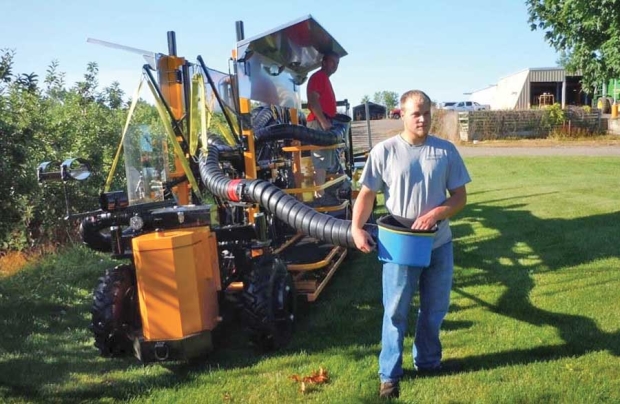
Andrew Duffy, a Phil Brown Welding employee, demonstrates the DBR Conveyor’s new pivoting, plastic bucket, designed to reduce worker strain. (Courtesy Phil Brown Welding)
A little more than six years ago, Good Fruit Grower reported on a field test of the DBR Conveyor Concepts vacuum system apple harvester.
Workers picked over-mature, Golden Delicious apples at the Pennsylvania State Fruit Research and Extension Center in Biglerville, Pennsylvania — after three days of rain — and sent the fruit through the harvester. It passed the bruised apple test “with flying colors.”
Based on data from a second bruising study performed by Michigan State University in 2013, the machine harvester bruised 10 percent fewer fruit than a two-person crew on ladders.
In addition, the machine-based, two-person teams who picked the fruit filled between 25 to 50 percent more bins per day than two-person crews using ladders.
Four years later, Phil Brown of Conklin, Michigan, the “B” of DBR, decided he could build even less bruising into his machine.
The design changes he made include widening the head; changing the foam inside the tubes; creating a new bucket and putting a pivot on the bucket hose.
An in-house study this year showed the design improvements Brown made to the machine delivered an additional 10 percent improvement over the human crew. “The apples we looked at showed almost no machine bruising at all,” he said.
How it works
The self-propelled machine features two sheltered platforms located on either side of the apparatus, upon which workers stand to pick fruit.
The platforms feature hand and foot controls to allow horizontal, forward and backward adjustment of their positions.
Workers pick fruit and place it in buckets strapped to their waists and shoulders on the platform.
Each bucket is connected to the machine by a single hose, which evacuates the fruit as it is picked through an elaborate array of neoprene-lined hoses to a distribution head, which gently drops the apples while evenly laying them into bins.
Once full, a set of forks mounted on the machine moves full bins to the side of the row. Then, an empty bin is selected from a trailing wagon by the same set of forks and inserted as a replacement underneath the harvester.
“The removal and replacement operation takes about 45 seconds,” Brown said.
Improvements
Brown first aimed to widen the lanes inside the machine to allow for larger fruit. “They are coming in at 12 feet per second,” he said. “Apples can’t hit anything but a soft foam pocket.”
Speaking of foam pockets, he also replaced the neoprene foam with a formulation of his own. “We tested a lot of different foam on the distribution wheels. The one we’re using now has more density than neoprene, will be gentler on the fruit and will hold up over the long haul.”
Distribution wheels are located inside the aluminum head. They act to slow down the apples after they leave the hoses, laying them on the distributor.
Next, Brown changed the distributor speed to be independent of wheel speed. In the first model, running speed and vehicle speed were fixed in a 2:1 ratio.
“When the wheel speed would increase, so would the distribution head speed, which increased bruising because it wouldn’t lay them in gently enough,” he said.
Instead of metal buckets on the front end, Brown now uses plastic ones. “They are not fixed on the end of the hose,” he said. “Now, they pivot so there is no strain on the workers at all.”
He also replaced the harvester’s 44-horsepower engine with a 60-horsepower model. More horses mean the harvester will be able to handle hills better as well as snow, extending its usage to year-round work, such as pruning, hand thinning, applying pheromones, trellising and picking. •
– by Dave Weinstock
Leave A Comment