After the Pink Lady block at Allan Brothers’ Mattawa, Washington, orchard was planted in 2014, crews raised the metal V-trellis around them.
It’s an expensive system at about $9,500 an acre for the steel and wire system, but it supports 2,420 trees per acre, owner Travis Allan told visitors as part of the IFTA tour.
The whole system depends on heavy-duty anchors similar to those that hold up utility poles.
The trees, which started as sleeping eyes, were planted in the 130-acre block in just a few days by a tractor.
Allan says he prefers to plant the dormant, cut-back sleeping eyes for the V-trellis system because the standard, 6-foot, feathered nursery trees are not a good fit for the structure of his trellis.
“This way I grow my own nursery tree and sculpt it where I want,” Allan said. “I like the ability to put the limbs where I want.”
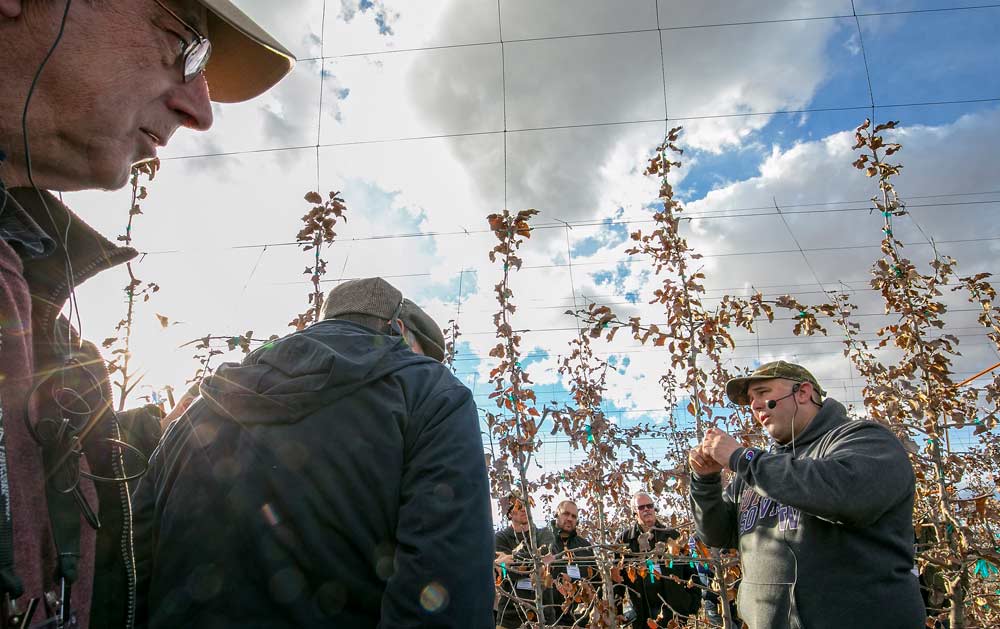
Craig Steely of Alstede Farms in New Jersey, left, leans in to watch Travis Allan, right, demonstrate how his crews secure young limbs to Yakima Valley Orchards’ all metal V-trellis system. Allan said he expects to harvest 120 bins per acre at the Mattawa, Washington, ranch. (TJ Mullinax/Good Fruit Grower)
The trade-off with tailor-grown trees is waiting until the third leaf for the first harvest. But the orchard produced 70 bins an acre in its first crop year, more than halfway to Allan’s goal of 120 bins per acre, he said.
Just down the road, Stemilt Growers opted to take a different route when establishing its Capstone Orchard. There, workers constructed the vertical trellis and installed the irrigation before planting the Fuji, Gala and Pink Lady trees by hand.
That way, the irrigation can be turned on within an hour of planting, said Robin Graham, assistant general manager for Stemilt Ag Services.
By planting on a 12-by-3-foot spacing, the rows are wide enough to allow platforms to travel the row to pick the tops first and leave the lower apples, which tend to need a little more time, Graham said.
At 10-foot spacing, they have found the platform can’t travel the row until the lower branches are harvested. And the wide, vertical systems may be able to work with an automated harvester in the future as well.
“Our reasons for staying with vertical have to do with looking at increased labor costs and a questionable labor pool,” Graham said. “And there’s value in doing what we know.” •
– by Kate Prengaman
Leave A Comment