Who wouldn’t want to harvest 60 bins an acre from an orchard planted just a year earlier?
The risk of cropping too soon — before trees have achieved enough growth — has long guided Stemilt Growers to refrain from cropping orchards until the third leaf.
But that rule was challenged by the company’s new Capstone Orchard in Mattawa, the “banana belt of Washington,” because the trees grew to the top wire in their trellis the first season, said Robin Graham, assistant Columbia Basin area manager for Stemilt Ag Services.
The rapid growth in Fuji and Gala blocks planted in 2015 forced orchard managers to break with company tradition.
“It turned out to be a good decision,” Graham said to attendees of the International Fruit Tree Association who toured the orchard during the 60th annual meeting in Wenatchee. In additional to the nearly 60 bins an acre harvested in 2016, the early cropping decision “sapped some of the vigor from the tree and left us with softer wood,” Graham said.
Directing that vigor, using bud counts to guide pruning, using girdling and growth regulators to create branches, and hand-thinning blossoms all help to push the 581-acre Capstone Orchard to its goal of 90 high-quality bins an acre.
It’s an example of how precision crop load management strategies are being built into today’s orchards from the ground up.
“I don’t think there is any function we do in the orchard today that doesn’t have a touch point for crop load management,” Dale Goldy, assistant general manager of Stemilt Ag Services, said during an IFTA panel.
But as tools for precision crop control expand — from high-tech models to guide chemical thinning to labor intensive leaf removal — growers large and small are selecting solutions for their orchards to maximize fruit quality without sacrificing too much yield.
Learning from Honeycrisp
Many of the modern crop load management strategies resulted from trial and error with Honeycrisp, Goldy said.
“I think if you talk to anybody growing Honeycrisp, we’ve all cropped it too early. Hopefully we’ve all learned from that,” said Justin Finkler, operations manager for Riveridge Land Co., which operates 860 acres of orchards in Sparta, Michigan.
Now, he’s aiming for 90 bins an acre off his newest Honeycrisp block, planted on a vertical system with a 10- by 3-foot spacing.
“We’re trying to up our game. We’re striving to obtain 90 percent packout so that we can provide that consistency for marketers,” Finkler said. “Crop load and quality don’t matter if you have the wrong varieties.
When putting these kinds of investments into your system, it’s good to know you are going down the right path.”
Producing high quality Honeycrisp and preventing trees from adapting a biannual bearing habit requires careful crop load balance. Light crop loads can produce large, bitter-pit prone fruit, but overcropping can reduce return bloom.
“With Honeycrisp we’ve had to take the crop load off slowly,” Goldy said. “We create resting spurs but we don’t want to stimulate bigger fruit size or bitter pit.”
Precision in practice
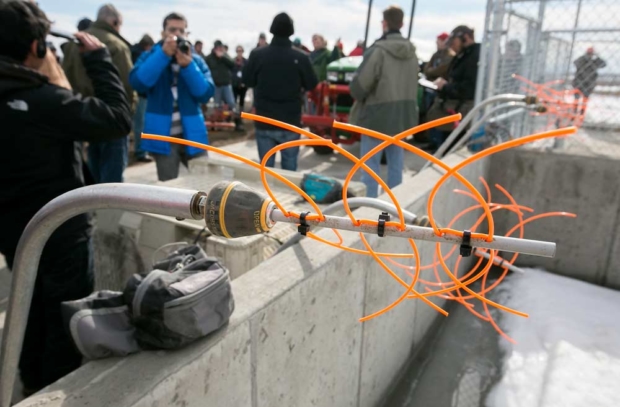
Once you’ve invested in new varieties and high density orchards, using crop load management strategies to increase fruit quality is key, Finkler said, because “there just isn’t room for a process or juice apple with the money you are putting into these new orchards.”
While pruning provides the foundation of the crop to come, Finkler said it’s hard to be aggressive in a region such as Michigan where late frost can kill buds. Because they tend to be more hesitant with pruning, they rely on chemical thinning, he said.
On the other hand, organic growers who can’t use chemical thinners are adapting string thinners for peak performance.
Orchard owner Mike Robinson, who farms near Royal City, showed off his variety-specific thinners to tour attendees, explaining that the longer strings were for harder-to-thin Fujis and shorter strings worked well on Galas.
A common refrain emerged from the tour and panel: It’s all about matching tools to your goals, whether your orchard is hundreds of acres or just a dozen.
“For us smaller guys, you need to think about your goals. You can make more money on bigger sizes,” said Peter Eisses, who operates a 40-acre farm in Nova Scotia. Small growers need to plant new varieties and new, efficient orchard systems to survive, he said in his presentation during the crop load panel. “It’s time to stop creating wood piles. It’s time to grow apples,” he said to audience applause.
Eisses said chemical thinning is an important part of how he manages his Honeycrisp.
“I hate hand thinning with a passion,” he said. “We have a hard time with labor and so have to rely a little more on chemical thinning.”
But while small growers like Eisses depend on chemical thinning to increase fruit size and value, Goldy said that Stemilt is moving away from it in the name of quality and consistency.
“With chemical thinning, we could never get exactly what we wanted,” he said. “The reality is it’s really difficult and we screw it up all the time, but for me, what we need to have as a goal is more consistent tree vigor and nutrient balance.”
Creating consistency
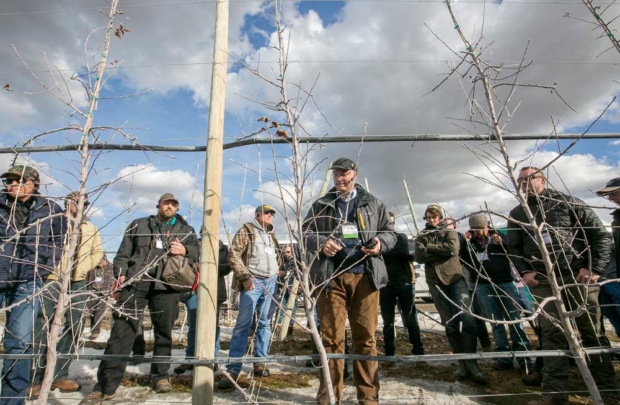
Many IFTA attendees were incredulous about the idea of hand-thinning blossoms, but Goldy said that the cost is worth it for hard to manage varieties like Honeycrisp and Fuji because it minimizes risk.
But, he also describes Stemilt’s hand thinning practice as a “touch up” after pruning, which is the primary way they control crop load. And pruning intensity is adapted to each tree, so that a fully loaded tree is pruned hard and a young tree that’s lagging in growth has more crop load taken off, Goldy said in a later interview.
“Ten, 15 years ago, the thought was that you used uniform farming practices to get uniformity. Thankfully we’ve gotten away from that because the more consistency you have from tree to tree the easier it is to manage the whole block,” Goldy said. “We end up using variable management techniques to create and enhance the consistency from tree to tree.”
The payoff from precise pruning and hand thinning is better balance throughout each block. Consistent trees mean consistent needs for irrigation and fertilizer and a more uniform harvest.
Or as Washington State University Horticulture Professor Stefano Musacchi put it, “Homogeneity of the tree brings you homogeneity of production.”
Other Washington growers aren’t shying away from investing in labor-intensive work that boosts fruit quality. Auvil Fruit Co. hires hundreds of workers to thin blooms by hand each spring in its orchards (Read: “Let hands take hold”).
Meanwhile, Travis Allan of Allan Brothers said that he trains crews to do leaf removal in his high-density orchards so that apples can get the color they need about two weeks before harvest.
“I tell them just to take off every leaf that blocks your view of the apple,” Allan said during a tour of the company’s Mattawa orchard.
The timing depends on the weather; if it’s really hot, he holds off leaf removal until closer to harvest. Allan also puts down reflective material about 10 days before harvest to boost color.
Back at Capstone, manager Brent Huck demonstrated the bud count-based pruning technique that provides the crop load foundation in a third-leaf Fuji block.
There’s plenty of branches for him to consider, as they’ve used a combination of notching and scoring, followed by three or four Promalin applications, to create branches.
At this orchard, they tend to create more branches than they need and then cut them back, which is expensive, but it also helps to control vigor, Huck said.
They aim for 90 buds a tree, pruning down from about 125 this year, Huck said. He tips the laterals he wants to grow to fill the horizontal space and lops off any branch that poses competition to the tree’s primary structure.
There’s plenty of pruning to do because at this warm, sunny site, “trees just jump out of the ground,” but using a bud count method also means leaving some branches that aren’t ideal structurally until next year, Huck said.
“We also need to grow enough apples to pay the bills,” he said. •
—by Kate Prengaman
Leave A Comment