Pallets stand five racks high, cramped, dark and sci-fi eerie. Robotic cranes, guided by lasers and bar codes, retrieve the pallets while automatic dollies on a looped track wheel them to and from a web of scaffolding.
No need for people in the catacombs of Matson Fruit’s cold storage warehouse in Selah, Washington, where electronics move inventory in tight quarters, staggering heights and near freezing environments with an efficiency way beyond that of a human.
“People aren’t so good at it; computers are awesome at it,” said Jordan Matson, who oversees packing and shipping for the company.

Jordan Matson, who oversees packing and shipping for Matson Fruit, stands on a crane at the company’s automated cold storage facility in Selah, Washington. Pallets of fruit are automatically stored and retrieved with robotic dollies and cranes instead of forklifts. (TJ Mullinax/Good Fruit Grower)
Matson Fruit is in its third year with a state-of-the-art cold storage facility that uses a mixture of robotic cranes, computerized inventory and automatic dollies to pack pallets of apples and pears higher and denser, with fewer people and less energy than a conventional cold storage unit that relies on people driving forklifts.
Matson, a member of the fifth-generation of owners in the company, declined to share numbers but estimated his family company spent 20 to 30 percent more on the automated warehouse than it would have on a conventional warehouse with the same capacity.
“You have to be pretty tech-savvy, innovative and a little bit insane probably to do this,” Matson said. But it’s working, he said, and other fruit packing companies in the Northwest are considering similar developments.
Trends and perspectives
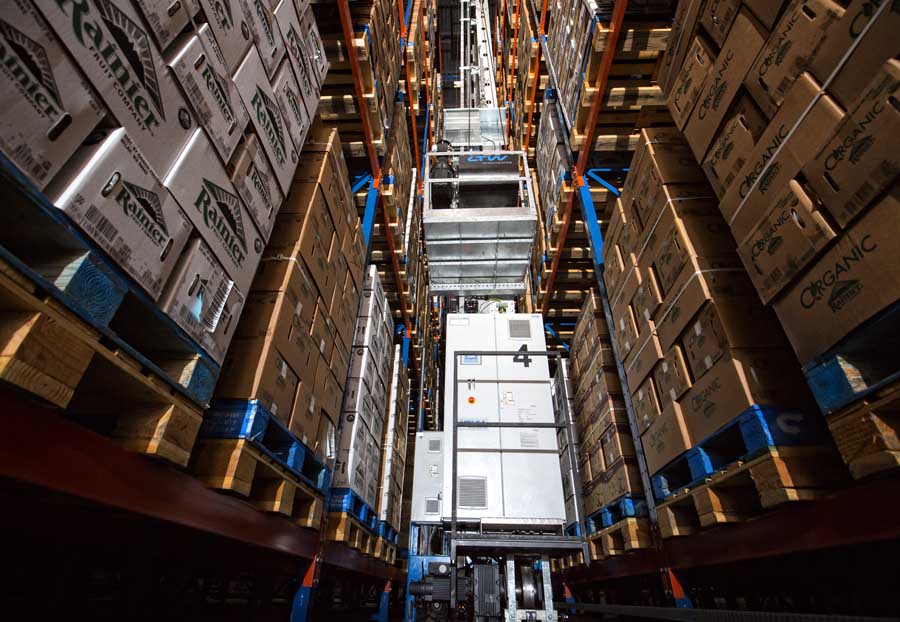
The No. 4 robotic crane, manufactured by LTW Intralogistics GmbH, operates in rows about 6 feet wide and can lift pallets five racks high. (TJ Mullinax/Good Fruit Grower)
The industry calls facilities like Matson’s automated storage and retrieval systems, or ASRS.
Matson’s cost disparity is on par in the worldwide cold storage industry, said Corey Rosenbusch, president and CEO of the Global Cold Chain Alliance, which is based in Alexandria, Virginia, and represents cold storage companies across the globe. “The technology is not cheap,” he said.
But the cost difference between conventional and ASRS facilities is getting narrower in the new age of automation, he said. New construction of cold storage runs anywhere from $115 to $170 per square foot. Conventionally built systems fall on the lower end of the spectrum, with ASRS on the higher end.
The benefits include lower energy costs, cheaper fire suppression, a safer work environment and more efficient use of labor.
A 2013 report by a consortium of cold storage industry organizations estimated an annual labor cost savings of $2.7 million per year for a facility with an 18-worker shift and each employee costing roughly $50,000 in wages, benefits and training expenses.
Also, ASRS facilities make more efficient use of space, allowing for three times the storage density of a conventional facility, the report said.
So far, the technology is more common in Europe, where premiums for land and labor are even higher than in the United States, and in the frozen foods industry than among fresh produce packers.
Rosenbusch foresees an increase in the United States and in Washington. For example, German company New Cold has an agreement for a massive ASRS warehouse with a seafood supplier in Seattle, he said, while New Jersey-based Preferred Refrigeration Services built two new facilities last year in Washington and announced an agreement for a third.
However, the rush for this technology may take longer to reach fresh produce. Fresh fruits and vegetables have faster turnaround and producers are less willing to risk damaging delicate products, he said.
Benefits to Matson
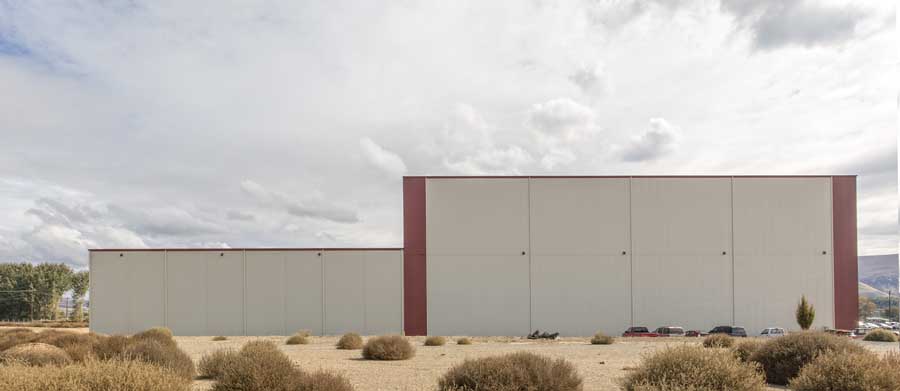
The exterior of the Matson Fruit cold storage warehouse in Selah, Washington. The right side of the warehouse, with steel siding and insulation, was built to allow higher stacking of pallets using robotic cranes. The left side of the warehouse, with concrete siding, is similar in size to a standard cold storage facility. (TJ Mullinax/Good Fruit Grower)
Increased storage density is one of Matson’s favorite aspects.
For one thing, his company can stack pallets higher and closer together because forklifts struggle to reach high items and need more room to turn around. Meanwhile, people driving forklifts only make use of 70 percent or so of the pallet space due to the imperfections inherent in driving, sorting and moving things around.
“You’re always burying something, and — oh, by Murphy’s Law — I always need the stuff in the back,” Matson said.
On the other hand, a computer-driven automated storage system makes use of 98 percent of the pallet space. Matson’s new facility has five cranes reaching two directions from the aisles. Each crane needs only one empty pallet space to maneuver pallets to reach those in the back.
The robots also allow his crews to more quickly assemble custom orders, cutting down on loading dock space. The fruit industry is in an era of custom packing for buyers who order pallets with say, seven boxes of one variety and two boxes of another, putting pressure on warehouses to quickly retrieve and replace pallets for each order, Matson said.
The company operates the warehouse with 10 to 15 employees per shift, about half the workforce it would take with a conventional facility. All the workers — quality control inspectors and forklift drivers — spend their time outside the storage area in the loading bay.
All the retrieving and replacing of pallets happens with the automated dollies and computer driven cranes, all tracked by computer.
“One of the true benefits of this system is pure inventory tracking and keeping control of everything,” said Lucas Hanson, Matson’s IT director. “Knowing where everything’s at. Every single one of these pallet positions, the system tracks.”
Added shipping manager Rumsey Abdulla: “And it stays in the cold.”
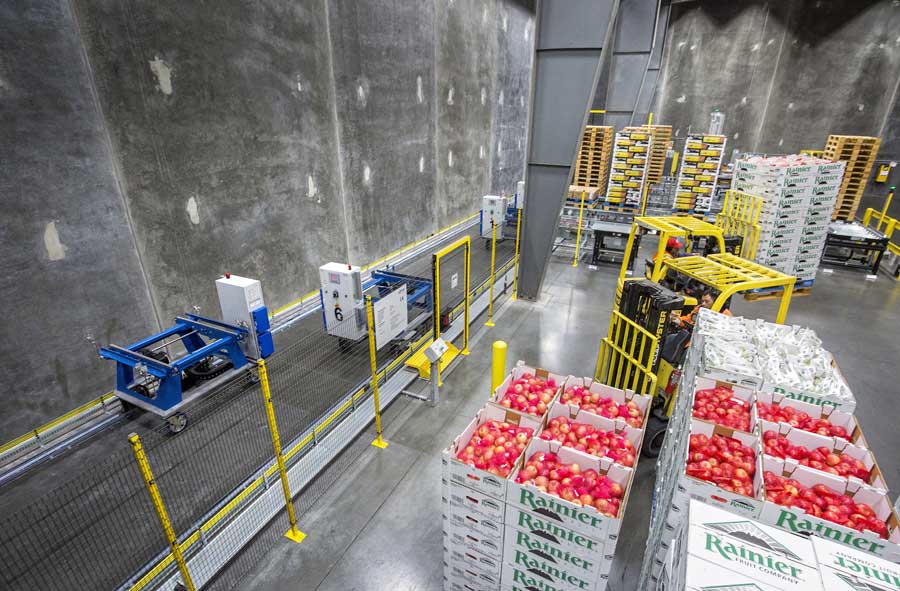
LTW Intralogistics robotic dollies move within a gated section at Matson Fruit’s automated cold storage facility. The dollies store and retrieve pallets for arriving or departing shipments.
(TJ Mullinax/Good Fruit Grower)
The 66,000-square-foot facility has 4,060 pallet spaces and stands 70 feet tall. Building that much capacity conventionally would have required 150,000 square feet or more. The building also has two empty crane aisles that would hold an additional 1,600 pallet positions for potential expansion in the future.
The company’s previous warehouse was built in 1982 when the facility packed 10,000 bins per year. In 2010, facing 150,000 to 170,000 bins a year, the Matsons began leasing storage space from another packing firm but knew they eventually would have to move.
Jordan Matson had heard of the ASRS technology and in 2010 visited a facility in Chicago. It was a tough decision, one made together by Matson, his brother Jason, his father Rod and uncle Daryl, who has since died. Abdulla and Hanson also participated.
Jordan Matson favored the ASRS, but “I tried to keep my personal opinion masked until the very end,” he said.
One of the biggest points of reluctance was not the cost, it was the question, “What happens if it breaks?” Jordan Matson said.
They have the capacity to get technicians on a video feed, have trained several in-house mechanics and keep a healthy supply of spare parts available. The company performs 99 percent of the maintenance in-house.
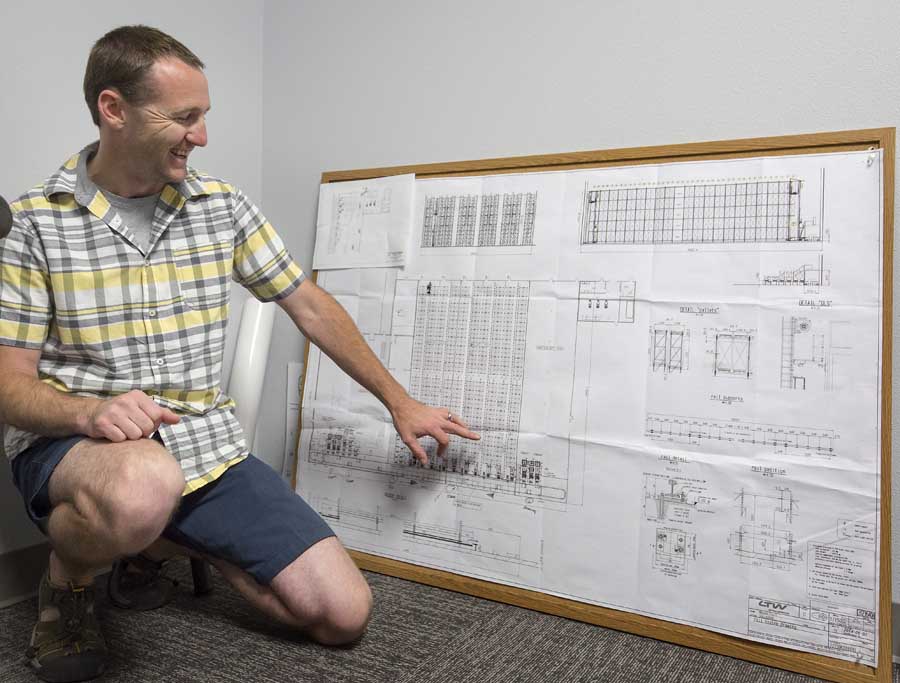
Jordan Matson shows the architectural plans for the Matson automated cold storage facility in August 2016. (TJ Mullinax/Good Fruit Grower)
Matson Fruit decided to take the risk and started construction in December 2013, finishing in September the next year in time for the 2014 crop. Austrian company LTW Intralogistics built the crane and robotics system.
Matson and his supervisors admit they have experienced troubles. They struggled to integrate software. Training was difficult at first but is getting better. And the dollies’ loop system — a novel approach even for LTW — develops points of instability and wear.
But they would do it over again.
“Automation is the future as it saves on physical space, energy and labor,” Matson said. •
– by Ross Courtney, photos by TJ Mullinax
Leave A Comment