canopy,” he said. •
– by Dave Weinstock
Your first sentence is inaccurate – carbaryl is a carbamate, not an organophosphate.
Byron, We checked and you are right. This article has been updated to fix that error. Thanks for catching that.