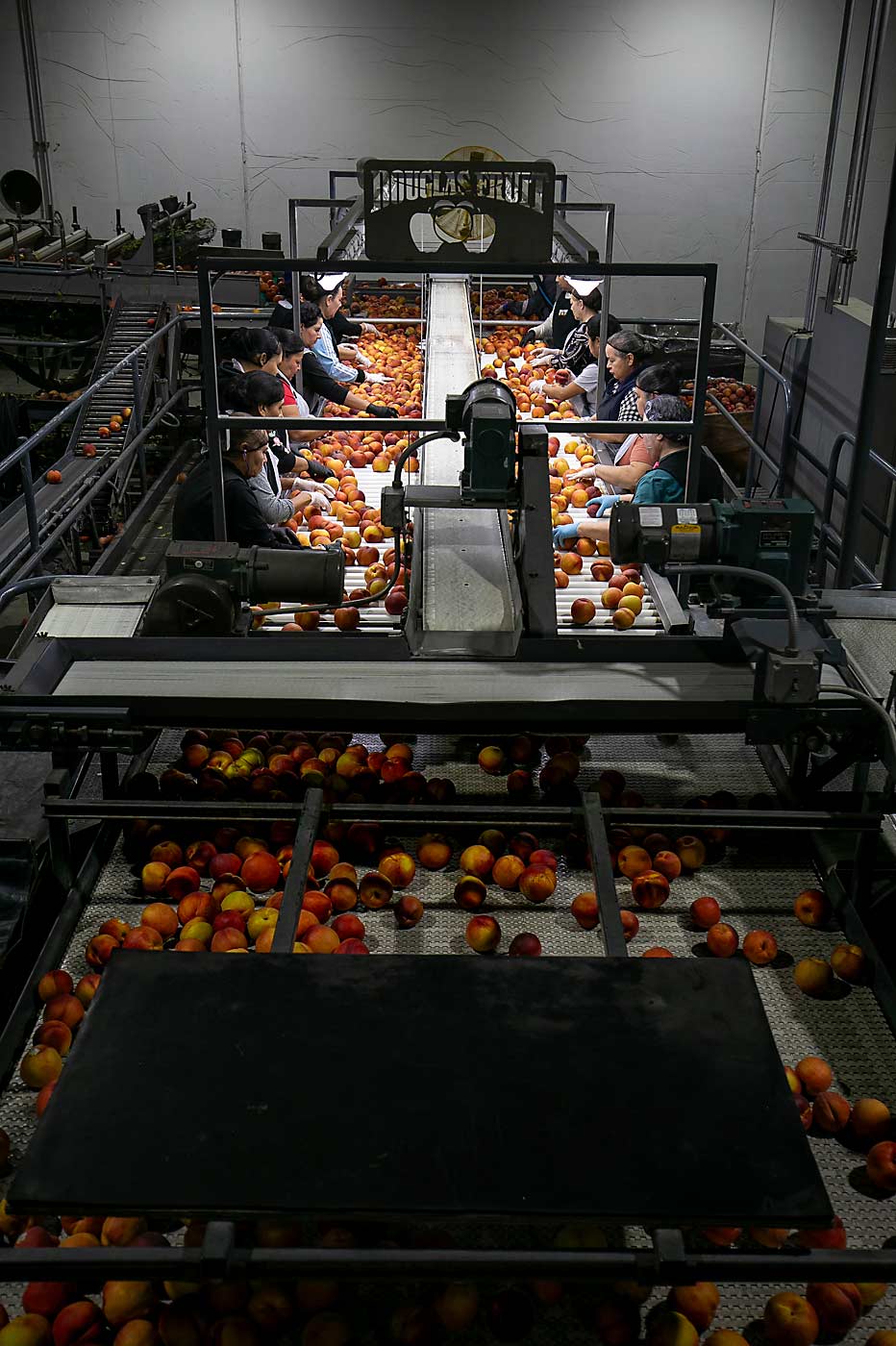
Packing perfect peaches leaves little margin for error.
“You have to get the bins in, get the fruit packed in the right box for the right customer, and shipped out in just a couple days,” said Pete Douglas, the general manager for Douglas Fruit. “They are more delicate than cherries.”
For decades, that precision packing has been in the hands — literally — of experienced line workers who know the grading standards by heart. But that’s all about to change.
“We’re going from hand packing everything to the latest and greatest in optical sorting,” he said. “And we hope that it works.”
The Douglas family has been watching the technology for stone fruit optical sorting improve over the past decade, making trips to California and Europe to watch different equipment in action. Stone fruit handling is trickier than apples or cherries, but it’s catching up. “The technology now is good enough we were ready to commit,” Pete said. “The software and hardware are now where it needs to be.”
In addition to the new Unitec optical sorter, automated bagging and tray-filling technology will reduce the labor demand on the line. But no one will be automated out of a job, Douglas said. Instead, it will give the company the steady capacity to pack apples and stone fruit at the same time.
“There are times of year when we need to double-crew this line or run three shifts,” he said. “This new line will eliminate that.”
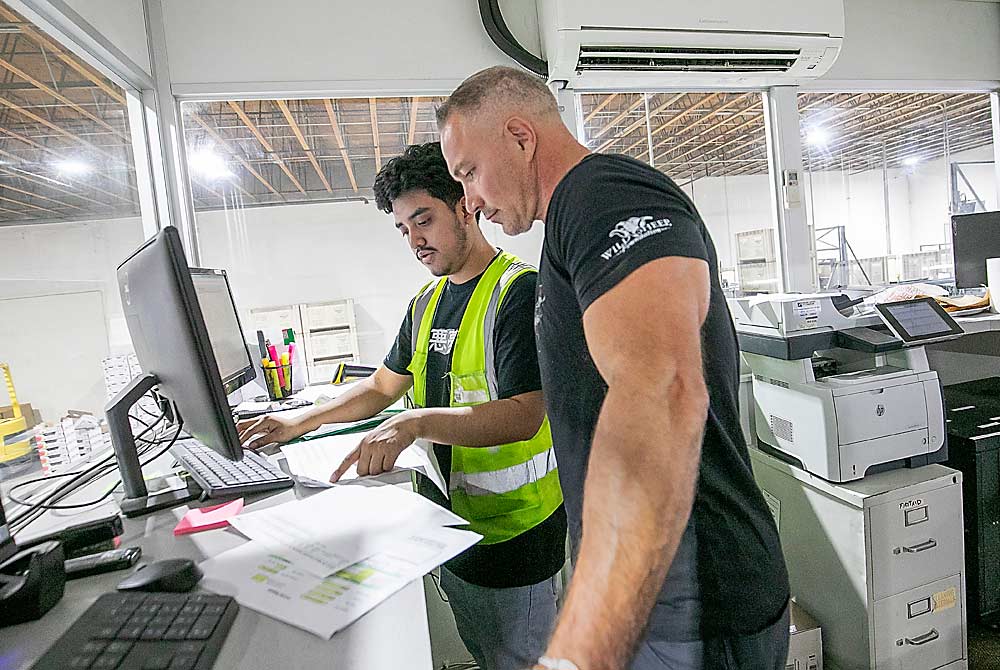
The new line marks an investment in labor efficiency and food safety today, but it will give them the capacity to expand their stone fruit acreage going forward, said David Douglas, president of the family company.
“What I talk a lot about is that we are a farming company. The warehouse is here to help us put the most return back to the farm,” David said. “We need to invest in the right equipment and right people to generate the most value for our growers.”
Right now, they pack some 30,000 bins of organic stone fruit and continue to see strong demand, Pete said. The new line has capacity to handle more, but they are cautiously expanding their stone fruit plantings to stay in step with the market.
Today, the family-owned farms are about 65 percent apples, 25 percent stone fruit and 10 percent cherries — which they send to sales partner Stemilt Growers for packing. They also pack apples for outside growers, but almost all of the stone fruit acreage is family-owned, which increases the consistency and reduces risk in the program, David said.
“We think we’re doing a good job of managing risk and diversifying,” David said.
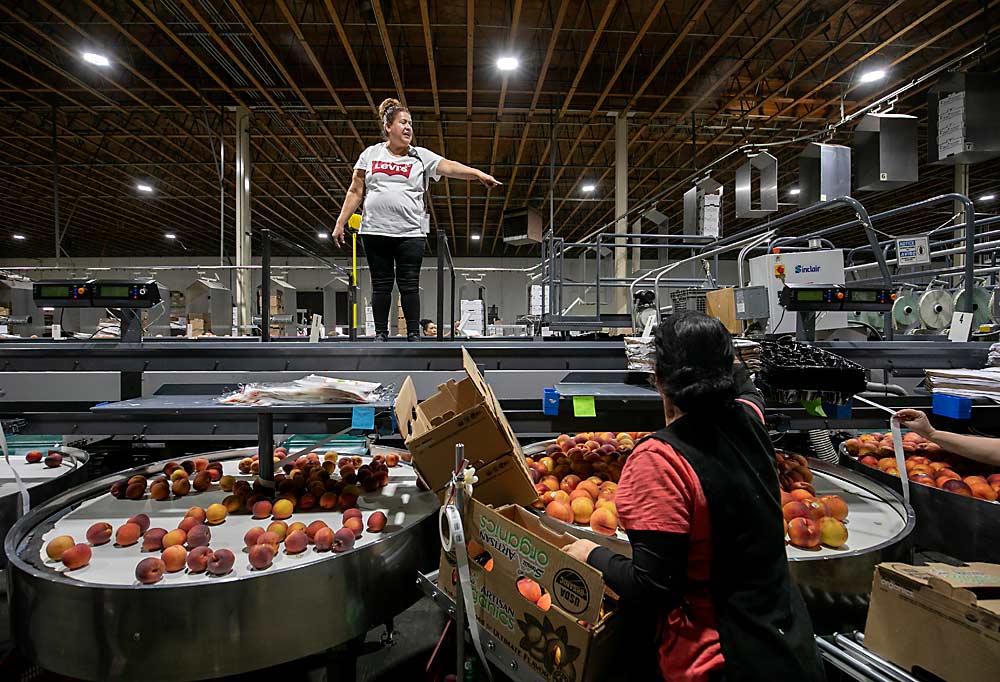
The effort in the orchard makes the fruit quality, Pete said, and the packing house protects that quality to get as much as possible to the consumers.
“We grade really hard. You can’t get 90 percent packout on peaches,” he said. “I’ll take the 75 percent and know it’s the best. That’s why we have customers.”
Peach packing is harder than apples, yes, but it’s also more rewarding, Douglas said. There’s an excitement to peach season.
“Customers can buy a Gala from anyone,” he said. “But they want to come meet us here to see the peaches.”
—by Kate Prengaman
Leave A Comment